What readers will learn from this article:
- Definition and significance of laser cutting
- Advantages of laser cutting over traditional cutting methods
- Basic principles and process of laser cutting
- Types of lasers used in laser cutting and their characteristics
- Factors affecting laser cutting quality and precision
- Materials suitable for laser cutting and limitations
- Recent advancements in laser cutting technology and their impact
- Benefits of laser cutting such as achieving intricate designs and reducing production costs
- Common applications of laser cutting in various industries
- Tips for choosing a reliable laser cutting service provider
- Safety considerations in laser cutting operations
- Future trends in laser cutting and emerging technologies.
Laser cutting has revolutionized the world of precision sheet metal fabrication, offering a wide range of advantages over traditional cutting methods. In this comprehensive handbook, we will explore the principles, process, types of lasers, factors affecting quality, suitable materials, advancements in technology, applications, choosing a service provider, safety considerations, and future trends in laser cutting. Whether you are a professional in the industry or simply curious about this cutting-edge technology, this guide will provide you with valuable insights.
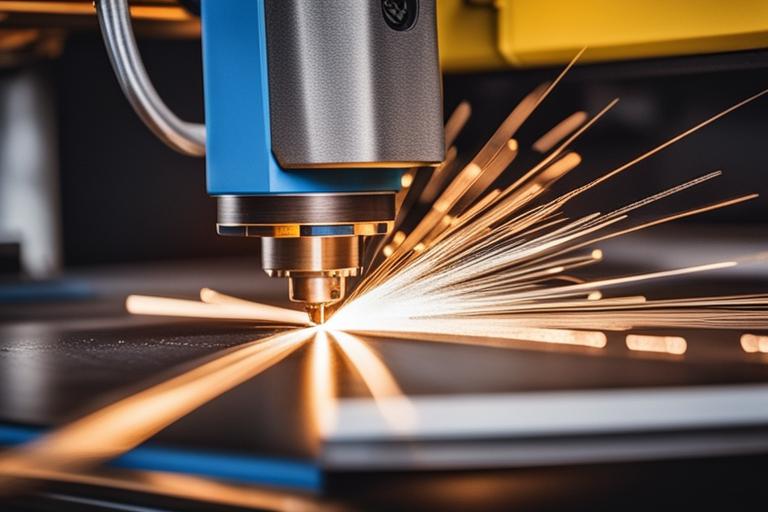
Principles and Process of Laser Cutting
Basic principles of laser cutting
Laser cutting involves using a high-powered laser beam to cut through various materials with precision. The laser beam is generated by a laser resonator, which amplifies the light and directs it towards a focusing lens. The focused laser beam is then directed onto the material to be cut, melting or vaporizing it along the predetermined cutting path.
Components of a laser cutting system
A laser cutting system consists of several key components that work together to achieve precise and efficient cutting. These components include the laser resonator, focusing lens, cutting head, motion control system, and assist gas system. Each component plays a crucial role in ensuring optimal cutting performance and quality.
Step-by-step process of laser cutting
The laser cutting process involves several steps that ensure accurate and clean cuts. First, the material to be cut is securely positioned on a cutting bed. The laser beam is then directed onto the material, melting or vaporizing it along the cutting path. The motion control system precisely moves the cutting head, guiding the laser beam along the desired cutting path. As the laser cuts through the material, an assist gas, such as oxygen or nitrogen, is used to remove molten material and prevent excessive heat buildup. This results in clean and precise cuts.

Types of Lasers Used in Laser Cutting
CO2 lasers and their characteristics
CO2 lasers are widely used in laser cutting due to their versatility and ability to cut a wide range of materials. These lasers generate a laser beam using a mixture of carbon dioxide, nitrogen, and helium gases. CO2 lasers are particularly effective for cutting non-metallic materials such as wood, acrylic, and plastics. They offer high power and can achieve intricate cuts with minimal heat-affected zones.
Fiber lasers and their advantages
Fiber lasers have gained popularity in recent years due to their high efficiency and ability to cut through various metals. These lasers utilize optical fibers doped with rare-earth elements, such as erbium or ytterbium, to generate a laser beam. Fiber lasers are known for their high power density, making them ideal for cutting thin to medium-thickness metals. They offer excellent beam quality, resulting in precise and clean cuts.
Other types of lasers used in specific applications
In addition to CO2 and fiber lasers, other types of lasers are used for specific applications. For example, neodymium-doped yttrium aluminum garnet (Nd:YAG) lasers are commonly used for welding and engraving. Excimer lasers are suitable for cutting and drilling fragile materials, such as glass and ceramics. The choice of laser depends on the specific material and cutting requirements.
Factors Affecting Laser Cutting Quality and Precision | Impact |
---|---|
Laser power | Higher power allows for faster cutting speeds and the ability to cut through thicker materials. However, it’s important to find the optimal balance to avoid excessive heat and potential damage to the material. |
Beam focus | A tightly focused beam allows for finer and more intricate cuts, while a wider beam focus may be necessary for cutting thicker materials. Achieving the right beam focus is crucial for maintaining cutting precision and achieving desired results. |
Cutting speed | Higher cutting speeds increase productivity but may result in reduced cutting quality. Slower cutting speeds allow for more precise cuts but may prolong production times. Finding the optimal cutting speed depends on the material thickness, desired quality, and production requirements. |

