What You Will Learn About Sheet Metal Fabrication
By reading this article, you will learn:
– Overview of sheet metal fabrication processes and the importance of precision and accuracy
– Different types of metals used, their properties, characteristics, and advantages in fabrication
– Various cutting and forming techniques, welding methods, CNC machining, surface treatment, quality control, applications, technological advancements, and tips for choosing a fabrication company
Sheet metal fabrication is a highly versatile process that transforms flat sheets of metal into a wide range of final products, from intricate electronic components to sturdy industrial machinery parts. This comprehensive guide, written by an industry expert with over 15 years of experience in precision sheet metal fabrication, aims to provide a detailed overview of sheet metal fabrication techniques, materials, processes, and applications.
Defining Sheet Metal Fabrication
1. Overview of the processes involved
Sheet metal fabrication encompasses a series of processes such as cutting, forming, welding, and finishing to shape and assemble metal sheets into the desired end product. Precision and accuracy are crucial elements in ensuring the quality and functionality of fabricated metal components.
2. Importance of precision and accuracy in sheet metal fabrication
Precision sheet metal fabrication is essential in meeting the exact specifications and tolerances required for various applications. Achieving high levels of precision ensures that the fabricated parts fit seamlessly and perform optimally within the intended systems, whether in automotive, aerospace, electronics, or medical devices.
Sheet Metal Materials and Properties
Types of Metals Used
The choice of metal significantly influences the fabrication process and the properties of the final product. Common metals used in sheet metal fabrication include:
1. Steel
Steel is a widely used material in sheet metal fabrication due to its exceptional strength, durability, and versatility.
2. Aluminum
Aluminum is favored for its lightweight nature, corrosion resistance, and excellent conductivity.
3. Copper
Copper’s malleability, electrical conductivity, and corrosion resistance make it a valuable material in sheet metal fabrication.
When considering the types of metals used in precision sheet metal fabrication, it’s important to understand the specific properties, characteristics, and advantages of each material in the fabrication process.
To delve deeper into the properties of these metals, you can refer to this insightful resource on sheet metal material properties.
Cutting and Forming Techniques
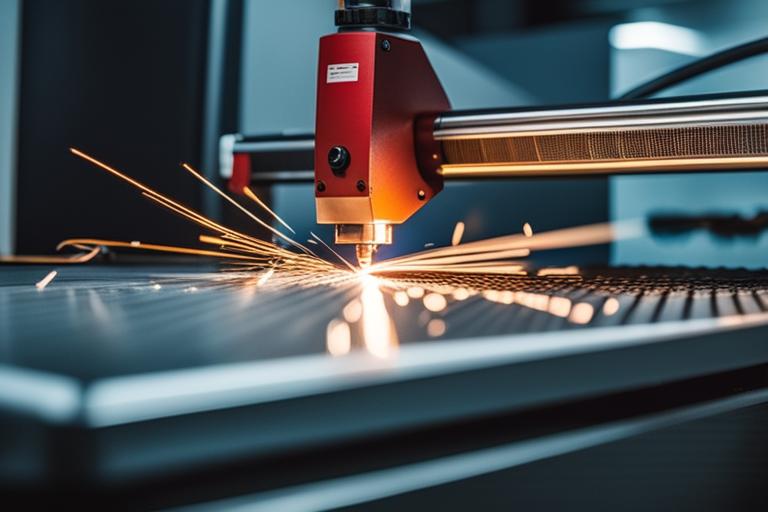
Cutting Methods
1. Laser Cutting
Laser cutting is a precise and efficient method that uses a high-powered laser to cut through sheet metal.
2. Waterjet Cutting
Waterjet cutting involves using a high-pressure stream of water mixed with an abrasive substance to cut through various types of metals.
3. Plasma Cutting
Plasma cutting utilizes ionized gas to melt and remove metal from the workpiece.

Forming Processes
1. Bending
Bending is a common forming process that involves deforming the metal sheet to create angles, curves, and various geometric shapes.
2. Punching
Punching is the process of creating holes, indentations, or other shapes in the metal sheet using a punch and die.
3. Stamping
Stamping involves using a die to shape the metal sheet into the desired form.
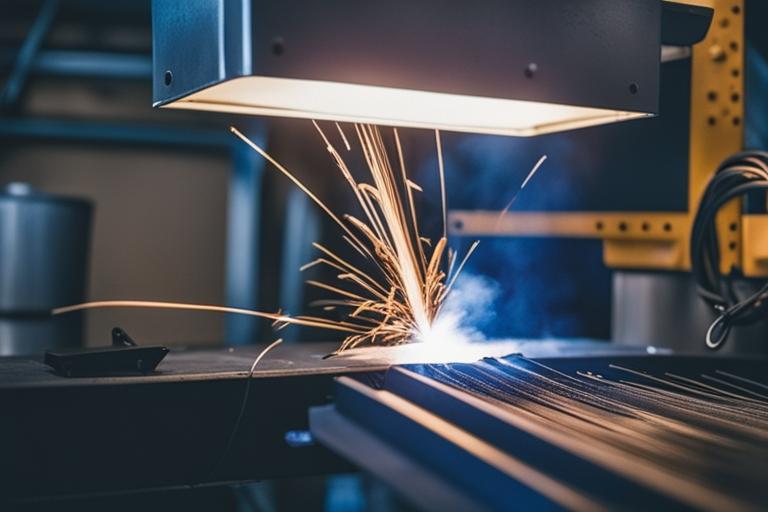
Joining and Welding in Sheet Metal Fabrication
Welding Techniques
1. MIG Welding
MIG (Metal Inert Gas) welding, also known as Gas Metal Arc Welding (GMAW), is a widely used welding process that utilizes a consumable wire electrode to join metal parts.
