Sheet metal fabrication is a subtractive manufacturing process that forms parts from thin metal sheets. Engineers often choose sheet metal parts for their high strength-to-weight ratio, durability, and versatility. This guide will provide a comprehensive overview of precision sheet metal fabrication techniques, applications, and best practices.
What You Will Learn About Sheet Metal Fabrication
- Definition and materials used in sheet metal fabrication.
- Design considerations and planning for precision.
- Cutting techniques and choosing the appropriate method.
- Forming and bending processes for accurate dimensions.
- Joining methods and selecting the most suitable technique.
- Surface treatment and finishing options.
- Quality control and inspection in fabrication.
- Applications and case studies for inspiration.
- Choosing a reliable fabrication service provider.
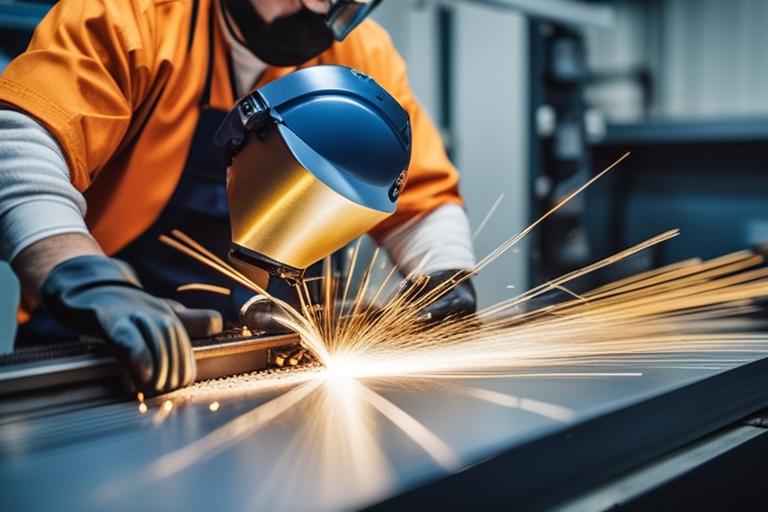
Understanding Sheet Metal Fabrication
Sheet metal fabrication services involve cutting and forming sheet stock using various tools such as shears, lasers, waterjets, plasma, or punch presses. A brake press is commonly used to create angular bends and transform the sheet into a three-dimensional object. This process can produce simple parts or complex geometries with custom die tools. Once the tools are set up, production of subsequent sheet parts is cost-effective, making it suitable for low to high volume production.
Sheet metal fabrication offers numerous benefits. The versatility of sheet metal allows for the creation of intricate designs and complex shapes. It is also highly durable and can withstand extreme conditions, making it ideal for a wide range of applications. Additionally, sheet metal is readily available and cost-effective, making it a popular choice for manufacturers.
To carry out sheet metal fabrication, various tools and equipment are used. Laser cutters, waterjets, and plasma cutters are used for precise and accurate cutting of the sheet metal. These tools utilize advanced technology to ensure clean cuts and minimize material waste. Shears and punch presses are commonly used for simpler cutting tasks.
Essential Design and Planning Considerations
Accurate design and planning are crucial in sheet metal fabrication to ensure the desired outcome. Computer-Aided Design (CAD) software plays a vital role in the process by allowing engineers to create detailed technical drawings and blueprints. CAD software provides precise measurements and enables engineers to visualize the final product before fabrication begins.
Creating precise blueprints and technical drawings is essential for successful sheet metal fabrication. These drawings serve as a guide for the fabrication process, ensuring accuracy and consistency. When creating blueprints, engineers must consider factors such as material selection and thickness based on the project requirements. The choice of material and its thickness will affect the fabrication techniques and feasibility of the project.
