Custom metal fabrication is a specialized process that involves the creation of metal products tailored to meet specific requirements. Whether it’s a unique design or a complex structure, custom metal fabrication offers a range of possibilities for creating high-quality metal products. In this article, we will explore the world of custom metal fabrication, its benefits and applications, the process involved, and how to choose the right custom metal fabricator.
What the reader will learn by reading this article:
- The significance of custom metal fabrication and the various techniques used.
- The benefits and applications of choosing custom metal fabrication.
- Factors to consider when selecting a custom metal fabricator and the importance of strategic material sourcing partnerships.
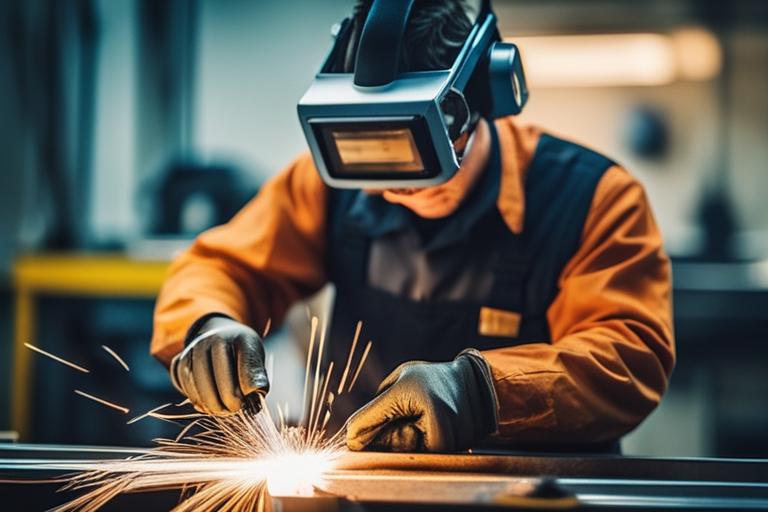
Understanding Custom Metal Fabrication
Custom metal fabrication is the process of transforming raw materials into finished metal products that are customized to meet specific needs. It involves the use of advanced techniques and machinery to shape, cut, and assemble metal components. The goal of custom metal fabrication is to create products that are not readily available in the market or to improve upon existing designs to achieve better performance and functionality.
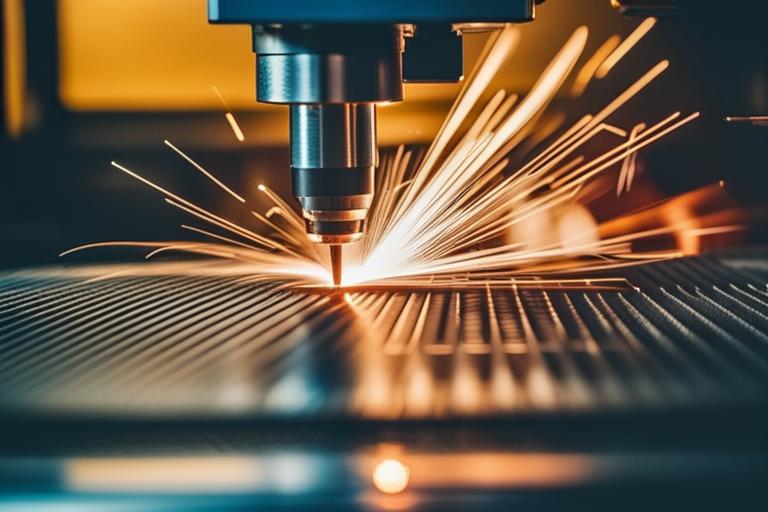
Techniques Used in Custom Metal Fabrication
Custom metal fabrication utilizes a variety of techniques to achieve the desired outcome. One of the most common techniques is laser cutting, which uses a high-powered laser beam to precisely cut through metal sheets. Laser cutting offers unmatched precision and allows for intricate designs and complex shapes to be achieved.