2. TIG Welding
TIG (Tungsten Inert Gas) welding, or Gas Tungsten Arc Welding (GTAW), is a precise welding process that uses a non-consumable tungsten electrode to produce strong, high-quality welds.
3. Spot Welding
Spot welding is a fast and efficient method for joining metal sheets by applying pressure and heat to specific points, creating localized welds.
Importance of Proper Joining Methods
The selection of appropriate joining methods is critical in ensuring the structural integrity and longevity of fabricated metal components.
In-depth insights into joining and welding processes in sheet metal fabrication can be found in this resource on welding techniques.
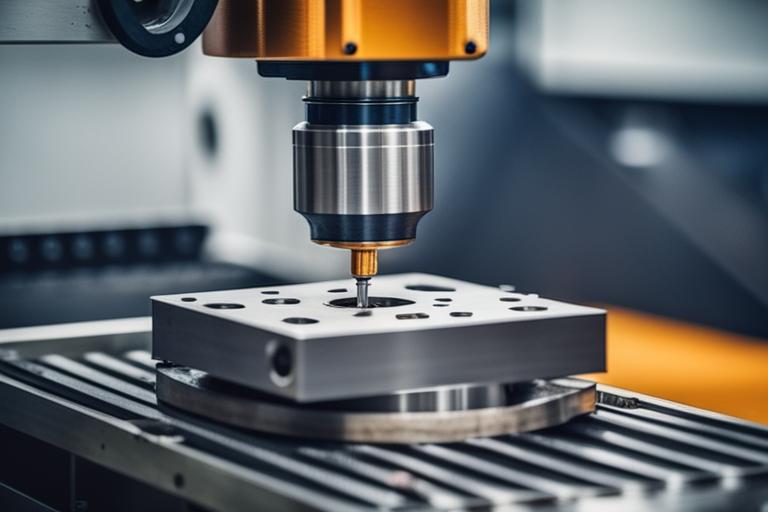
CNC Machining and Precision in Sheet Metal Fabrication
Role and Significance of CNC Machining
CNC (Computer Numerical Control) machining plays a pivotal role in achieving precise and complex components in sheet metal fabrication.
1. Creating precise and complex components
CNC machining enables the production of intricate and highly accurate components with tight tolerances.
2. Advantages in fabrication processes
The use of CNC machining enhances efficiency, repeatability, and accuracy in sheet metal fabrication.
To delve further into the role of CNC machining, you can refer to this resource on CNC precision in sheet metal fabrication.
Surface Treatment and Finishing Processes
Importance of Surface Finishing
Surface finishing is a critical aspect of sheet metal fabrication that enhances the aesthetics, durability, and functionality of fabricated components.
1. Enhancing aesthetics and functionality
Surface finishing not only improves the visual appeal of fabricated parts but also provides protection against corrosion, wear, and other environmental factors.
Various Finishing Techniques
1. Powder Coating
Powder coating is a popular finishing method that involves applying a dry powder to the metal surface, which is then cured to form a durable and attractive finish.
2. Anodizing
Anodizing is an electrochemical process that creates a protective oxide layer on the surface of aluminum.
3. Painting
Painting is a versatile finishing option that provides a decorative and protective layer to metal components.
For more detailed information on surface treatment and finishing processes, you can explore this resource on metal finishing techniques.
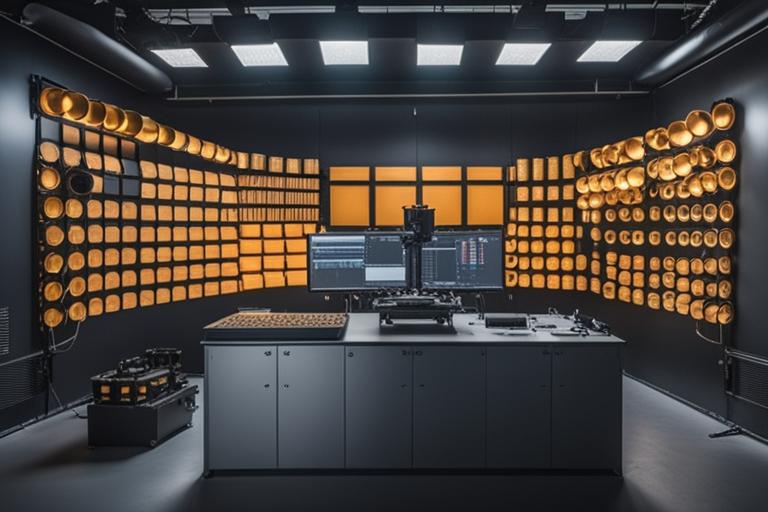
Quality Control and Inspection in Sheet Metal Fabrication
Significance of Quality Control Measures
Quality control measures are essential in maintaining the precision, consistency, and reliability of fabricated metal components.
