What You Will Learn:
- Understanding the process and importance of OEM metal fabrication services in precision sheet metal.
- The benefits of outsourcing OEM metal fabrication services.
- How to find the right contract manufacturer for OEM metal fabrication services.
Are you looking for high-quality metal components and products for your original equipment manufacturing (OEM) needs? Precision sheet metal fabrication is the answer. In this comprehensive guide, we will explore the world of OEM metal fabrication services, covering everything from understanding the process and its benefits to finding the right contract manufacturer, collaboration on design and engineering, material selection and sourcing, the manufacturing process, finishing and surface treatment, quality assurance and inspection, and packaging and delivery.
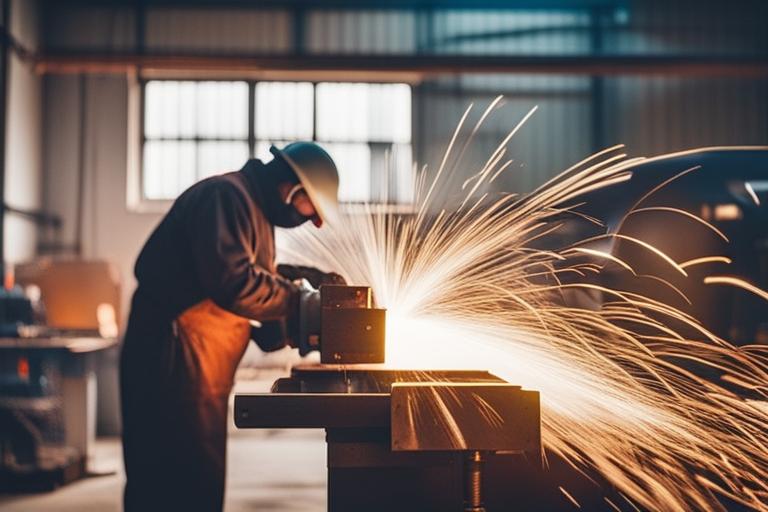
Understanding OEM Metal Fabrication Services
OEM metal fabrication services involve the production of metal components and products based on the specifications provided by the original equipment manufacturer. Industries such as agriculture, automotive, construction, medical, and more heavily rely on these services. The process typically starts with cutting metal sheets into desired shapes and sizes. Specialized equipment is then used to bend the metal sheets to achieve the desired angles and dimensions. Welding is employed to join the metal components together, ensuring structural integrity and durability. Finally, finishing processes such as painting, powder coating, plating, or anodizing are applied to protect the metal components from corrosion and enhance their appearance.
Precision and quality assurance are of utmost importance in OEM metal fabrication services. Each step of the process requires meticulous attention to detail to ensure that the final product meets the required specifications. Advanced machinery and equipment are used to achieve precise cuts, bends, and welds. Quality control measures are implemented to identify and rectify any defects or imperfections, ensuring that the finished product meets the highest standards.
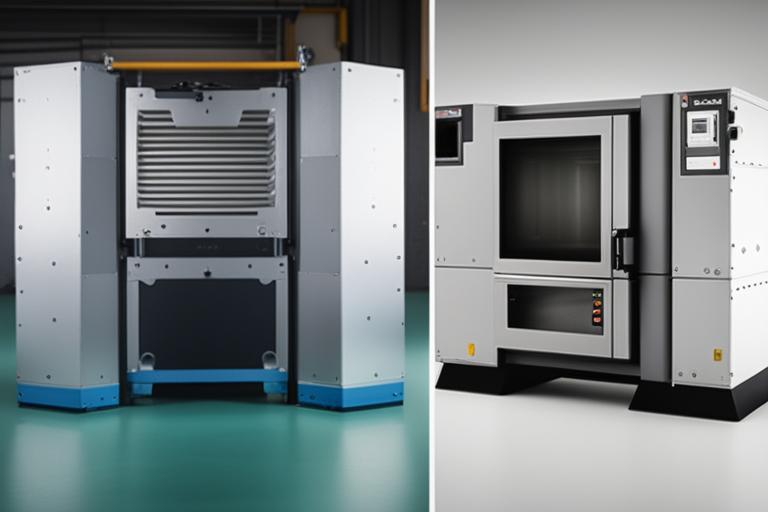
Benefits of Outsourcing OEM Metal Fabrication Services
Outsourcing OEM metal fabrication services brings numerous advantages to original equipment manufacturers. One key benefit is cost savings. By partnering with a contract manufacturer, OEMs can reduce overhead costs as they will not have to invest in expensive equipment, specialized facilities, or additional personnel. Contract manufacturers often benefit from economies of scale, enabling them to procure materials at lower costs and pass those savings on to their clients.
