Metal fabrication has been around for centuries, involving the creation of metal structures through cutting, bending, and assembling processes. However, with the rise of precision sheet metal fabrication, the industry has transformed significantly. In this article, we will explore the different techniques involved in metal fabrication, the raw materials used, and the future of this industry.
Precision Sheet Metal Fabrication: Key Points
By reading this article, you will learn:
– About the different techniques used in metal fabrication including cutting, bending, welding, and finishing
– The importance of quality control in metal fabrication and its role in ensuring accuracy and consistency in finished products
– How metal fabrication plays a crucial part in various industries and modern manufacturing, as well as advancements in automation and robotics in the field.

Raw Materials
Metal fabrication involves the use of different types of metals, including steel, aluminum, copper, and brass. The selection of the metal depends on the intended use of the finished product. For example, steel is preferred for structural applications due to its strength, while aluminum is used for lightweight applications due to its low density. Other factors to consider when selecting the metal include its ductility, hardness, and machinability.
Sourcing raw materials for metal fabrication can be a complex process due to the variety of metals used. Some fabrication shops may purchase raw materials from suppliers, while others may have their metalworking facilities. Additionally, some metals, such as copper and brass, may be more challenging to source than others due to their scarcity or high cost.
One resource for sheet metal fabrication is Precision Metal Fabrication and Weldments, Inc.. They offer precision metal fabrication services, including sheet metal fabrication and laser cutting. They also provide secondary services such as assembly, CNC laser cutting, CNC punching, and welding. The company is veteran-owned and has capabilities in design support, forming, painting, prototyping, and more. They showcase various completed projects and aim to provide quality products and services with a focus on customer satisfaction.
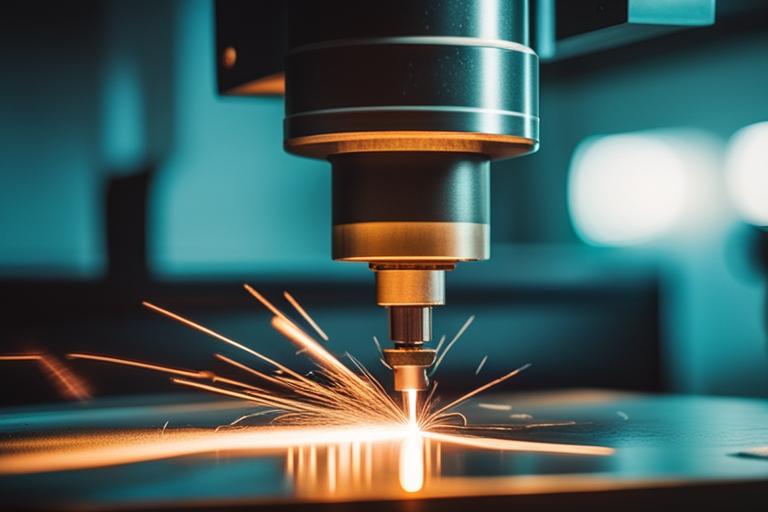
Cutting Techniques
Cutting is a crucial step in metal fabrication, and it involves separating the metal into the desired shape and size. There are various cutting techniques, ranging from manual to automated processes. Manual cutting techniques include sawing and shearing, while automated techniques include laser cutting, water jet cutting, and plasma cutting.
Laser cutting is a popular technique in sheet metal fabrication due to its precision and speed. It involves using a high-powered laser to cut through the metal, and it can cut through a variety of metals, including steel, aluminum, and titanium. Water jet cutting, on the other hand, uses a high-pressure stream of water and abrasive material to cut through the metal. Plasma cutting involves using a plasma torch to melt the metal, creating a clean cut.
The choice of cutting technique depends on factors such as the metal thickness, the desired accuracy, and the complexity of the design. For example, laser cutting is preferred for intricate designs, while water jet cutting is preferred for thicker materials.
One resource for sheet metal cutting is Capabilities. They offer sheet metal punching services, which involves using a die and punch to create holes and other shapes in the metal. They also offer sheet metal forming and welding services.
