What you will learn from this article:
- The significance of custom metal fabrication in the precision sheet metal fabrication industry.
- The process of gathering detailed requirements for custom metal fabrication projects.
- Factors to consider when selecting the appropriate material for a custom metal fabrication project.
Custom metal fabrication is a specialized process that involves the creation of precision sheet metal products according to specific customer requirements. This industry plays a crucial role in various sectors, including manufacturing, construction, automotive, aerospace, and more. The demand for custom metal fabrication services has been steadily increasing as businesses recognize the importance of tailored solutions to meet their unique needs.
When it comes to precision sheet metal fabrication, off-the-shelf solutions may not always suffice. Custom metal fabrication allows for intricate designs, precise measurements, and the use of specific materials to ensure optimal performance and functionality. Whether you need a one-of-a-kind component or a large-scale production run, custom metal fabrication can provide the solutions you require.
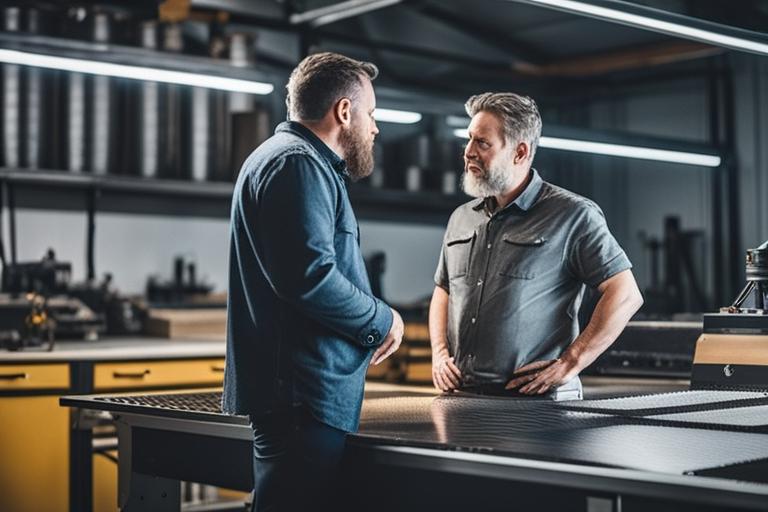
Understanding the Needs and Requirements for Custom Metal Fabrication
To ensure successful custom metal fabrication, it is essential to understand the specific needs and requirements of each project. This involves thorough communication and collaboration between the customer and the fabrication team. By gathering detailed information, the fabrication provider can create a product that meets the customer’s expectations.
During the initial consultation, the fabrication team will discuss the project’s objectives, design specifications, and functionality requirements. They will also consider factors such as budget constraints, project timelines, and any industry-specific regulations that need to be followed. This comprehensive understanding of the project requirements enables the fabrication team to provide accurate quotes and realistic timelines.
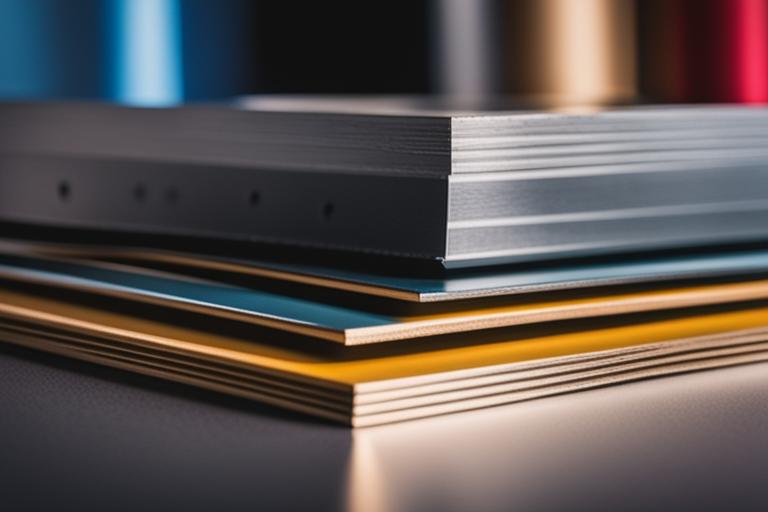
Material Selection for Custom Metal Fabrication
One of the critical decisions in custom metal fabrication is selecting the appropriate material for the project. Various metals are commonly used in precision sheet metal fabrication, including stainless steel, carbon steel, aluminum, and more. Each material has its unique properties and advantages, making it suitable for specific applications.
