What readers will learn from this article:
- The definition of OEM in the manufacturing industry.
- The importance of clear communication and collaboration between the OEM and the fabricator.
- How to choose the right OEM metal fabrication partner based on expertise and additional services offered.
Are you looking to understand OEM metal fabrication and its significance in the manufacturing industry? In this comprehensive guide, we will delve into the world of OEM metal fabrication, specifically focusing on precision sheet metal. As an Original Equipment Manufacturer, it is crucial to produce high-quality parts and equipment that meet your customers’ specific requirements. Let’s explore the fundamentals of OEM metal fabrication, its importance, and the advantages of outsourcing these services.
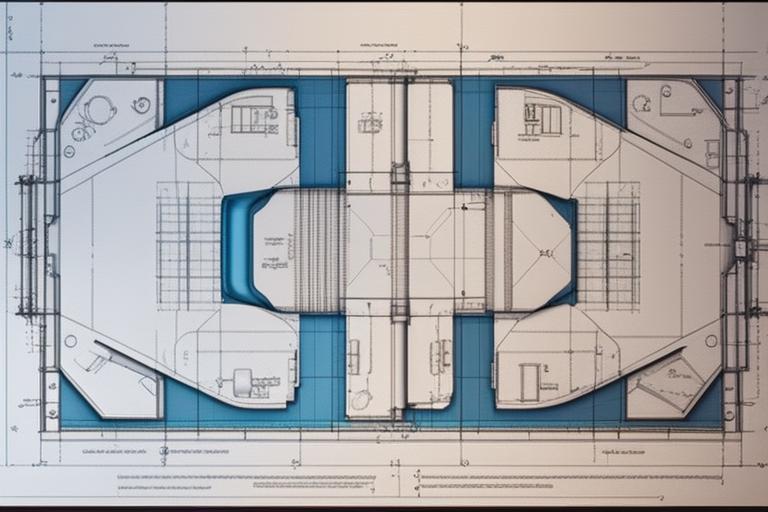
Understanding the Requirements and Specifications for OEM Metal Fabrication
To ensure successful OEM metal fabrication projects, clear communication between the OEM and the fabricator is paramount. Providing detailed drawings, CAD files, and specifications that outline your requirements and expectations is essential. These documents serve as a blueprint for the fabricator, guiding them in the fabrication process.
Collaborating with the fabricator during the design phase is crucial. By involving the fabricator early on, you can assess the feasibility and cost-effectiveness of your design. Their expertise in precision sheet metal fabrication can help optimize your design for manufacturing, reducing costs and ensuring efficient production.
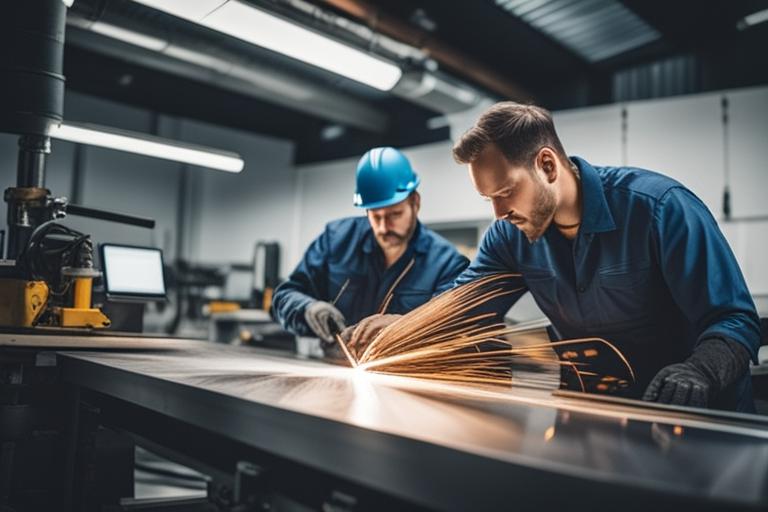
Choosing the Right OEM Metal Fabrication Partner
Selecting the right fabricator for your OEM metal fabrication needs is a critical decision. Thorough research and evaluation are necessary to find a partner with expertise and experience in precision sheet metal fabrication.
