What readers will learn by reading the article:
- The definition and purpose of custom enclosures in precision sheet metal fabrication.
- The benefits, types, and materials used in custom enclosures.
- Design considerations, fabrication techniques, finishing options, and cost considerations.
- Reputable manufacturers and services, as well as future trends and innovations in custom enclosures.
Custom enclosures are specialized structures designed to house and protect sensitive equipment, electronics, and components. Precision sheet metal fabrication plays a crucial role in various industries where the need for custom enclosures arises. In this comprehensive guide, we will explore the world of custom enclosures, including their benefits, types, materials, design considerations, fabrication techniques, finishing options, manufacturers, cost considerations, and future trends.
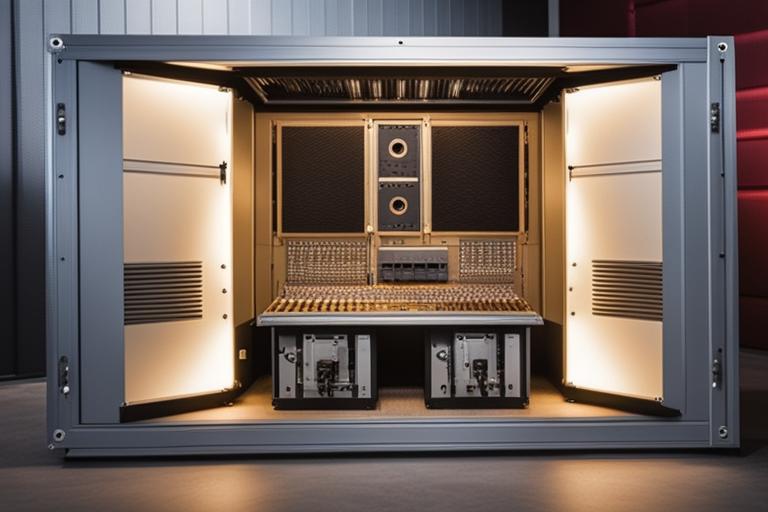
Understanding Custom Enclosures
Custom enclosures are tailor-made structures that provide a secure and protective environment for a wide range of applications. Whether it’s car audio systems, electronics, reptile habitats, stainless steel electrical enclosures, or PCB enclosures, custom enclosures offer a solution that ensures optimal functionality, aesthetics, and protection.
One example of a company specializing in custom enclosures for car audio is CUSTOM ENCLOSURES CAR AUDIO. With over three decades of experience in the industry, they have been a trusted provider of mobile electronics in Bristol since 1989. They offer a diverse range of products and services, including entertainment systems, remote start and heated seats, and leather kits. Their experienced technicians provide reliable advice, installation, and customer service.
The benefits of using custom enclosures are manifold. Firstly, they enhance the functionality of the equipment by providing a dedicated space for its operation and storage. By customizing the enclosure dimensions, connectors, and mounting options, the equipment’s performance can be optimized. Additionally, custom enclosures contribute to the aesthetics of the overall product, making it visually appealing and aligning it with the brand’s image.
Furthermore, custom enclosures offer a high level of protection to the equipment and components they house. They shield sensitive electronics from external factors such as dust, moisture, and physical damage. This protection ensures the longevity and reliability of the equipment, reducing the risk of malfunctions and downtime.
Types of Custom Enclosures
Custom enclosures come in various types, each suited for specific applications. Let’s explore some of the most common types:
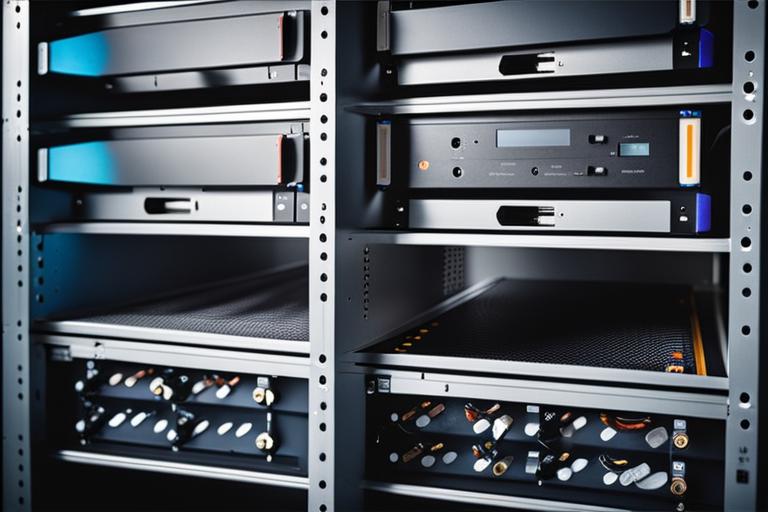
Rackmount Enclosures
Rackmount enclosures are widely used in data centers, server rooms, and audiovisual setups. They are designed to fit industry-standard rack systems and provide a secure and organized space for mounting servers, networking equipment, and audiovisual components. Rackmount enclosures offer easy access to the equipment, efficient cable management, and effective heat dissipation.