When choosing a material, factors such as strength, durability, corrosion resistance, and cost-efficiency must be considered. For example, stainless steel is known for its excellent corrosion resistance, making it ideal for outdoor applications or environments with high humidity. On the other hand, carbon steel offers high strength and is often used in structural components.
It is important to consult with the fabrication provider to determine the most suitable material for your project. They can provide expert advice based on their experience and knowledge of different materials.
For more information on material selection in custom metal fabrication, you can refer to this source.
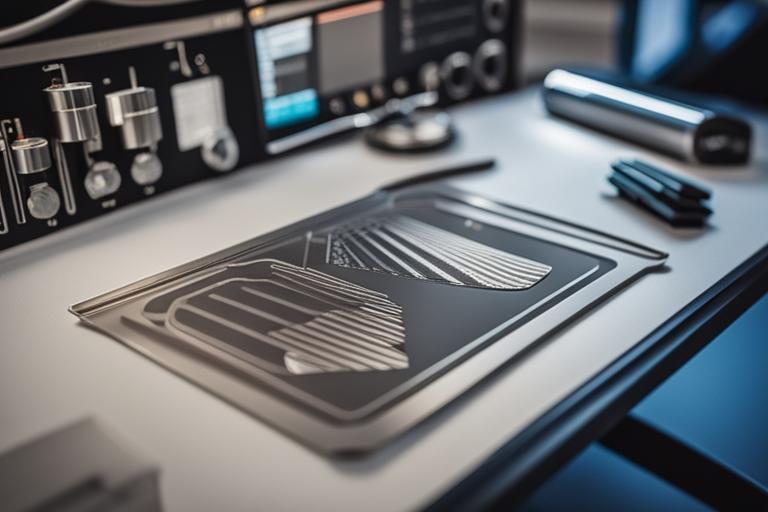
Design and Engineering in Custom Metal Fabrication
Design and engineering are fundamental aspects of the custom metal fabrication process. A well-designed product ensures functionality, efficiency, and cost-effectiveness. Modern fabrication companies utilize computer-aided design (CAD) tools and software to create precise and accurate designs.
CAD software allows designers to create detailed 2D and 3D models of the product, considering factors such as dimensions, tolerances, and assembly requirements. This digital representation helps identify potential issues and allows for adjustments before the fabrication process begins. By optimizing the design, unnecessary material waste can be minimized, reducing costs and improving efficiency.
The engineering team plays a crucial role in custom metal fabrication by providing technical expertise and ensuring that the design meets all requirements. They utilize advanced software tools such as AutoCAD, Rhino, Fusion 360, and SOLIDWORKS to assist in the design process. These tools enable them to perform tasks such as surface modeling, solid modeling, piping design, and finite element analysis.
For more information on the role of design and engineering in custom metal fabrication, you can refer to this source.
Laser Cutting and CNC Punching in Custom Metal Fabrication
Laser cutting and CNC punching are two essential processes in precision sheet metal fabrication. Laser cutting utilizes a high-powered laser beam to cut through metal sheets with precision and accuracy. This process is highly versatile and can create complex shapes and designs with ease. The laser beam is controlled by computer programming, ensuring consistency and repeatability.
The benefits of laser cutting are numerous. Firstly, it offers exceptional precision, allowing for tight tolerances and intricate designs. Secondly, laser cutting is a fast process, reducing production time and increasing efficiency. Additionally, laser cutting produces minimal material waste, making it a cost-effective solution.
CNC punching, on the other hand, involves using a computer-controlled machine to create holes, shapes, and designs in metal sheets. This process is ideal for creating repetitive patterns or perforations in the metal. CNC punching is highly efficient, allowing for high-speed production and consistent results.
For more information on laser cutting and CNC punching in custom metal fabrication, you can refer to this source.
Forming, Rolling, and Welding Techniques in Custom Metal Fabrication
Forming and rolling techniques are used to shape metal sheets into desired forms and dimensions. Bending, folding, and rolling are common methods employed during the fabrication process. These techniques allow for the creation of curved surfaces, angled edges, and complex structures.
