Are you looking for an efficient and cost-effective method for creating intricate designs and shapes in sheet metal? Look no further than sheet metal punching. This process involves creating holes in sheet metal using a punch press or a CNC punching machine, and it is essential for precision fabrication. In this ultimate guide, we will explore the basics of sheet metal punching, its advantages, types of machines used, tooling and dies, design considerations, quality control, applications, and more.
Sheet Metal Punching in Precision Fabrication: The Ultimate Guide
By reading this article, you will learn: – What sheet metal punching is and how it works – The advantages of sheet metal punching – The difference between punch press and CNC punching – How tooling and dies are used in sheet metal punching – Design considerations and quality control in sheet metal punching – Applications and examples of punched parts in different industries.
Sheet Metal Punching Basics
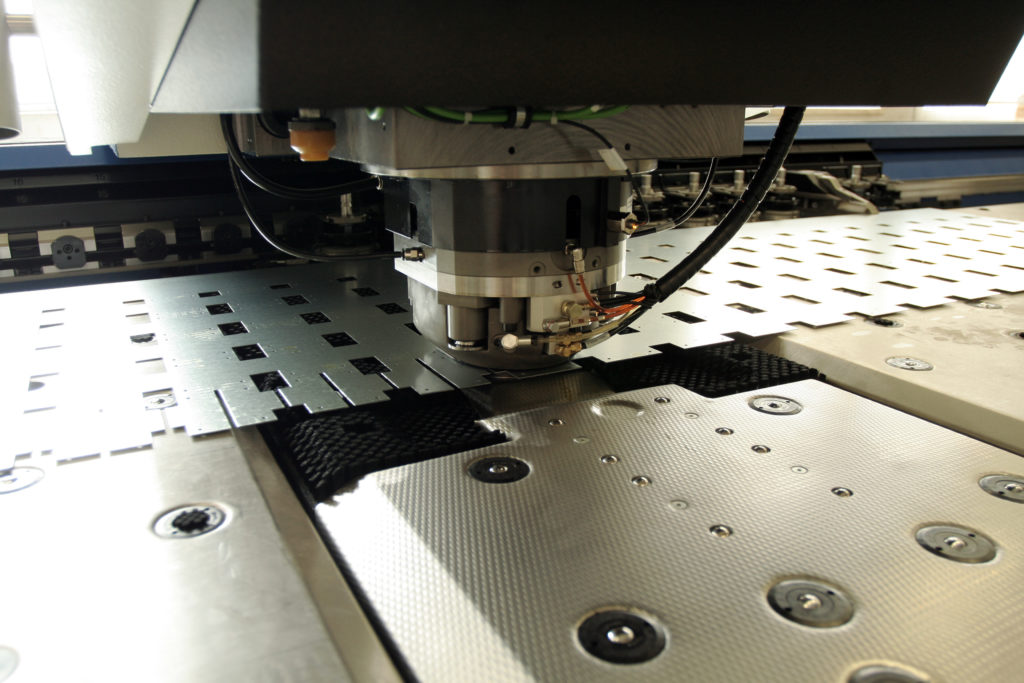
Sheet Metal Punching Definition
Sheet metal punching is the process of creating holes in sheet metal using a punch press or a CNC punching machine. The process involves cutting and piercing the sheet metal using dies mounted on presses. Different metals require specific pressure for punching, and the process involves creating holes of various shapes and sizes.
How Sheet Metal Punching Works
In sheet metal punching, the sheet metal is positioned on a die, and the punch presses down on the metal, creating a hole through the sheet. The punch and die are designed to create the desired hole shape, and the process can create holes of different sizes and shapes. The process can also be used to create notches, louvers, and other shapes in sheet metal.
