What readers will learn from this article:
- The definition and purpose of custom enclosures in precision sheet metal fabrication
- The importance of proper design and fabrication techniques in creating custom enclosures
- Factors to consider when choosing a custom enclosure manufacturer
Are you curious about custom enclosures in precision sheet metal fabrication? Look no further! In this comprehensive handbook, we will explore the intricacies of custom enclosures and their significance in various industries. From design and fabrication processes to material selection and finishes, we will cover it all. By the end of this article, you will have a solid understanding of custom enclosures and their importance in safeguarding sensitive equipment.
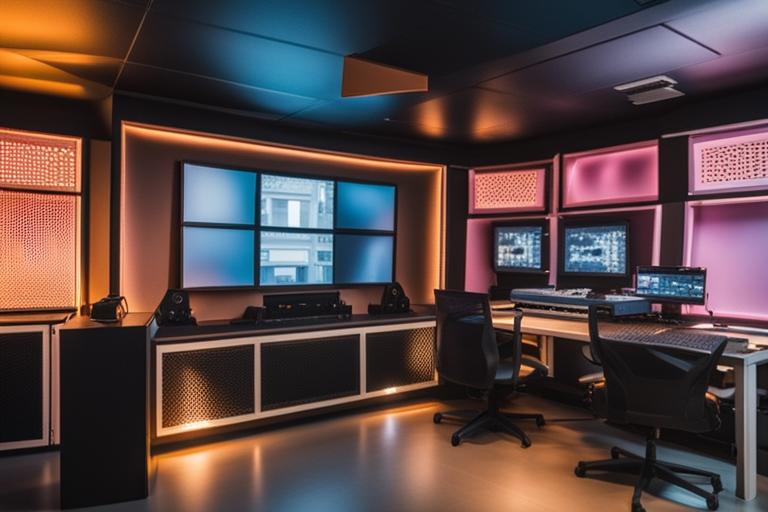
Understanding Custom Enclosures
A. Definition and Purpose of Custom Enclosures
Custom enclosures are specially designed and fabricated housings that provide protection and support for various equipment and components. These enclosures are tailored to meet specific requirements, ensuring a perfect fit and optimal functionality. Their primary purpose is to safeguard sensitive equipment from harsh environmental conditions, physical damage, and unauthorized access.
B. Industries that Utilize Custom Enclosures
Custom enclosures find application in a wide range of industries. In the electronics industry, they house delicate circuit boards and electronic components, protecting them from dust, moisture, and electromagnetic interference. In the automotive industry, custom enclosures house sophisticated audio systems and other electronic devices. Other industries that rely on custom enclosures include aerospace, telecommunications, medical, and industrial.
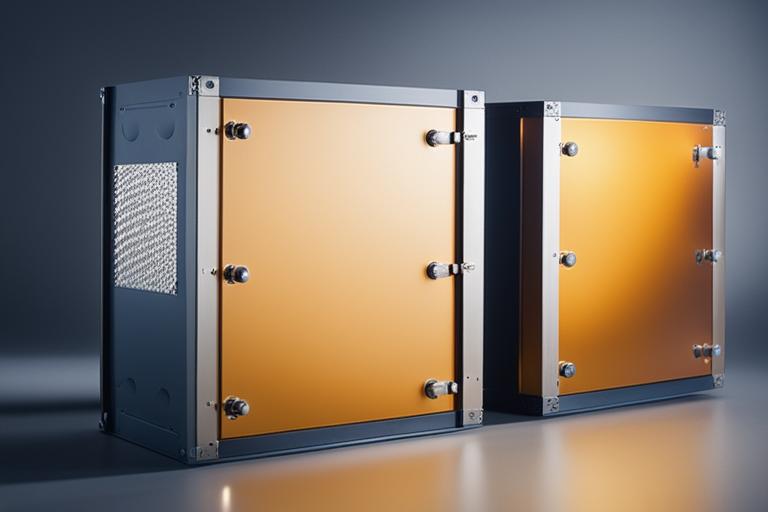
C. Types of Custom Enclosures
Custom enclosures come in various shapes and sizes, depending on the specific application and equipment being housed. Some common types include rack-mount enclosures, designed to fit into standard equipment racks, and chassis enclosures, which provide a complete housing solution for electronic devices. Wall-mounted enclosures are another popular option, offering a space-saving solution for easily accessible equipment.
