What the reader will learn by reading this article:
- The importance and versatility of sheet metal forming in precision sheet metal fabrication.
- The different sheet metal forming processes, such as bending, spinning, drawing, and stretching.
- The tools and techniques used in sheet metal forming, including dies, punching tools, press brakes, and roll forming.
Sheet metal forming is a versatile and cost-effective manufacturing technique that plays a crucial role in shaping various metal components used in industries such as automotive, aerospace, and electronics. In this comprehensive guide, we will explore the intricacies of sheet metal forming and its importance in precision fabrication.
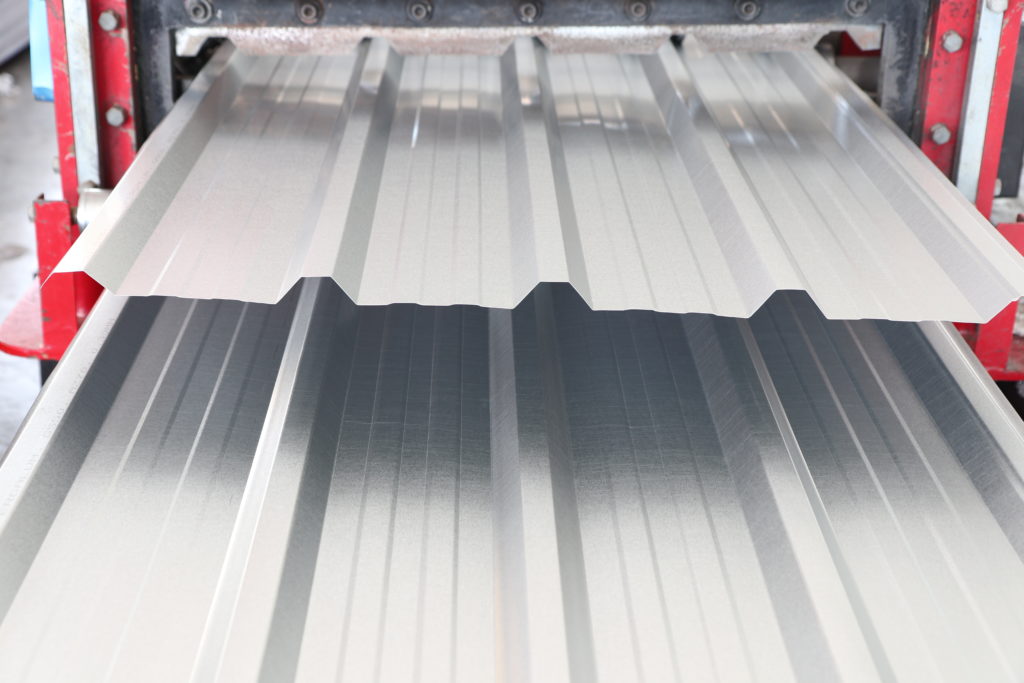
Understanding Sheet Metal
Before delving into the world of sheet metal forming, it is essential to understand the material itself. Sheet metal is a flat, thin, and malleable material that is commonly used in the manufacturing industry. It is typically made of metals such as steel, aluminum, or copper, and comes in various thicknesses, ranging from as thin as 0.4 mm to as thick as 6 mm.
Selecting the right type and thickness of sheet metal is crucial for successful forming processes. Different metals possess varying mechanical properties and behaviors during forming. For example, aluminum is lightweight and highly formable, making it suitable for applications that require intricate shapes. On the other hand, steel offers excellent strength and durability, making it ideal for structural components.
The formability of sheet metal is influenced by several factors, including its thickness, ductility, and strain hardening characteristics. Thicker sheets may require more force to deform, while highly ductile metals can withstand greater deformation without fracture. Strain hardening, which causes the metal to become harder and less ductile as it is deformed, also affects the formability.
