What readers will learn from this article:
- The importance of precision sheet metal fabrication in various industries.
- The definition and benefits of sheet metal punching in precision sheet metal fabrication.
- The types of punches and dies used in sheet metal punching and their applications.
Sheet metal punching is a fundamental process in precision sheet metal fabrication. It involves impressing a form on a surface by applying pressure or percussion with a steel punch tool. This technique allows for the creation of holes, shapes, and features in sheet metal, making it a crucial process in industries such as automotive, aerospace, electronics, and construction.
In this comprehensive guide, we will demystify the sheet metal punching process, providing insights into its benefits, applications, and best practices. We will explore the equipment and tools required, discuss the preparation necessary before punching, and outline the step-by-step process. We will also cover quality control, safety considerations, and post-punching operations. Additionally, we will compare sheet metal punching to stamping to help you make informed decisions regarding your fabrication needs.
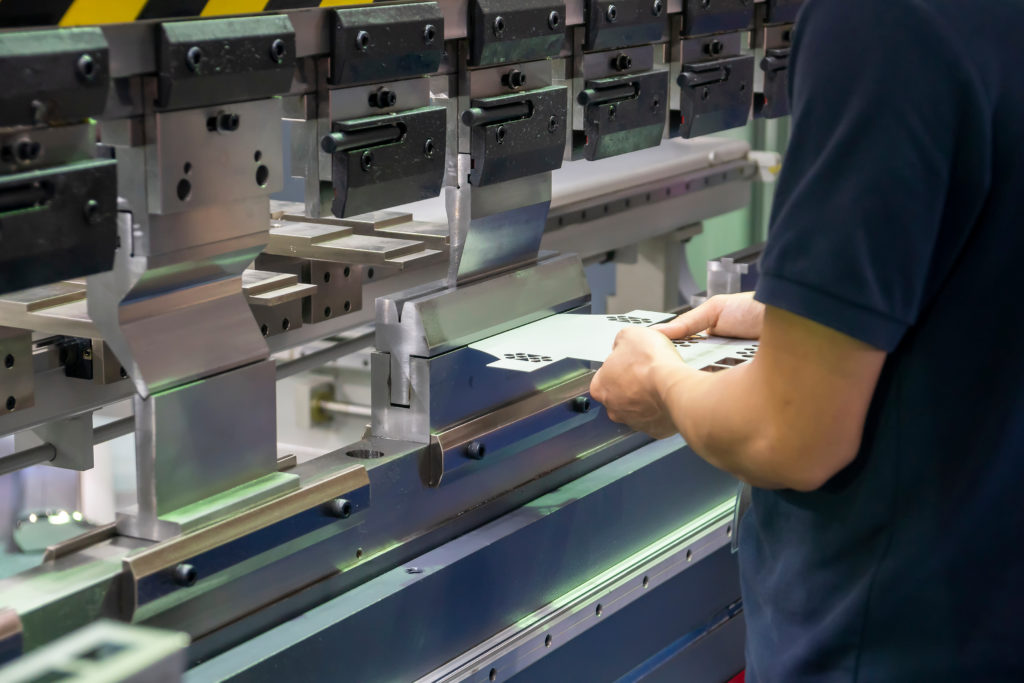
Understanding Sheet Metal Punching
Sheet metal punching is a versatile technique that offers advantages over other methods like stamping or laser cutting. It involves forcing a punch through the sheet metal to create a hole or form a shape. The punch press machine, equipped with punches and dies, is the primary tool used for sheet metal punching.
Compared to other metalworking processes, sheet metal punching offers greater speed and efficiency. It is a cost-effective method for creating holes and features in sheet materials. Additionally, sheet metal punching can create multiple shaped holes, providing flexibility in design and functionality.
Different types of punches and dies are used in sheet metal punching, depending on the desired outcome. Standard punches create round holes, while special punches with custom shapes are used for intricate designs. Dies support the sheet metal during the punching process and provide clearance for the punch.
