What will readers learn from this article?
- The definition and significance of sheet metal forming in precision sheet metal fabrication.
- The different types of sheet metal forming processes, their characteristics, and applications.
- Design considerations, tooling and equipment, process steps, quality control, challenges and troubleshooting, advancements and trends, and applications and industries utilizing sheet metal forming.
Sheet metal forming is a vital process in precision sheet metal fabrication. It involves shaping and manipulating thin metal sheets into desired components and structures. This versatile fabrication technique finds applications in various industries such as automotive, aerospace, electronics, construction, and appliances. In this comprehensive guide, we will explore different types of sheet metal forming processes, materials used, design considerations, tooling and equipment, process steps, quality control, troubleshooting, advancements, applications, and more.
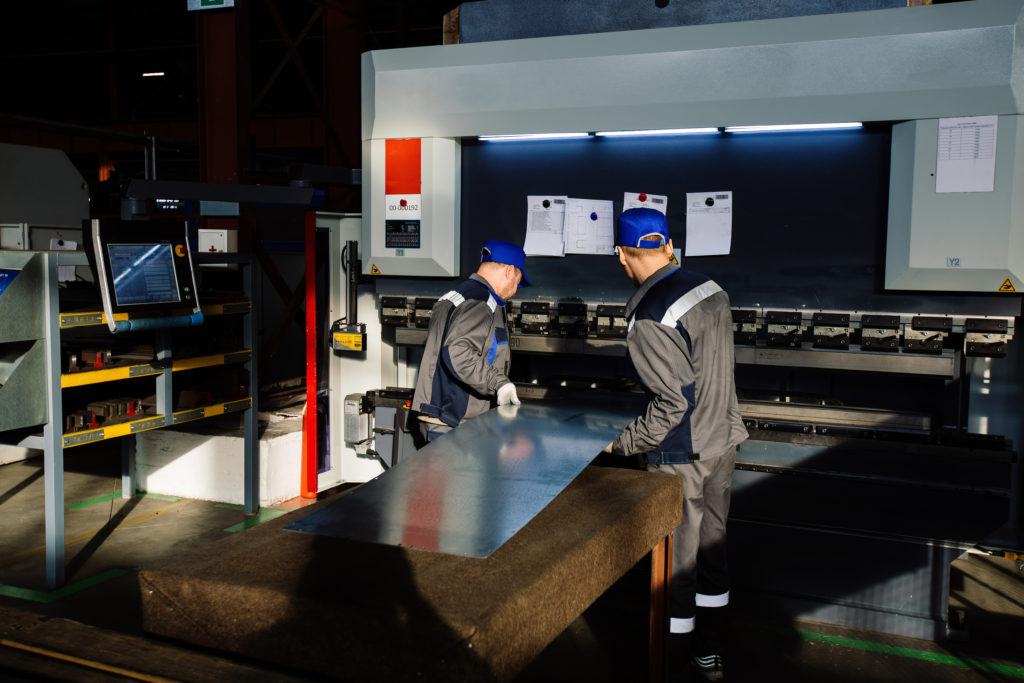
Types of Sheet Metal Forming Processes
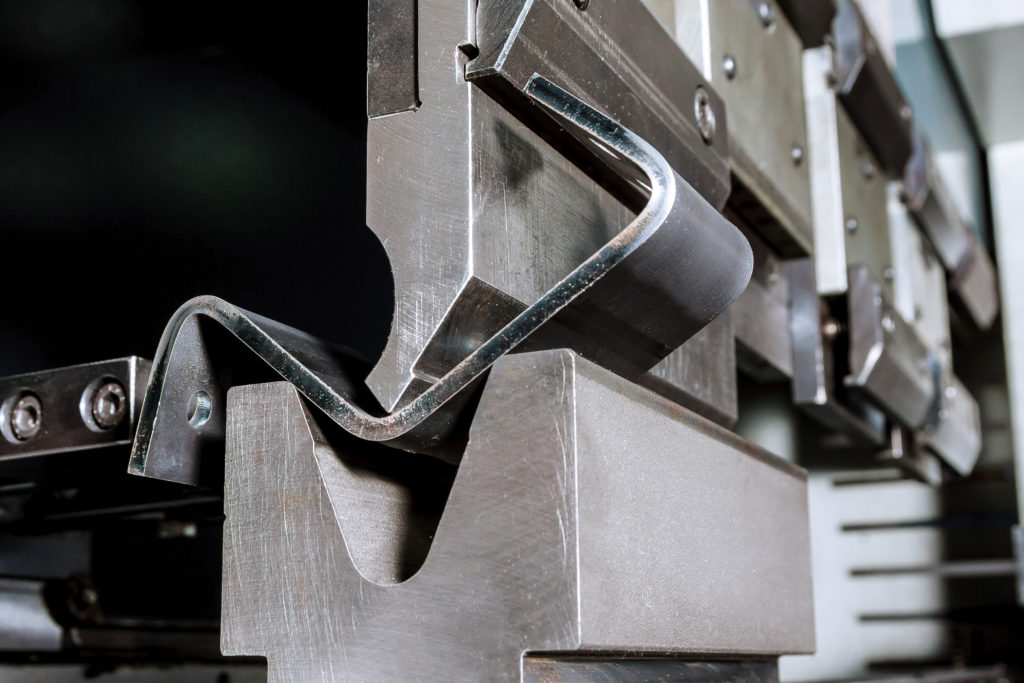
Bending: Creating Angles, Curves, and Complex Geometries
Bending is a common sheet metal forming process that shapes the metal sheet along a straight axis to create angles, curves, and complex geometries. This process is widely used in manufacturing brackets, enclosures, frames, and other structural components. Bending can be performed using press brakes, which use punches and dies to shape the metal sheet.
Bending offers several advantages, including high design flexibility, cost-effectiveness, and the ability to create strong and durable parts. The process allows for the formation of both simple and complex shapes, making it suitable for a wide range of applications. For example, bending is commonly used in the production of automotive body panels, HVAC ductwork, and furniture components.
Deep Drawing: Creating Hollow-Shaped Components
Deep drawing is a sheet metal forming process used to create hollow-shaped components like cups, cans, and containers. The process involves pulling a metal sheet into a die cavity using a punch. As the punch forces the metal into the die, it undergoes plastic deformation, resulting in the desired shape.
Deep drawing offers excellent material utilization, minimizing waste by taking advantage of the sheet’s inherent ductility. It provides high dimensional accuracy and surface finish, making it suitable for applications requiring tight tolerances. Deep drawing is commonly used in the production of kitchenware, automotive parts, and metal packaging.
Stretching: Creating Complex Contours and Curves
