With the increasing advancements in manufacturing processes, sheet metal fabrication is a vital contribution to production – yet these processes are often associated with inefficiency and waste that significantly add to overall costs, lead times, and product life cycles.
This brings significant pressure on manufacturers to optimize their efficiency while upholding quality standards. Lean Manufacturing facilitates this process of becoming increasingly efficient through management of resources like material, energy and labor – bolstering productivity levels within sheet metal fabrication workflows from storage solutions all the way up to thin sheet metal processing.
Utilizing lean principles helps create a streamlined production facility which eliminates unnecessary steps for an enhanced customer experience. Here we will explore how you can maximize efficiency within your sheet metal fabrication by way of leaning out your operations!
Key Takeaways
- Lean manufacturing is a production method that seeks to maximize productivity and minimize waste by identifying, evaluating and eliminating wastage.
- Applying these principles of lean manufacturing in sheet metal fabrication leads to improved efficiency, reduced waste, increased safety and resource optimization.
- Implementing specific strategies such as Big Steel Rack sheets storage system, 6S lean methodology and preventative maintenance improve visibility while aiding effective workflow management.
- Quality control measures also help reduce defective processes or products while adding value throughout the process with minimal costs.
Understanding Lean Manufacturing in Sheet Metal Fabrication
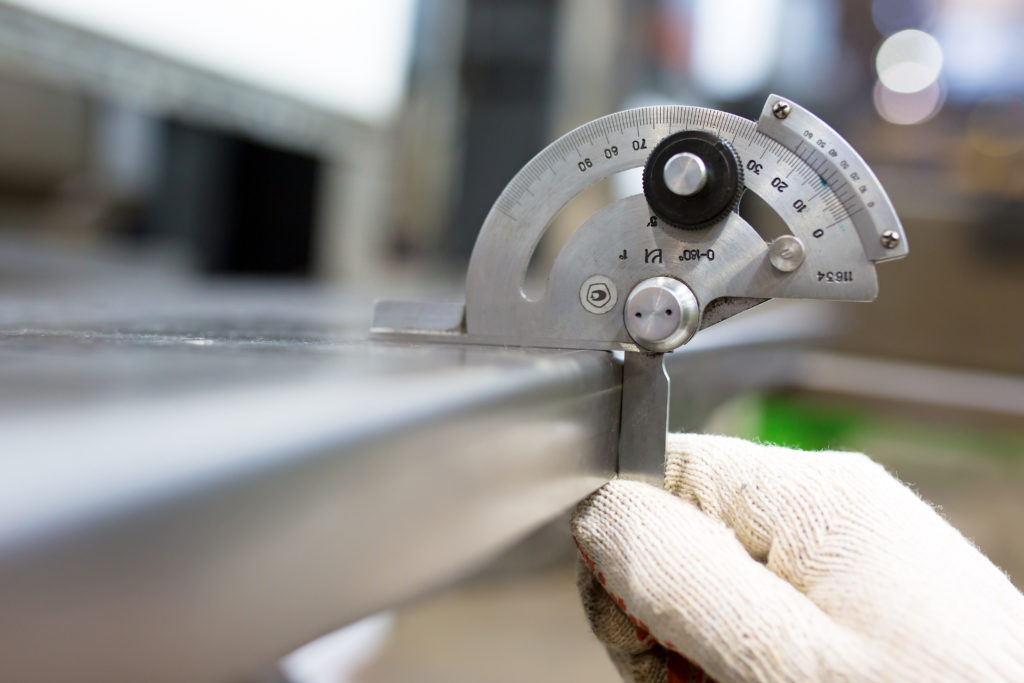
We explore the key aspects of lean manufacturing when applied to sheet metal fabrication, from its definitions and goals to its principles.
Definition of lean manufacturing
Lean manufacturing is a production method that seeks to maximize productivity and minimize waste. It focuses on identifying and eliminating the various forms of waste present in traditional processes, such as waiting, overproduction, scrap or rework.
This process can be applied to many types of production industries – including sheet metal fabrication – to reduce costs, improve quality, and boost efficiency. The five main principles underlying lean manufacturing are value-based thinking; focused value stream improvement; flow; pull system optimization; and perfection or continuous evolution towards future state goals.
Lean utilizes Just In Time (JIT) techniques whereby components are only produced when needed — allowing for faster turnaround times without extra waiting periods for materials or machines.
Goals and principles
Lean manufacturing is an approach to production that eliminates waste from the entire process, with a focus on maximizing efficiency and minimizing costs. It involves defining processes and tools in order to streamline operations and improve overall productivity.
The goals of implementing lean techniques in sheet metal fabrication are to reduce process time, eliminate non-value-added activities, maximize resources while optimizing quality control measures across all stages of production.
Furthermore, it also helps identify places where innovation could add value or help increase efficiency throughout the entire sheet metal fabrication operation. With its principles including organization via flow design; setting performance targets; visualizing work; sustaining improvement efforts through continuous improvement metrics like key performance indicators (KPIs); encouraging problem solving by employees at all levels; waste elimination through reduced cycle times and material elimination by defect prevention initiatives – this system provides manufacturers near limitless opportunities for cost reductions as well as improved quality results without adding extra complexity or overhead into the operations.
