What readers will learn by reading this article:
- The definition and importance of OEM sheet metal fabrication in precision manufacturing
- Key considerations when undertaking OEM sheet metal fabrication projects
- How to research and select a reputable OEM sheet metal fabrication provider
- Tips for effective collaboration with the provider and ensuring quality control
- The logistics of production, delivery, and post-production support in OEM sheet metal fabrication
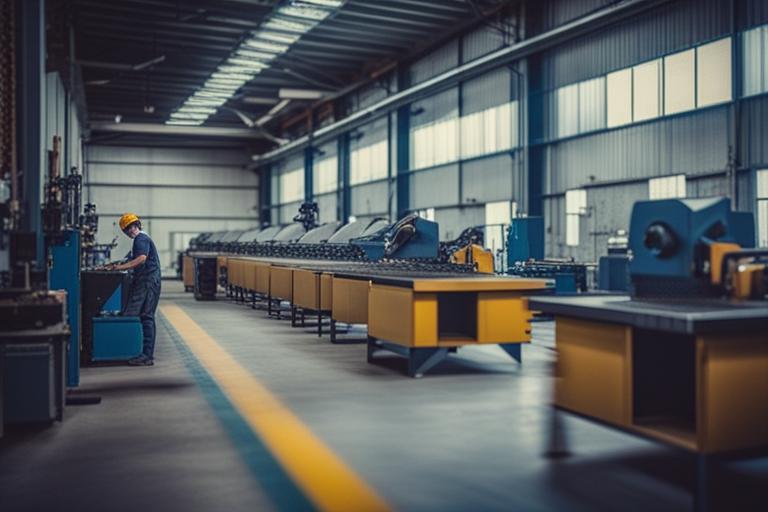
What is OEM Sheet Metal Fabrication?
OEM sheet metal fabrication is a specialized manufacturing process that involves the creation of precision sheet metal components according to the specifications and requirements of original equipment manufacturers (OEMs). It is a crucial aspect of precision manufacturing, as it plays a significant role in the production of various products across different industries.
Sheet metal fabrication refers to the process of transforming flat metal sheets into usable components or products through cutting, bending, forming, and assembling. This versatile manufacturing technique is widely used in industries such as automotive, aerospace, electronics, telecommunications, and many more.
OEM sheet metal fabrication is particularly important because it caters specifically to the needs of OEMs. OEMs are companies that design and manufacture products or components that are marketed and sold by another company under their own brand name. These products can range from simple brackets and enclosures to complex assemblies.
Concept and Applications of Sheet Metal Fabrication in Various Industries
Sheet metal fabrication is a fundamental process in the manufacturing industry, with applications in various sectors. The automotive industry relies heavily on OEM sheet metal fabrication for the production of components such as body panels, chassis, and exhaust systems. Precision manufacturing ensures that these parts meet the required specifications, tolerances, and safety standards.
In the aerospace industry, OEM sheet metal fabrication is vital for the production of aircraft components, including fuselages, wings, and engine parts. These components must be lightweight, yet strong and durable, to meet the demanding requirements of the aviation industry.
The electronics industry also heavily relies on OEM sheet metal fabrication for the production of enclosures, brackets, and other components used in electronic devices. These components need to have precise dimensions and tolerances to ensure proper fit and functionality within the electronic devices.
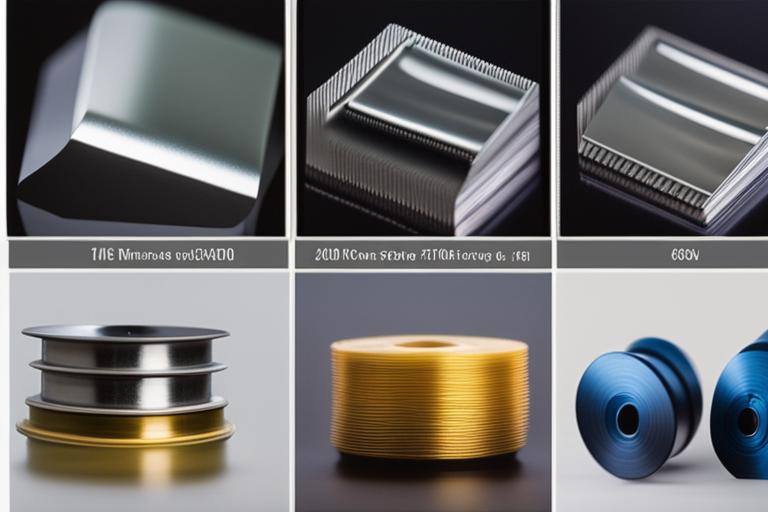
Benefits of OEM Sheet Metal Fabrication
OEM sheet metal fabrication offers several benefits that make it a preferred choice for precision manufacturing:
- Cost-Effectiveness: OEM sheet metal fabrication allows for efficient production processes, reducing costs associated with tooling, material waste, and labor. With the ability to produce components at scale, OEMs can achieve cost savings while maintaining high quality.