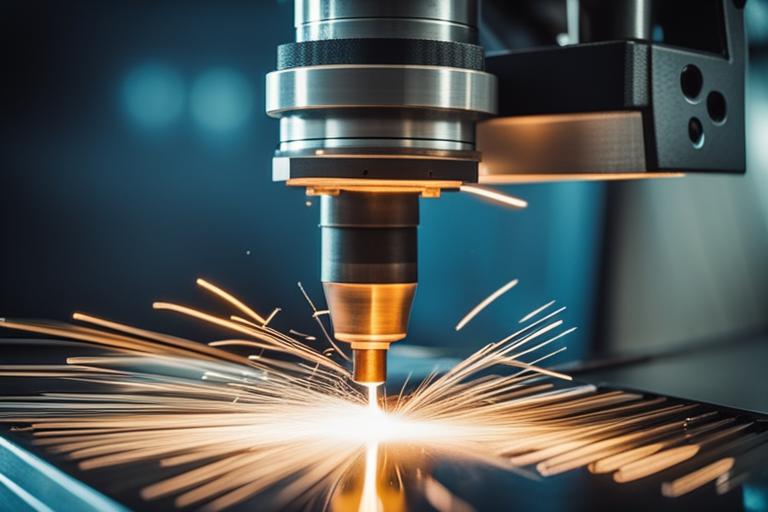
Bending and Forming Techniques
Bending and forming are essential processes in metal fabrication, and they involve shaping the metal into the desired shape. There are various bending and forming techniques, ranging from manual to automated processes. Manual techniques include press brakes and roll forming, while automated techniques include CNC bending and stamping.
Press brakes are the most common bending technique in sheet metal fabrication. They involve using a machine to apply force to the metal to create a bend, and they can create bends with different angles and shapes. Roll forming involves feeding the metal through a series of rollers to create a uniform shape, such as a tube or a channel.
Stamping involves using a die and punch to create a shape in the metal, and it is often used in mass production. CNC bending involves using a computer-controlled machine to create precise bends in the metal.
The choice of bending and forming technique depends on factors such as the metal thickness, the desired accuracy, and the complexity of the design. For example, press brakes are preferred for creating simple bends, while CNC bending is preferred for creating complex shapes.
One resource for sheet metal forming is Capabilities. They offer sheet metal forming services, including press brakes, roll forming, and CNC bending. They also offer welding services.
Bending and Forming Techniques | Welding Techniques |
---|---|
Press brakes | MIG welding |
Roll forming | TIG welding |
CNC bending | Stick welding |
Stamping | Robotic welding |
Welding Techniques
Welding is a crucial step in metal fabrication, and it involves joining two or more pieces of metal together. There are various welding techniques, ranging from manual to automated processes. Manual techniques include MIG, TIG, and stick welding, while automated techniques include robotic welding.
MIG welding involves using a wire feed to join the metal, while TIG welding involves using a tungsten electrode to create the weld. Stick welding involves using a stick electrode to create the weld, and it is often used in outdoor applications due to its portability. Robotic welding involves using a robot to create the weld, and it is preferred for high-volume production.
The choice of welding technique depends on factors such as the metal thickness, the desired strength, and the complexity of the design. For example, MIG welding is preferred for thinner metals, while TIG welding is preferred for thicker metals.
One resource for welding services is Capabilities. They offer various welding services, including MIG, TIG, and stick welding. They also offer welded assemblies.
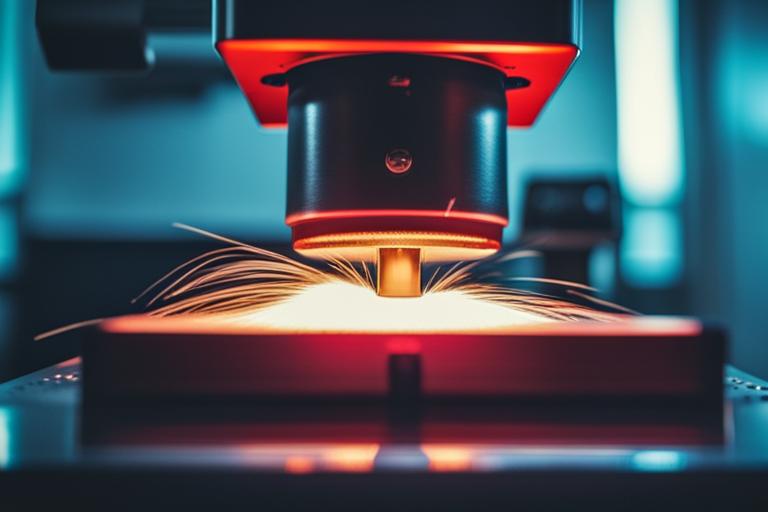
Finishing Techniques
Finishing is the final step in metal fabrication, and it involves preparing the metal surface for the desired finish. There are various finishing techniques, ranging from surface preparation to coating and plating.
