Learn about Custom Enclosures in Metal Fabrication
Readers will learn:
– The types and applications of custom enclosures in various industries, including electrical, electronics, industrial, automotive, and reptile and pet enclosures.
– The materials, design, and precision manufacturing techniques used in creating custom enclosures, including stainless steel, aluminum, CAD design, laser cutting, CNC machining, and welding.
– Quality standards, compliance, case studies, future trends, and how to choose a custom enclosure provider.
Custom enclosures play a pivotal role in various industries, providing a tailored solution for housing electronic components, industrial equipment, automotive systems, and even pet habitats. In this comprehensive guide, we delve into the significance, types, materials, design, manufacturing techniques, quality standards, case studies, future trends, and factors to consider when choosing a custom enclosure provider. This article aims to provide a deep understanding of custom enclosures and their vital role in precision sheet metal fabrication across diverse sectors.
Defining Custom Enclosures
Custom enclosures, as the name suggests, are specifically designed and manufactured to encase and protect various types of equipment, devices, or living organisms. These enclosures are tailored to individual specifications, ensuring a perfect fit and optimal functionality for the intended application. They are fabricated using precision sheet metal techniques to meet the unique requirements of different industries.
Importance of Custom Enclosures in Various Industries
The significance of custom enclosures spans across a wide spectrum of industries, including electronics, telecommunications, automotive, industrial automation, and pet care. These enclosures provide a secure housing for sensitive electronic components, protect machinery from environmental factors, and offer safe and comfortable habitats for pets and reptiles.
Role of Precision Sheet Metal Fabrication in Custom Enclosures
Precision sheet metal fabrication is the cornerstone of custom enclosure manufacturing. This specialized fabrication process involves cutting, bending, and assembling sheet metal to create custom enclosures with high precision and accuracy. The use of advanced techniques ensures that the enclosures meet stringent quality standards and regulatory requirements.
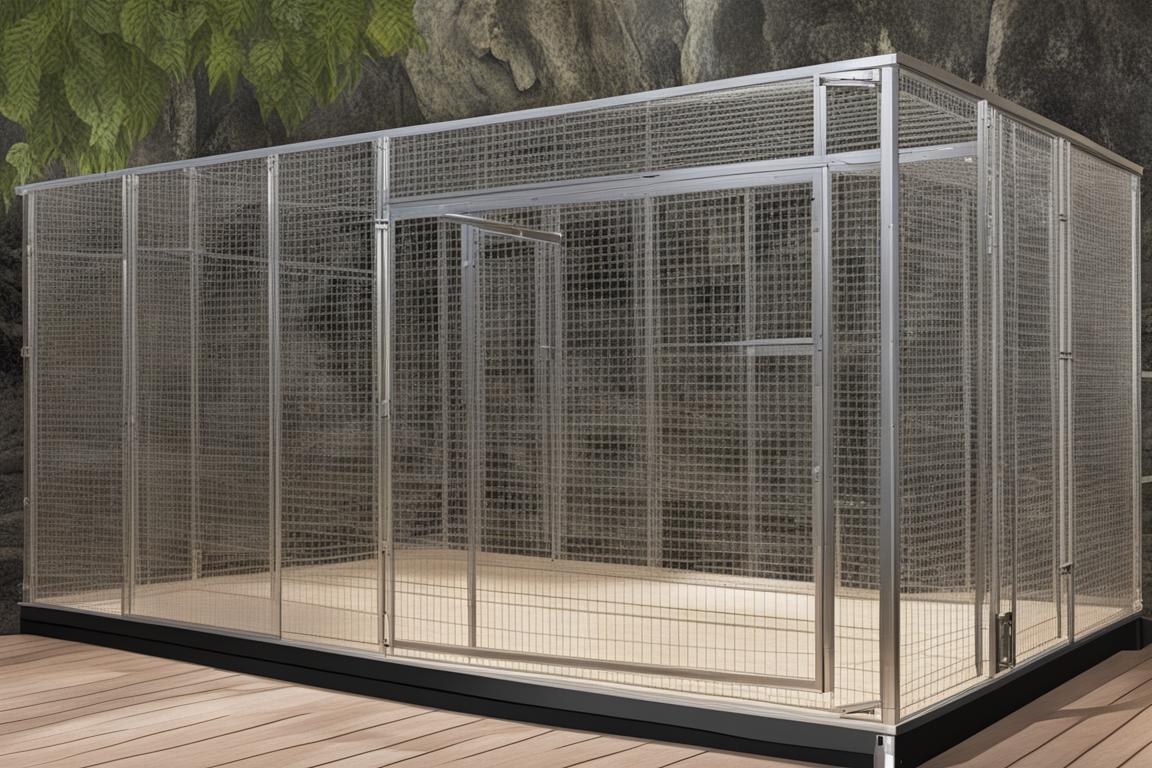
Types and Applications of Custom Enclosures
Electrical and Electronics Enclosures
Custom enclosures are extensively used in the electrical and electronics industry to house sensitive components such as circuit boards, control panels, and power distribution systems. These enclosures safeguard the equipment from dust, moisture, and electromagnetic interference, ensuring reliable performance and longevity.