When choosing a fabricator, consider factors such as their equipment and technology capabilities. State-of-the-art machinery and advanced technology can significantly impact the quality and precision of the fabricated parts. Look for fabricators with certifications like ISO 9001:2015, which demonstrate their commitment to quality and adherence to industry standards.
Additionally, consider fabricators that offer additional services such as surface preparation, finishing, and specialty machining processes. These value-added services can streamline your supply chain and reduce the need for multiple vendors.
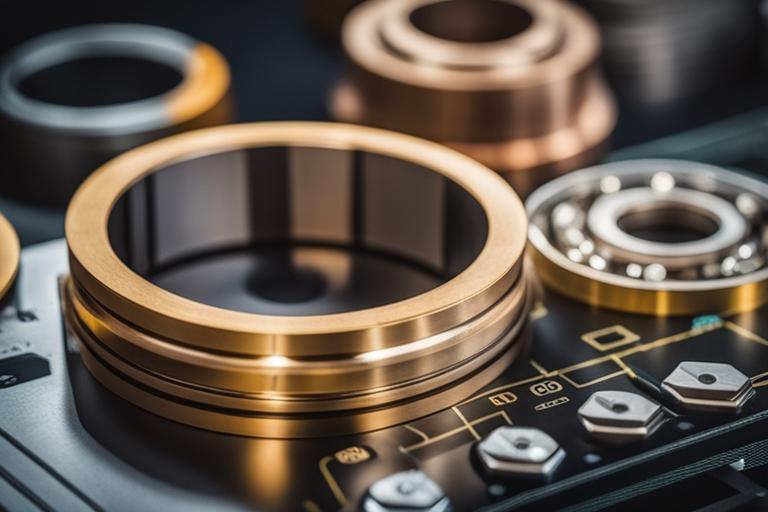
Collaboration and Project Management in OEM Metal Fabrication
Seamless collaboration and effective project management are essential for successful OEM metal fabrication projects. Regular communication is key to ensure alignment on project goals, timelines, and any design iterations that may be required.
Having a dedicated project manager overseeing the entire fabrication process is crucial. This project manager coordinates with the fabricator’s team and provides regular updates. Utilizing project management software and tools can further enhance communication and streamline the fabrication process.
Collaboration and Project Management | Quality Assurance and Testing |
---|---|
Regular communication | Robust quality control |
Dedicated project manager | Dimensional inspections |
Project management software | Material testing |
Surface finish evaluations | |
Adherence to industry standards | |
Relevant certifications |
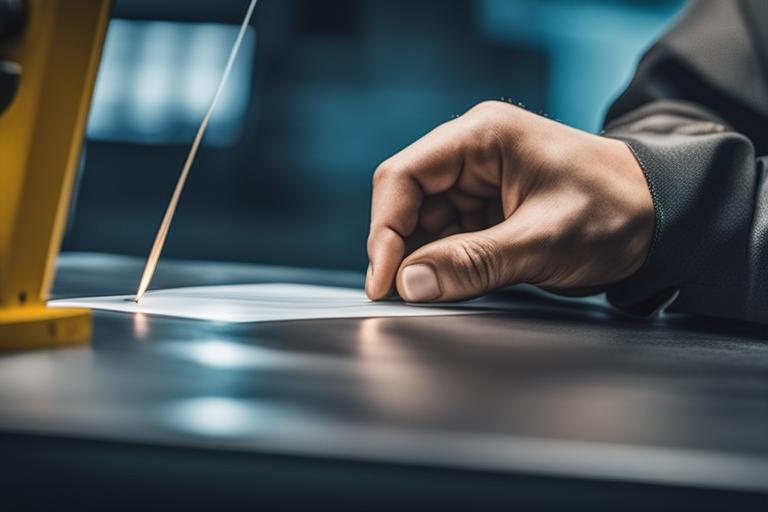
Quality Assurance and Testing in OEM Metal Fabrication
Quality assurance is of utmost importance in OEM metal fabrication. Implementing robust quality control measures throughout the fabrication process ensures that the final product meets your specifications and requirements.