Surface preparation techniques include sandblasting and grinding, which involve removing any surface imperfections. Coating techniques include powder coating and painting, which involve applying a layer of coating to the metal surface to protect it from corrosion. Plating techniques involve applying a layer of metal, such as chrome or gold, to the metal surface to improve its appearance.
The choice of finishing technique depends on factors such as the desired appearance, the intended use of the finished product, and the cost. For example, powder coating is preferred for outdoor applications due to its durability, while painting is preferred for indoor applications.
One resource for finishing techniques is Precision Metal Fabrication and Weldments, Inc.. They offer various finishing services, including powder coating and painting.
Quality Control
Quality control is an essential aspect of metal fabrication, and it involves ensuring that the finished product meets the desired specifications. There are various inspection techniques and equipment used in quality control, including visual inspection, coordinate measuring machines (CMMs), and ultrasonic testing.
Visual inspection involves visually inspecting the finished product for any defects, while CMMs involve using a computer-controlled machine to measure the product’s dimensions. Ultrasonic testing involves using high-frequency sound waves to inspect the product for any internal defects.
Ensuring accuracy and consistency in the finished product is crucial in metal fabrication, as it can affect the product’s performance and safety.
Case Study: Precision Sheet Metal Fabrication in the Automotive Industry
One of the most significant industries that rely heavily on metal fabrication is the automotive industry. A car manufacturer, XYZ Motors, wanted to create a specialized vehicle that required precise sheet metal fabrication.
The team of engineers at XYZ Motors worked with a precision sheet metal fabrication company, ABC Fabrication, to create the parts necessary for the vehicle. The team at ABC Fabrication used laser cutting techniques to create the precise shapes needed for the car parts. They then used automated bending and forming techniques to shape the metal into the exact specifications required.
The metal parts then went through a series of finishing techniques, including surface preparation and powder coating, to ensure the parts were ready for assembly. The parts were then inspected using advanced quality control techniques to ensure accuracy and consistency in the final product.
The precision sheet metal fabrication provided by ABC Fabrication allowed XYZ Motors to create a specialized vehicle that met their exact requirements. The use of metal fabrication techniques ensured that the parts were precise, durable, and suitable for the intended use.
This case study highlights the importance of precision sheet metal fabrication in the automotive industry and how it can provide companies with the exact parts they need to create specialized vehicles.
Applications of Metal Fabrication
Metal fabrication has various applications in different industries, including construction, automotive, aerospace, and manufacturing. Examples of products created through metal fabrication include structural beams, automotive parts, airplane components, and machinery.
One resource for metal fabrication services is OEM Fabrication. They specialize in OEM fabrication and offer various services, including sheet metal fabrication, welding, and finishing. They also offer design and engineering support.
Future of Metal Fabrication
The future of metal fabrication looks promising, with the rise of new technologies and techniques. Advancements in automation and robotics are making metal fabrication more efficient and cost-effective. For example, robots can perform repetitive welding tasks, freeing up human labor for more complex tasks.
Additionally, new materials, such as composites, are being used in metal fabrication, offering improved strength-to-weight ratios and corrosion resistance. The integration of 3D printing technology in metal fabrication is also becoming more prevalent, offering new possibilities in design and customization.
In conclusion, metal fabrication is an important process in various industries and involves the use of different techniques and equipment to create metal structures. The rise of precision sheet metal fabrication has transformed the industry, and with new advancements in technology and materials, the future of metal fabrication looks promising. Quality control is crucial to ensure safe and ethical practices, and there are various resources available for metal fabrication services.
Q & A
What is precision sheet metal fabrication?
Precision sheet metal fabrication is the process of cutting, bending, and assembling metal sheets with high accuracy.
Who can benefit from precision sheet metal fabrication?
Industries such as aerospace, medical, and electronics can benefit from precision sheet metal fabrication.
How does precision sheet metal fabrication differ from regular metal fabrication?
Precision sheet metal fabrication involves the use of specialized equipment and techniques to achieve high accuracy and tight tolerances.
What materials can be used in precision sheet metal fabrication?
Materials such as stainless steel, aluminum, copper, and brass can be used in precision sheet metal fabrication.
How long does it take to complete a precision sheet metal fabrication project?
The time it takes to complete a precision sheet metal fabrication project varies depending on the complexity and size of the project.
What if I need a custom design for my precision sheet metal fabrication project?
Our team of experts can work with you to create a custom design that meets your specific requirements and needs.