Welding is another critical aspect of custom metal fabrication. It involves joining metal components together using various welding methods such as MIG welding, TIG welding, and spot welding. Welding provides strength and structural integrity to the fabricated product.
Skilled fabricators utilize their expertise to determine the most suitable forming, rolling, and welding techniques based on the project requirements. They ensure that the fabrication process is carried out accurately and efficiently.
For more information on forming, rolling, and welding techniques in custom metal fabrication, you can refer to this source.
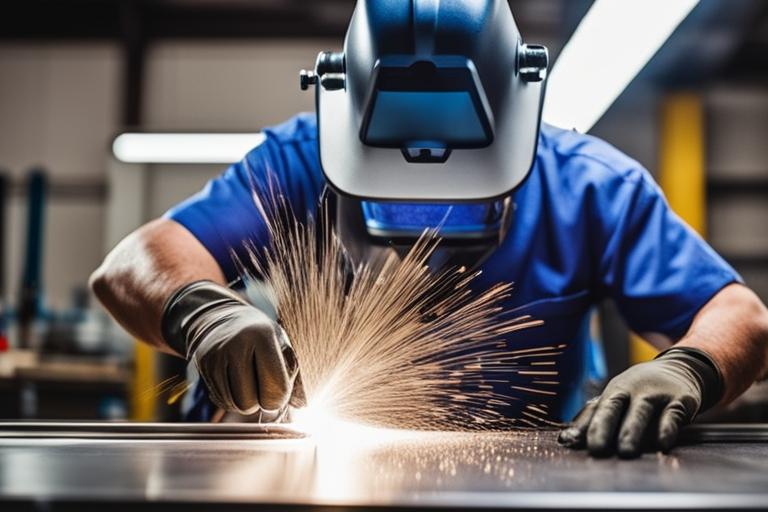
Finishing and Surface Treatment in Custom Metal Fabrication
Finishing and surface treatment play a crucial role in the overall quality and appearance of custom metal fabrication projects. These processes enhance aesthetics, durability, and resistance to corrosion.
Various finishing techniques are employed, depending on the desired outcome. Powder coating, painting, anodizing, and plating are some of the common methods used to protect the metal surface and enhance its appearance. These techniques provide a protective layer, preventing corrosion and extending the lifespan of the fabricated product.
Surface treatment is another important aspect of custom metal fabrication. It involves processes such as sandblasting, polishing, and deburring to remove imperfections and create a smooth and flawless surface. Surface treatment improves the overall quality and ensures that the fabricated product meets the highest standards.
For more information on finishing and surface treatment in custom metal fabrication, you can refer to this source.
Quality Control and Inspection in Custom Metal Fabrication
Ensuring quality control throughout the custom metal fabrication process is essential to deliver products that meet customer expectations. Fabrication companies implement rigorous quality control measures to maintain high standards and prevent defects.
Inspection tools and techniques are used to verify the accuracy, precision, and adherence to specifications. These may include visual inspections, dimensional measurements, non-destructive testing, and more. By conducting thorough inspections at various stages of the fabrication process, fabricators can identify and rectify any issues early on, minimizing the risk of errors or defects.
Quality control not only ensures the final product’s integrity but also reflects the fabricator’s commitment to customer satisfaction. By delivering products that meet or exceed expectations, fabrication companies build trust and establish long-term relationships with their customers.
For more information on quality control and inspection in custom metal fabrication, you can refer to this source.
Personal Story: The Perfect Fit for a Custom Metal Fabrication Project
At ABC Manufacturing, we pride ourselves on delivering exceptional custom metal fabrication solutions to meet the unique needs of our clients. One such success story involves our collaboration with Smith Industries, a leading automotive parts manufacturer.
Smith Industries approached us with a specific requirement for a custom metal bracket that would securely hold a critical component in their new line of electric vehicles. The bracket needed to be lightweight yet durable, with precise dimensions to ensure a perfect fit. They were also looking for a cost-effective solution that would not compromise on quality.
Our team of experienced engineers and designers worked closely with Smith Industries to understand their needs and specifications. Utilizing advanced computer-aided design (CAD) tools, we developed a design that met their requirements while optimizing for cost-effectiveness.