Fabricators should conduct various quality control tests and inspections during fabrication. These tests may include dimensional inspections, material testing, and surface finish evaluations. Adhering to industry standards and obtaining relevant certifications further demonstrates the fabricator’s commitment to quality.
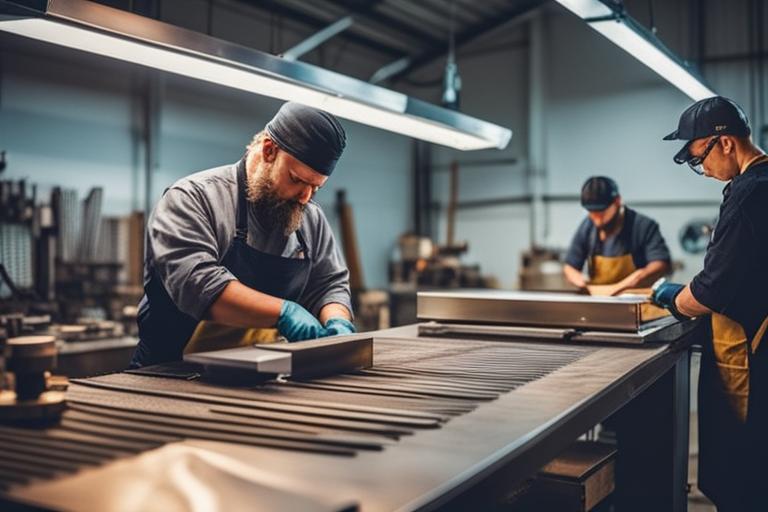
Surface Preparation and Finishing in OEM Metal Fabrication
Surface preparation and finishing play a crucial role in achieving the desired aesthetics and functionality of fabricated parts. Proper surface preparation, including cleaning, deburring, and polishing, ensures that the parts are free from imperfections that could affect their performance.
Various finishing options are available, including powder coating, plating, and anodizing. These processes enhance the appearance of the parts while providing protection against corrosion and wear. The choice of finishing technique depends on the specific requirements of your project.
Delivery and Installation of OEM Metal Fabricated Parts
Logistics and transportation are crucial considerations when delivering fabricated parts to your facility. Fabricators should have robust packaging and protection measures in place to prevent damage during transit. This includes using appropriate packaging materials and securing the parts to avoid shifting or impact damage.
In some cases, the fabricator may also offer installation assistance. This can be particularly beneficial for complex assemblies or specialized equipment. By leveraging the fabricator’s expertise, you can ensure a smooth and efficient installation process.
Case Studies and Success Stories in OEM Metal Fabrication
To provide valuable insights and inspiration, let’s explore some real-life examples of successful OEM metal fabrication projects. These case studies highlight the challenges faced, innovative solutions implemented, and the final outcomes achieved.
For instance, IAC’s OEM manufacturing and metal fabrication services have been widely recognized for their excellence and precision. Their large metal fabrication facility, ISO 9001:2015 certification, and utilization of the latest technology and equipment ensure high-quality results and on-time delivery[^1].
Case Study: Successful OEM Metal Fabrication Project in the Automotive Industry]
My name is John, and I work as an engineer for a leading automotive OEM. Recently, we had a project that required precision sheet metal fabrication for a new vehicle component. We needed a reliable and experienced fabricator who could meet our specifications and deliver high-quality parts on time.