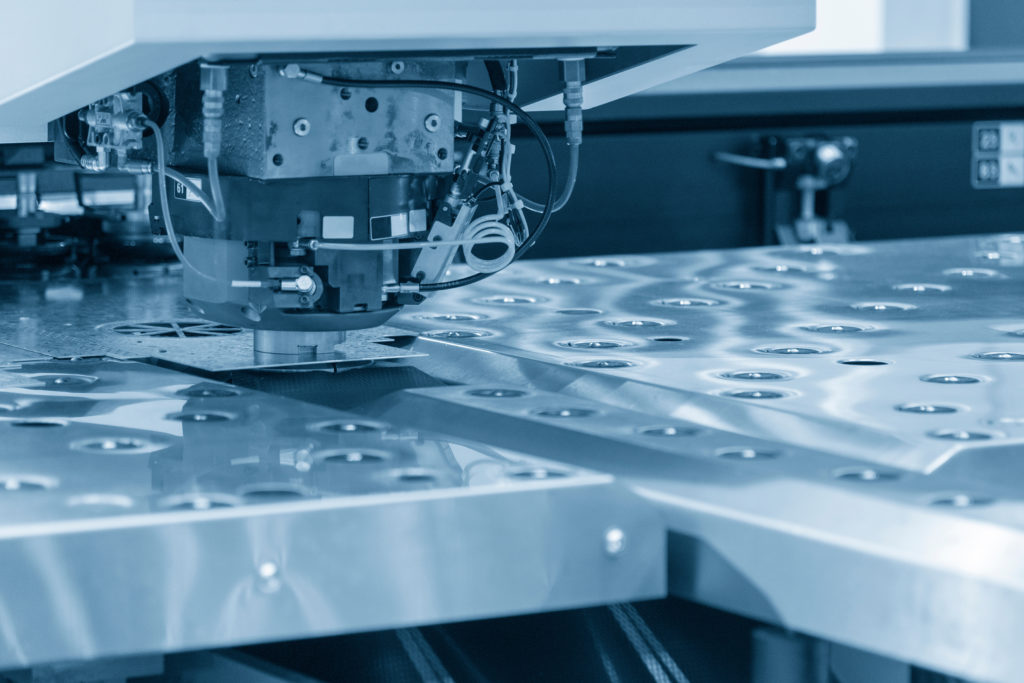
Types of Metals for Sheet Metal Punching
Sheet metal punching can be performed on various metals, including steel, stainless steel, aluminum, brass, copper, and others. Different metals require different forces and pressure for punching, and the process is adjusted accordingly.
Sheet Metal Thickness
The thickness of the material that can be punched depends on the machine used. For example, a punch press can typically punch materials up to 1/4 inch thick, while CNC punching machines can punch materials up to 1 inch thick.
Types of Punches in Sheet Metal Punching
There are various types of punches used in sheet metal punching, including round punches, oblong punches, square punches, rectangular punches, and more. The punches are designed to create different hole shapes and sizes, and they can be customized to suit specific applications.
Advantages of Sheet Metal Punching
Efficiency and Cost-Effectiveness
Sheet metal punching is a highly efficient and cost-effective process. It can be automated, reducing the need for manual labor, and it is generally faster and more accurate than other methods. It is also less expensive than some other methods, such as laser cutting.
Superior Quality and Precision
Sheet metal punching creates high-quality and precise parts. The process can create clean and accurate holes, and it can be used to create intricate designs and shapes. The finished parts are typically of high quality and require little or no additional finishing.
Accurate Hole Placement
Sheet metal punching allows for accurate hole placement, which is essential for many applications. The process can create holes with tight tolerances, ensuring that parts fit together perfectly.
Versatility in Design
Sheet metal punching allows for versatility in design. The process can create a wide variety of shapes and sizes, and it can be used to create parts with complex geometries. This versatility allows for greater creativity in design and a wider range of applications.