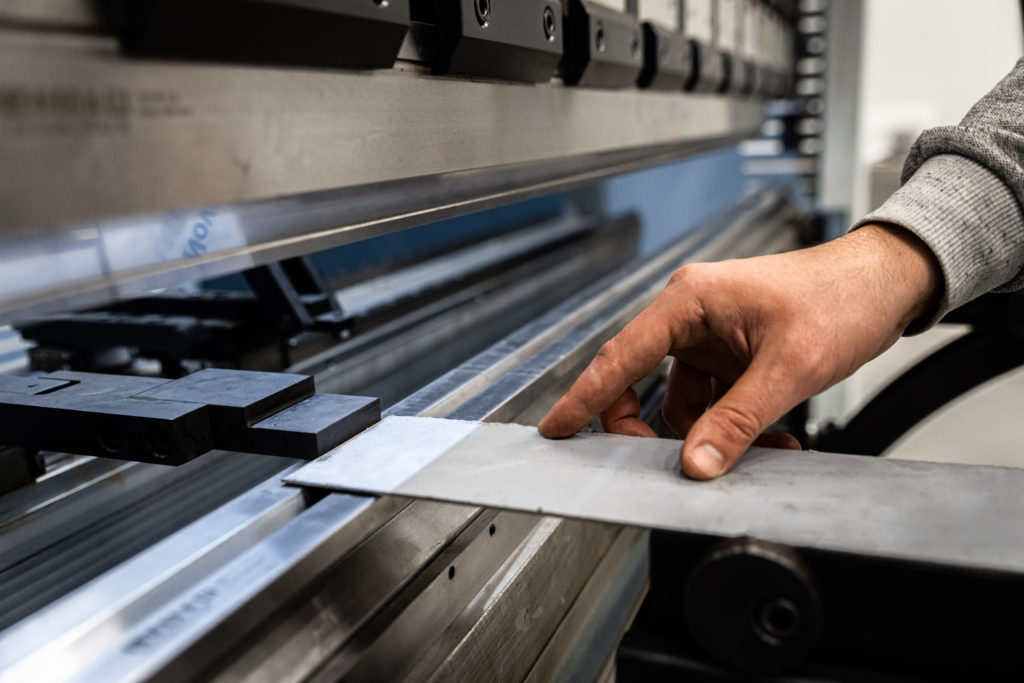
Common Sheet Metal Forming Processes
Sheet metal forming encompasses a range of processes that transform flat sheets into three-dimensional components. Let’s explore some of the most commonly used forming processes:
Bending
Bending is a fundamental sheet metal forming process that involves deforming the material to achieve desired angles or shapes. It is commonly used to create features such as flanges, brackets, and channels. The bending process typically involves clamping the sheet metal between a punch and a die, which exert a force to deform the material.
There are several types of bending methods used in sheet metal fabrication. Air bending, for example, involves using a punch and die to form the desired angle without completely bottoming out the material. This method allows for greater flexibility and adjustability in achieving different bend angles. Bottoming, on the other hand, involves fully pressing the material into the die to achieve a precise angle. Coining is a bending method that produces sharp, crisp bends by applying significant force to the workpiece.
Spinning
Spinning is a specialized sheet metal forming process used to create cylindrical or conical shapes. It involves rotating a sheet metal disc against a mandrel while applying force. As the spinning tool moves along the surface of the sheet metal, it gradually forms the desired shape.
Spinning offers several advantages over other forming processes. It allows for the creation of seamless shapes, eliminating the need for joints or welding. It also offers excellent dimensional accuracy and surface finish. Spinning is commonly used in the production of components such as automotive wheels, lighting fixtures, and satellite dishes.
Drawing
Drawing is a process that involves transforming a flat sheet metal blank into a cup or shell shape. It utilizes a die and punch to stretch the material and form it into the desired shape. Deep drawing is a common drawing method used to create components with a significant depth-to-diameter ratio, such as kitchen sinks and beverage cans.
Another variation of drawing is hydroforming, which uses fluid pressure to shape the sheet metal. This process involves placing the sheet metal on a die and applying fluid pressure to force it into the desired shape. Hydroforming offers greater design freedom and allows for the production of complex shapes with minimal material thinning.
Stretching
Stretching is a sheet metal forming process that involves elongating or expanding the material to create complex shapes. It is commonly used to manufacture components such as automotive body panels and aircraft fuselages. Stretch forming combines stretching and bending to achieve the desired shape.
Stretch forming typically involves clamping the sheet metal at its edges and applying a stretching force to elongate it. This process allows for the creation of curved or contoured shapes that cannot be achieved through simple bending. Stretch forming offers excellent dimensional accuracy and minimizes material wrinkling or deformation.
Personal Story: Overcoming Challenges in Sheet Metal Forming
At XYZ Manufacturing, we recently took on a challenging sheet metal forming project that required precise fabrication and complex shapes. Our client, a leading aerospace company, needed a series of custom sheet metal components for their new aircraft design. The parts had to be lightweight, durable, and able to withstand extreme conditions.
