Precision sheet metal fabrication is a crucial process in modern industrial manufacturing. It involves the use of various techniques to create highly accurate and detailed metal components. This guide will provide you with a comprehensive understanding of precision sheet metal fabrication, including its definition, importance, key steps, and examples of industries that heavily rely on this process. By the end, you will have a solid understanding of precision sheet metal fabrication and the companies that offer these services.
What readers will learn from this article:
- Definition and importance of precision sheet metal fabrication in modern industrial manufacturing.
- Key industries that rely on precision sheet metal fabrication.
- Understanding the purpose, benefits, and commonly used metals in precision sheet metal fabrication.
- Importance of design and engineering, material selection and preparation, and precision fabrication techniques.
- Assembly, joining, and finishing processes in precision sheet metal fabrication.
- Quality control and inspection measures.
- Secondary services and additional capabilities offered by precision sheet metal fabrication companies.
- Industry-specific certifications and the importance of customer satisfaction in precision sheet metal fabrication.
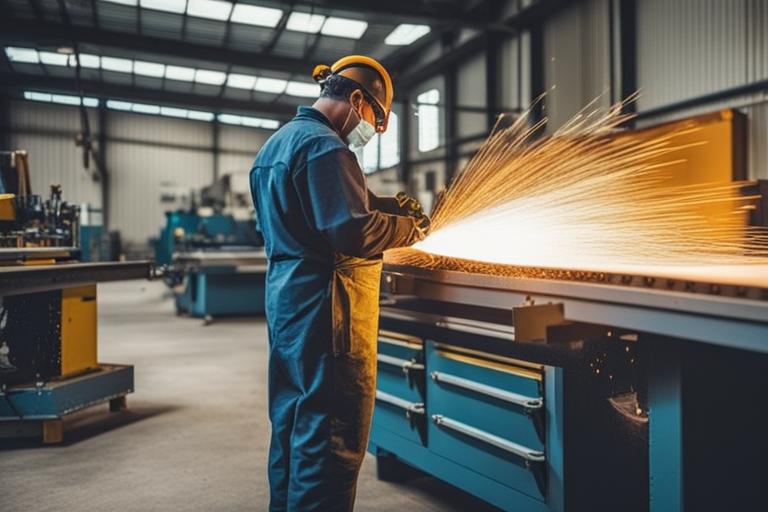
What is Precision Sheet Metal Fabrication?
Precision sheet metal fabrication is the process of creating accurate metal components using various techniques. These techniques include CNC plate cutting, laser cutting, bending, forming, and welding. The primary goal is to produce high-quality and precise metal parts that meet design requirements and specifications.
The benefits of precision sheet metal fabrication are numerous. It ensures accuracy in the manufacturing process, resulting in components that fit together perfectly and function as intended. This accuracy also leads to improved efficiency, as precise parts require less time and effort during assembly. Furthermore, precision sheet metal fabrication is cost-effective, as it minimizes material waste and reduces the need for additional modifications or adjustments.
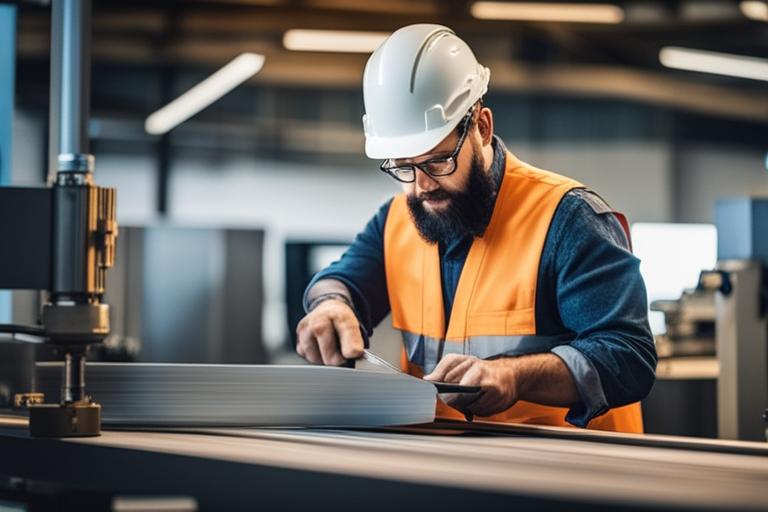
Importance of Design and Engineering in Precision Sheet Metal Fabrication
Design and engineering are vital in achieving successful precision sheet metal fabrication. Designers and engineers work together to create detailed and accurate plans that serve as the foundation for the manufacturing process. Computer-Aided Design (CAD) software is often used to create 3D models and technical drawings, allowing for precise measurements and visualizations.
