Are you looking to enhance your skills in sheet metal fabrication? Whether you’re a beginner or an experienced professional, learning new tips and techniques can help take your fabrication abilities to the next level. In this comprehensive guide, we will explore the key aspects of sheet metal fabrication, from understanding different materials to mastering cutting and forming techniques. With expert advice and insights, you can improve your knowledge and expertise in this versatile field.
What you will learn by reading this article:
- Different types of sheet metals commonly used in fabrication.
- Factors to consider when choosing the appropriate sheet metal for a project.
- Importance of creating detailed engineering drawings or CAD files.
- Key design considerations for sheet metal fabrication.
- Various cutting and forming techniques in sheet metal fabrication.
- Different methods of joining and assembly.
- Surface finishing options for sheet metal parts.
- Importance of quality control in sheet metal fabrication.
- Additional services offered by sheet metal fabrication companies.
- Benefits of partnering with a reputable sheet metal fabrication company.
- How to find reliable sheet metal fabrication service providers and request quotes.
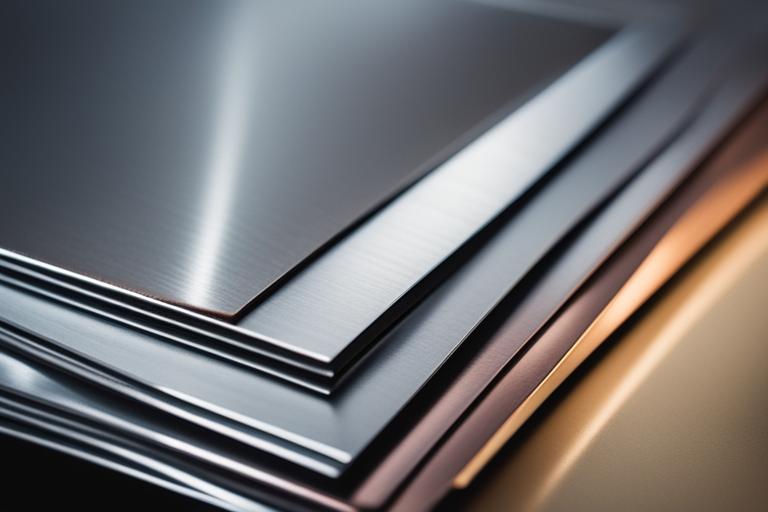
Understanding Sheet Metal Materials
Before diving into the intricacies of sheet metal fabrication, it’s crucial to have a solid understanding of the different types of sheet metals commonly used in the field. Stainless steel, aluminum, and copper are among the most popular choices due to their unique properties and wide availability.
Stainless steel is known for its exceptional strength, corrosion resistance, and heat resistance. It is commonly used in applications where durability and aesthetics are paramount, such as architectural structures, kitchen equipment, and automotive components.
Aluminum, on the other hand, is lightweight, highly malleable, and offers excellent conductivity. It finds extensive use in industries like aerospace, automotive, and electronics, where weight reduction is a critical factor.
Copper is valued for its excellent electrical conductivity and heat transfer capabilities. It is commonly utilized in electrical wiring, heat exchangers, and plumbing systems.
When choosing the appropriate sheet metal for a specific project, several factors must be considered. Strength, corrosion resistance, conductivity, and cost are some of the key considerations. It’s essential to select a material that aligns with the project requirements and offers the desired properties.
Material properties play a crucial role in achieving the desired outcomes in sheet metal fabrication. Understanding the characteristics of different metals allows fabricators to optimize their processes and deliver high-quality products. For more in-depth information on sheet metal materials, you can refer to the Custom Sheet Metal Fabrication Service provided by Xometry.