Stretching, also known as stretch forming, is a sheet metal forming process that involves elongating the metal sheet to create complex contours and curves. The process is commonly used in the aerospace industry to manufacture aircraft skins, fuselage sections, and wing components.
Stretching offers the advantage of producing smooth and wrinkle-free surfaces as the metal sheet is uniformly stretched over a die. This process allows for the creation of large and intricate parts without the need for multiple welds or joints. Stretch forming is widely used in industries such as aerospace, marine, and architectural metalwork.
Roll Forming: Creating Long, Uniform Sections
Roll forming is a continuous sheet metal forming process that involves passing a metal strip through consecutive sets of rollers to gradually shape it into the desired profile. This process is commonly used to produce long, uniform sections with consistent cross-sections, such as metal roofing, cladding, and steel studs.
Roll forming offers high production rates and excellent repeatability, making it suitable for large-scale manufacturing. It allows for the creation of complex profiles with consistent dimensions and tolerances. Roll-formed components find applications in the construction, automotive, and appliance industries.
Metal/Alloy | Properties and Characteristics | Common Applications |
---|---|---|
Steel | – High strength | – Automotive body panels |
– Durability | – Construction components | |
– Affordability | – Appliance parts | |
—————– | ———————————————————————— | ————————————————————- |
Aluminum | – Excellent corrosion resistance | – Aerospace components |
– Lightweight | – Automotive parts | |
– Good formability | – Electronics | |
—————– | ———————————————————————— | ————————————————————- |
Stainless Steel | – Superior corrosion resistance | – Kitchenware |
– High strength | – Medical equipment | |
—————– | ———————————————————————— | ————————————————————- |
Copper | – Excellent electrical conductivity | – Electrical applications |
– Good thermal properties | – Heat transfer components | |
—————– | ———————————————————————— | ————————————————————- |
Brass | – Good formability | – Decorative applications |
– Corrosion resistance | – Architectural applications | |
– Attractive appearance |
Materials Used in Sheet Metal Forming
Sheet metal forming can be performed using a wide range of metals and alloys, depending on the specific requirements of the application. Commonly used materials include steel, aluminum, stainless steel, copper, and brass. The choice of material depends on factors such as strength, corrosion resistance, formability, and cost.
