What to Learn About Custom Enclosures in Metal Fabrication
- Importance and benefits of custom enclosures
- They provide housing and protection for equipment.
- Customization options cater to specific industry needs.
- Precision fabrication techniques and materials
- Techniques include laser cutting, welding, and powder coating.
- Materials used can be aluminum, stainless steel, or galvanized steel.
- How to choose a fabrication partner
- Consider experience, capabilities, lead times, and customer service.
Custom enclosures play a pivotal role in various industries where equipment and machinery require specialized housing and protection. These enclosures are meticulously designed to meet specific requirements, ensuring the safety and functionality of the components they house. The significance of custom enclosures lies in their ability to provide tailored solutions that standard off-the-shelf enclosures may not offer. By investing in custom enclosures, businesses can enhance equipment performance, prolong its lifespan, and maintain operational efficiency.
Types of Custom Enclosures
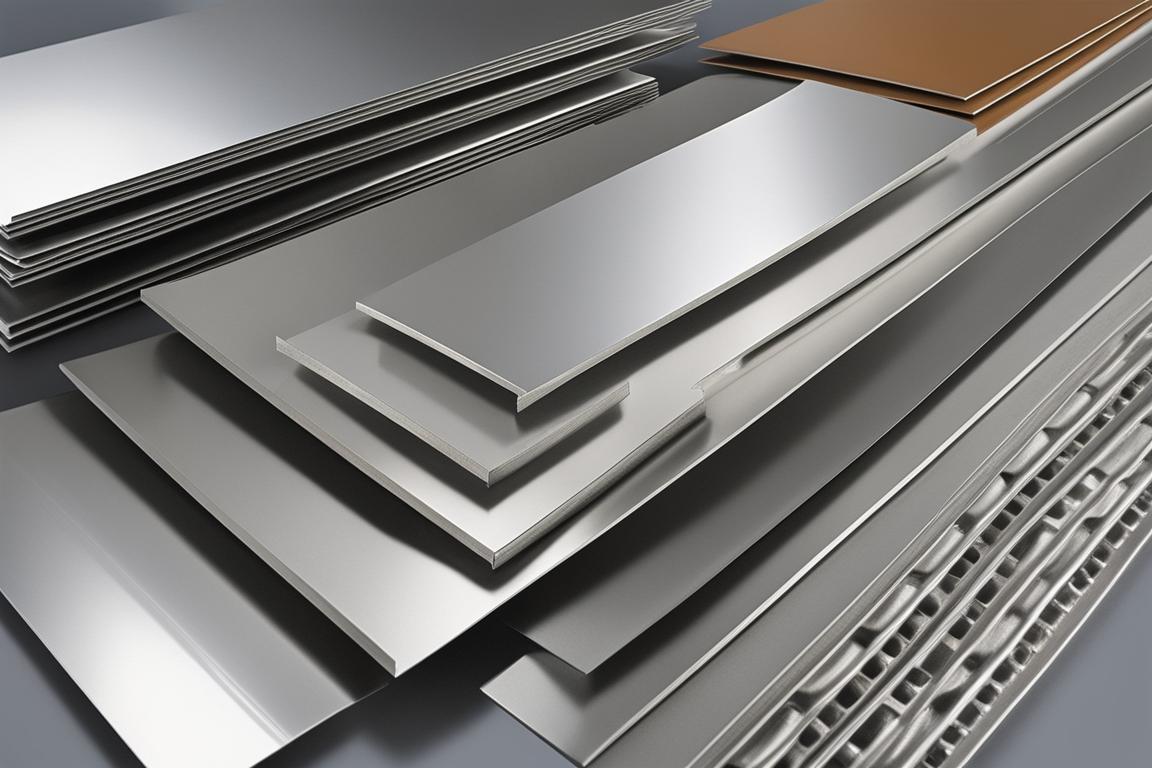
Materials Used in Custom Enclosures
Custom enclosures are typically crafted from a range of materials, each offering unique properties to suit diverse industrial needs. Common materials used in custom enclosure fabrication include aluminum, known for its lightweight yet durable nature; stainless steel, prized for its corrosion resistance; and galvanized steel, favored for its robustness in challenging environments.