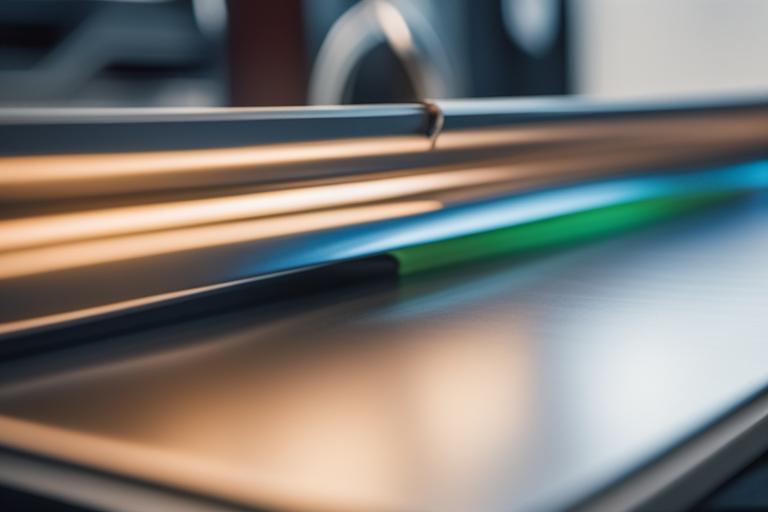
Design and Engineering for Sheet Metal Fabrication
Effective design and engineering are fundamental to successful sheet metal fabrication. Creating detailed engineering drawings or computer-aided design (CAD) files is crucial to ensure accurate and efficient manufacturing processes. These drawings provide fabricators with essential information about part geometry, tolerances, and assembly requirements.
Collaboration between designers and engineers is vital during the design phase to optimize the manufacturability of sheet metal parts. By working together, they can identify potential issues early on and make necessary design adjustments to streamline the fabrication process. Utilizing design software and simulation tools further enhances the ability to validate designs before fabrication.
To enhance your design and engineering skills, it’s beneficial to stay updated with the latest advancements in CAD software and simulation tools. These tools can significantly improve the efficiency and accuracy of the design process, ultimately leading to better outcomes in sheet metal fabrication. Additionally, exploring resources like Protolabs’ Sheet Metal Fabrication Service can provide valuable insights and expertise in design optimization for fabrication.
Cutting Techniques | Description |
---|---|
Laser cutting | Uses a high-powered laser beam to accurately cut through sheet metal. |
Waterjet cutting | Employs a high-pressure stream of water mixed with abrasive materials to cut through the metal. |
CNC punching | Uses a machine equipped with multiple tools to punch holes and create complex shapes in the metal. |
Forming Techniques | Description |
---|---|
Press brakes | Applies force to bend the metal along specific lines. |
Roll-forming machines | Gradually shapes the metal by passing it through a series of rollers. |
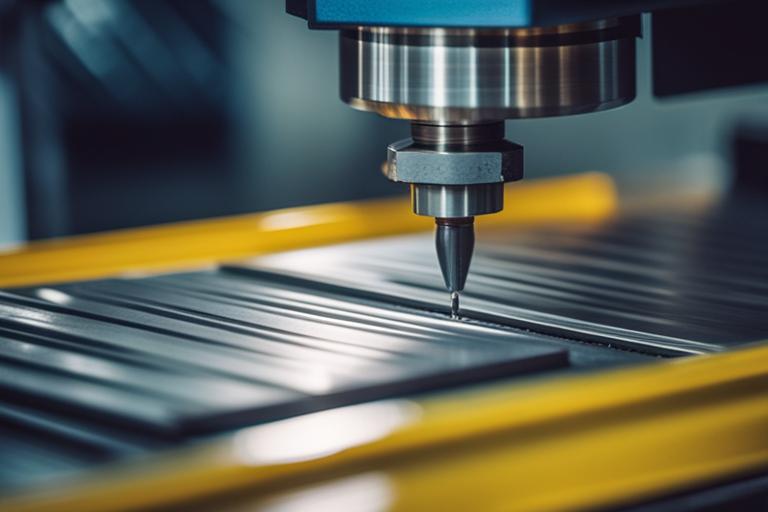
Cutting and Forming Techniques
Cutting and forming are two essential techniques in sheet metal fabrication. Various cutting techniques are employed depending on the complexity of the design and the desired level of precision. Laser cutting, waterjet cutting, and computer numerical control (CNC) punching are commonly used methods.
Laser cutting utilizes a high-powered laser beam to accurately cut through the sheet metal. It offers excellent precision and is suitable for both simple and intricate designs. Waterjet cutting, on the other hand, employs a high-pressure stream of water mixed with abrasive materials to cut through the metal. This technique is ideal for materials that are sensitive to heat, such as plastic-coated metals or heat-treated alloys.
CNC punching involves using a machine equipped with multiple tools to punch holes and create complex shapes in the sheet metal. It is a cost-effective method suitable for high-volume production.