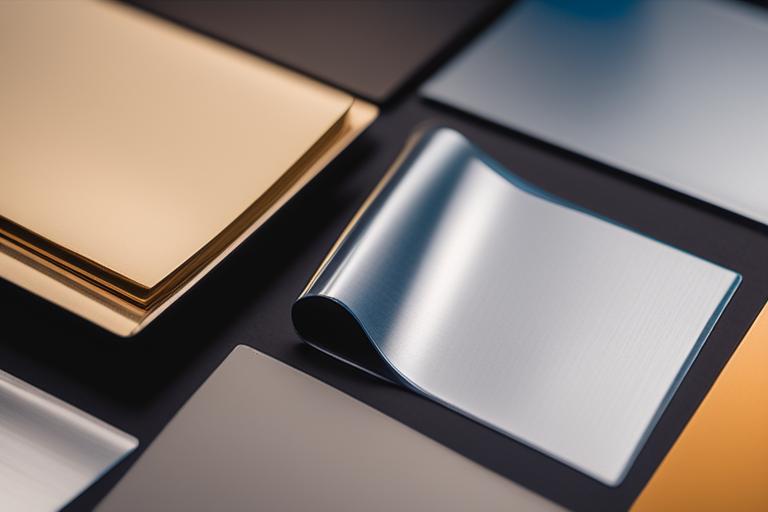
D. Materials Commonly Used in Custom Enclosure Fabrication
The choice of material for custom enclosures is crucial as it directly impacts durability, functionality, and overall performance. Stainless steel, aluminum, and galvanized steel are commonly used materials. Stainless steel enclosures offer excellent corrosion resistance and durability, making them ideal for outdoor or harsh environments. Aluminum enclosures are lightweight and provide good heat dissipation, making them suitable for electronics and telecommunications applications. Galvanized steel enclosures are known for their strength and affordability, making them a popular choice in various industries.
To ensure optimal material selection, consult experienced custom enclosure manufacturers who can provide expert advice based on your specific requirements.
Factor | Importance |
---|---|
Proper design | Critical in ensuring the enclosure meets functional and aesthetic requirements and enhances overall appearance |
Size | Determined by equipment dimensions and additional components |
Shape | Consider space constraints and aesthetic preferences |
Functionality | Provide easy access for maintenance and repairs, proper ventilation for heat dissipation, and cable management to prevent interference |
Aesthetics | Align with overall branding and style, creating a visually pleasing appearance |
Software tools | Specialized computer-aided design (CAD) software facilitates detailed 3D modeling, visualization, and modification |
Techniques | Rapid prototyping and 3D printing can be used for creating physical prototypes for testing and validation |
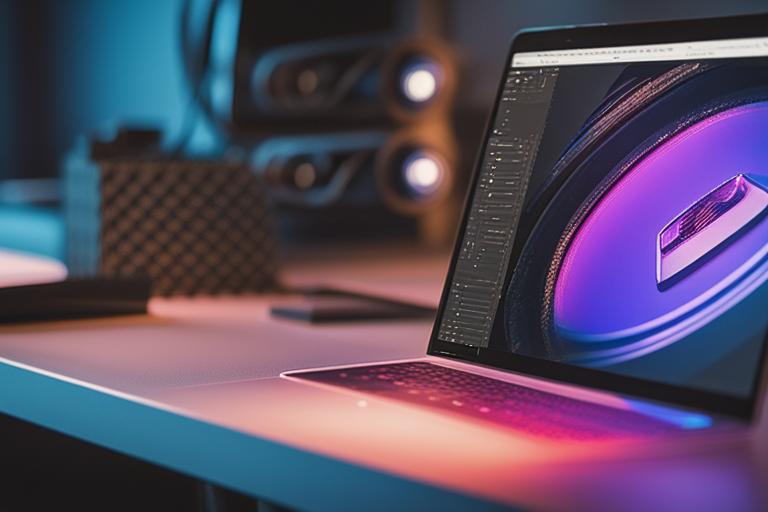
Designing Custom Enclosures
A. Importance of Proper Design in Custom Enclosure Fabrication
Proper design is critical in the fabrication of custom enclosures. It ensures the enclosure meets functional and aesthetic requirements while considering factors like size, shape, and ease of installation. A well-designed custom enclosure enhances the overall appearance of the equipment and provides efficient heat dissipation, cable management, and accessibility.
B. Key Factors to Consider During the Design Phase
Several key factors should be taken into account during the design phase. Determine the size of the enclosure based on equipment dimensions and additional components. Consider the shape, including any space constraints or aesthetic preferences.
Functionality is crucial. The enclosure should provide easy access for maintenance and repairs, proper ventilation for heat dissipation, and cable management to prevent interference. Aesthetics should align with overall branding and style, creating a visually pleasing appearance.
C. Software Tools and Techniques Used in Designing Custom Enclosures
Designing custom enclosures requires specialized software tools, with computer-aided design (CAD) being the most common. CAD software allows designers to create detailed 3D models, visualize the final product, and make necessary modifications. These tools facilitate collaboration between designers, engineers, and clients throughout the design process.
In addition to CAD software, techniques like rapid prototyping and 3D printing can be utilized to create physical prototypes. These techniques allow for further testing and validation of the design before moving into the fabrication phase.