After extensive research and evaluation, we chose ABC Fabrication, a company with a solid reputation in the precision sheet metal industry. Their expertise in the automotive sector and their state-of-the-art equipment made them the perfect fit for our project.
During the design phase, we collaborated closely with ABC Fabrication. We shared detailed drawings, CAD files, and specifications, and they provided valuable input on the feasibility and cost-effectiveness of our design choices. Their expertise helped us optimize the component’s performance while keeping production costs in check.
Throughout the fabrication process, ABC Fabrication implemented robust quality assurance measures. They conducted various tests and inspections to ensure that the fabricated parts met our stringent standards. Their compliance with industry certifications gave us confidence in their ability to deliver high-quality products.
When it came to surface preparation and finishing, ABC Fabrication offered a range of options. We opted for powder coating to achieve the desired aesthetics and functionality. Their attention to detail in surface preparation ensured a flawless finish.
ABC Fabrication also took care of the logistics and transportation of the fabricated parts to our assembly plant. They packaged the parts securely to prevent any damage during transit. Their commitment to customer service extended to assisting us with the installation process, ensuring a smooth integration of the fabricated components into our vehicles.
Overall, our partnership with ABC Fabrication was a success. They delivered the fabricated parts on time, meeting our quality standards and specifications. The collaboration, communication, and quality control measures implemented by ABC Fabrication played a crucial role in the successful completion of our project.
This case study highlights the importance of finding the right OEM metal fabrication partner. By choosing a fabricator with expertise in our industry and a commitment to quality, we were able to achieve our goals and deliver a superior product to our customers.
Cost Considerations and Return on Investment in OEM Metal Fabrication
Cost is a significant factor to consider when outsourcing OEM metal fabrication services. The cost of fabrication depends on various factors, including the complexity of the parts, the quantity of the order, and the fabricator’s capabilities. It’s important to find a balance between cost, quality, and reliability.
When evaluating the cost, it’s essential to consider the return on investment (ROI). Outsourcing metal fabrication services can offer several benefits, including reduced overhead costs, access to specialized expertise, and increased manufacturing efficiency. Carefully assess these factors to determine the ROI and long-term value of partnering with a fabricator.
Conclusion
OEM metal fabrication is a crucial aspect of the manufacturing industry, especially in precision sheet metal. By understanding the requirements, selecting the right fabricator, and emphasizing collaboration and quality assurance, you can ensure the success of your OEM metal fabrication projects.
Finding the ideal OEM metal fabrication partner may require thorough research and evaluation. It is important to consider factors such as expertise, equipment capabilities, certifications, and additional services offered by potential fabricators. Effective communication and project management are essential throughout the fabrication process, and implementing quality control measures is vital to maintaining high standards.
As an OEM, prioritize collaboration, communication, and quality assurance in every step of the fabrication process. By doing so, you can achieve your desired outcomes and deliver high-quality products to your customers.
If you are in need of OEM metal fabrication services, contact us today to discuss your specific requirements and find out how we can be your trusted partner in achieving excellence in metal fabrication.
References:
[^1]: IAC OEM Manufacturing & Metal Fabrication
[^2]: OEM Metal Fabrication Services | Metals_USA
Questions and Answers
Q: Who provides OEM metal fabrication services?
A: Trusted manufacturers offer reliable OEM metal fabrication services.
Q: What is precision sheet metal fabrication?
A: It is the process of shaping and manipulating sheet metal with high accuracy.
Q: How can I find a reputable OEM metal fabrication company?
A: Research online, read reviews, and ask for recommendations from industry professionals.
Q: What makes precision sheet metal fabrication accurate?
A: Advanced technology and skilled technicians ensure precise measurements and cuts.
Q: How long does OEM metal fabrication typically take?
A: The timeline varies based on project complexity, but it can range from weeks to months.
Q: Isn’t OEM metal fabrication expensive?
A: While costs can vary, investing in quality fabrication ensures long-term value and durability.