Once the cutting process is complete, the next step is to form the sheet metal into the desired shape. This is done using tools like press brakes and roll-forming machines. Press brakes apply force to bend the metal along specific lines, while roll-forming machines gradually shape the metal by passing it through a series of rollers.
Precise measurements and proper tooling selection are crucial in achieving accurate and consistent results. Computer-controlled machines are often used to ensure precise and repeatable cutting and forming operations. These machines can greatly enhance the efficiency and quality of sheet metal fabrication.
For a more detailed understanding of cutting and forming techniques in sheet metal fabrication, you can refer to the Sheet Metal Fabrication Guide provided by Hubs.
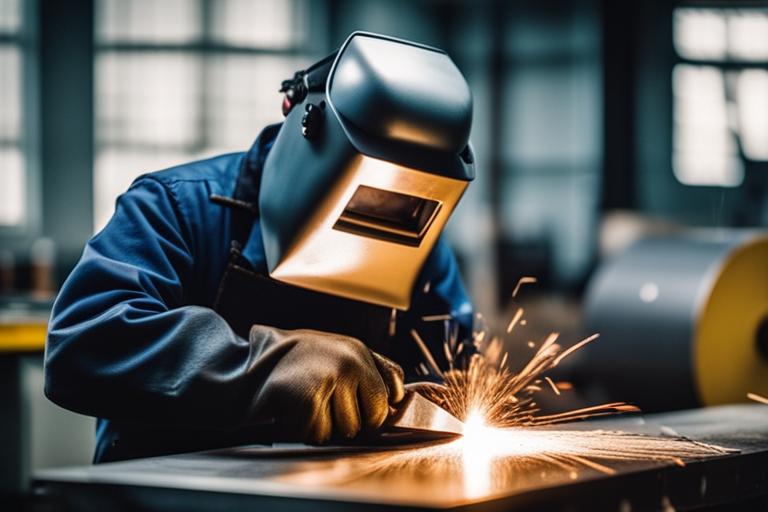
Joining and Assembly Methods
Joining and assembly are critical steps in sheet metal fabrication, as they determine the structural integrity and functionality of the final product. Various methods are employed to join sheet metal parts, including welding, riveting, and adhesive bonding.
Welding is a popular technique that involves melting the edges of the metal parts and fusing them together. It provides strong and durable joints, making it suitable for load-bearing applications. Riveting involves using metal fasteners to join the parts, while adhesive bonding utilizes specialized adhesives to create a bond between the surfaces.
Proper fit-up and alignment during the assembly process are essential to ensure the integrity of the final product. Jigs, fixtures, and welding robots are often utilized to improve efficiency and accuracy in the assembly process. These tools help ensure consistent and precise positioning of the parts during joining.
Quality control is of utmost importance during the joining and assembly stages. Inspecting the fit and finish of the assembled parts, as well as conducting tests to verify structural integrity, are crucial steps in ensuring the overall quality of the fabricated product.
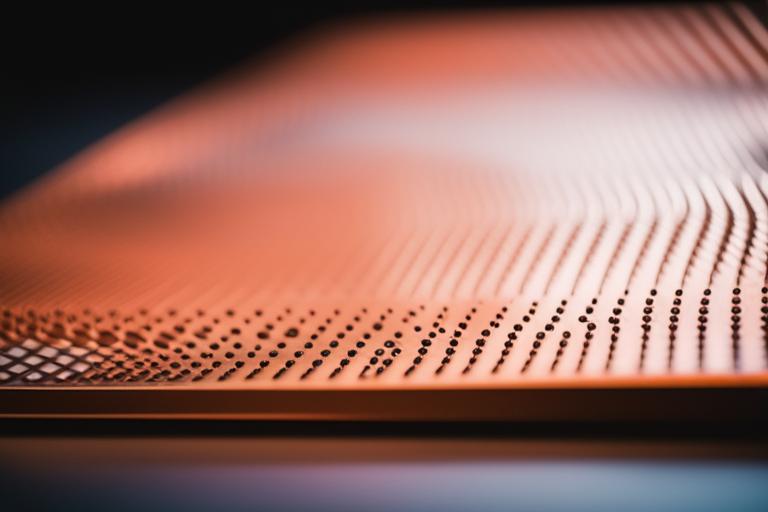
Surface Finishing and Coating Options
Surface finishing plays a significant role in sheet metal fabrication, providing both aesthetic appeal and enhanced functionality. There are various surface finishing options available, including powder coating, plating, and anodizing.