Industrial and Automotive Enclosures
In industrial and automotive settings, custom enclosures are employed to protect control systems, instrumentation, and electrical wiring from harsh operating environments. They are designed to withstand extreme temperatures, vibrations, and exposure to chemicals, making them indispensable for industrial automation and automotive applications.
Reptile and Pet Enclosures
Custom enclosures also cater to the needs of pet owners and breeders by providing specialized habitats for reptiles, birds, and small animals. These enclosures are designed to create a comfortable and safe environment for pets, incorporating features such as heating elements, UV lighting, and secure locking mechanisms.
Varied Applications in Precision Sheet Metal Fabrication
The versatility of custom enclosures extends to diverse applications in precision sheet metal fabrication, ranging from housing sophisticated electronic assemblies to protecting delicate scientific instruments in research laboratories and medical facilities.
Type of Enclosure | Material | Key Properties | Typical Applications |
---|---|---|---|
Electrical/Electronics | Stainless Steel | Corrosion resistance, durability, hygienic properties | Food processing, pharmaceutical, outdoor settings |
Industrial/Automotive | Aluminum | Lightweight, robust, excellent thermal conductivity | Aerospace, marine, telecommunications |
Reptile/Pet | Galvanized Steel | Protection against rust and corrosion | Outdoor, industrial, pet care settings |
Varied Applications | Composite/Specialty | Balance of strength, weight, resistance to environmental factors | Research laboratories, medical facilities |
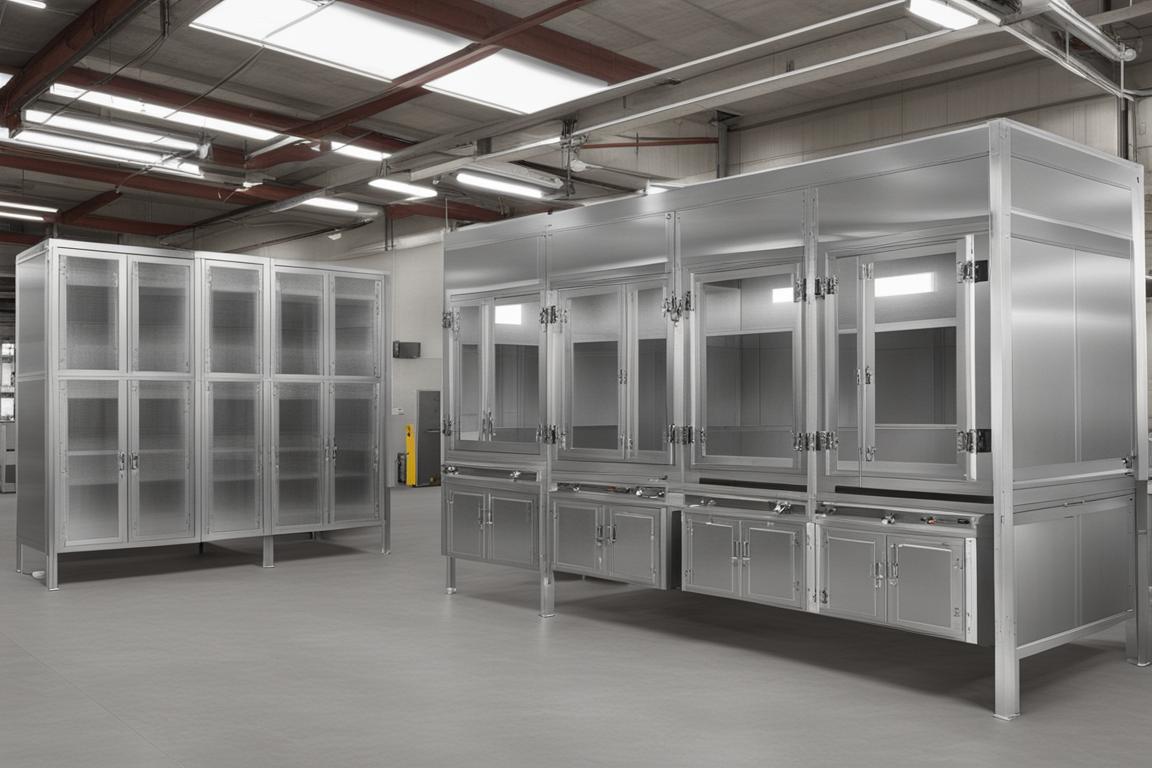
Materials and Construction of Custom Enclosures
Stainless Steel Enclosures
Stainless steel is a popular choice for custom enclosures due to its exceptional corrosion resistance, durability, and hygienic properties. These enclosures are well-suited for demanding environments such as food processing facilities, pharmaceutical plants, and outdoor installations.
Aluminum Enclosures
Aluminum enclosures offer a lightweight yet robust solution for housing electronic and electrical equipment. They are favored for their excellent thermal conductivity, non-magnetic properties, and resistance to corrosion, making them ideal for aerospace, marine, and telecommunications applications.
Galvanized Steel Enclosures
Galvanized steel enclosures provide superior protection against rust and corrosion, making them suitable for outdoor and industrial settings where exposure to moisture and harsh conditions is a concern. These enclosures are known for their ruggedness and long-term reliability.