Varieties of Custom Enclosures
Custom enclosures come in various designs tailored to specific functions. Examples include rackmount enclosures for efficient equipment stacking, console enclosures for centralized control systems, and fully customized designs that cater to unique requirements. The versatility in design allows for seamless integration of equipment while ensuring optimal protection and accessibility.
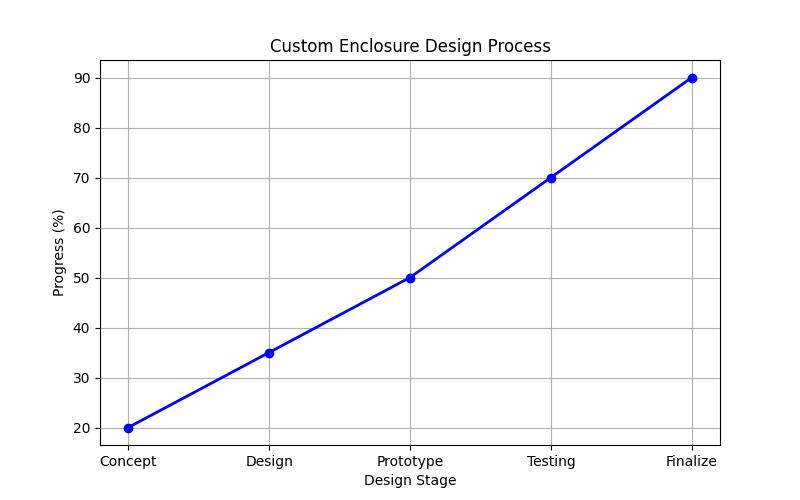
Design and Engineering of Custom Enclosures
The design and engineering phase of custom enclosures is a meticulous process that involves advanced techniques to ensure precision and functionality. Computer-Aided Design (CAD) software is utilized to create detailed 3D models of the enclosure, facilitating prototyping and testing to validate the design’s efficacy. Engineers adhere to industry standards and specifications to guarantee compliance and optimal performance of the custom enclosure.
Precision Fabrication Techniques for Custom Enclosures
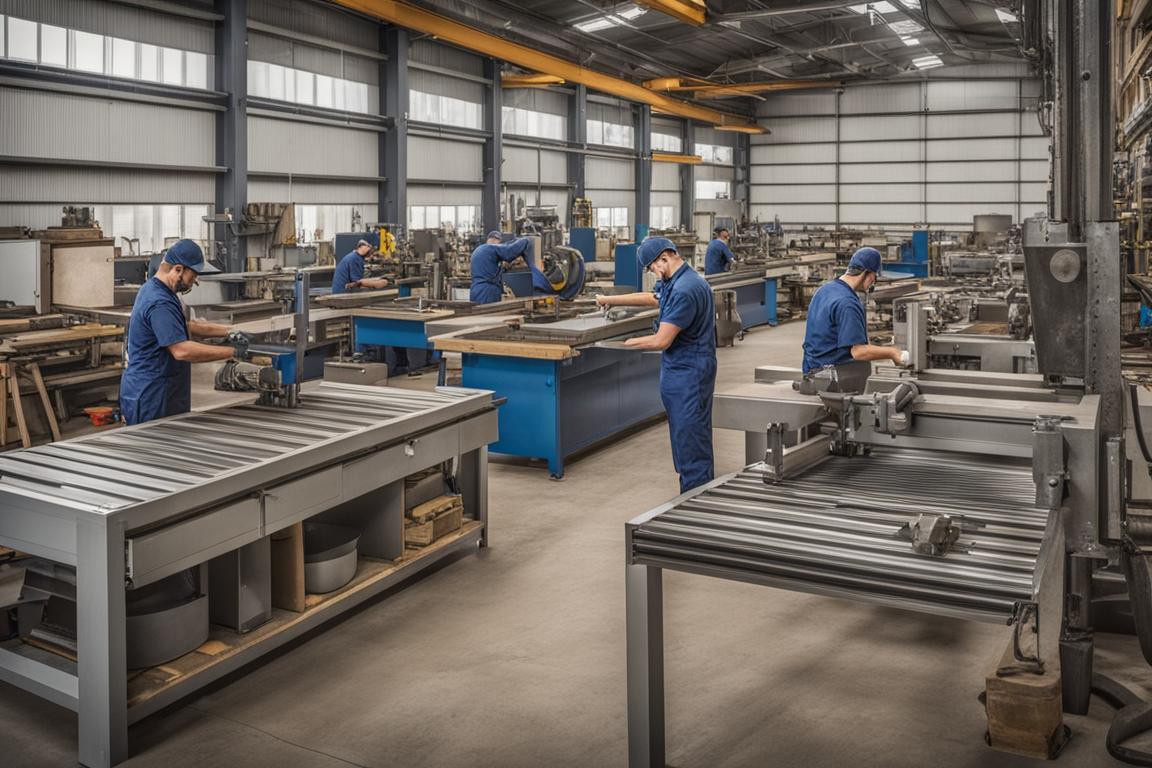
Fabrication Processes
Fabrication of custom enclosures entails a series of intricate processes, including laser cutting, CNC punching, bending, welding, and powder coating. These techniques are employed to shape and assemble enclosure components with utmost accuracy, maintaining structural integrity and aesthetic appeal throughout the fabrication process.
Importance of Precision
Precision in fabrication is paramount when creating custom enclosures to ensure a seamless fit, optimal functionality, and longevity of the final product. By upholding high standards of precision, manufacturers can deliver custom enclosures that meet stringent quality requirements and exceed client expectations.
Customization Options for Enclosures