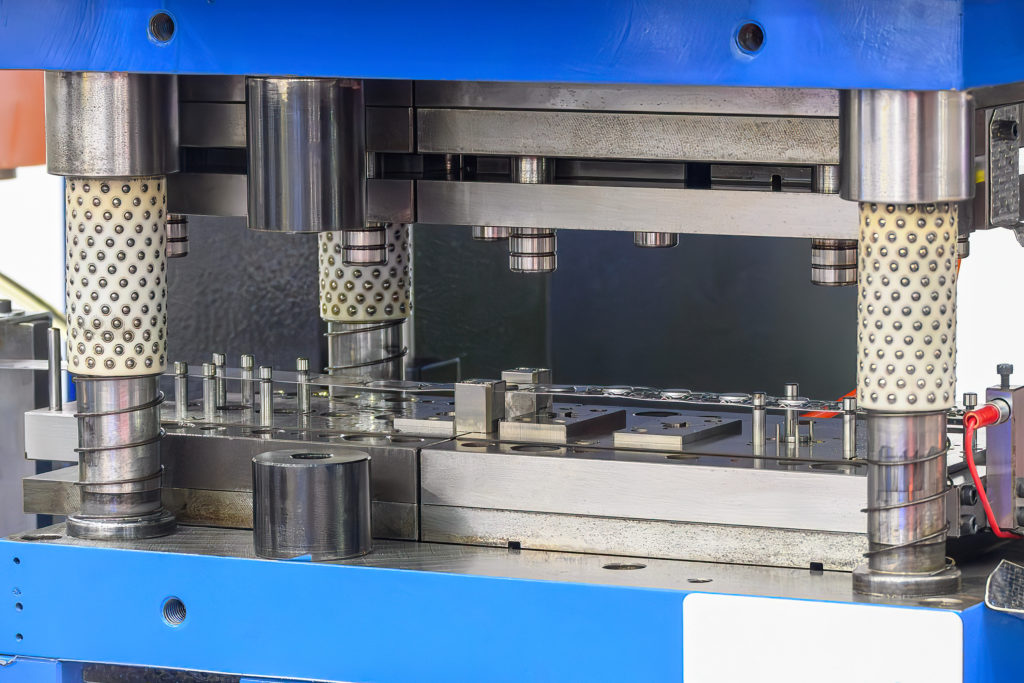
Equipment and Tools for Sheet Metal Punching
To carry out sheet metal punching effectively, the right equipment and tools are essential. The punch press machine is the centerpiece of sheet metal punching operations. It consists of a hydraulic or mechanical press that provides the force required to punch through the sheet metal. The machine includes a ram, which holds the punch and applies the force.
When selecting a punch press for sheet metal punching, factors like maximum sheet size, tonnage capacity, and material handling capability should be considered. Choosing a machine that meets the requirements of the intended punching applications is crucial.
In addition to the punch press, various tooling options are available for different punching applications. Punches, dies, and other accessories are designed to create specific hole sizes and shapes. The choice of tooling depends on factors like material thickness, desired hole size, and shape complexity. Custom tooling can be created for unique punching requirements.
Equipment and Tools for Sheet Metal Punching | Preparing for Sheet Metal Punching |
---|---|
Punch press machine | Proper material selection |
Punches, dies, and tooling | Accurate measurement and marking |
Custom tooling | Securely clamping the workpiece |
Preparing for Sheet Metal Punching
Proper material selection and preparation are crucial before initiating the sheet metal punching process. The choice of material depends on the application and desired properties of the finished product. Common materials used in sheet metal punching include stainless steel, aluminum, and carbon steel.
Accurate measurement and marking of the sheet metal are essential for precise punching. Using appropriate measuring tools, like calipers or rulers, the dimensions for hole placement or shape formation can be marked. Care should be taken to avoid measurement errors, as they can lead to misalignment during the punching process.
Securely clamping the workpiece is another important aspect of preparing for sheet metal punching. The sheet metal should be firmly held in place to prevent movement or shifting during the punching operation. This ensures accuracy and prevents damage to the material or the punch press machine.