Cutting Technique | Description | Advantages | Limitations |
---|---|---|---|
Laser Cutting | Uses a high-powered laser beam to melt and vaporize the metal, resulting in a clean and precise cut | – Suitable for intricate designs and tight tolerances – Minimal material waste – High precision and accuracy |
– Higher operating cost compared to other methods – Limited to certain materials and thicknesses |
Waterjet Cutting | Uses a high-pressure stream of water mixed with an abrasive substance to cut through the metal | – Versatile, can handle various materials and thicknesses – No heat-affected zone – No mechanical stress on the material |
– Slower cutting speed compared to other methods – Lower precision compared to laser cutting |
Plasma Cutting | Involves the use of ionized gas to heat and cut through the metal | – Faster cutting speed – Suitable for thicker materials – Lower cost compared to laser cutting |
– Not as precise as laser cutting – Heat-affected zone and potential for distortion |
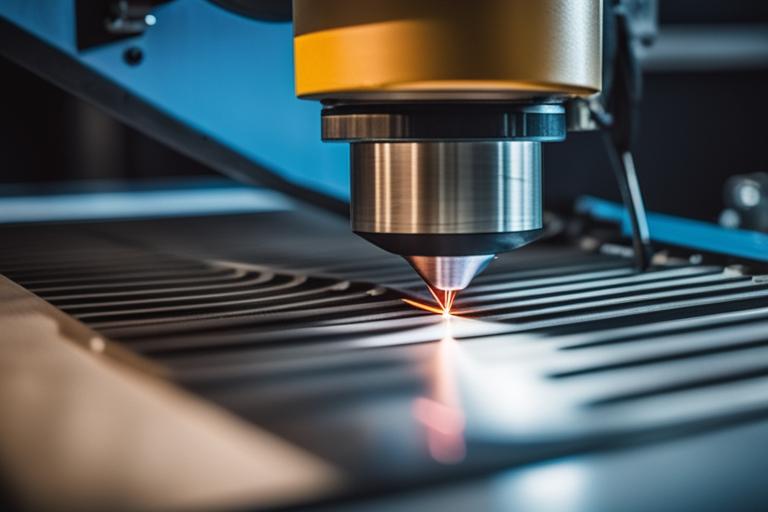
Cutting Techniques in Sheet Metal Fabrication
Cutting is a fundamental process in sheet metal fabrication. Different cutting methods are used based on the complexity of the design and the required precision. Laser cutting, waterjet cutting, and plasma cutting are commonly employed techniques.
Laser cutting utilizes a high-powered laser beam to melt and vaporize the metal, resulting in a clean and precise cut. This method is suitable for intricate designs and tight tolerances. Waterjet cutting, on the other hand, uses a high-pressure stream of water mixed with an abrasive substance to cut through the metal. It is a versatile method that can handle various materials and thicknesses. Plasma cutting involves the use of ionized gas to heat and cut through the metal. It is a faster cutting method suitable for thicker materials.
When choosing the appropriate cutting method, various factors need to be considered, including the material type and thickness, desired precision, and cost. Each cutting technique has its advantages and limitations, and the selection should be based on the specific requirements of the project.
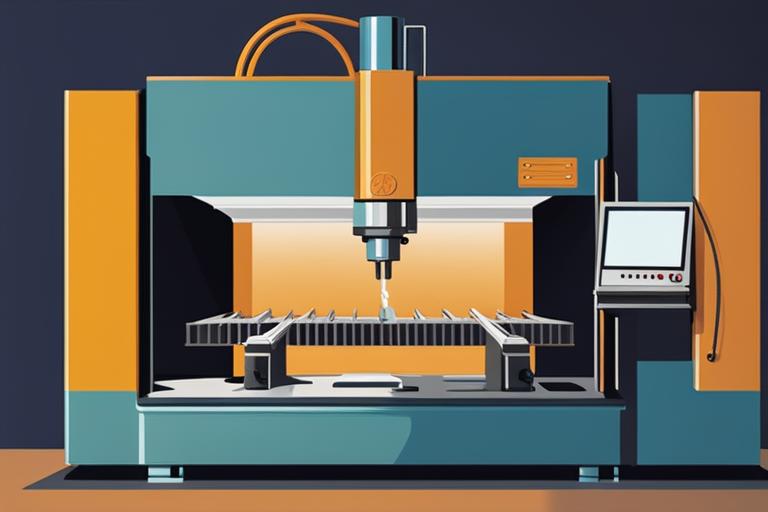
Forming and Bending Processes
Forming and bending are essential techniques in sheet metal fabrication that allow for the creation of three-dimensional shapes. The brake press is a commonly used tool for bending and forming sheet metal. It uses a punch and die set to create angular bends at specific locations. The bending process requires precise calculations and adjustments to achieve the desired angles and dimensions.