- Customization Options: Sheet metal fabrication provides a wide range of customization options, allowing OEMs to create components that meet their specific requirements. From material selection to finishing options, OEMs have the flexibility to design and produce components tailored to their needs.
- Quick Turnaround Time: With advancements in manufacturing technology and processes, OEM sheet metal fabrication enables fast production cycles. This is particularly important for OEMs that require rapid prototyping or have strict deadlines to meet.
- High-Quality Output: Reputable OEM sheet metal fabrication providers prioritize quality and adhere to stringent quality control measures. This ensures that the components produced meet the required standards and specifications, providing OEMs with reliable and durable products.
By leveraging the benefits of OEM sheet metal fabrication, OEMs can streamline their manufacturing processes, reduce costs, and deliver high-quality products to the market.
Key Considerations for OEM Sheet Metal Fabrication
Successful OEM sheet metal fabrication requires careful planning and consideration of various factors to ensure the desired outcome. Here are some key considerations to keep in mind:
Identifying Project Requirements: Materials, Dimensions, Tolerances, and Finishes
Before engaging in OEM sheet metal fabrication, it is crucial to clearly define the project requirements. This includes determining the desired materials, dimensions, tolerances, and finishes for the components to be produced.
Materials used in sheet metal fabrication can vary depending on the application and industry. Commonly used materials include steel, aluminum, stainless steel, and copper. Each material has its own properties and characteristics that influence factors such as strength, weight, and corrosion resistance.
Dimensions and tolerances play a critical role in determining the functionality and fit of the final components. It is important to define precise measurements and tolerances to ensure that the components meet the required specifications. This is particularly important for assemblies where multiple components need to fit together accurately.
Finishes, such as painting, powder coating, or plating, not only enhance the aesthetics of the components but also provide protection against corrosion and wear. Selecting the appropriate finish is essential to meet the specific requirements of the end product.
Scalability and Compatibility with Other Assembly Parts
When considering OEM sheet metal fabrication, it is essential to assess the scalability of the manufacturing process. As OEMs often require large quantities of components, the fabrication provider should have the capacity and capability to handle high-volume production efficiently.
Additionally, it is crucial to ensure compatibility between the sheet metal components and other assembly parts. Proper fit and functionality are essential for the seamless integration of the components into the final product. Collaboration between the OEM and the fabrication provider is vital to address any compatibility issues and optimize the design for manufacturability.
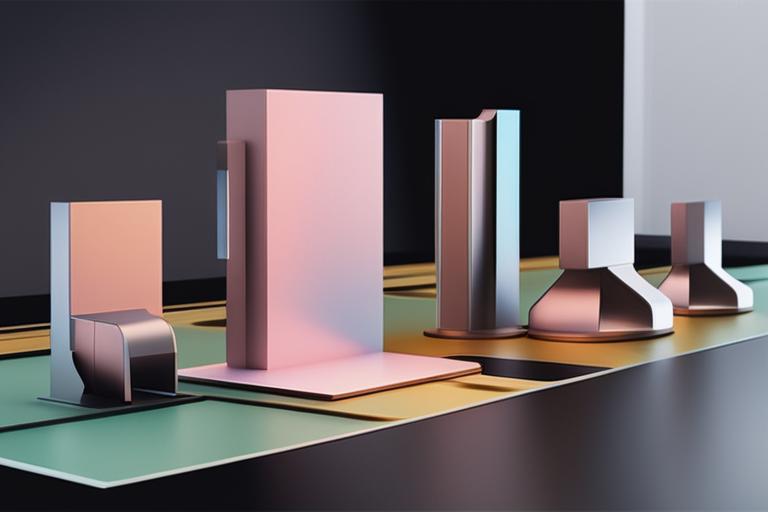
Importance of Design for Manufacturability and Cost Efficiency
Design for manufacturability (DFM) is a critical aspect of OEM sheet metal fabrication. DFM involves designing components and assemblies in a way that optimizes the manufacturing process, reduces costs, and ensures high-quality output.