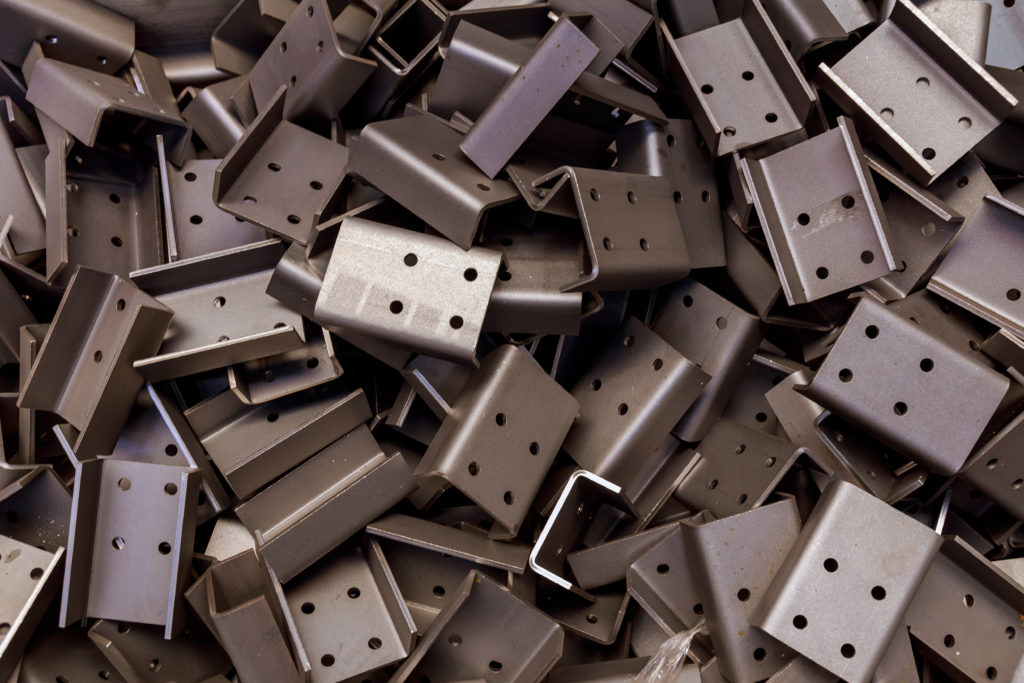
Punch Press vs. CNC Punching
Punch Press and CNC Punching Machines Definition
A punch press is a machine that uses a mechanical or hydraulic press to punch holes in sheet metal. A CNC punching machine is a computer-controlled machine that uses a punch to create holes in sheet metal.
Advantages and Disadvantages of Each Machine Type
Punch presses are generally more cost-effective than CNC punching machines and are better suited for high-volume production runs. CNC punching machines are more versatile and can create more complex shapes and designs than punch presses. However, they are generally more expensive and require more maintenance.
Factors that Determine Machine Selection
The choice between a punch press and a CNC punching machine depends on several factors, including the volume of production, the complexity of the design, the thickness of the material, and the available budget.
Punch Press | CNC Punching Machine |
---|---|
Uses a mechanical or hydraulic press to punch holes in sheet metal | Uses a punch to create holes in sheet metal and is computer-controlled |
More cost-effective than CNC punching machines | More versatile and can create more complex shapes and designs than punch presses |
Better suited for high-volume production runs | Generally more expensive and require more maintenance |
Can only produce simple shapes and designs | Can produce intricate and complex shapes and designs |
Limited customization options | High degree of customization options |
Ideal for punching holes in thicker materials | Ideal for punching holes in thinner materials |
Reasoning: This table compares the punch press and the CNC punching machine, two major types of machines used in sheet metal punching. The table highlights the advantages and disadvantages of each machine type, as well as factors that determine machine selection. It also includes a comparison of the types of shapes and designs that can be produced using each machine type. This table provides a quick overview of the differences between the two machine types and can help readers make informed decisions about which machine is best suited for their needs.