One particular component, a curved panel for the aircraft’s fuselage, posed a significant challenge. The design called for a compound curve, meaning the panel had to be formed into a shape that combined both convex and concave curves. Achieving this shape with traditional sheet metal forming processes was difficult due to the complexity and tight tolerances required.
To overcome this challenge, our team developed a unique approach using the stretching process. We utilized a specialized stretching machine that allowed us to gradually elongate the sheet metal in a controlled manner, creating the desired compound curve. This method required precise calculations and adjustments to ensure the final shape met the design specifications.
Throughout the project, we encountered various obstacles, such as material springback and wrinkling of the sheet metal. However, our experienced team of engineers and technicians worked diligently to optimize the process parameters and implement corrective measures. Through iterative testing and adjustments, we were able to overcome these challenges and successfully produce the curved panels to meet the client’s requirements.
The impact of sheet metal forming on the final product quality and performance was evident in this project. The accurately formed components contributed to the overall aerodynamic efficiency and structural integrity of the aircraft. Our client was impressed with the precision and attention to detail in our fabrication process, which ultimately led to a successful partnership and future collaborations.
This case study highlights the importance of expertise, innovation, and problem-solving skills in sheet metal forming. It demonstrates the critical role that precision fabrication plays in industries such as aerospace, where even the slightest deviation can have significant consequences. By understanding the unique requirements of each project and leveraging the right tools and techniques, we can overcome challenges and deliver exceptional results in sheet metal forming.
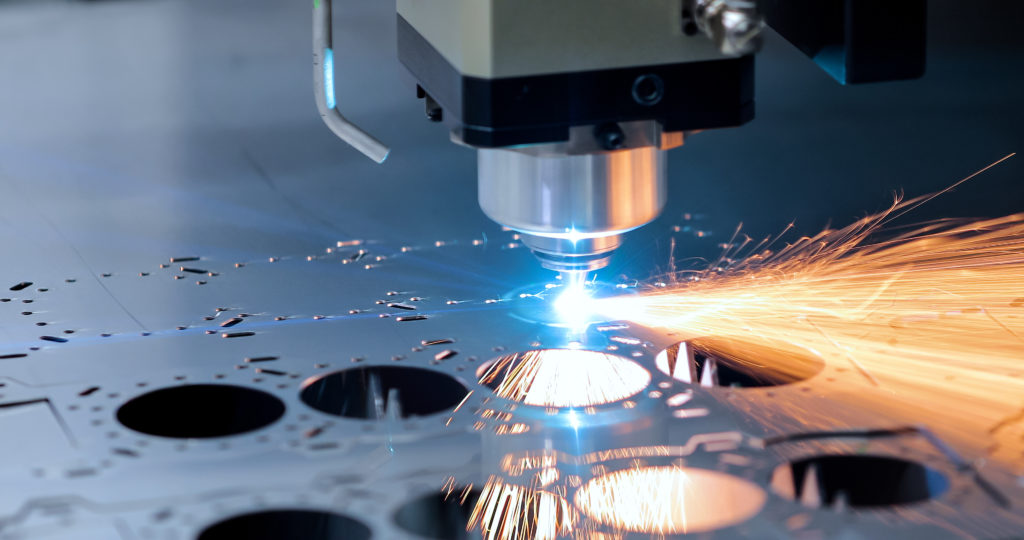
Tools and Techniques for Sheet Metal Forming
Sheet metal forming requires the use of various tools and techniques to achieve precise and accurate results. Let’s explore some of the key tools and techniques employed in the process:
Dies
Dies play a critical role in sheet metal forming. They are specialized tools that shape the material by exerting pressure or force. Dies can be classified into several types, including bending dies, drawing dies, and forming dies. Each type of die is designed to accommodate specific forming processes and achieve the desired shape.
Die design considerations include factors such as material flow, radii, and clearance. Optimizing the design of the die can help minimize material waste, reduce production time, and ensure consistent quality. Advanced die design techniques, such as finite element analysis (FEA), enable manufacturers to simulate the forming process and optimize the die design before production.
Punching Tools
Punching tools are used to create holes, notches, or other features in sheet metal. They are typically attached to a press or a punching machine, which applies force to the punch to deform the material. Punching is commonly used in applications such as perforated sheets, electrical enclosures, and automotive body panels.
There are different types of punching operations, including blanking, piercing, and notching. Blanking involves cutting out a flat piece from the sheet metal, while piercing creates a hole or opening in the material. Notching is a process that removes a small piece of material to create a specific shape or feature.