Apart from the brake press, other forming techniques such as roll forming and stretch forming are employed for specific applications. Roll forming involves passing the sheet metal through a series of rollers to progressively shape it into the desired profile. Stretch forming, on the other hand, utilizes tension to stretch the metal and form complex curves and contours.
To achieve accurate bends and maintain dimensional tolerances, proper setup and calibration of the equipment are crucial. The selection of the appropriate forming technique depends on factors such as the complexity of the design, material properties, and dimensional requirements.
Joining Methods in Sheet Metal Fabrication
Joining methods play a significant role in sheet metal fabrication to assemble multiple parts and create a finished product. Various joining techniques are employed, including fasteners, welding, and adhesive bonding.
Fasteners such as screws, rivets, and bolts are commonly used in sheet metal fabrication. They provide a secure and removable connection between parts. Welding is another widely used joining method that involves melting the metal surfaces and fusing them together. It creates a strong and permanent bond, making it suitable for applications that require high strength. Adhesive bonding utilizes specialized adhesives to join the sheet metal parts. It offers advantages such as weight reduction, improved aesthetics, and enhanced corrosion resistance.
The choice of joining method depends on factors such as the material type, design requirements, and intended application. Each technique has its advantages and limitations, and careful consideration is necessary to ensure a reliable and efficient joining process.
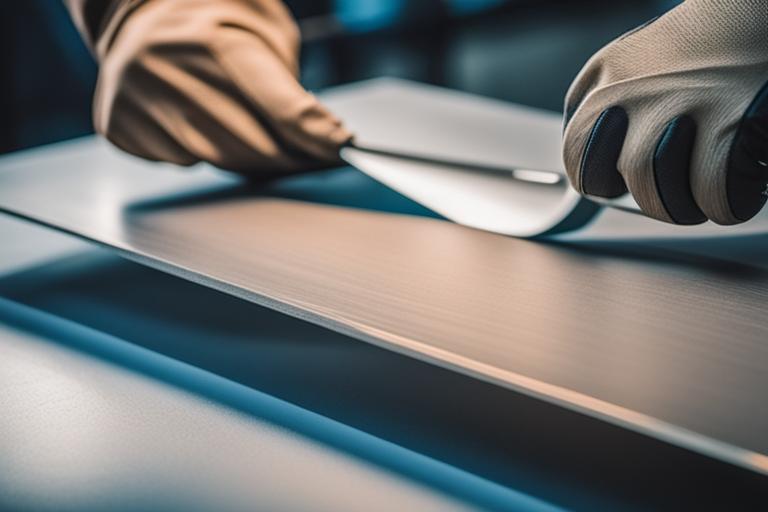
Surface Treatment and Finishing Techniques
Surface treatment and finishing are crucial steps in sheet metal fabrication to enhance the appearance, durability, and functionality of the final product. Various techniques are employed to achieve different finishes and properties.
Common finishing techniques include painting, powder coating, and anodizing. Painting provides a protective layer and allows for customization through a wide range of colors and finishes. Powder coating involves applying a dry powder to the metal surface, which is then cured to form a durable and attractive finish. Anodizing is an electrochemical process that creates a protective oxide layer on the metal surface, enhancing corrosion resistance and providing a decorative finish.
Deburring and polishing processes are also employed to remove sharp edges and achieve smooth surfaces. Deburring eliminates burrs and sharp edges left from the fabrication process, enhancing safety and aesthetics. Polishing creates a smooth and reflective surface finish, improving the overall appearance of the sheet metal part.
The choice of surface treatment and finishing method depends on factors such as the desired aesthetics, functional requirements, and environmental considerations. Proper surface treatment and finishing contribute to the overall quality and longevity of the fabricated parts.