Type of Tooling and Die | Description |
---|---|
Round dies | Used to create circular holes in sheet metal |
Oblong dies | Used to create elongated holes in sheet metal |
Square dies | Used to create square holes in sheet metal |
Rectangular dies | Used to create rectangular holes in sheet metal |
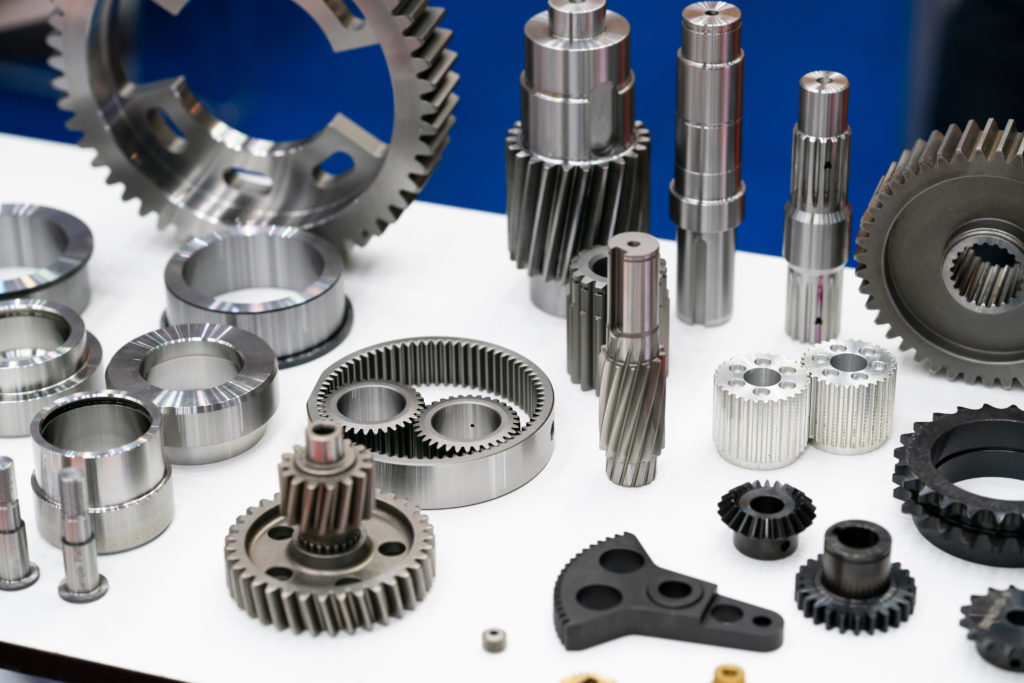
Tooling and Dies
Importance of Tooling and Dies in Sheet Metal Punching
Tooling and dies are essential components of sheet metal punching. The quality of the tooling and dies used can have a significant impact on the quality of the finished parts.
Types of Tooling and Dies
There are several types of tooling and dies used in sheet metal punching, including round, oblong, square, and rectangular dies. The dies are typically made of hardened steel and are designed to withstand the pressures of punching.
Customization of Tooling and Dies
Tooling and dies can be customized to suit specific applications. Customized tooling and dies can create parts with unique shapes and sizes, ensuring that the finished parts meet the required specifications.
Design Considerations
Case Study: Customized Tooling and Dies for Sheet Metal Punching
At ABC Fabrication, we had a client who needed a custom part made for their product but the design required unique hole placements that could not be achieved with standard tooling and dies. The client had already tried other fabrication methods but was not satisfied with the results.
After discussing the requirements with the client, our team of engineers and toolmakers designed and fabricated a customized tooling and die set that was specific to the client’s part. This allowed for the precise hole placement needed for their design.
Using the customized tooling and dies, we were able to produce high-quality parts with consistent accuracy, meeting the client’s exact specifications. The client was pleased with the results and has continued to work with us for their future fabrication needs.
This case study demonstrates the importance of customized tooling and dies in sheet metal punching and how it can help achieve unique design requirements. It also shows the benefits of working with an experienced fabrication company that can provide customized solutions to meet specific needs.
Optimization of Designs for the Punching Process
Designs should be optimized for the punching process to ensure the best possible results. This may involve adjusting the design to accommodate the limitations of the punching machine, such as the thickness of the material or the size of the punch.
Avoidance of Common Pitfalls That Affect Quality
Designs should also avoid common pitfalls that can affect the quality of the finished parts, such as sharp corners, small holes close together, or holes too close to the edge of the material.