Press Brakes
Press brakes are versatile machines used for precise bending and forming of sheet metal. They consist of a punch and a die, which exert force on the material to achieve the desired bend angle or shape. Press brakes are commonly used in applications such as brackets, enclosures, and structural components.
There are different types of press brakes available, including mechanical, hydraulic, and servo-electric. Mechanical press brakes utilize a motor and a flywheel to generate force, while hydraulic press brakes use hydraulic cylinders. Servo-electric press brakes employ servo motors to achieve high precision and energy efficiency.
Roll Forming
Roll forming is a continuous sheet metal forming process that gradually shapes the material using a series of rollers. It is commonly used to produce components with consistent cross-sections, such as rails, tubes, and profiles. Roll forming offers several advantages, including high production speed, excellent dimensional accuracy, and repeatability.
The process begins with a flat strip of sheet metal, which is fed through a series of rollers that progressively shape the material. Each set of rollers performs a specific bending or forming operation, gradually transforming the flat strip into the desired shape. Roll forming is particularly suitable for high-volume production and long components.
Traditional Metal Tooling | 3D Printed Tools |
---|---|
Higher upfront costs and lead times | Lower upfront costs and shorter lead times |
Limited customization and iteration options | Easy customization and quick iteration |
Suitable for high-volume production and demanding forming processes | More suitable for prototyping and low volume production |
Consistent mechanical properties | Mechanical properties may not be comparable to traditional metal tooling |
Longer production timelines | Can be slower than traditional machining methods |
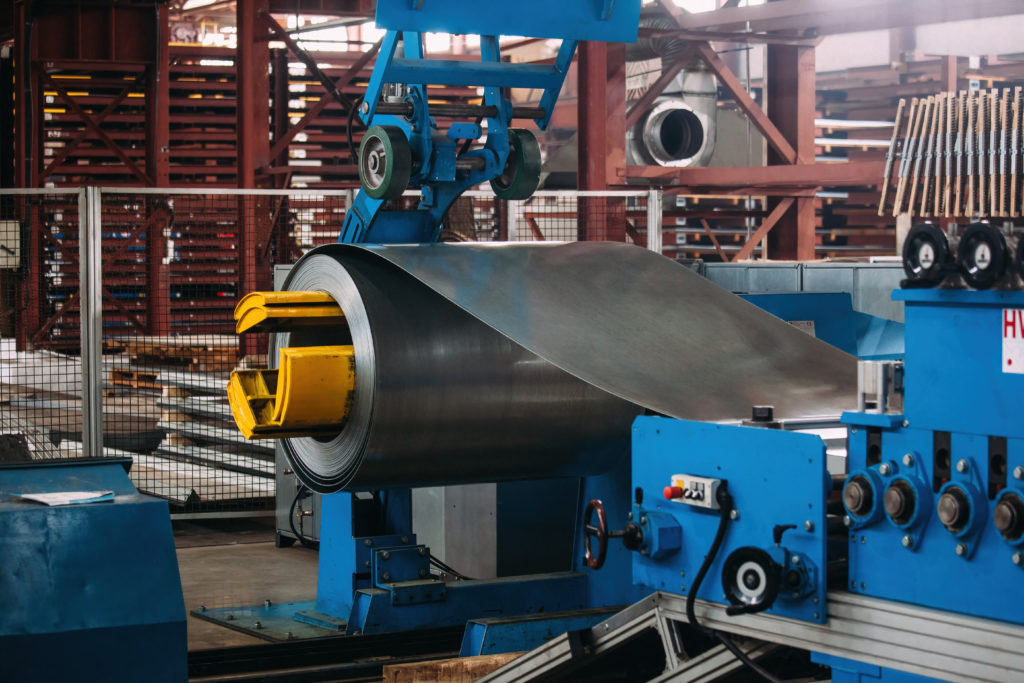
Advantages of Using 3D Printed Tools in Sheet Metal Forming
The emergence of 3D printing technology has revolutionized various industries, including sheet metal forming. The use of 3D printed tools offers several advantages over traditional metal tooling.
Benefits of using 3D printed tools for prototyping and low volume production
3D printed tools provide manufacturers with a cost-effective solution for prototyping and low volume production. Traditional metal tooling often requires significant upfront costs and lead times, making it impractical for small production runs. With 3D printing, manufacturers can quickly produce custom tools with complex geometries, reducing both cost and lead time.