Tailored Features
Custom enclosures offer a myriad of customization options to address specific needs. These options include varying sizes to accommodate different equipment dimensions, ventilation systems for heat dissipation, diverse mounting solutions for installation flexibility, door configurations for accessibility, and a range of finishes to enhance aesthetics and durability. By tailoring these features, custom enclosures can effectively meet the demands of diverse industries and applications.
Industry-Specific Customization
Manufacturers can tailor custom enclosures to align with industry-specific requirements, such as IP ratings for environmental protection, EMI/RFI shielding for electromagnetic interference mitigation, and NEMA standards for enclosure performance in hazardous locations. Customization ensures that enclosures are optimized to function seamlessly in their intended environments.
Quality Control and Testing Procedures
Ensuring Quality
Quality control measures and rigorous testing procedures are integral to the fabrication of custom enclosures. Manufacturers adhere to industry standards and certifications to maintain quality assurance throughout the production process, from material selection to final assembly. Quality checks and inspections are conducted at various stages to guarantee the reliability and performance of custom enclosures.
Certifications and Standards
Manufacturers of custom enclosures often hold certifications like ISO 9001:2015, indicating their commitment to quality management systems. Compliance with industry standards ensures that custom enclosures meet regulatory requirements and deliver consistent performance, instilling confidence in clients regarding the product’s reliability and durability.