Benefits of Lean Manufacturing in Sheet Metal Fabrication
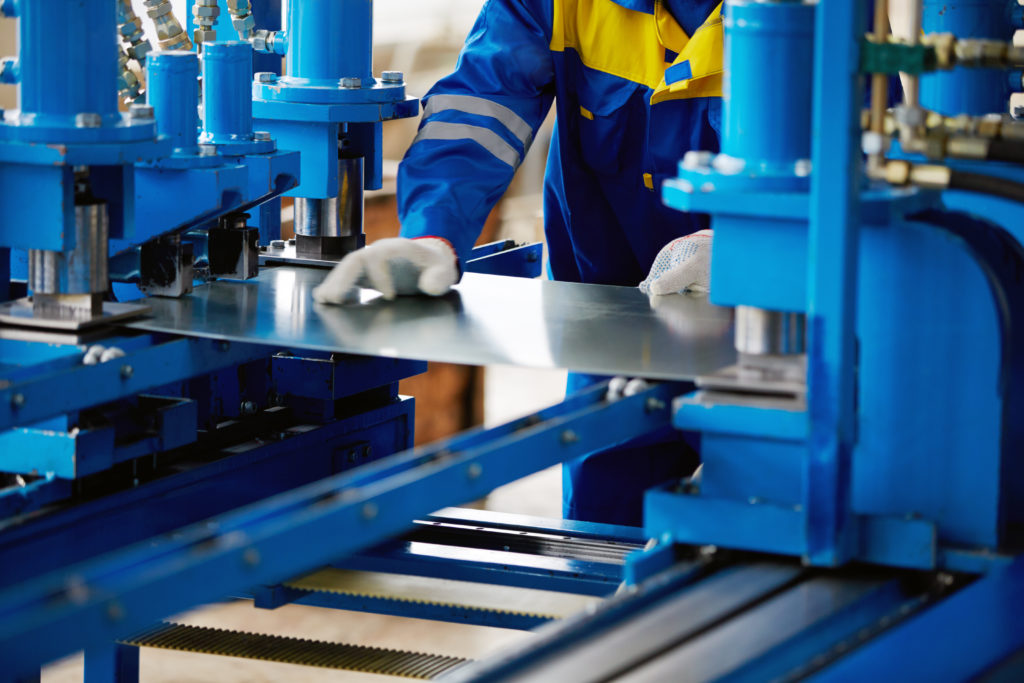
Lean manufacturing in sheet metal fabrication helps to enhance efficiency, reduce waste and increase safety at the same time.
Improved efficiency
Implementing lean techniques in sheet metal fabrication can drastically improve efficiency. Lean manufacturing focuses on optimizing processes, such as storage systems and thin sheet metal processing, to reduce waste and increase output.
By eliminating any unnecessary steps from production, manufacturers are able to complete jobs faster while also reducing operational costs. There are various strategies that can be utilized to maximize productivity including operating with minimum resources and scheduling production according to customer demand.
This allows for a more streamlined workflow which leads to improved lead time, internal customer response (ICR) and customer completion rate (CCR). Additionally, 6S lean methodology reduces non-value added activities like sorting and disposal of excess materials by establishing an efficient workspace that is easy for workers to access components quickly.
Reduced waste
As sheet metal fabricators, it is essential to reduce waste in our production processes. Lean manufacturing helps us achieve this goal by focusing on eliminating non-value added activities and optimizing resources.
By implementing lean techniques such as value stream mapping, 5S methodology, and continuous improvement initiatives we can minimize waste leading to cost savings, improved productivity and increased customer satisfaction.
Lean storage systems also help ensure that raw materials are properly stocked so there’s no inventory build-up or gaps in the workflow which would lead to waste of material or time.
Applying principles from lean manufacturing to thin sheet metal processing will enable capabilities for smarter resource management achieving better results while boosting efficiency and reducing scrap rate drastically.
Increased safety
The implementation of lean manufacturing techniques in sheet metal fabrication can lead to enhanced safety in the workplace. Lean manufacturing focuses on eliminating waste and unnecessary process steps, which can reduce potential hazardous situations.
Automation capabilities implemented into sheet metal production processes also help maximize safety, as it reduces the need for manual labor that could be subject to injury or risk from manual tasks.
These automation developments not only improve safety but also lower labor costs by removing many strenuous and tedious jobs typically needed during production processes. Additionally, companies can implement lean storage systems such as racks and shelves specifically designed for storing materials used throughout the entire metal fabrication process — helping greatly minimize any environmental hazards associated with storing heavy metals or sharp objects.
Implementing Lean Techniques in Sheet Metal Storage
We can streamline sheet metal production by introducing lean storage systems that enable us to reduce the amount of space and resources allocated to storing supplies, while also improving tracking and inventory control for easy access.