Cost and lead time advantages compared to traditional metal tooling
Traditional metal tooling can be expensive and time-consuming to produce, especially for complex forming processes. 3D printed tools offer a more cost-effective and time-efficient alternative. By utilizing 3D printing technology, manufacturers can rapidly iterate and optimize tool designs without the need for expensive tooling modifications.
Customization and quick iteration with 3D printed tools
One of the significant advantages of 3D printed tools is the ability to customize and iterate designs quickly. Manufacturers can easily modify tool designs to accommodate specific forming requirements or optimize performance. This flexibility allows for greater design freedom and faster response to design changes or customer requests.
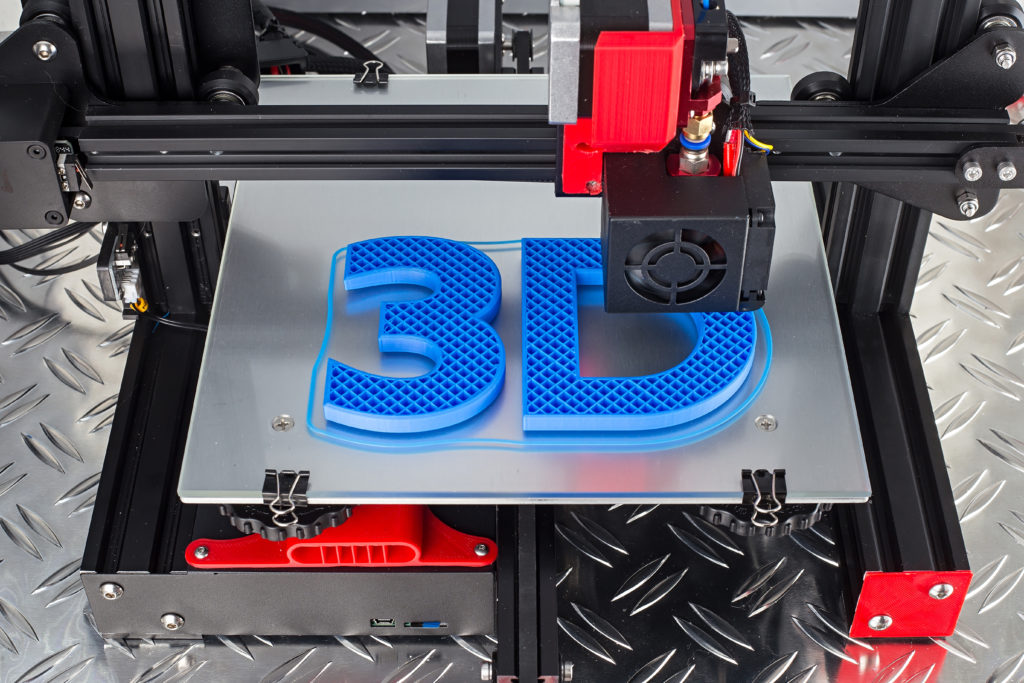
Limitations and considerations when using 3D printed tools
While 3D printed tools offer numerous advantages, it is essential to consider their limitations. The mechanical properties of 3D printed materials may not be comparable to those of traditional metal tooling, limiting their suitability for high-volume production or highly demanding forming processes. Additionally, 3D printing can be slower than traditional machining methods, which may impact production timelines.
To explore the potential of 3D printed tools further, it is recommended to refer to research papers and case studies from experts in the field. Sheet Metal Forming is an excellent resource that provides detailed information on rapid tooling for sheet metal forming, including white papers and webinars for in-depth learning.
Frequently Asked Questions
What is sheet metal forming?
Sheet metal forming is a process that shapes flat metal sheets into desired 3D forms.
Who uses sheet metal forming?
Various industries such as automotive, aerospace, and electronics rely on sheet metal forming.
How does sheet metal forming work?
Sheet metal forming involves bending, punching, and cutting to shape metal sheets using specialized tools and machines.
What are the benefits of precision sheet metal fabrication?
Precision sheet metal fabrication ensures accurate, high-quality parts with tight tolerances for optimal performance.
How can precision sheet metal fabrication improve product durability?
By using precise measurements and high-quality materials, precision sheet metal fabrication creates durable products that can withstand rigorous conditions.
But isn’t sheet metal forming expensive?
While initial costs may be higher, sheet metal forming offers long-term cost savings due to its durability and ability to create complex shapes efficiently.