To fabricate the bracket, we employed laser cutting and CNC punching techniques. Laser cutting allowed us to achieve precise and clean cuts, ensuring the integrity of the metal bracket. CNC punching allowed us to create intricate holes and shapes, enabling the bracket to accommodate various mounting options.
Once the metal sheets were cut and punched, our skilled technicians used bending and welding techniques to form the bracket into its final shape. We paid meticulous attention to detail during the welding process to ensure the strength and durability of the bracket.
To provide a flawless finish, we applied a powder coating that not only enhanced the aesthetics but also provided corrosion resistance. This surface treatment ensured that the bracket would withstand the demanding conditions of the automotive industry.
Our quality control team conducted thorough inspections at every stage of the fabrication process to guarantee that the bracket met the highest standards. The final product underwent rigorous testing to ensure it met Smith Industries’ specifications and exceeded their expectations.
The custom metal bracket we delivered to Smith Industries was not only a perfect fit for their electric vehicles but also exceeded their durability and cost-effectiveness expectations. Our collaboration with Smith Industries stands as a testament to the diverse applications and successful outcomes that can be achieved through custom metal fabrication.
If you have unique metal fabrication needs like Smith Industries, don’t settle for off-the-shelf solutions. Reach out to ABC Manufacturing for a custom metal fabrication solution that is tailored to your specifications and delivers unmatched quality and value.
Delivery and Customer Satisfaction in Custom Metal Fabrication
Timely delivery and customer satisfaction are crucial aspects of custom metal fabrication. Fabrication companies understand the importance of meeting project deadlines and ensuring that the fabricated product fulfills the customer’s requirements.
Effective communication and project management are key to achieving customer satisfaction. Fabricators maintain open lines of communication, providing regular updates on the progress of the project. They address any concerns or questions promptly, ensuring that the customer’s needs are met.
Post-delivery support is also an essential part of customer satisfaction. Fabrication companies provide assistance and guidance, even after the product has been delivered. This ensures that any post-installation issues or maintenance requirements are addressed, further enhancing customer satisfaction.
Case Studies and Success Stories in Custom Metal Fabrication
To gain a better understanding of the practical applications and outcomes of custom metal fabrication, let’s explore some real-life case studies and success stories.
Case Study 1: Automotive Industry
A leading automotive manufacturer required a custom metal component for their latest vehicle model. The fabrication team worked closely with the customer to design and produce a lightweight yet durable component that met stringent safety standards. Through the use of advanced CAD tools and precision fabrication techniques, the team successfully delivered the product on time, exceeding the customer’s expectations.
Case Study 2: Aerospace Industry
An aerospace company needed a custom metal enclosure for their satellite communication system. The fabrication team collaborated with the customer’s engineering team to create a design that met the strict requirements for weight, structural integrity, and electromagnetic compatibility. Through meticulous design optimization and precision fabrication, the team delivered a high-quality enclosure that surpassed industry standards.
These case studies highlight the versatility and effectiveness of custom metal fabrication in various industries. The ability to tailor solutions to meet specific needs and requirements sets custom metal fabrication apart from standardized off-the-shelf options.
Conclusion
Custom metal fabrication is an essential service that offers tailored solutions to businesses in the precision sheet metal industry. By choosing custom metal fabrication, businesses can benefit from unique designs and precise engineering that meet their specific requirements. The fabrication process, from material selection to quality control, ensures the delivery of high-quality products.
Whether you need a single prototype or a large-scale production run, custom metal fabrication provides the precision, accuracy, and flexibility necessary to bring your ideas to life. By partnering with experienced fabrication companies, you can guarantee timely delivery, customer satisfaction, and products that exceed your expectations.
Take advantage of the possibilities offered by custom metal fabrication to fulfill your specific needs and leverage the expertise of fabrication companies to achieve your desired outcomes.
To learn more about custom metal fabrication and explore the services provided by leading fabrication providers, visit the following resources:
Remember, custom metal fabrication is the key to unlocking precision, quality, and functionality in the world of sheet metal. Whether your project is large or small, custom metal fabrication can provide the solutions you need.
Contact us today to discuss your custom metal fabrication needs and begin the process of turning your ideas into reality.