CNC punching is another technique used in custom metal fabrication. It involves the use of a computer-controlled machine to punch holes and create patterns in metal sheets. This technique is ideal for large-scale production and ensures consistent accuracy.
Forming is the process of bending or shaping metal sheets to create three-dimensional structures. This technique is often used to create curves, angles, and complex geometries. Rolling, on the other hand, involves passing metal sheets through rollers to achieve a desired thickness or shape.
Welding plays a crucial role in custom metal fabrication as it involves joining metal components together. Welding techniques such as MIG (Metal Inert Gas) and TIG (Tungsten Inert Gas) welding are commonly used to create strong and durable connections between metal parts.
Finishing is the final step in the custom metal fabrication process. It involves surface treatment techniques such as sanding, polishing, painting, or powder coating to enhance the appearance and protect the metal product from corrosion.
Technique | Description |
---|---|
Laser Cutting | Uses a high-powered laser beam to precisely cut through metal sheets, allowing for intricate designs and complex shapes. |
CNC Punching | Utilizes a computer-controlled machine to punch holes and create patterns in metal sheets, ensuring consistent accuracy. |
Forming | Bends or shapes metal sheets to create three-dimensional structures, often used for curves, angles, and complex geometries. |
Rolling | Passes metal sheets through rollers to achieve a desired thickness or shape. |
Welding (MIG, TIG) | Joins metal components together using techniques such as Metal Inert Gas (MIG) and Tungsten Inert Gas (TIG) welding. |
Finishing | Applies surface treatment techniques like sanding, polishing, painting, or powder coating to enhance appearance and prevent corrosion. |
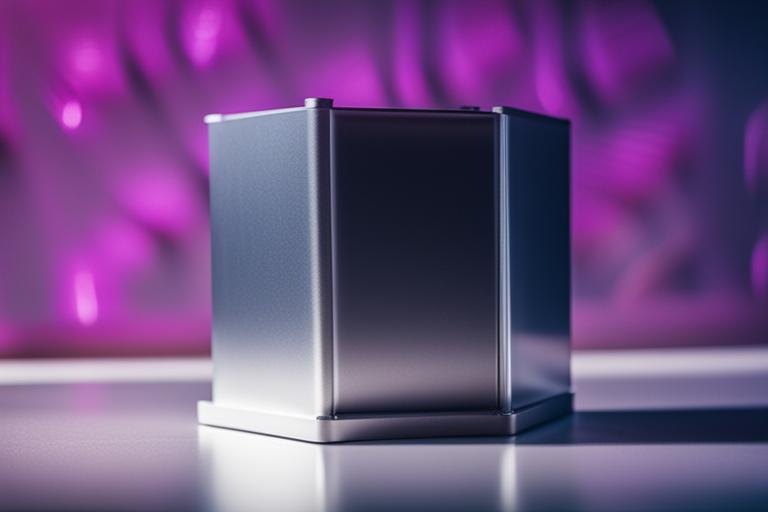
Benefits and Applications of Custom Metal Fabrication
Choosing custom metal fabrication over off-the-shelf products offers a range of benefits. One of the key advantages is the ability to customize the product to meet specific requirements. Custom metal fabrication allows for unique designs, sizes, and functionalities that are tailored to the customer’s needs. This level of customization is not possible with mass-produced products.
In addition to customization, custom metal fabrication also offers superior quality. Each product is carefully crafted and undergoes strict quality control measures throughout the fabrication process. This ensures that the final product meets the highest standards of durability, precision, and functionality.
Furthermore, custom metal fabrication can be a cost-effective solution in the long run. While the initial investment may be higher compared to off-the-shelf products, custom-made metal products are often more durable and require less maintenance. This can result in significant cost savings over time.
Applications of Custom Metal Fabrication
Custom metal fabrication finds applications in a wide range of industries and sectors. One of the prominent industries that benefit from custom metal fabrication is the automotive industry. Custom metal fabricators play a crucial role in creating specialized parts and components for vehicles, including chassis, frames, and exhaust systems.