Increased efficiency is another advantage of outsourcing. Contract manufacturers specialize in metal fabrication and have the expertise and experience to optimize the manufacturing process. They employ advanced technologies and equipment to streamline operations, resulting in faster turnaround times and improved productivity. This enables OEMs to meet their production deadlines more effectively and enhance their overall operational efficiency.
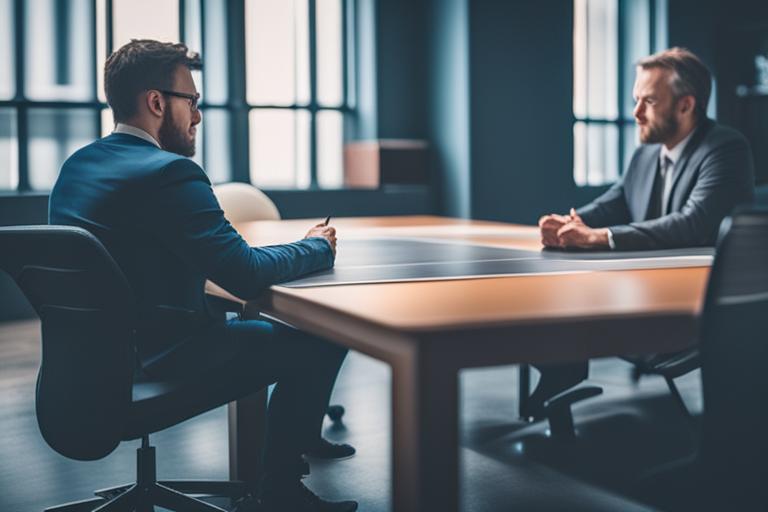
Finding the Right Contract Manufacturer for OEM Metal Fabrication Services
When searching for a contract manufacturer for OEM metal fabrication services, thorough research is crucial. It is essential to identify reputable companies with a proven track record in delivering high-quality products and services. Online directories, industry networks, and referrals from trusted sources can help in the selection process.
Capabilities, experience, and certifications are key factors to consider when evaluating potential contract manufacturers. The contract manufacturer should have a diverse range of fabrication capabilities, including cutting, bending, welding, and finishing. Their experience in working with various industries and materials is also important. Certifications such as ISO 9001:2015 indicate that the contract manufacturer adheres to internationally recognized quality management standards.
Assessing the equipment, technology, and quality control measures specific to OEM metal fabrication services is crucial. Advanced machinery and equipment contribute to precision and efficiency in metal fabrication. Additionally, the contract manufacturer should have robust quality control processes in place to ensure that the final product meets the required specifications. This may include inspection protocols, documentation of quality records, and adherence to industry standards.
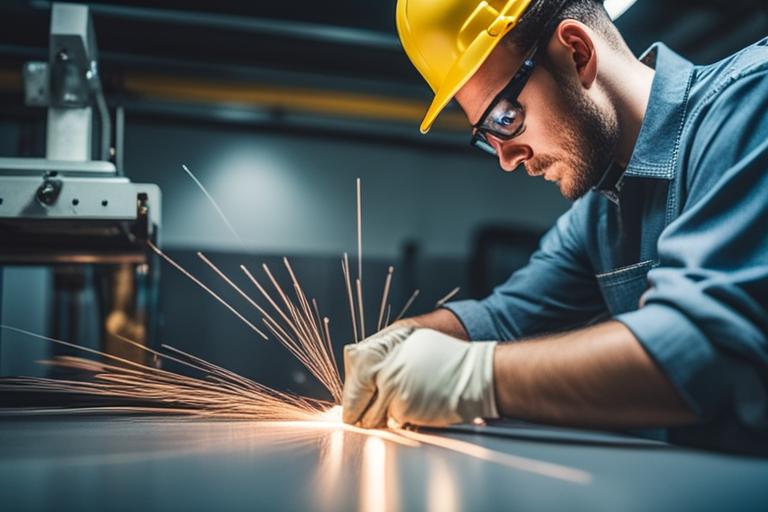
Collaboration on Design and Engineering for OEM Metal Fabrication Services
Collaboration between the OEM and the contract manufacturer’s engineering team is crucial for the success of OEM metal fabrication projects. The engineering team plays a vital role in translating the OEM’s product specifications into detailed manufacturing plans. By working closely together, both parties can optimize the design for efficient manufacturing and cost-effectiveness.