Quality Control and Testing Procedures | Applications of Custom Enclosures |
---|---|
– Quality control measures ensure fabrication standards are met | – Telecommunications: safeguarding sensitive equipment |
– Compliance with industry standards like ISO 9001:2015 | – Electronics: organizing and protecting components |
– Rigorous testing procedures to guarantee reliability | – Healthcare: optimizing equipment performance |
– Inspections at various stages of production | – Aerospace: enhancing safety measures |
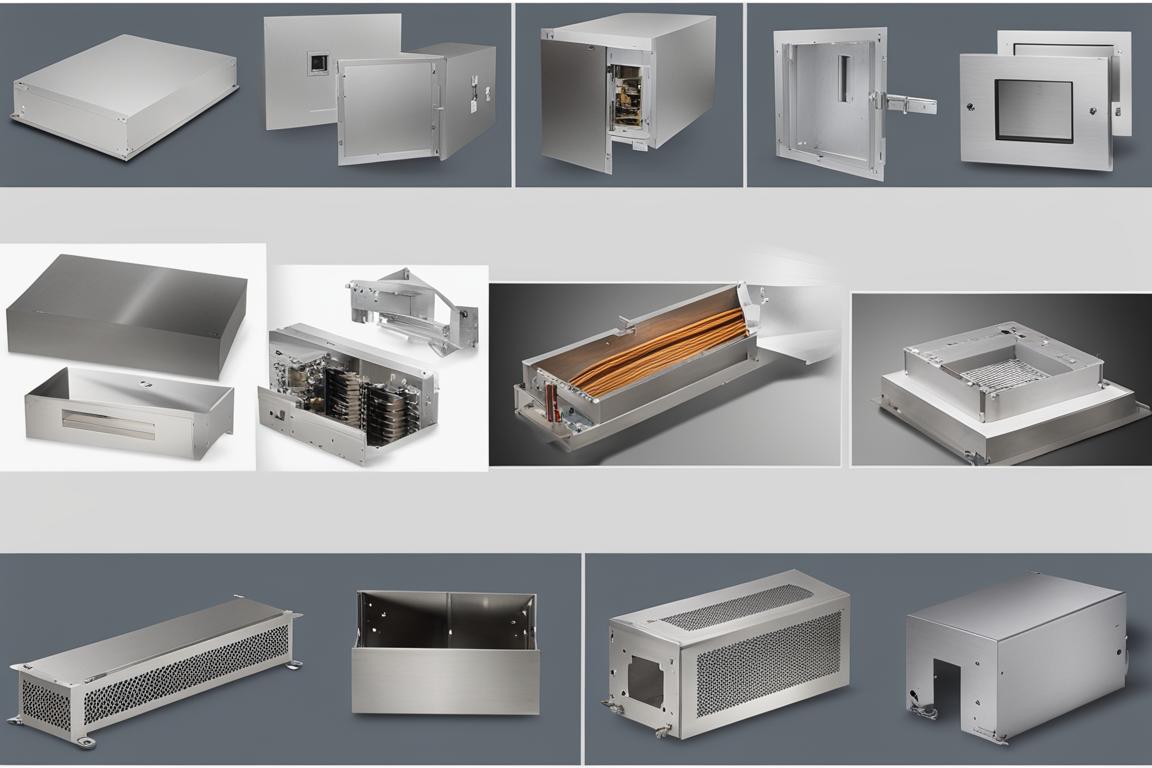
Applications of Custom Enclosures
Custom enclosures find widespread applications across industries where equipment protection and organization are paramount. From telecommunications and electronics to healthcare and aerospace, custom enclosures serve diverse sectors by safeguarding sensitive components and optimizing operational efficiency. Manufacturers tailor designs to suit unique industry challenges, providing bespoke solutions that enhance equipment performance and longevity.
Case Studies on Custom Enclosures
Real-World Success Stories
Numerous companies have leveraged custom enclosures to address specific challenges and achieve operational excellence. Case studies highlight how custom solutions have optimized equipment performance, streamlined workflows, and enhanced safety measures in various industries. By investing in custom enclosures, businesses can witness tangible improvements in efficiency, reliability, and overall operational effectiveness.