Commonly Used Metals and Alloys
- Steel: Steel is a popular choice for sheet metal forming due to its high strength, durability, and affordability. It is widely used in automotive, construction, and appliance industries.
- Aluminum: Aluminum offers excellent corrosion resistance, lightweight properties, and good formability. It is commonly used in aerospace, automotive, and electronics industries.
- Stainless Steel: Stainless steel provides superior corrosion resistance and high strength. It is widely used in applications requiring hygienic and aesthetic properties, such as kitchenware and medical equipment.
- Copper: Copper possesses excellent electrical conductivity and thermal properties, making it suitable for electrical and heat transfer applications.
- Brass: Brass is a copper-zinc alloy that offers good formability, corrosion resistance, and an attractive appearance. It is commonly used in decorative and architectural applications.
In conclusion, sheet metal forming is a versatile process that allows for the creation of complex components and structures. Understanding the different types of processes and materials used is crucial for achieving precision fabrication. By leveraging the right techniques and materials, manufacturers can produce high-quality sheet metal components for a wide range of applications in various industries.
Case Study: Automotive Industry – Optimizing Sheet Metal Forming for Cost Efficiency
In the automotive industry, precision and cost efficiency are crucial factors in sheet metal forming. Let’s take a look at a real-world case study that highlights the importance of optimizing the forming process.
Company: ABC Auto Manufacturing Challenge: Increasing Production Efficiency and Reducing Costs in Sheet Metal Forming
ABC Auto Manufacturing, a leading automobile manufacturer, was facing challenges in their sheet metal forming processes. The company was experiencing high production costs and time-consuming operations due to frequent tooling changes and material waste.
To address these challenges, ABC Auto Manufacturing decided to collaborate with a specialized sheet metal forming company, XYZ Fabrications. XYZ Fabrications had expertise in optimizing sheet metal forming processes through advanced simulation tools and process optimization techniques.
Solution: Simulation-driven Process Optimization
XYZ Fabrications conducted a thorough analysis of ABC Auto Manufacturing’s production line and identified areas of improvement. By utilizing advanced simulation software, they were able to accurately predict the behavior of the sheet metal during forming processes, reducing the need for physical prototypes and trial-and-error iterations.
With the simulation-driven approach, XYZ Fabrications optimized the tooling design, die geometry, and process parameters to minimize material waste, reduce cycle times, and improve overall production efficiency. By fine-tuning the process, they were able to achieve the desired precision while significantly reducing costs.
Results: Increased Efficiency and Cost Savings
The collaboration between ABC Auto Manufacturing and XYZ Fabrications yielded impressive results. By implementing the optimized sheet metal forming processes, ABC Auto Manufacturing achieved:
- Reduced Scrap and Material Waste: The simulation-driven approach helped minimize material waste, resulting in significant cost savings for the company.
- Improved Production Efficiency: By optimizing the process parameters and tooling design, cycle times were reduced, enabling higher production rates and increased efficiency.
- Enhanced Component Quality: The optimized forming processes ensured consistent and high-quality components, meeting the stringent requirements of the automotive industry.
Through this case study, we can see the tangible benefits of optimizing sheet metal forming processes in the automotive industry. By leveraging advanced simulation tools and process optimization techniques, companies can achieve cost savings, improve production efficiency, and deliver high-quality components for various industries.
Questions
What is sheet metal forming?
Sheet metal forming is the process of shaping metal sheets into desired shapes using various techniques.
Who uses precision sheet metal fabrication?
Precision sheet metal fabrication is used by industries like automotive, aerospace, and electronics.
How does sheet metal forming work?
Sheet metal forming works by applying force to bend or stretch metal sheets to achieve desired shapes.
What are the advantages of precision sheet metal fabrication?
Precision sheet metal fabrication offers high accuracy, durability, and cost-effectiveness for producing complex metal parts.
How long does sheet metal forming take?
The time required for sheet metal forming depends on the complexity of the design and the chosen forming technique.
But isn’t precision sheet metal fabrication expensive?
While precision sheet metal fabrication may have higher initial costs, it offers long-term cost savings due to its durability and accuracy.