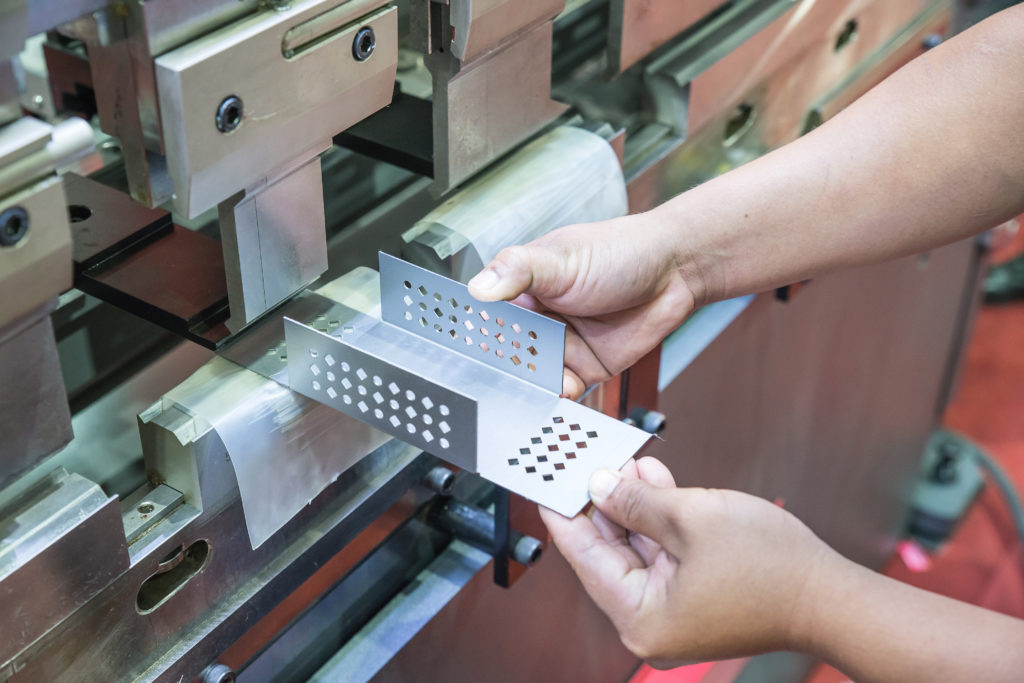
The Sheet Metal Punching Process
The sheet metal punching process involves several steps that need to be followed meticulously to achieve the desired results. Here is a step-by-step overview of the process:
- Loading the sheet metal: Carefully position and align the sheet metal on the punch press machine. Secure it in place to prevent any movement during the punching operation.
- Setting up the punch press: Configure the punch press machine with the appropriate punches, dies, and tooling required for the specific punching operation. Select punch and die sizes based on the desired hole size and shape.
- Aligning the tooling: Accurately align the punch and die to ensure precise punching. Proper alignment prevents distortion or damage to the sheet metal and extends the life of the punches and dies.
- Adjusting variables: Adjust variables like punching force, clearance, and speed based on the material thickness and desired outcome. These adjustments optimize the punching process for efficient and accurate results.
- Initiating the punching operation: Activate the punch press machine once all preparations and adjustments are made. The ram applies the necessary force, and the punch penetrates the sheet metal, creating the desired hole or shape.
- Repeating the process: For multiple holes or shapes, reposition and align the sheet metal following the same steps. This allows for the creation of multiple features in a single sheet of metal.
During the sheet metal punching process, issues may arise, such as burrs, tool wear, or misalignment. These can be addressed through troubleshooting techniques, like adjusting the clearance or performing regular maintenance on the punches and dies. Proper maintenance and care of the punch press machine ensure consistent performance and longevity.