Wall-Mount Enclosures
Wall-mount enclosures are ideal for applications where floor space is limited or when wall mounting is more convenient. They are commonly used in home automation systems, security systems, and small-scale network installations. Wall-mount enclosures are compact, easy to install, and allow for efficient cable management.
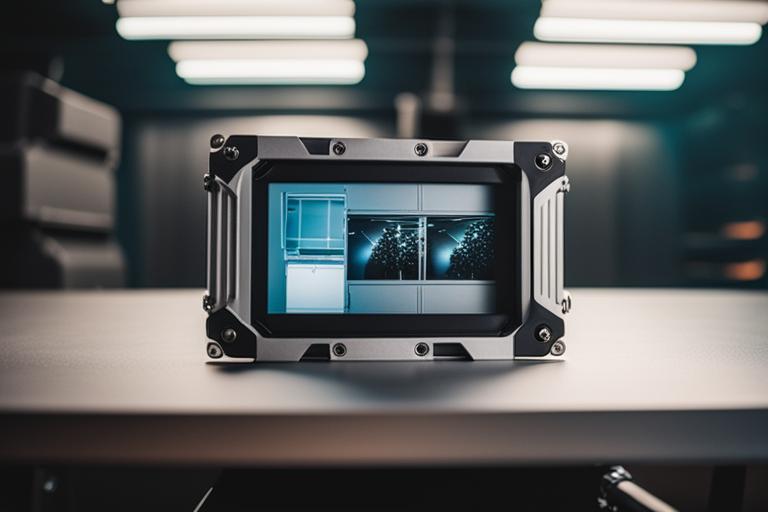
Handheld Enclosures
Handheld enclosures are designed for portable devices and handheld instruments. They are commonly used in industries such as medical, measurement, and communication. Handheld enclosures provide a comfortable grip, ergonomic design, and protection for the internal electronics. They often feature buttons, display windows, and battery compartments.
Instrument Enclosures
Instrument enclosures are specifically designed to house electronic instruments and control panels. They are widely used in laboratories, industrial automation, and scientific research. Instrument enclosures offer precise dimensions, customizable cutouts for displays and controls, and protection against electromagnetic interference.
One notable manufacturer of custom enclosures is Protocase. They specialize in custom sheet metal enclosures and offer a 2-3 day turnaround with no minimum orders. Protocase provides a wide range of enclosure styles and finishes, catering to both small and large manufacturing runs.
Selecting the Right Material
Choosing the appropriate material is a critical aspect of custom enclosure design. The material should align with the specific requirements of the application, considering factors such as durability, conductivity, and corrosion resistance. Here are some commonly used materials for custom enclosures:
Stainless Steel
Stainless steel is a popular choice for custom enclosures due to its excellent corrosion resistance and durability. It provides robust protection against harsh environments, making it suitable for outdoor applications. Stainless steel enclosures are commonly used in industrial settings, marine environments, and transportation.
Aluminum
Aluminum is known for its lightweight yet sturdy properties. It offers good electrical conductivity and is easily machinable. Aluminum enclosures are commonly used in electronics, aerospace, and automotive industries. They are favored for their excellent heat dissipation properties, making them suitable for applications with high thermal loads.
Galvanized Steel
Galvanized steel is a cost-effective option for custom enclosures. It is steel coated with a layer of zinc to enhance its corrosion resistance. Galvanized steel enclosures are commonly used in outdoor applications where protection against rust and corrosion is essential. They are widely utilized in telecommunications, power distribution, and industrial equipment.
When selecting the material for custom enclosures, it is crucial to consider the specific requirements of the application. Factors such as environmental conditions, weight limitations, and budgetary constraints should be taken into account to ensure the optimal material choice.