Composite and Specialty Materials
In addition to traditional metals, custom enclosures can be constructed from composite materials and specialty alloys to meet specific performance requirements. These materials offer a balance of strength, weight, and resistance to environmental factors, expanding the possibilities for custom enclosure design and application.
Applications and Benefits in Precision Sheet Metal Fabrication
The choice of materials for custom enclosures is critical in ensuring the longevity and performance of the housed components. By selecting the appropriate material and construction techniques, manufacturers can create enclosures that meet industry-specific standards and exceed customer expectations.
Design and Customization
CAD Design and Prototyping
The design phase of custom enclosures often involves computer-aided design (CAD) to create precise 3D models and prototypes. This allows for thorough evaluation of the enclosure’s form, fit, and function before proceeding to the manufacturing stage, ensuring that the final product meets all requirements.
Customization Options for Specific Industry Requirements
Custom enclosures can be tailored to accommodate unique features such as integrated cooling systems, cable management provisions, and secure locking mechanisms. This customization ensures that the enclosures seamlessly integrate with the specific equipment and operational needs of different industries.
.
FAQs
Who needs custom enclosures in precision sheet metal fabrication?
Manufacturers and engineers who require specialized housing for their electronic components.
What materials are used for custom enclosures in sheet metal fabrication?
Typically, custom enclosures are made from aluminum, stainless steel, or galvanized steel for durability.
How are custom enclosures designed and fabricated for specific needs?
They are designed using CAD software and fabricated using techniques such as laser cutting and CNC bending.
What if I need a custom enclosure with specific dimensions?
Our fabrication process allows for precise customization to meet your exact specifications.
How can custom enclosures improve the efficiency of electronic components?
By providing a tailored housing solution, custom enclosures can enhance protection and optimize functionality.
What are the benefits of custom enclosures over standard off-the-shelf options?
Custom enclosures offer tailored designs, precise fit, and specialized features not found in standard options.