Lean storage systems
are essential to optimizing process efficiency and packaging costs in sheet metal fabrication. Lean storage systems provide an organized approach, which helps prevent damage to sheet metal parts due to mishandling during transportation or stocking. Examples of lean storage systems include Big Steel Rack sheet storage, which allow for safer sign offs while preventing damages caused by manual handling and improper layering of materials. This reduces wasted material, time and resources associated with production processes that occur when metal sheets are damaged from the start. Additionally, organizing the aisleways makes it easier for staff members to quickly find what they need as well as making sure everything is put away properly after being used. These same principles apply when processing thin sheets of metal- proper organization and placement make it far easier to apply lean production techniques such as resource optimization in order to maximize efficiency and minimize waste during production processes.
Creating a leaner production facility
Implementing lean techniques can help create a leaner production facility in sheet metal fabrication, driving improved efficiency and waste reduction. Lean manufacturing focuses on eliminating physical waste and other forms of waste such as wastes of motion, transportation, delivery time, inventory, and defects. By streamlining workflows, optimizing resources, and eliminating unnecessary steps, organizations are able to achieve the goal of leaner operations.
Applying Lean Production to Thin Sheet Metal Processing
To optimize resources, eliminate unneeded steps and maximize efficiency in thin sheet metal production, we must evaluate current processes for potential improvement opportunities.
Resource optimization
is an essential component of the lean manufacturing process for sheet metal fabrication. By optimizing resources such as raw material, energy, time and labor, manufacturers can effectively reduce waste while improving efficiency. To achieve resource optimization in the workplace, certain strategies and tools are used to place emphasis on identifying areas where time or materials could be saved.
Results and benefits
Implementing lean manufacturing techniques in sheet metal fabrication offers a variety of benefits for manufacturers. Lean production optimizes resources such as raw material, energy, time and labor thus improving efficiency significantly while also reducing waste.
It also simplifies processes across the supply chain while enhancing productivity in terms of output rates along with quality control measures. This leads to improved customer satisfaction and cost reductions which are important advantages that lean implementation provides for sheet metal fabrication operations.
By applying this technique strategically over an extended period, manufacturers are able to reap maximal results from their efforts in terms of increased business growth due to higher output coupled with fewer expenses incurred by optimized resource utilization.
Lean Manufacturing Techniques for Sheet Metal Stamping
We will explore case studies of how a company implemented lean production to improve their stamping operations, identify areas for improvement, and analyze the results.
Case study of improving productivity
The application of Lean Manufacturing techniques can have a profound effect on productivity in sheet metal fabrication. In a study conducted by an industrial metal processing firm, the utilization of lean manufacturing strategies and process improvements resulted in significant gains.
The focus of this case study was reducing scrap rate in the edge-bending process of a metal door case by implementing Lean Six Sigma methodology. Efficiency and waste reduction were achieved through increased resource optimization, capacity utilization, cycle time reduction, lead time reduction, inventory optimization and improved product quality.
Through these changes the total number of rejected parts dropped from 11% to just 0.5%. Implemented correctly, lean manufacturing processes can result in huge savings for any sheet metal manufacturer while also providing greater customer satisfaction due to higher quality products – both vital elements for success within the industry.
Identifying areas for improvement
As manufacturers, it’s essential to identify areas of improvement in order to maximize efficiency and minimize waste. Lean manufacturing is a successful approach that focuses on reducing physical and non-physical waste while improving operational flow and production performance. Key steps for identifying areas of improvement include evaluating existing processes, measuring performance against established benchmarks, and addressing the 8 lean forms of waste: transportation, waiting, overproduction/overprocessing, operator motion, scrap/reworking materials or products, storage management issues, idle time due to equipment breakdowns and resources wastage.
Conclusion
Lean manufacturing is an effective strategy for optimizing processes and minimizing waste in sheet metal fabrication. It focuses on eliminating any activities that don’t directly create value to the customer, reducing resource usage while increasing efficiency, quality, and overall production outcomes.
The key principles of lean manufacturing – such as continuous improvement, streamlining workflows, resources optimization and standardized work procedures can help boost productivity without sacrificing safety or precision.
When implemented successfully in sheet metal fabrication enterprises can realize significant cost savings while enhancing their ability to deliver top-quality products. Utilizing these techniques promises manufacturers a future of increased capacity with less downtime, improved accuracy from raw material to end product all while accruing bottom-line benefits in the form of reduced costs and increased profitability over time.
FAQs
1. What is lean manufacturing?
Lean manufacturing is a process improvement system that focuses on eliminating wasted time, effort, and cost in order to maximize efficiency.
2. How can lean manufacturing techniques be used in sheet metal fabrication?
The use of lean principles can help streamline processes within sheet metal fabrication by removing non-value-added steps from the production cycle and utilizing resources more effectively.
3. What are some specific examples of “waste” reduction during sheet metal fabrication?
Some examples include reducing delivery times, automation of repetitive tasks, waste reuse or recycling programs, better inventory management systems, and smarter machine utilization methods.
4. What kind of benefits do companies get from implementing lean manufacturing techniques for their sheet metal operations?
Companies that implement these strategies often realize improved quality control standards as well as reduced costs due to increased efficiency and reduction in material waste.