Collaborating closely with the fabrication provider during the design phase can help identify potential design improvements that can enhance manufacturability and reduce production costs. The fabrication provider’s expertise in sheet metal fabrication techniques and processes can provide valuable insights into design modifications that can streamline production.
By considering these key factors, OEMs can ensure a smooth and successful OEM sheet metal fabrication process, resulting in high-quality components that meet their requirements.
Researching and Selecting an OEM Sheet Metal Fabrication Provider
Choosing the right OEM sheet metal fabrication provider is crucial to the success of a project. Here are some steps to help you in the research and selection process:
List of Reputable OEM Sheet Metal Fabrication Companies Specializing in Precision Manufacturing
When initiating the search for an OEM sheet metal fabrication provider, it is essential to compile a list of reputable companies that specialize in precision manufacturing. This can be done through online research, industry directories, and recommendations from trusted sources.
One such reputable provider is O.E.M. Precision[^1^]. They are a top provider of sheet metal fabrication and manufacturing services, offering a wide range of capabilities and customized solutions. They excel in handling complex projects and prioritize quality and service.
Factors to Consider when Evaluating Potential Providers: Experience, Capabilities, Certifications, and Quality Control Measures
When evaluating potential OEM sheet metal fabrication providers, several factors should be considered:
- Experience: Look for providers with extensive experience in OEM sheet metal fabrication, particularly in your industry or specific application. An experienced provider is more likely to have the expertise and knowledge to meet your requirements effectively.
- Capabilities: Assess the provider’s capabilities in terms of equipment, technology, and production capacity. Ensure that they have the necessary machinery, tools, and resources to handle your project efficiently.
- Certifications: Verify if the provider holds relevant certifications, such as ISO 9001:2015, which ensures adherence to quality management systems. Certifications demonstrate the provider’s commitment to maintaining quality standards.
- Quality Control Measures: Inquire about the provider’s quality control processes and measures. A reputable provider will have robust quality control systems in place to ensure that the components produced meet the required specifications and standards.
Assessing Past Work and Customer Satisfaction: Samples, Reviews, and References
To gain insights into the capabilities and performance of potential OEM sheet metal fabrication providers, it is essential to assess their past work and customer satisfaction. This can be done through:
- Samples: Request samples of their previous work to evaluate the quality, precision, and finish of the components produced. This will give you an idea of their craftsmanship and attention to detail.
- Reviews: Look for reviews and testimonials from previous customers. Online platforms, industry forums, and social media can provide valuable feedback on the provider’s performance, reliability, and customer service.
- References: Ask the provider for references from their past clients. Contact these references to inquire about their experience working with the provider and whether they would recommend their services.
By conducting thorough research and evaluation, you can select an OEM sheet metal fabrication provider that meets your specific requirements and delivers high-quality components.
Factors to Consider | OEM Precision | Competitor A | Competitor B | Competitor C |
---|---|---|---|---|
Experience | High | Medium | High | Low |
Capabilities | High | Medium | High | Medium |
Certifications | ISO 9001:2015 | None | ISO 9001:2015 | None |
Quality Control | Robust | Basic | Robust | Basic |
Past Work | Excellent | Good | Excellent | Good |
Customer Satisfaction | Positive | Mixed | Positive | Mixed |
Collaboration with the OEM Sheet Metal Fabrication Provider
Effective collaboration between the OEM and the sheet metal fabrication provider is crucial for a successful project outcome. Here are some key steps involved in the collaborative process:
Effective Communication and Collaboration with the Provider
Clear and effective communication is essential throughout the OEM sheet metal fabrication process. Establish open lines of communication and maintain regular contact with the fabrication provider to discuss project requirements, progress, and any modifications or challenges that may arise.
Collaboration is key when it comes to optimizing the design for manufacturability and cost efficiency. Involve the fabrication provider early in the design phase to leverage their expertise and insights. They can provide valuable suggestions and recommendations that can improve the manufacturability of the components while minimizing costs.
Steps Involved in the Collaborative Process: Design Review, Material Selection, and Prototyping
The collaborative process typically involves several steps:
- Design Review: Share the component designs with the fabrication provider for a thorough review. This review aims to identify any design improvements or modifications that can enhance manufacturability, reduce costs, or improve the overall functionality of the components.
- Material Selection: Collaborate with the fabrication provider to select the most suitable materials for the components. Consider factors such as strength, weight, corrosion resistance, and cost-effectiveness when making material choices.