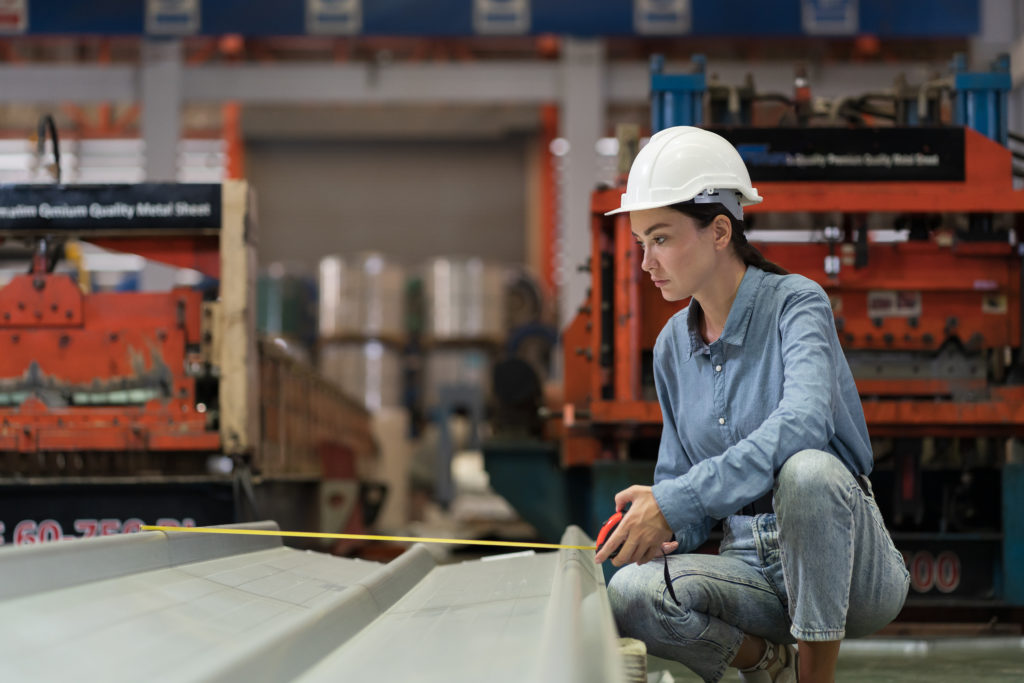
Quality Control and Safety in Sheet Metal Punching
Quality control is critical in sheet metal punching to ensure the accuracy and integrity of the finished products. Inspect the punched sheet metal for defects, like burrs or misaligned holes. Quality control measures may include visual inspection, dimensional checks, and functional testing, depending on the project’s requirements.
Safety is paramount in any manufacturing process, including sheet metal punching. Operators should be trained in the safe operation of the punch press machine and follow all safety guidelines provided by the manufacturer. Proper use of personal protective equipment, like safety glasses and gloves, is essential to prevent injuries.
Regular maintenance and inspections of the punch press machine contribute to safety. Address any abnormalities or signs of wear promptly to prevent accidents and ensure the well-being of operators.
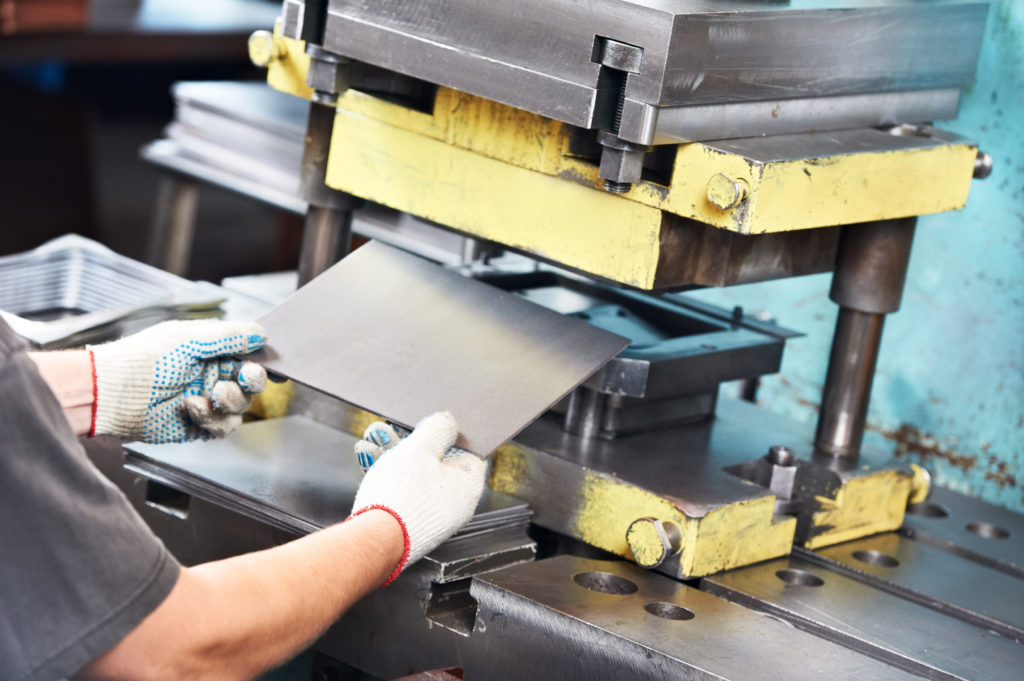
Post-Punching Operations
After the sheet metal punching process, additional operations may be required to prepare the punched components for their intended use. These operations include deburring, cleaning, and surface finishing. Deburring removes sharp edges or burrs left on the sheet metal after punching. Cleaning ensures the removal of contaminants or residues that may affect the finished product’s quality. Surface finishing techniques, like painting or powder coating, can be applied to enhance the appearance and protect the punched components.