Collaboration between designers, engineers, and clients is crucial to ensure project success. Clear communication and understanding of design requirements and specifications help streamline the fabrication process and minimize errors. By involving all stakeholders from the beginning, potential issues can be identified and addressed early on, saving time and resources.
Material Selection and Preparation in Precision Sheet Metal Fabrication
Selecting the appropriate sheet metal material is crucial in precision sheet metal fabrication. The choice of material depends on various factors, including the project requirements, desired properties of the final product, and budget constraints. Common sheet metal materials include stainless steel, aluminum, copper, and various alloys.
Once the material is selected, proper preparation is essential. This includes cleaning the surface to remove any contaminants that may affect the fabrication process or the quality of the final product. Cutting and shaping the sheet metal to the required dimensions are also key steps in material preparation.
Precision sheet metal fabrication techniques such as CNC plate cutting and laser cutting are commonly used to ensure precise material preparation. CNC plate cutting uses computer-controlled machines to cut the sheet metal with high accuracy and repeatability. Laser cutting utilizes a laser beam to melt, burn, or vaporize the material, resulting in precise cuts.
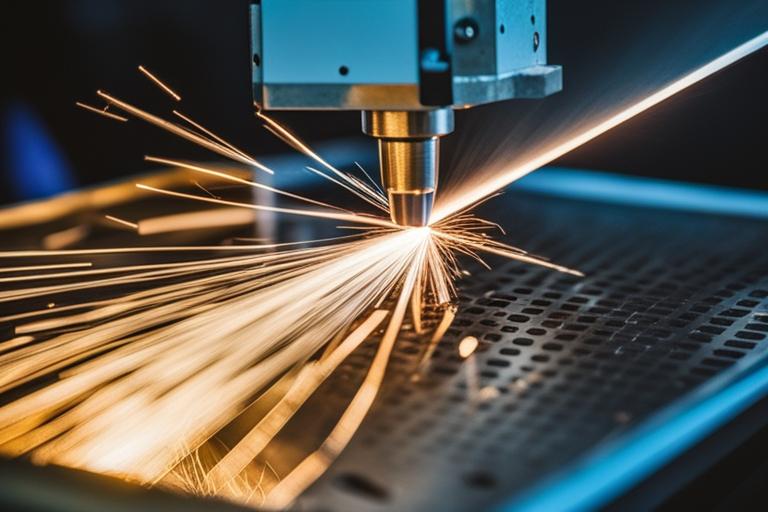
Precision Fabrication Techniques in Precision Sheet Metal Fabrication
Precision sheet metal fabrication involves various techniques to shape and form the metal components accurately. Bending is a commonly used technique that involves using a press brake to bend the sheet metal at specific angles. This technique allows for the creation of complex shapes and precise angles.
Forming is another technique used in precision sheet metal fabrication. It involves using specialized tools to shape the sheet metal into desired curves or contours. This technique is commonly used in the aerospace and automotive industries, where aerodynamic shapes are required.
Punching is a technique that involves using a turret punch press to create holes or shapes in the sheet metal. This technique offers high precision and productivity, making it suitable for mass production.
Skilled craftsmen play a vital role in executing precise fabrication techniques. Their experience and expertise enable them to operate machinery effectively, interpret technical drawings, and make adjustments as needed. Their attention to detail and dedication to quality contribute to the overall success of the precision sheet metal fabrication process.