1. Ensuring precision and accuracy
Quality control measures encompass rigorous inspection and testing procedures to verify the dimensional accuracy, material integrity, and functional performance of fabricated parts.
Inspection Techniques and Equipment
The use of advanced inspection techniques and equipment, such as Coordinate Measuring Machines (CMM) and non-destructive testing methods, allows for thorough and accurate assessment of fabricated components, ensuring compliance with the highest quality standards.
To gain further insights into quality control and inspection in sheet metal fabrication, you can refer to this resource on quality control measures.
Applications and Industries Utilizing Sheet Metal Fabrication
Sheet metal fabrication finds extensive applications across various industries, playing a vital role in the production of components for:
Automotive
In the automotive industry, sheet metal fabrication is integral to the manufacturing of vehicle bodies, chassis components, and engine parts, contributing to the structural integrity and safety of automobiles.
Aerospace
Aerospace applications rely heavily on precision sheet metal fabrication for the production of aircraft components, structural elements, and avionics enclosures, ensuring reliability and performance in demanding aviation environments.
Electronics
The electronics industry utilizes sheet metal fabrication for creating intricate enclosures, heat sinks, and mounting hardware for electronic devices, catering to the needs of diverse consumer and industrial electronic products.
Medical Devices
Precision sheet metal fabrication plays a crucial role in producing medical equipment, devices, and components that require high levels of accuracy, cleanliness, and compliance with stringent regulatory standards.
For more information on the applications and industries benefiting from sheet metal fabrication, you can explore this resource on diverse applications of sheet metal fabrication.
Technological Advancements in Sheet Metal Fabrication
Impact of Latest Technologies
1. Automation and robotics
The integration of advanced automation and robotics in sheet metal fabrication processes has revolutionized production capabilities, leading to increased efficiency, reduced labor costs, and enhanced precision in manufacturing.
2. Advanced materials and tooling
The development of cutting-edge materials and tooling technologies has expanded the possibilities in sheet metal fabrication, allowing for the fabrication of complex geometries and innovative designs with improved strength and performance characteristics.
To gain further insight into the technological advancements shaping the future of sheet metal fabrication, you can refer to this resource on emerging technologies in metal fabrication.
Selecting the Right Sheet Metal Fabrication Partner
Tips for Choosing a Fabrication Company
When selecting a sheet metal fabrication partner, it is crucial to consider factors such as the company’s:
1. Reputation and experience
Seek a fabrication company with a proven track record of delivering high-quality, precision components and a deep understanding of diverse industry requirements.
2. Quality assurance processes
Ensure that the fabrication partner adheres to stringent quality control measures and has certifications that validate their commitment to maintaining exceptional standards.
Factors to Consider When Evaluating Potential Partners
1. Customization and production capabilities
Evaluate the fabrication company’s ability to handle customized projects and their production capacity to meet varying volume requirements.
2. Online quote and ordering options
Efficient communication and streamlined processes, such as online quoting and ordering systems, contribute to a seamless and hassle-free collaboration with the fabrication partner.
When considering selecting the right sheet metal fabrication partner, it’s essential to make an informed decision based on the company’s capabilities and commitment to quality. For further guidance, you can explore this resource on choosing the right fabrication partner.
Conclusion
Recap of the importance of precision sheet metal fabrication
Precision sheet metal fabrication is a cornerstone of modern manufacturing, playing a crucial role in the production of diverse components across industries. The meticulous attention to detail, advanced techniques, and stringent quality control measures ensure that fabricated parts meet the highest standards of precision and functionality.
In conclusion, precision sheet metal fabrication encompasses a wide array of techniques, materials, and processes that are essential for the manufacturing of critical components across diverse industries. By understanding the intricacies of sheet metal fabrication and its applications, businesses can make informed decisions to optimize the production of high-quality, precision components.
Answers To Common Questions
Who uses precision sheet metal fabrication services?
Precision sheet metal fabrication services are used by industries such as aerospace, automotive, electronics, and medical equipment.
What is precision sheet metal fabrication?
Precision sheet metal fabrication is the process of cutting, bending, and assembling sheet metal to create high-quality, detailed parts and products.
How is precision sheet metal fabrication different from regular fabrication?
Precision sheet metal fabrication involves tighter tolerances and higher-quality finishes compared to regular fabrication processes.
What are the benefits of precision sheet metal fabrication?
Precision sheet metal fabrication offers high accuracy, intricate designs, and the ability to work with a variety of metals for specialized applications.
How can I ensure the quality of precision sheet metal fabrication?
You can ensure quality by choosing a reputable fabricator with experience, certifications, and a track record of delivering precise, high-quality products.
What if I need custom designs for my sheet metal parts?
Reputable precision sheet metal fabricators offer custom design services to meet specific client requirements and ensure satisfaction.