- Prototyping: Prototyping is an essential step in the OEM sheet metal fabrication process. Collaborate with the provider to produce prototypes of the components to ensure they meet the required specifications and functionality. Prototyping allows for testing and validation before moving into full-scale production.
By fostering collaboration and open communication, OEMs can leverage the expertise of the sheet metal fabrication provider to optimize designs for manufacturability, reduce costs, and ensure a smooth production process.
Case Study: How XYZ Manufacturing Improved Efficiency with OEM Sheet Metal Fabrication
At XYZ Manufacturing, we were facing a challenge in producing sheet metal components for our products. Our in-house fabrication process was time-consuming and expensive, resulting in delays and increased costs. We knew we needed a solution to improve efficiency and quality while reducing production time.
After researching and evaluating potential OEM sheet metal fabrication providers, we decided to partner with Precision Metalworks, a reputable company specializing in precision manufacturing. We were impressed with their experience, capabilities, and certifications, as well as their commitment to quality control measures.
During the collaboration process, we worked closely with Precision Metalworks to review our designs and select the appropriate materials. They provided valuable insights and suggestions for optimizing our designs for manufacturability and cost efficiency. With their expertise, we were able to make necessary adjustments to our designs and achieve better results.
Precision Metalworks implemented stringent quality control measures throughout the production process. They conducted inspections, tests, and certifications to ensure the highest level of product quality. We appreciated their timely communication and updates, which kept us informed of the progress and allowed us to plan accordingly.
The production and delivery phase went smoothly, thanks to Precision Metalworks’ efficient logistics and attention to detail. The finished OEM sheet metal components were shipped and delivered on time. We were also impressed with their post-production support, including warranty, maintenance, and excellent customer service.
Since partnering with Precision Metalworks, we have seen a significant improvement in our production process. Our efficiency has increased, resulting in shorter lead times and reduced costs. The quality of our sheet metal components has also improved, leading to higher customer satisfaction.
Choosing a reliable OEM sheet metal fabrication provider like Precision Metalworks has been instrumental in our success. We highly recommend conducting thorough research and selecting a reputable provider to meet your OEM sheet metal fabrication needs. It can make a significant difference in the precision sheet metal industry and help your company achieve its goals.
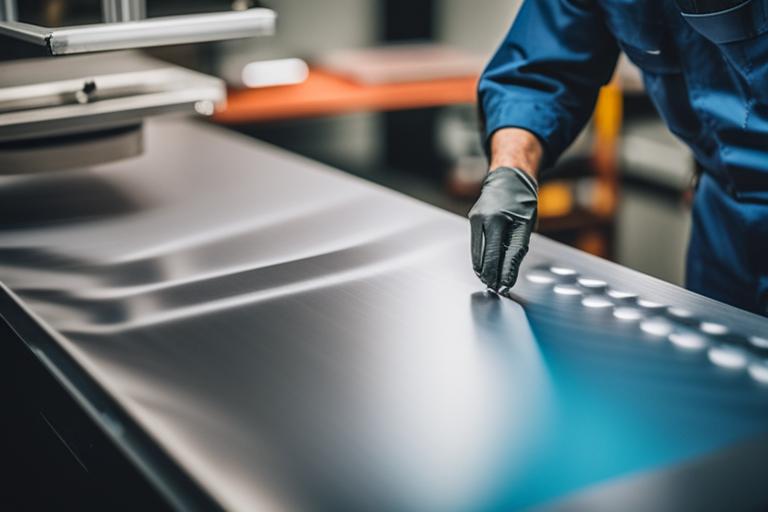
Quality Control in OEM Sheet Metal Fabrication
Quality control is a critical aspect of OEM sheet metal fabrication to ensure that the components produced meet the required standards and specifications. Here are some key considerations for implementing quality control measures:
Implementing Quality Control Measures throughout the Production Process
Quality control should be implemented at every stage of the OEM sheet metal fabrication process. This includes:
- Incoming Inspection: Thoroughly inspect the incoming raw materials to ensure they meet the required specifications and quality standards. This helps prevent any issues or defects from being introduced into the production process.
- In-Process Inspections: Conduct regular inspections during the fabrication process to monitor the quality and accuracy of the components being produced. This can involve dimensional checks, visual inspections, and other tests as required.
- Final Inspection: Perform a comprehensive final inspection of the finished components to ensure they meet all the specified requirements. This includes verifying dimensions, tolerances, finishes, and any other specified criteria.
.