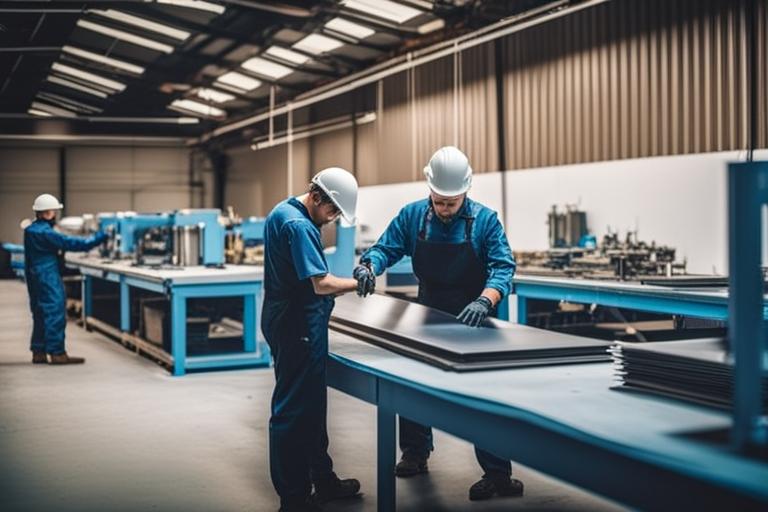
Assembly, Joining, and Finishing in Precision Sheet Metal Fabrication
Accurate assembly is crucial in precision sheet metal fabrication to ensure the structural integrity of the final product. Joining techniques such as welding, riveting, and fastening are used to connect different components together securely. Welding involves melting and fusing the metal parts together. Riveting and fastening involve using mechanical fasteners to join the components.
After assembly, the finishing process begins. Finishing includes deburring, grinding, and surface treatments to ensure a smooth and polished final product. Deburring removes any sharp edges or burrs that may be present after the fabrication process. Grinding helps achieve precise dimensions and surface finishes. Surface treatments, such as painting, powder coating, or anodizing, enhance the appearance and provide additional protection against corrosion.
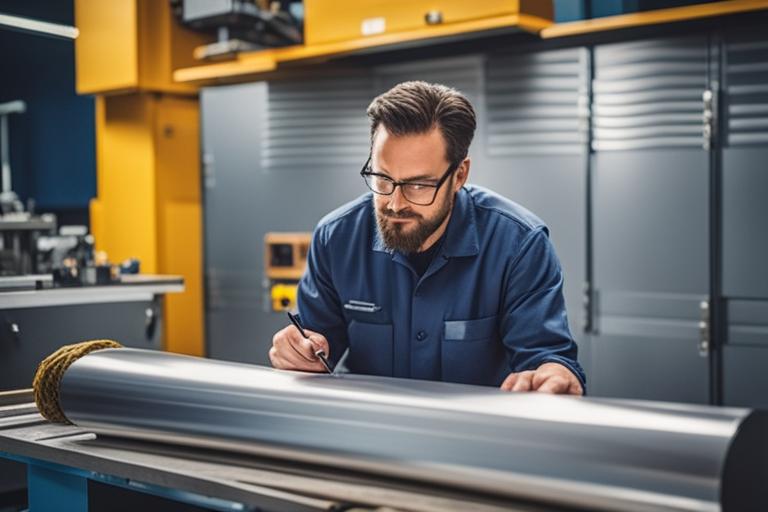
Quality Control and Inspection in Precision Sheet Metal Fabrication
Quality control is of utmost importance in precision sheet metal fabrication. A dedicated quality control department ensures that all components meet the required specifications and quality standards. They utilize measurement tools and inspection techniques to verify accuracy and compliance throughout the fabrication process.
Inspection techniques such as coordinate measuring machines (CMM) and optical measurement systems are used to measure critical dimensions and check for any deviations from the design specifications. These tools provide accurate and reliable measurements, ensuring that the final product meets the required tolerances.
Secondary Services and Additional Capabilities in Precision Sheet Metal Fabrication
Precision sheet metal fabrication companies often offer secondary services to provide comprehensive solutions to their clients. These services may include CNC laser cutting, welding, bending, and assembly. CNC laser cutting is a precise and efficient method for cutting complex shapes and patterns in sheet metal. Welding is used to join components together securely, while bending allows for the creation of precise angles and shapes.
In addition to secondary services, precision sheet metal fabrication companies have additional capabilities to handle various project requirements. They can assist with prototype development, small to large production runs, and blanket orders. From concept to completion, these companies have the expertise and resources to take projects from initial designs to the final product.
Industry-Specific Certifications and Customer Satisfaction in Precision Sheet Metal Fabrication
Precision sheet metal fabrication companies often hold industry-specific certifications to ensure compliance with quality standards. Certifications such as ISO 9001 or AS9100 demonstrate a commitment to quality and continuous improvement. These certifications provide assurance to clients that the company follows strict quality control processes and delivers high-quality products.