Factors Affecting Laser Cutting Quality and Precision
Laser power and its impact on cutting capabilities
The power of the laser used in laser cutting directly affects its cutting capabilities. Higher laser power allows for faster cutting speeds and the ability to cut through thicker materials. However, it’s important to find the optimal balance between power and cutting speed to avoid excessive heat and potential damage to the material.
Beam focus and its effect on cutting precision
The focus of the laser beam plays a critical role in determining the precision of the cuts. A tightly focused beam allows for finer and more intricate cuts, while a wider beam focus may be necessary for cutting thicker materials. Achieving the right beam focus is crucial for maintaining cutting precision and achieving desired results.
Cutting speed and its relation to efficiency and quality
The cutting speed, or the rate at which the laser beam moves across the material, affects both efficiency and quality. Higher cutting speeds increase productivity but may result in reduced cutting quality. Slower cutting speeds allow for more precise cuts but may prolong production times. Finding the optimal cutting speed depends on the material thickness, desired quality, and production requirements.

Safety Considerations in Laser Cutting
Laser cutting is a powerful and efficient method of sheet metal fabrication, but it is important to prioritize safety when working with lasers. One example of the importance of safety measures in laser cutting operations is the case of Sarah, a skilled metal fabricator who experienced a near-miss incident.
Sarah’s Story: A Near-Miss Incident
Sarah had been working in the sheet metal fabrication industry for over a decade. She was experienced and well-trained in laser cutting techniques, but one day, she encountered a potentially dangerous situation. While operating a laser cutting machine, Sarah noticed a small flame coming from the nozzle area. She immediately hit the emergency stop button and activated the fire suppression system.
Thanks to her quick thinking and adherence to safety protocols, Sarah was able to prevent a major fire. Upon further investigation, it was determined that a piece of scrap metal had inadvertently fallen into the laser beam path, causing the flame. This incident highlighted the importance of regular maintenance and inspection of laser cutting machines, as well as the need for a vigilant eye to spot potential hazards.
Ensuring Safety in Laser Cutting Operations
Sarah’s story serves as a reminder of the critical safety considerations that must be taken into account when working with lasers. Some key safety measures to implement in laser cutting operations include:
- Machine Maintenance: Regularly inspecting and maintaining laser cutting machines, ensuring that all components are in good working condition and any potential issues are addressed promptly.
- Fire Safety: Installing fire suppression systems and ensuring that operators are trained in their use. It is also important to keep the work area clear of flammable materials and have fire extinguishers readily available.
- Personal Protective Equipment (PPE): Providing operators with appropriate PPE, such as safety glasses, gloves, and protective clothing, to protect against laser radiation and thermal hazards.
- Training and Education: Ensuring that all operators are properly trained in laser cutting techniques, safety procedures, and emergency protocols.
- Workplace Organization: Maintaining a clean and organized work environment to minimize the risk of accidents and to ensure easy access to emergency exits and equipment.
By implementing these safety measures and staying vigilant, metal fabricators can minimize the risk of accidents and create a safe working environment for laser cutting operations.
Remember, safety should always be the top priority in any laser cutting operation. Taking the necessary precautions will not only protect employees but also help maintain the integrity and efficiency of the laser cutting process.

Materials Suitable for Laser Cutting
Laser cutting is suitable for a wide range of materials, including metals, plastics, composites, rubbers, and foams. Metals such as stainless steel, aluminum, and mild steel can be cut with high precision and minimal heat-affected zones. Non-metallic materials like acrylic, wood, and leather can also be easily cut using laser technology, allowing for intricate designs and patterns.
Conclusion
Laser cutting is a highly versatile and efficient method for cutting a wide range of materials. Its ability to produce precise and intricate cuts makes it a popular choice in various industries. However, it is important to be aware of the challenges and limitations that certain materials may present when it comes to laser cutting. Reflective materials like copper and brass, as well as materials with high thermal conductivity, can affect cutting efficiency and quality. Therefore, understanding the properties and limitations of different materials is crucial for successful laser cutting projects.
If you would like to learn more about laser cutting and its applications, we encourage you to visit our websites Ponoko and Xometry. Our team of experts is ready to assist you with any questions or inquiries you may have. Contact us today to discuss your laser cutting needs and to explore how we can help bring your ideas to life.
Frequently Asked Questions
Who uses laser cutting in precision sheet metal fabrication?
Manufacturers and industries that require intricate designs and precise cuts use laser cutting in precision sheet metal fabrication.
What is laser cutting in precision sheet metal fabrication?
Laser cutting is a process that uses a high-powered laser beam to cut through sheet metal with extreme precision and accuracy.
How does laser cutting work in precision sheet metal fabrication?
Laser cutting works by focusing a high-intensity laser beam onto the sheet metal, melting and vaporizing the material along the desired cutting path.
What are the benefits of laser cutting in precision sheet metal fabrication?
Laser cutting offers advantages such as high precision, clean cuts, minimal material waste, and the ability to cut complex shapes with ease.
How does laser cutting compare to other cutting methods in precision sheet metal fabrication?
Laser cutting surpasses traditional methods by providing tighter tolerances, smoother edges, and the ability to cut a wider range of materials.
What if I have specific design requirements for my precision sheet metal fabrication project?
Laser cutting can accommodate various design requirements, including intricate patterns, fine details, and precise measurements, ensuring your project’s success.