The aerospace industry is another sector where custom metal fabrication is of utmost importance. The ability to create lightweight, yet strong metal structures is crucial in the aerospace industry. Custom metal fabrication techniques ensure that aircraft components are designed to withstand extreme conditions and meet stringent safety standards.
The electronics industry also relies on custom metal fabrication for the production of specialized enclosures, racks, and brackets for electronic devices. The precision and customization offered by custom metal fabrication ensure that electronic components are protected and properly housed.
The architecture and construction industry also benefits from custom metal fabrication. From decorative metal works to structural elements, custom metal fabricators provide the necessary expertise to create unique and visually appealing metal structures that enhance the overall design.
Specific Applications
One specific application that showcases the capabilities of custom metal fabrication is the construction of commercial grain elevators and feed mills. These structures require precision sheet metal work to create the bins, chutes, and conveyors needed for grain storage and processing. Custom metal fabricators specialize in designing and fabricating these large-scale structures, ensuring efficiency, durability, and safety.
Choosing the Right Custom Metal Fabricator
Selecting the right custom metal fabricator is crucial for the success of your project. There are several factors to consider when making this decision.
Experience and Expertise
First and foremost, consider the fabricator’s experience and expertise in the field of custom metal fabrication. Look for a company that has a long-standing reputation and a track record of delivering high-quality products. An experienced fabricator will have the necessary knowledge and skills to handle complex projects and provide innovative solutions.
Certifications and Quality Control
Check if the custom metal fabricator holds relevant certifications and complies with industry standards. Certifications such as ISO 9001 demonstrate a commitment to quality and adherence to strict quality control processes. A fabricator with certifications ensures that your product will meet the required specifications and undergoes thorough inspections at every stage of the fabrication process.
Equipment and Capabilities
Evaluate the fabricator’s equipment and capabilities to ensure they can handle your project requirements. Advanced machinery and technology are essential for precision sheet metal work. Additionally, consider the fabricator’s range of capabilities, including laser cutting, CNC punching, welding, and finishing. A fabricator with a diverse set of capabilities can offer comprehensive solutions and deliver a wide range of products.
Material Sourcing Partnerships
Another important factor to consider is the fabricator’s material sourcing partnerships. Strategic partnerships with top material suppliers ensure competitive pricing and availability of the required materials. This can significantly impact the overall cost and timeline of your project.
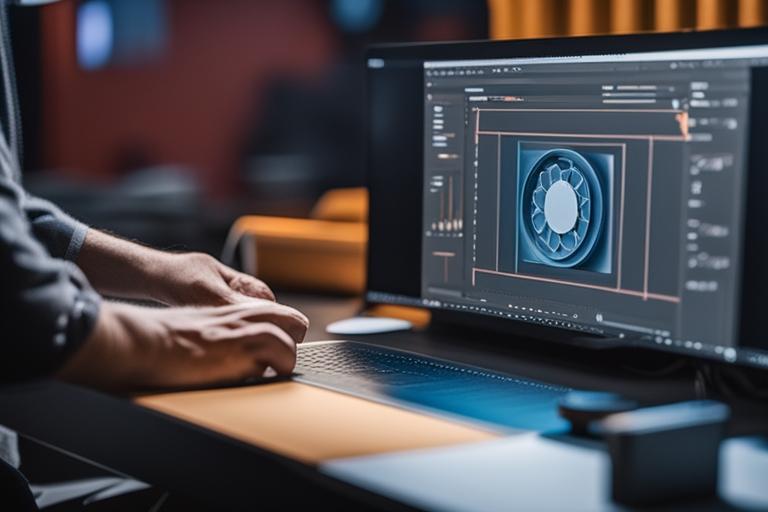
Designing the Custom Metal Product
The design phase of custom metal fabrication is a collaborative process between the customer and the fabricator. Clear communication and a detailed understanding of the project requirements are essential for a successful outcome.