Customer satisfaction is a key focus in precision sheet metal fabrication. Companies strive to meet and exceed customer expectations by delivering products that meet design requirements, specifications, and deadlines. By prioritizing customer satisfaction, precision sheet metal fabrication companies build long-lasting relationships and earn a reputation for excellence.
Company Name | Location | Certifications |
---|---|---|
Precision Metal Fabrication and Weldments | [location] | ISO 9001, AS9100 |
Precision Metal Industries (PMI) | [location] | ISO 9001, AS9100 |
AP Precision Metals, Inc. | [location] | ISO 9001, AS9100, ITAR |
Examples of Precision Sheet Metal Fabrication Companies
Precision Metal Fabrication and Weldments, Inc. and Precision Metal Industries (PMI) are examples of companies that provide precision sheet metal fabrication services. Their websites showcase examples of precision sheet metal fabrications, highlighting the quality and precision achieved in their projects.
Case Study: The Impact of Precision Sheet Metal Fabrication in the Electronics Industry
John’s Electronics Manufacturing Company: A Success Story
John is the founder of an electronics manufacturing company that specializes in designing and producing high-quality electronic devices. He understands the importance of precision in the manufacturing process to ensure the functionality, durability, and aesthetic appeal of his products. That’s why he decided to partner with a precision sheet metal fabrication company to meet his manufacturing needs.
Step 1: Design and Engineering Collaboration
John’s team worked closely with the precision sheet metal fabrication company’s engineers to develop detailed and accurate designs for their electronic devices. Utilizing Computer-Aided Design (CAD) software, they were able to create intricate designs that met their specific requirements.
Step 2: Material Selection and Preparation
With the guidance of the precision sheet metal fabrication company, John’s team selected the appropriate sheet metal material for their electronic devices. They understood the importance of material preparation, including cleaning, cutting, and shaping, to ensure precise fabrication. The precision sheet metal fabrication company used advanced techniques, such as CNC plate cutting and laser cutting, to prepare the materials.
Step 3: Precision Fabrication Techniques
The skilled craftsmen at the precision sheet metal fabrication company executed various fabrication techniques, such as bending, forming, and punching, to create the desired components for John’s electronic devices. They utilized state-of-the-art machinery, including CNC press brakes and turret punches, to achieve accuracy and precision.
Step 4: Assembly, Joining, and Finishing
Accurate assembly was crucial for John’s electronic devices to ensure structural integrity. The precision sheet metal fabrication company employed various joining techniques, such as welding, riveting, and fastening, to assemble the components. They also performed finishing processes, including deburring, grinding, and surface treatments, to achieve a polished and professional look.
Step 5: Quality Control and Inspection
Throughout the manufacturing process, the precision sheet metal fabrication company had a dedicated quality control department that closely monitored the production. They used measurement tools and inspection techniques to ensure that each component met the required specifications. This emphasis on quality control helped John’s electronic devices maintain the highest standards.
Conclusion
John’s collaboration with a precision sheet metal fabrication company proved to be a game-changer for his electronics manufacturing company. The precision, accuracy, and quality control offered by the fabrication company allowed John to produce high-quality electronic devices that satisfied his customers’ expectations. By leveraging precision sheet metal fabrication, John was able to stay ahead in the competitive electronics industry.
Conclusion
Precision sheet metal fabrication is a complex and vital process in modern industrial manufacturing. It involves various techniques, materials, and quality control measures to ensure the production of accurate and high-quality metal components. By understanding the importance of precision, accuracy, and quality control, you can ensure the success of your precision sheet metal fabrication projects.
If you have industrial manufacturing needs that require precision sheet metal fabrication, reach out to companies like Precision Metal Fabrication and Weldments, Inc., Precision Metal Industries (PMI), or AP Precision Metals, Inc. These companies possess the expertise, industry-specific certifications, and commitment to customer satisfaction necessary to meet your precision sheet metal fabrication requirements.
For further information or to discuss your specific precision sheet metal fabrication needs, please contact us at [insert contact information]. We are here to assist you and provide tailored solutions for your industrial manufacturing requirements.