Computer-aided design (CAD) software is commonly used to facilitate collaboration and visualization during the design process. It allows for the creation of three-dimensional models that can be refined and modified based on feedback and requirements. This enhances communication and ensures that the final design meets the OEM’s expectations.
During the collaboration process, the contract manufacturer’s engineering team can provide valuable insights and suggestions to improve the manufacturability of the product. Their expertise helps identify potential design issues or challenges and propose alternative solutions. This proactive collaboration leads to the development of a robust and efficient manufacturing plan.
Section | Topic | Subtopics |
---|---|---|
IV | Collaboration on Design | – Importance of collaboration |
and Engineering | – Role of engineering team | |
for OEM Metal | – Use of CAD software | |
Fabrication Services | – Value of engineering insights and suggestions | |
——— | ——————————— | ——————————————————————————————– |
V | Material Selection and Sourcing | – Importance of material selection |
for OEM Metal | – Guidance from contract manufacturer | |
Fabrication Services | – Collaboration in material sourcing | |
– Consideration of cost, availability, and compliance | ||
– Established relationships with material suppliers |
Material Selection and Sourcing for OEM Metal Fabrication Services
Choosing the right materials is crucial in OEM metal fabrication services to ensure the desired strength, durability, and corrosion resistance of the final product. The contract manufacturer can provide guidance and expertise in material selection based on the project’s specific requirements. Factors such as cost, availability, and compliance with industry and regulatory standards should also be considered.
Collaboration with the contract manufacturer in material sourcing is essential to obtain high-quality materials at competitive prices. Contract manufacturers often have established relationships with material suppliers, enabling them to procure materials efficiently. This collaboration ensures that the OEM receives materials that meet the required specifications while optimizing costs.

Manufacturing and Production in OEM Metal Fabrication Services
The manufacturing process in OEM metal fabrication services involves a series of steps to transform raw materials into finished metal components or products. This includes cutting, bending, welding, and assembly. Advanced machinery and equipment are utilized to achieve precise and accurate results.
Cutting is the initial step in the manufacturing process, where metal sheets are cut into the desired shapes and sizes. This can be done through various methods such as laser cutting, plasma cutting, or waterjet cutting. Precision is crucial in this stage to ensure accurate dimensions and minimize material waste.
Bending is another critical step in OEM metal fabrication services. Specialized equipment, such as press brakes, is used to bend the metal sheets into the desired angles and shapes. The accuracy of the bends is essential to achieve the required dimensions and ensure proper fit and function of the final product.
Welding is employed to join metal components together. It is a crucial process that requires skilled welders and adherence to welding standards. Different welding techniques, such as MIG (Metal Inert Gas) welding or TIG (Tungsten Inert Gas) welding, may be used depending on the project’s requirements.
Once the metal components are cut, bent, and welded, they are assembled to form the final product. This may involve additional processes such as fastening, riveting, or bonding. The assembly process requires precision and attention to detail to ensure proper alignment and functionality.
Throughout the manufacturing process, strict quality control measures are implemented. Inspections and tests are conducted to verify that the components meet the required specifications. This ensures that the final product is of the highest quality and meets the OEM’s expectations.
Finishing and Surface Treatment in OEM Metal Fabrication Services
Finishing and surface treatment are essential steps in OEM metal fabrication services. These processes not only enhance the appearance of the final product but also provide protection against corrosion and wear.
Various finishing options are available, depending on the desired aesthetic and functional requirements. Painting is a common finishing method that provides both protection and customization options. Powder coating is another popular option that offers a durable and attractive finish. Plating or anodizing can be employed to improve corrosion resistance and provide decorative finishes.
Collaboration with the contract manufacturer is crucial in selecting the most suitable finishing method. The contract manufacturer can provide guidance based on their expertise and knowledge of different finishing techniques. Factors such as the intended use of the product, environmental conditions, and industry requirements should be considered when choosing a finishing method.
Quality Assurance and Inspection for OEM Metal Fabrication Services
Quality assurance is a critical aspect of OEM metal fabrication services. The contract manufacturer should have robust quality control measures in place to ensure that the final product meets the required specifications and industry standards.
Thorough inspections and tests are conducted throughout the manufacturing process to identify any defects or imperfections. This may include dimensional inspections, visual inspections, mechanical testing, or non-destructive testing methods such as ultrasonic testing or X-ray inspection. The results of these inspections and tests are documented to provide traceability and accountability.
Certifications such as ISO 9001:2015 indicate that the contract manufacturer has implemented quality management systems to consistently deliver high-quality products. These certifications provide reassurance to the OEM that the contract manufacturer follows internationally recognized quality standards.