Utilizing CAD Tools
To facilitate the design process, custom metal fabricators utilize Computer-Aided Design (CAD) tools such as AutoCAD, Rhino, Fusion 360, and SOLIDWORKS. These tools enable fabricators to create accurate 3D models of the desired product, allowing for better visualization and fine-tuning of the design.
Advanced Design Techniques
Advanced design techniques such as surface modeling, solid modeling, piping design, and finite element analysis play a crucial role in custom metal fabrication. Surface modeling enables the creation of smooth and complex shapes, while solid modeling ensures structural integrity and dimensional accuracy. Piping design is vital for projects that involve fluid flow, such as in the oil and gas industry. Finite element analysis helps optimize the design by simulating the behavior of the metal structure under various conditions.
Material Selection and Sourcing
Choosing the right material is key to the success of any custom metal fabrication project. Different metals offer varying properties that determine their suitability for specific applications.
Commonly Used Metals
Carbon steel, stainless steel, and aluminum are among the most commonly used metals in custom metal fabrication. Carbon steel is known for its strength and affordability, making it suitable for a wide range of applications. Stainless steel is highly resistant to corrosion and offers excellent aesthetic appeal, making it ideal for architectural and decorative projects. Aluminum is lightweight and has good thermal and electrical conductivity, making it a popular choice in industries such as aerospace and electronics.
Strategic Material Sourcing
To ensure competitive pricing and availability of materials, custom metal fabricators often establish strategic partnerships with top material suppliers. These partnerships allow fabricators to access high-quality materials at favorable prices, ultimately benefiting the customer in terms of cost and lead time.
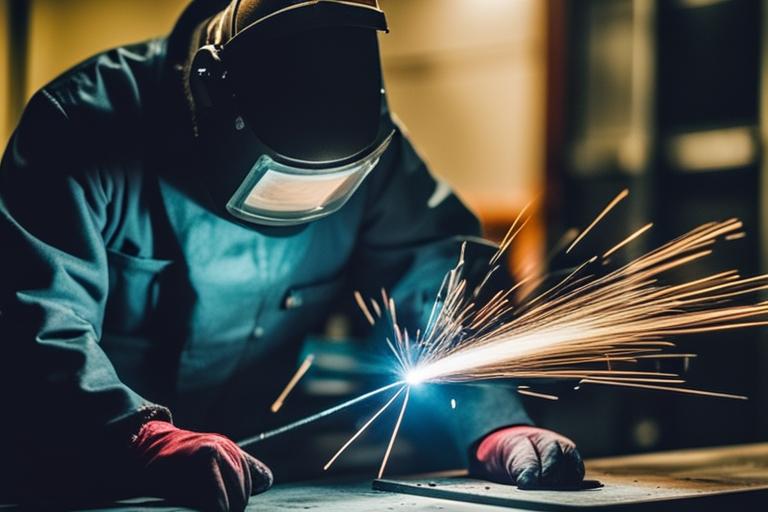
Custom Metal Fabrication Process
The custom metal fabrication process involves several steps, each essential to the creation of a high-quality metal product.
Step-by-Step Breakdown
- Design: The process begins with the design phase, where the customer’s requirements are translated into detailed plans and specifications. CAD tools are utilized to create accurate 3D models.
- Material Selection: The appropriate material is chosen based on factors such as strength, durability, corrosion resistance, and aesthetic appeal.
- Material Preparation: The selected material is prepared by cutting it into the required dimensions, either manually or using advanced cutting techniques such as laser cutting or CNC punching.
- Forming and Shaping: The metal sheets are bent, formed, or shaped using specialized machinery and tools to achieve the desired geometry.
- Joining: Metal components are joined together using various welding techniques such as MIG or TIG welding. This step ensures the structural integrity and strength of the final product.