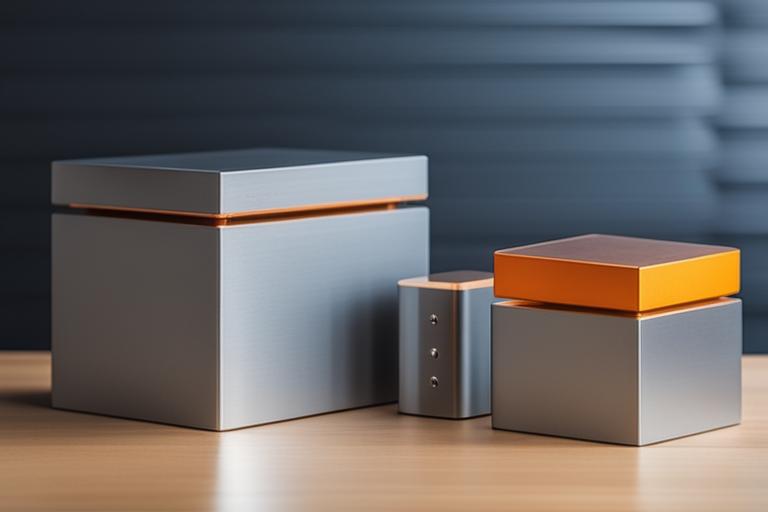
Design Considerations
Designing custom enclosures requires careful consideration of several factors to ensure functionality, aesthetics, and ease of use. Here are some key design considerations to keep in mind:
Size and Shape
The size and shape of the enclosure should be determined based on the dimensions of the equipment or components it will house. It should provide sufficient space for the proper installation, operation, and maintenance of the internal elements. The shape of the enclosure should be ergonomic and visually pleasing, aligning with the overall product design.
Accessibility
Easy accessibility is crucial for maintenance and repairs. The enclosure should provide convenient access points for connectors, buttons, and interfaces. Consideration should also be given to the ease of replacing components or upgrading equipment within the enclosure.
Case Study: Custom Enclosure Solutions for Car Audio Enthusiasts
Car audio enthusiasts are always on the lookout for ways to enhance their audio systems and create a premium sound experience while on the road. One particular car audio enthusiast, named Sarah, wanted to upgrade her car’s audio system with custom enclosures that would not only improve the sound quality but also add a touch of personal style to her vehicle.
Sarah contacted a reputable manufacturer specializing in custom enclosures for precision sheet metal fabrication. She explained her requirements and the manufacturer’s design team worked closely with her to create a unique and functional solution.
The design team took into consideration the size and shape of Sarah’s vehicle, as well as the specific audio components she wanted to install. They recommended a custom rackmount enclosure that would fit perfectly in her trunk while maximizing the available space for the audio equipment.
To ensure optimal sound performance, the design team incorporated proper ventilation and cable management features into the custom enclosure. They also suggested using aluminum as the material for the enclosure due to its lightweight yet durable nature.
Once the design was finalized, the manufacturer used laser cutting and CNC machining techniques to precisely fabricate the custom enclosure according to Sarah’s specifications. The enclosure was then finished with a powder coating in a color that matched her car’s interior, giving it a sleek and cohesive look.
Sarah was thrilled with the final result. The custom enclosure not only provided a secure and organized space for her audio components but also enhanced the overall sound quality in her car. She received many compliments from friends and fellow car audio enthusiasts who were impressed by the custom enclosure’s design and functionality.
This case study showcases how custom enclosures can be tailored to meet the unique needs of car audio enthusiasts, allowing them to achieve their desired sound experience while adding a touch of personal style to their vehicles. It also highlights the importance of partnering with experienced manufacturers who can provide design assistance and deliver high-quality custom enclosures.
Ventilation
Proper ventilation is essential to prevent heat buildup within the enclosure. Heat-generating components should be positioned strategically, and ventilation holes or fans should be incorporated to facilitate airflow. This helps maintain optimal operating temperatures and prolongs the lifespan of the equipment.
Cable Management
Efficient cable management is vital to ensure a tidy and organized enclosure. Cable routing features such as cable glands, tie-down points, and cable trays can help keep the interior space clutter-free and facilitate future modifications or repairs.
Mounting Options
The enclosure should provide appropriate mounting options to ensure secure and stable installation. Mounting brackets, rails, or DIN rails can be used depending on the application requirements. The mounting mechanism should be robust enough to withstand vibrations or shocks that may occur during operation.