Powder coating involves applying a dry powder to the surface of the sheet metal and then heating it to form a protective layer. This technique offers excellent durability, corrosion resistance, and a wide range of color options.
Plating involves depositing a thin layer of metal onto the surface of the sheet metal. This process enhances the appearance, corrosion resistance, and electrical conductivity of the parts. Common plating materials include zinc, nickel, and chromium.
Anodizing is an electrochemical process that creates an oxide layer on the surface of aluminum. This oxide layer provides improved corrosion resistance and can be dyed to achieve various colors.
Proper cleaning and preparation of the sheet metal before applying surface finishes are crucial to ensure adhesion and longevity. Masking techniques may be employed to protect specific areas from being coated or finished, allowing for selective treatment.
For more information on surface finishing and coating options in sheet metal fabrication, you can refer to the Sheet Metal Fabrication 101 Guide provided by RapidDirect.
Case Study: Optimizing Sheet Metal Design for Efficiency and Cost Savings
At XYZ Manufacturing, we recently had a project that required the fabrication of a complex sheet metal part for a new product. Our team of designers and engineers collaborated closely to optimize the design for efficiency and cost savings.
The part had intricate geometries and required multiple bends and cutouts. We knew that it was crucial to create detailed engineering drawings and CAD files to ensure accurate fabrication. By utilizing design software and simulation tools, we were able to validate the design before moving forward with production.
During the design phase, we focused on reducing material waste and minimizing the number of operations required for fabrication. By making small adjustments to the part’s geometry, we were able to eliminate unnecessary features and streamline the production process.
Additionally, our team paid close attention to tolerances and assembly requirements. We knew that precise measurements and proper fit-up were essential for achieving structural integrity. We used computer-controlled machines to ensure consistent and accurate cutting and forming operations.
By optimizing the design and engineering aspects of the sheet metal part, we were able to achieve significant cost savings and improve overall efficiency. The reduced material waste and streamlined production process resulted in shorter lead times and increased customer satisfaction.
This case study highlights the importance of collaboration between designers and engineers in sheet metal fabrication. By considering factors such as part geometry, tolerances, and assembly requirements, we were able to optimize the design for efficiency and cost savings. Utilizing design software and simulation tools further enhanced the manufacturability of the part. By focusing on continuous improvement and staying updated with the latest advancements in sheet metal fabrication techniques and technologies, we were able to deliver high-quality products to our customers.
Quality Control in Sheet Metal Fabrication
Maintaining high-quality standards is essential in sheet metal fabrication to ensure the dimensional accuracy and functionality of the fabricated parts. Quality control measures are implemented throughout the fabrication process to identify and rectify any deviations or defects.
Inspection tools and techniques, such as coordinate measuring machines (CMM) and visual inspections, are commonly used to verify the dimensional accuracy of the fabricated parts. CMMs provide precise measurements by capturing data points and comparing them to the design specifications.
Rigorous testing is conducted to ensure that the fabricated parts meet industry standards and customer requirements. This may involve destructive testing, non-destructive testing, or performance testing, depending on the application and regulatory requirements.
Statistical process control (SPC) methods are often employed to monitor and improve the fabrication process. SPC involves collecting and analyzing data during production to identify trends, detect defects, and make necessary adjustments to maintain consistent quality.
By applying these expert tips and techniques, you can enhance your skills and knowledge in sheet metal fabrication. Whether you’re a beginner or an experienced professional, continuous learning and improvement are key to mastering this versatile field. So, start implementing these strategies in your fabrication processes and take your skills to new heights.
Frequently Asked Questions
What is sheet metal fabrication?
Sheet metal fabrication is the process of shaping and manipulating metal sheets to create various products.
Who can benefit from precision sheet metal fabrication?
Industries such as automotive, aerospace, and electronics greatly benefit from precision sheet metal fabrication.
How is sheet metal fabricated with precision?
Precision sheet metal fabrication involves using advanced tools and techniques to ensure accurate measurements and cuts.
What are the advantages of precision sheet metal fabrication?
Precision fabrication ensures high-quality products, durability, and a perfect fit for specific applications.
How long does it take to complete a sheet metal fabrication project?
The time required for a sheet metal fabrication project varies based on complexity, design, and the size of the project.
What if I have specific design requirements for my sheet metal project?
Professional fabricators can work closely with you to meet your specific design requirements and provide custom solutions.