- Finishing: The fabricated metal product undergoes surface treatment processes such as sanding, polishing, painting, or powder coating to enhance its appearance and protect it from corrosion.
- Quality Control: Throughout the fabrication process, strict quality control measures are implemented to ensure that the final product meets the required specifications. Inspections are conducted at each stage to identify and rectify any potential issues.
- Delivery: Once the fabrication process is complete, the finished product is carefully packaged and delivered to the customer, ready for installation or use.
Case Studies and Success Stories
Real-life examples of successful custom metal fabrication projects demonstrate the versatility and capabilities of precision sheet metal fabrication.
One such example is the fabrication of custom-designed metal brackets for an automotive company. The custom metal fabricator worked closely with the customer to understand their requirements and design specifications. Utilizing advanced CAD tools and precision sheet metal fabrication techniques, the fabricator was able to create brackets that perfectly fit the customer’s unique application. The brackets were not only aesthetically pleasing but also met the required strength and durability standards.
Another success story involves the creation of custom metal enclosures for electronic devices. The custom metal fabricator collaborated with the customer to design and fabricate enclosures that provided optimal protection for sensitive electronic components. The use of advanced surface modeling and solid modeling techniques ensured that the enclosures were not only functional but also visually appealing. The end result was a series of custom metal enclosures that met the customer’s specifications and exceeded their expectations.
Personal Story: The Power of Collaboration in Custom Metal Fabrication
During my time working in the custom metal fabrication industry, I had the opportunity to collaborate with a client on a unique project that truly showcased the power of collaboration in creating exceptional metal products. The client, John, owned a small winery and wanted to design a custom wine rack that would not only showcase his bottles but also add a touch of elegance to his tasting room.
In the initial design phase, John and I sat down to discuss his vision and requirements for the wine rack. He wanted a sleek, modern design that could hold a large number of bottles while still being visually appealing. Using CAD tools, we were able to bring his ideas to life, exploring different surface and solid modeling options until we found the perfect design.
Once the design was finalized, the fabrication process began. We utilized laser cutting and CNC punching techniques to precisely cut and shape the metal components for the wine rack. The custom-formed metal pieces were then welded together to create a sturdy frame that could support the weight of the wine bottles.
Throughout the fabrication process, John was actively involved, visiting the workshop frequently to provide feedback and ensure that his vision was being brought to life. This collaboration allowed us to make adjustments and fine-tune the design along the way, resulting in a final product that exceeded John’s expectations.
The finished wine rack was not only functional but also a work of art. It added a touch of sophistication to John’s tasting room and became a conversation piece among his patrons. Seeing the satisfaction on John’s face and hearing the positive feedback from his customers was incredibly rewarding and reinforced the importance of collaboration in the custom metal fabrication process.
This project was a testament to the power of collaboration between the customer and the fabricator. By working closely together, we were able to create a custom metal product that perfectly met John’s needs and brought his vision to life. It highlighted the endless possibilities of precision sheet metal fabrication and the ability to create truly unique and personalized metal products.
Quality Assurance and Certifications
Quality assurance plays a crucial role in custom metal fabrication. Fabricators employ various measures to ensure that the final product meets the highest standards of quality and durability.
One important aspect of quality assurance is the implementation of industry standards and certifications. Certifications such as ISO 9001 demonstrate a fabricator’s commitment to quality and adherence to strict quality control processes. These certifications provide customers with the assurance that their custom metal products have been fabricated using the best practices and meet the required specifications.
Conclusion
Custom metal fabrication offers a world of possibilities for creating high-quality metal products that are tailored to specific requirements. From automotive components to architectural structures, precision sheet metal fabrication plays a vital role in various industries. By choosing the right custom metal fabricator, collaborating in the design phase, and utilizing advanced techniques, customers can achieve superior quality, durability, and functionality in their metal products. The future of custom metal fabrication looks promising, with continuous advancements in technology and the ever-growing demand for specialized metal products.
.