Case Study: From Concept to Reality – The Success Story of ABC Manufacturing
At the heart of the precision sheet metal fabrication industry is the ability to turn ideas and concepts into tangible products. One such success story is the journey of ABC Manufacturing, a company that specializes in custom sheet metal fabrication for various industries.
ABC Manufacturing was approached by a client in the medical equipment industry who needed a specific component for a new surgical device. The client had a rough idea of what they wanted, but needed the expertise and precision of ABC Manufacturing to bring their concept to life.
With the client’s initial sketches and specifications in hand, ABC Manufacturing’s team of skilled engineers got to work. Utilizing CAD software, they created detailed blueprints and technical drawings, ensuring every dimension and angle was precise. They also worked closely with the client to select the most suitable material and thickness for the component, considering its function and durability.
Once the design was finalized, ABC Manufacturing employed their cutting-edge laser cutting technology to accurately cut the sheet metal according to the specifications. The laser cutting process provided clean, precise cuts, ensuring the component’s dimensions were maintained with utmost accuracy.
Next came the forming and bending processes. ABC Manufacturing utilized their state-of-the-art brake press to create the required angular bends in the sheet metal. With careful attention to detail, they achieved the desired shape and maintained dimensional tolerances throughout the process.
The component then underwent the joining process, where ABC Manufacturing utilized their expertise in welding to securely join the different parts together. This ensured the component’s strength and durability, vital for its function in the surgical device.
To achieve a flawless finish, ABC Manufacturing employed their surface treatment and finishing techniques. They carefully removed any sharp edges through deburring and achieved a smooth surface through polishing. The component was then finished with a protective powder coating, ensuring it would withstand the demands of its intended use.
Throughout the entire process, ABC Manufacturing had a robust quality control and inspection process in place. Every step was meticulously checked to ensure the component met the highest standards of precision and quality. As a result, the final product exceeded the client’s expectations and was ready to be integrated into the surgical device.
This success story of ABC Manufacturing showcases the importance of accurate design, precise fabrication techniques, and rigorous quality control in sheet metal fabrication. By understanding the client’s needs, utilizing advanced technology, and maintaining a commitment to excellence, ABC Manufacturing was able to turn a concept into a reality, providing their client with a high-quality component that met their exact specifications.
Quality Control and Inspection in Sheet Metal Fabrication
Quality control is of utmost importance in sheet metal fabrication to ensure that the final product meets the required specifications and standards. Inspection techniques are employed to verify dimensional accuracy, surface quality, and overall integrity.
Dimensional measurement is a critical aspect of quality control in sheet metal fabrication. Precise measurements are taken using specialized tools such as calipers, micrometers, and coordinate measuring machines (CMMs). Visual inspection is also performed to identify any defects, imperfections, or inconsistencies.
Industry standards and certifications play a vital role in ensuring quality in sheet metal fabrication. Compliance with standards such as ISO 9001 demonstrates a commitment to quality management systems and processes. Certification from reputable organizations further validates the capabilities and reliability of the fabrication service provider.
Establishing a robust quality control process involves regular inspections, documentation, and continuous improvement. It helps identify and rectify any issues early in the fabrication process, ensuring that the final product meets the highest quality standards.
Applications and Case Studies
Sheet metal fabrication finds applications in various industries, ranging from automotive and aerospace to electronics and construction. The versatility of sheet metal allows for the creation of components and structures used in different products and systems.
For example, in the automotive industry, sheet metal fabrication is used to manufacture body panels, chassis components, and exhaust systems. In the aerospace industry, it is employed in the production of aircraft structures, engine components, and interior fixtures. The electronics industry utilizes sheet metal fabrication for the creation of enclosures, racks, and heat sinks. In the construction industry, sheet metal fabrication is essential for architectural components, HVAC systems, and metal roofing.
Numerous case studies highlight the impact of sheet metal fabrication on product development and innovation. From custom prototypes to large-scale production, sheet metal fabrication has played a pivotal role in bringing ideas to reality and advancing various industries.
.