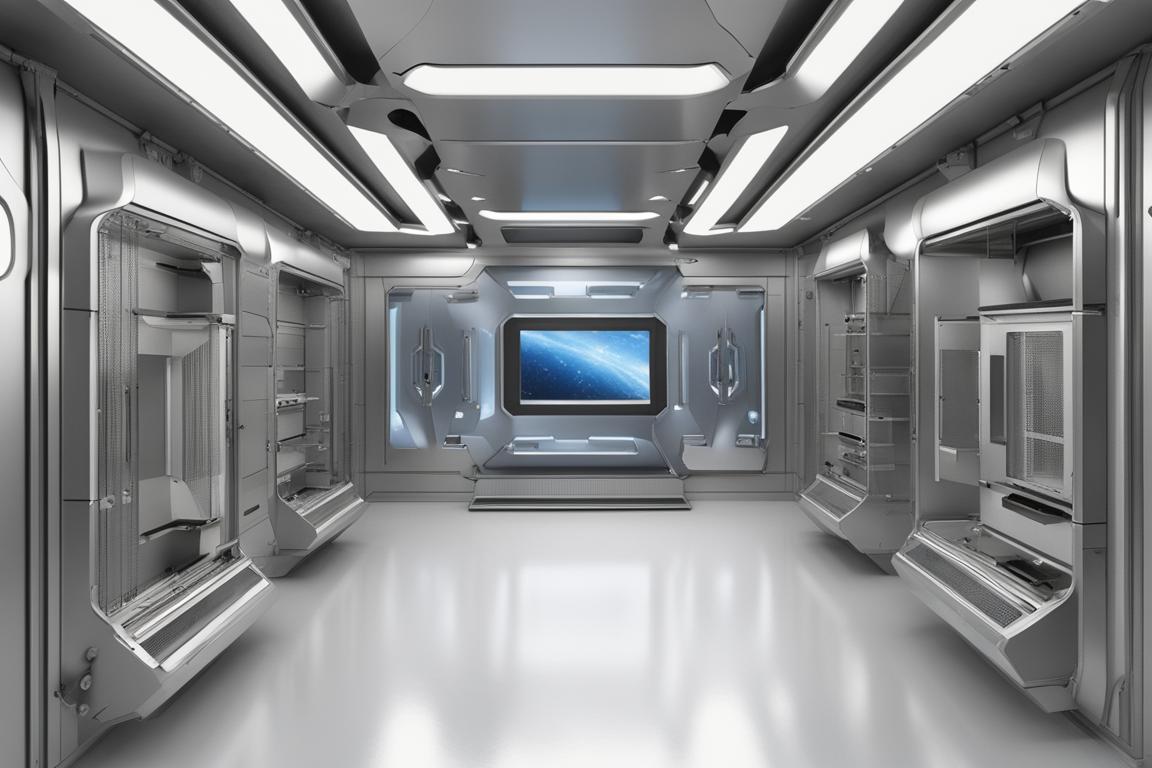
Future Trends in Custom Enclosures
Technological Advancements
The landscape of precision sheet metal fabrication is continually evolving, driven by technological advancements and innovative practices. Emerging trends in custom enclosure design include the integration of smart technologies for remote monitoring, the use of sustainable materials for eco-friendly solutions, and the implementation of automation for enhanced production efficiency. These trends shape the future of custom enclosures by offering cutting-edge solutions that align with evolving industry demands.
Selecting a Fabrication Partner for Custom Enclosures
Choosing the Right Partner
When selecting a fabrication partner for custom enclosures, businesses should consider several factors to ensure a successful collaboration. Experience in precision sheet metal fabrication, capabilities to deliver complex designs, adherence to strict lead times, and a commitment to exceptional customer service are key considerations. By partnering with a reputable fabricator, businesses can access expertise and resources to create custom enclosures that meet their exact specifications and quality standards.
Conclusion
In conclusion, custom enclosures are indispensable in today’s industrial landscape, offering tailored solutions for equipment housing and protection. Precision fabrication, customization options, and stringent quality assurance are pivotal in ensuring the effectiveness of custom enclosures. By investing in high-quality, customized enclosures, businesses can enhance operational efficiency, prolong equipment lifespan, and showcase a dedication to excellence and innovation in metal fabrication.
For innovative enclosure solutions, explore Protocase’s custom electronic enclosures. If you are looking for expandable and stackable enclosure options, check out Custom Cages’ large reptile enclosures.
For expert assistance in designing and manufacturing custom enclosures tailored to your specific needs, contact us today!
Questions and Answers
Who can benefit from custom enclosures in precision sheet metal fabrication?
Companies in industries like electronics, telecommunications, and medical devices.
What materials are typically used for custom enclosures in sheet metal fabrication?
Common materials include aluminum, stainless steel, and galvanized steel.
How are custom enclosures designed and manufactured in precision sheet metal fabrication?
They are designed using CAD software and then fabricated using cutting, bending, and welding techniques.
What makes custom enclosures from precision sheet metal fabrication more costly?
The customization and precision involved in the design and manufacturing process can lead to higher production costs.
How can I ensure that my custom enclosure meets industry standards and regulations?
Work with a reputable sheet metal fabrication company that has experience in your industry and adheres to quality standards.