In some cases, additional processes, like bending, welding, or assembly, may be necessary to transform the punched sheet metal into a final product. These processes are often performed in conjunction with sheet metal punching to achieve the desired form and functionality.
Sheet Metal Punching vs. Stamping
Sheet metal punching and stamping are two distinct metalworking processes, each with its own advantages and applications. While sheet metal punching primarily involves creating holes, stamping is used to achieve specific shapes or forms. Sheet metal punching is well-suited for small parts and prototypes, offering flexibility in design and hole placement. Stamping is ideal for mass production, where large quantities of identical parts are required.
When deciding between sheet metal punching and stamping, factors like product volume, design complexity, and cost-effectiveness should be considered. Sheet metal punching is often preferred for low to medium volumes or when design flexibility is crucial. Stamping, with its ability to produce high volumes of identical parts at a lower cost per unit, is more suitable for large-scale production.
Case Study: Enhancing Efficiency and Precision with Sheet Metal Punching
John works as a project manager for a manufacturing company that specializes in precision sheet metal fabrication. Recently, the company received a project to create intricate sheet metal components for a high-tech electronics device. The client had specific requirements for hole placement, shape, and size, which made it challenging to achieve the desired outcome using traditional metalworking processes.
To meet the client’s expectations, John decided to utilize sheet metal punching techniques. By using a punch press machine with the appropriate tooling, he was able to accurately create the required holes and shapes in the sheet metal. The precision and repeatability of the punching process ensured consistent results throughout the production run.
Not only did sheet metal punching provide the necessary accuracy, but it also improved efficiency in the manufacturing process. The punch press machine could perform multiple punches in quick succession, reducing the time required to create each component. This allowed John’s team to meet tight deadlines without compromising on quality.
Moreover, sheet metal punching offered cost savings compared to alternative methods. By minimizing waste and utilizing the sheet metal efficiently, the project stayed within budget. The streamlined process also reduced the need for extensive post-punching operations, such as deburring or surface finishing.
Overall, this case study demonstrates the effectiveness of sheet metal punching in enhancing efficiency and precision in precision sheet metal fabrication. By leveraging the capabilities of the punch press machine and selecting the right tooling, John’s team successfully met the client’s requirements while optimizing production time and costs. The utilization of sheet metal punching techniques proved to be a valuable solution for complex projects that demand both accuracy and efficiency.
Conclusion
Sheet metal punching is a vital process in precision sheet metal fabrication, offering speed, efficiency, and flexibility in creating holes, shapes, and features. By understanding the equipment, tools, and techniques involved, you can harness the benefits of sheet metal punching in various industries. Remember to prioritize quality control, safety, and post-punching operations to ensure the production of high-quality components. Whether you choose sheet metal punching or stamping, make an informed decision based on your specific requirements and production volume.
Common Questions
What is sheet metal punching?
Sheet metal punching is a process that uses a punch press to create holes in sheet metal.
Who can benefit from sheet metal punching?
Manufacturers and fabricators in the precision sheet metal fabrication industry can benefit from sheet metal punching.
How does sheet metal punching work?
Sheet metal punching works by using a punch and die set to forcefully pierce holes in sheet metal.
What are the advantages of sheet metal punching?
Sheet metal punching offers high precision, quick production, and cost-effective hole creation in sheet metal.
How can sheet metal punching improve efficiency?
Sheet metal punching eliminates the need for time-consuming drilling or other manual hole creation methods.
What if my sheet metal design requires complex hole patterns?
Precision sheet metal fabricators can use advanced CNC punch presses to create complex hole patterns accurately.