In the event that any issues or defects are identified during the quality assurance process, corrective actions are implemented. This may involve reworking the components, replacing defective parts, or modifying the manufacturing process to prevent recurrence. Continuous improvement is a key aspect of quality assurance in OEM metal fabrication services.
Case Study: How Outsourcing OEM Metal Fabrication Services Improved Efficiency and Cost Savings
At XYZ Corporation, we were facing a challenge with our OEM metal fabrication services. Our in-house manufacturing processes were not as efficient as we had hoped, resulting in increased costs and longer production lead times. We recognized the need for a change and decided to explore the option of outsourcing our OEM metal fabrication services to a contract manufacturer.
After extensive research, we identified ABC Manufacturing as a reputable contract manufacturer specializing in precision sheet metal fabrication. Their capabilities, experience, and certifications aligned perfectly with our needs. We reached out to them and began a collaboration on our latest project.
During the design and engineering phase, we worked closely with ABC Manufacturing’s engineering team. They provided valuable insights and suggestions for optimizing our product design for efficient manufacturing and cost-effectiveness. Utilizing computer-aided design (CAD) software, we were able to visualize and refine the design to meet our specifications.
Material selection and sourcing were also key considerations. ABC Manufacturing helped us choose the most appropriate materials based on strength, durability, corrosion resistance, and cost. They had established relationships with suppliers, allowing us to source high-quality materials at competitive prices while ensuring compliance with industry and regulatory standards.
Once the manufacturing process began, we witnessed a significant improvement in efficiency. ABC Manufacturing utilized advanced machinery and equipment for precise cutting, bending, welding, and assembly. They adhered to strict quality control measures and industry standards, ensuring that each component met our specifications.
The finishing and surface treatment phase was equally impressive. ABC Manufacturing offered a range of finishing options such as painting, powder coating, plating, or anodizing. We collaborated with them to select the most suitable finish, considering aesthetics, corrosion resistance, and durability.
Throughout the entire project, ABC Manufacturing conducted thorough quality assurance and inspection processes. They conducted inspections and tests to ensure that the final product met our specifications. Any potential issues or defects were addressed promptly, and corrective actions were implemented.
When it came to packaging and delivery, ABC Manufacturing demonstrated their commitment to efficient supply chain management. They determined the appropriate packaging methods for safe transportation and coordinated logistics for on-time delivery to meet our project deadlines. Their tracking capabilities provided us with peace of mind, knowing that our products were in good hands.
By outsourcing our OEM metal fabrication services to ABC Manufacturing, we were able to achieve significant cost savings and increased efficiency. The collaboration between our teams resulted in a successful project that met our quality expectations. We now prioritize precision, quality, and collaboration in all our OEM metal fabrication services, ensuring that we maximize efficiency and deliver high-quality products to our customers.
Packaging and Delivery for OEM Metal Fabrication Services
Proper packaging and delivery are essential in ensuring that the finished products are transported safely to the OEM’s location. The contract manufacturer should determine the appropriate packaging methods based on the size, weight, and fragility of the products.
Coordinating logistics and on-time delivery is crucial to meet project deadlines. The contract manufacturer should have efficient supply chain management processes in place to ensure timely delivery. This may involve collaboration with shipping and logistics providers to optimize transportation routes and minimize transit times.
Tracking capabilities are important in packaging and delivery to provide visibility and transparency. The contract manufacturer should be able to provide updates on the shipment’s status and location, allowing the OEM to plan accordingly. Effective communication between the contract manufacturer and the OEM is key to ensuring a smooth and efficient delivery process.
Frequently Asked Questions
What is OEM metal fabrication?
OEM metal fabrication refers to the production of customized metal parts or products for original equipment manufacturers.
Who can benefit from precision sheet metal fabrication?
Manufacturers in various industries, such as automotive, aerospace, and electronics, can benefit from precision sheet metal fabrication.
How does precision sheet metal fabrication work?
Precision sheet metal fabrication involves cutting, bending, and assembling metal sheets to create customized products with high accuracy.
What are the advantages of OEM metal fabrication?
OEM metal fabrication offers cost-effective, high-quality, and reliable solutions tailored to specific manufacturing needs.
What if I need a unique design for my metal product?
Our team of experts in OEM metal fabrication can work with you to create a customized design that meets your specific requirements.
How can I ensure the quality of my precision sheet metal parts?
We employ strict quality control measures throughout the fabrication process to ensure the highest level of precision and durability.