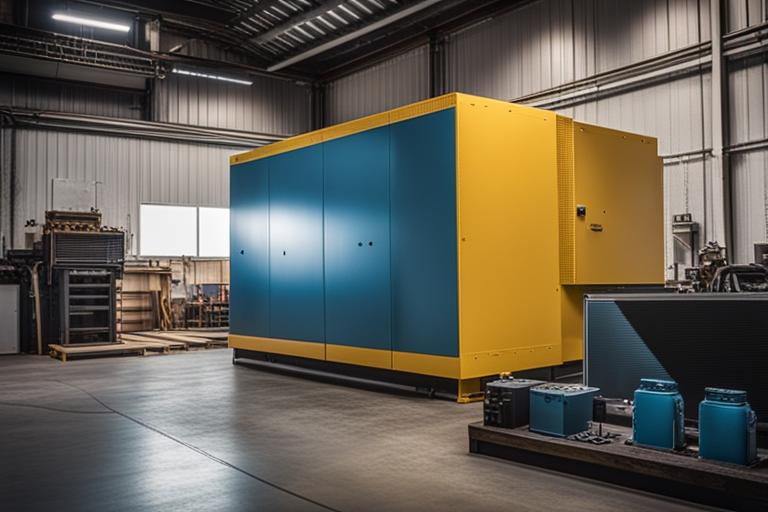
Real-Life Examples of Successful Custom Enclosure Projects
To further illustrate the importance and impact of custom enclosures, let’s explore a few real-life examples of successful projects:
- Medical Equipment Enclosure: A custom enclosure was designed and fabricated to house a medical device used for patient monitoring. The enclosure provided protection against dust and liquid ingress while ensuring easy access for maintenance. The design incorporated proper ventilation to prevent overheating, and the use of stainless steel material ensured durability and corrosion resistance.
- Telecommunications Enclosure: In the telecommunications industry, a custom enclosure was created to house critical networking equipment. The enclosure featured a rack-mount design for easy installation and space-saving. It incorporated cable management solutions to organize and protect internal wiring, ensuring optimal performance and reducing the risk of interference.
These real-life examples demonstrate the versatility and effectiveness of custom enclosures in various industries.
Case Study: Custom Enclosure Design for a Telecommunications Company
In this case study, we will explore how a telecommunications company successfully utilized custom enclosures to improve the functionality and performance of their products.
Background: ABC Telecommunications is a leading provider of network solutions for businesses. They were facing challenges with their existing off-the-shelf enclosures, as they were unable to accommodate their specific equipment requirements and hindered efficient cable management.
Challenge: ABC Telecommunications needed custom enclosures that could house their networking equipment while providing easy access for maintenance and cable management. They also required a sleek and professional design to match their brand image.
Solution: The company collaborated with a custom enclosure manufacturer, XYZ Fabrication, to design and fabricate tailored enclosures that met their specific needs. The design team at XYZ Fabrication worked closely with ABC Telecommunications to understand their requirements and translate them into a functional enclosure design.
The custom enclosures created for ABC Telecommunications featured rack-mount configurations with removable panels for easy access to the equipment. They incorporated cable management systems to organize and route cables effectively, reducing the risk of entanglement and damage. Additionally, the enclosures were designed with a modern and sleek aesthetic to align with the company’s brand identity.
Results: The custom enclosures provided numerous benefits for ABC Telecommunications. They improved the functionality of their networking equipment by providing a well-organized and easily accessible environment. The cable management systems reduced the time required for maintenance and troubleshooting, leading to increased operational efficiency.
Furthermore, the professional and sleek design of the enclosures enhanced the company’s brand image and helped them stand out in a competitive market. The custom enclosures provided a seamless and professional appearance while maintaining the necessary functionality.
By utilizing custom enclosures, ABC Telecommunications was able to overcome their challenges and achieve their desired outcomes. The collaboration with XYZ Fabrication ensured that the custom enclosures met their specific requirements and provided the necessary functionality and aesthetic appeal.
This case study demonstrates the positive impact of custom enclosures on functionality, performance, and brand image for businesses in the telecommunications industry. By investing in custom enclosures, companies can optimize their equipment’s performance while maintaining a professional and customized appearance.
Conclusion
Custom enclosures play a vital role in protecting sensitive equipment and components in multiple industries. By understanding the design and fabrication processes, material selection, and the importance of proper design, you can ensure the functionality and longevity of your equipment. Consult experienced custom enclosure manufacturers who can guide you through the process and help you create the perfect enclosure for your specific needs. With the right custom enclosure, you can safeguard your equipment and optimize its performance for years to come.
Frequently Asked Questions
What are custom enclosures used for in precision sheet metal fabrication?
Custom enclosures are used to protect and house delicate electronic components.
Who can benefit from using custom enclosures in precision sheet metal fabrication?
Manufacturers, engineers, and designers can all benefit from custom enclosures.
How are custom enclosures designed and fabricated in precision sheet metal fabrication?
Custom enclosures are designed using CAD software and then fabricated using precision sheet metal techniques.
What materials are commonly used for custom enclosures in precision sheet metal fabrication?
Aluminum, stainless steel, and carbon steel are commonly used materials for custom enclosures.
How long does it take to manufacture custom enclosures in precision sheet metal fabrication?
The manufacturing time for custom enclosures varies depending on complexity, but typically ranges from a few days to a few weeks.
What if I need a custom enclosure with specific dimensions that are not standard?
No worries! Custom enclosures can be designed and fabricated to meet your specific dimensions and requirements.