Design software and CAD/CAM tools play a crucial role in creating precise and functional custom enclosures. They enable designers to visualize the final product, make accurate measurements, and ensure compatibility with the equipment or components.
Design Consideration | Description |
---|---|
Size and Shape | Determined based on the dimensions of the equipment or components, providing sufficient space for installation, operation, and maintenance. |
Accessibility | Easy access points for connectors, buttons, and interfaces, as well as consideration for component replacement or equipment upgrades. |
Ventilation | Strategic positioning of heat-generating components, incorporation of ventilation holes or fans to facilitate airflow and maintain optimal operating temperatures. |
Cable Management | Features such as cable glands, tie-down points, and cable trays to keep the interior space organized and facilitate modifications or repairs. |
Mounting Options | Appropriate mounting options such as brackets, rails, or DIN rails for secure and stable installation. |
Design Software and CAD/CAM Tools | Utilizing design software and CAD/CAM tools to visualize the final product, make accurate measurements, and ensure compatibility. |
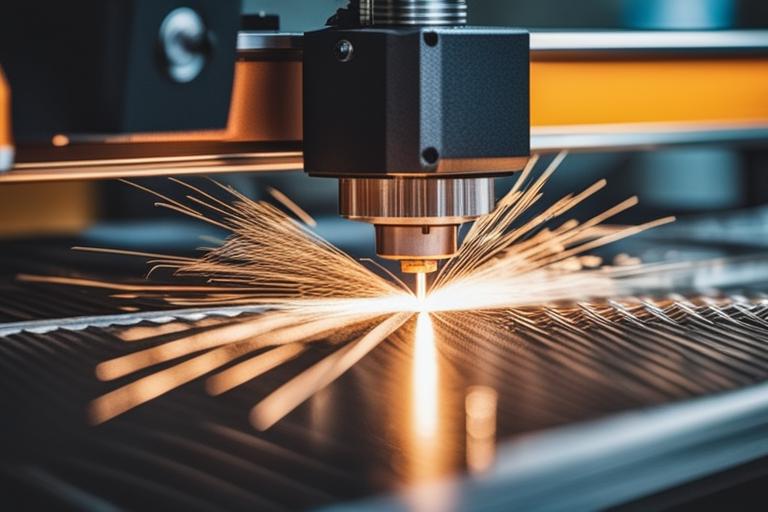
Precision Sheet Metal Fabrication Techniques
Precision sheet metal fabrication techniques are employed to transform raw sheet metal into custom enclosures with high accuracy and quality. Here are some commonly used techniques:
Laser Cutting
Laser cutting is a precise and efficient method for cutting intricate shapes and patterns in sheet metal. It uses a focused laser beam to melt or vaporize the material, resulting in clean and precise cuts. Laser cutting allows for complex designs and precise tolerances, making it ideal for creating custom enclosures with intricate features.
CNC Machining
CNC (Computer Numerical Control) machining involves using computer-controlled machines to remove material from the sheet metal, creating the desired shape. It offers high precision, repeatability, and versatility in creating complex features and cutouts. CNC machining is commonly used for producing custom enclosures that require precise dimensions and intricate details.
Forming
Forming techniques such as bending, folding, and stamping are used to shape the sheet metal into the desired enclosure design. Bending machines and press brakes are utilized to create bends and folds, while stamping presses can be used to create embossed or debossed features. Forming techniques allow for the creation of three-dimensional shapes and ensure structural integrity.
Accurate measurements and tolerances are crucial in precision sheet metal fabrication. Any discrepancies in measurements can lead to improper fitment and compromise the functionality of the custom enclosure. Advanced measurement tools and quality control processes are employed to ensure precise fabrication.
Finishing and Coating Options
Finishing and coating custom enclosures are essential steps to enhance their durability and protect them from environmental factors. Here are some common finishing options:
Powder Coating
Powder coating involves applying a dry powder to the surface of the enclosure and then curing it under heat. This process creates a durable and attractive finish that provides excellent corrosion resistance. Powder coating allows for a wide range of color options and provides a smooth and even coating.
Anodizing
Anodizing is an electrochemical process that forms a protective layer of oxide on the surface of aluminum enclosures. This layer enhances corrosion resistance and durability while maintaining the natural metallic appearance of the aluminum. Anodized enclosures are commonly used in electronics, aerospace, and automotive industries.
Painting
Painting is a versatile finishing option that allows