Use of CAD Software for Design
CAD software can be used to design parts for sheet metal punching. This software can create 3D models of the part, allowing designers to visualize the finished part and make any necessary adjustments before production.
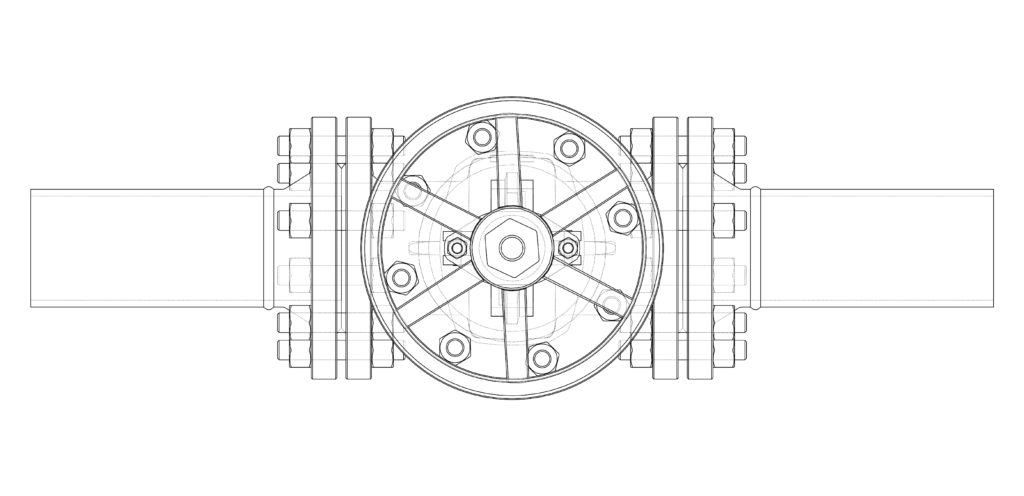
Quality Control
Importance of Quality Control in Sheet Metal Punching
Quality control is essential in sheet metal punching to ensure that the finished parts meet the required specifications and standards. Quality control can help identify any issues early in the process, reducing the risk of costly errors.
Methods Used to Ensure Parts Meet Required Specifications and Standards
Several methods are used to ensure that parts meet the required specifications and standards. These methods may include visual inspection, dimensional inspection, and testing.
Inspection and Testing
Inspection and testing may involve checking the dimensions of the finished parts, verifying the hole placement and size, and testing the parts for strength and durability.
Applications
Applications of Sheet Metal Punching in Precision Fabrication
Sheet metal punching is used in many applications in precision fabrication, including automotive, aerospace, electronics, and more. It is used to create parts such as brackets, enclosures, panels, and more.
Examples of Punched Parts in Different Industries
In the automotive industry, sheet metal punching is used to create parts such as brackets, engine covers, and door panels. In the aerospace industry, it is used to create parts such as wing skins, fuselage panels, and engine components. In the electronics industry, it is used to create parts such as enclosures, faceplates, and brackets.
Case Studies
Case Study 1: Automotive Industry
A sheet metal punching company was contracted by an automotive manufacturer to create door panels for a new line of vehicles. The company used a CNC punching machine to create the intricate designs required for the door panels. The finished parts were of high quality and met all of the required specifications.
Case Study 2: Aerospace Industry
A sheet metal punching company was contracted by an aerospace manufacturer to create wing skins for a new aircraft. The company used a punch press to create the required holes and shapes in the sheet metal. The finished parts were of high quality and met all of the required specifications.
Conclusion
Sheet metal punching is a versatile and cost-effective process that can create high-quality, precise parts. By understanding the basics of sheet metal punching, the advantages of different machines, the importance of tooling and dies, design considerations, quality control, and applications, you can make informed decisions about your precision fabrication needs. With the use of case studies, it is clear that sheet metal punching is not only an effective method for precision fabrication, but it can also be applied to a wide range of industries.