What you will learn from this article:
- How laser cutting works and the types of lasers used in precision sheet metal fabrication.
- The benefits of laser cutting, including precision, cost-effectiveness, and time-saving advantages.
- Factors to consider when choosing a laser cutting machine, materials that can be cut, and safety considerations.
Are you interested in mastering the art of laser cutting in precision sheet metal fabrication? Look no further! In this comprehensive guide, we will delve into the world of laser cutting, exploring its technology, benefits, machine configurations, material considerations, applications, and safety considerations. By the end of this guide, you will have the knowledge you need to become an expert in laser cutting for precision sheet metal fabrication.
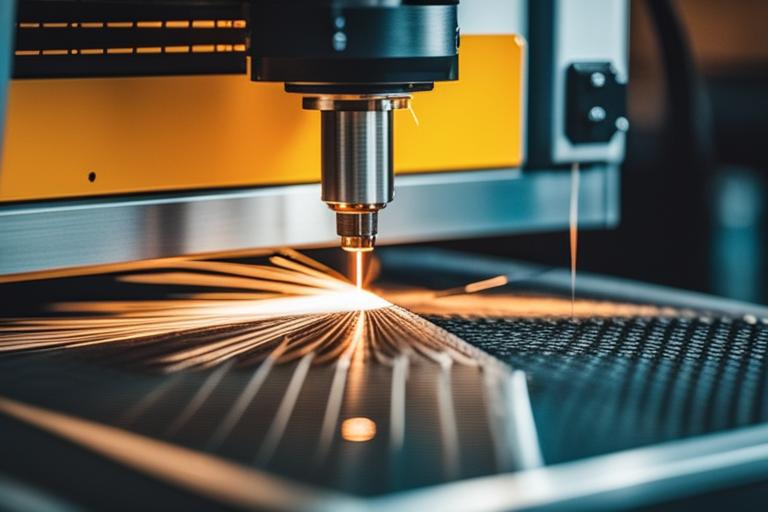
Understanding Laser Cutting Technology
Laser cutting is a precise and high-quality method used in various industries to cut materials using a laser beam. It works by using a laser beam to vaporize materials, resulting in a precise cut edge. The laser beam is generated by either CO2 lasers or fiber lasers, with each type having its own suitability for different materials. CO2 lasers are commonly used for non-metallic materials, while fiber lasers are preferred for cutting metals. The power of the laser beam determines the cutting speed and the maximum thickness of the material that can be cut.
Compared to other cutting techniques such as plasma cutting or waterjet cutting, laser cutting offers superior precision and accuracy. The focused laser beam can achieve intricate and complex designs with ease. Additionally, laser cutting eliminates the need for secondary finishing processes, reducing both time and material wastage.

Benefits of Laser Cutting in Precision Sheet Metal Fabrication
Precision sheet metal fabrication requires utmost accuracy and attention to detail. Laser cutting provides several benefits that make it an ideal choice for this field. Firstly, laser cutting allows for easier work holding, as the laser beam does not exert physical force on the material being cut. This reduces the risk of damage or deformation during the cutting process.
Furthermore, laser cutting minimizes contamination on the material, as there is no direct contact between the cutting tool and the workpiece. This is especially important for industries where cleanliness is crucial, such as the medical or semiconductor industry.
Another advantage of laser cutting is the minimal warping of the material. Traditional cutting methods like shearing or punching can cause distortion or warping due to the mechanical force applied. Laser cutting, on the other hand, produces a narrow heat-affected zone, minimizing the chances of warping.
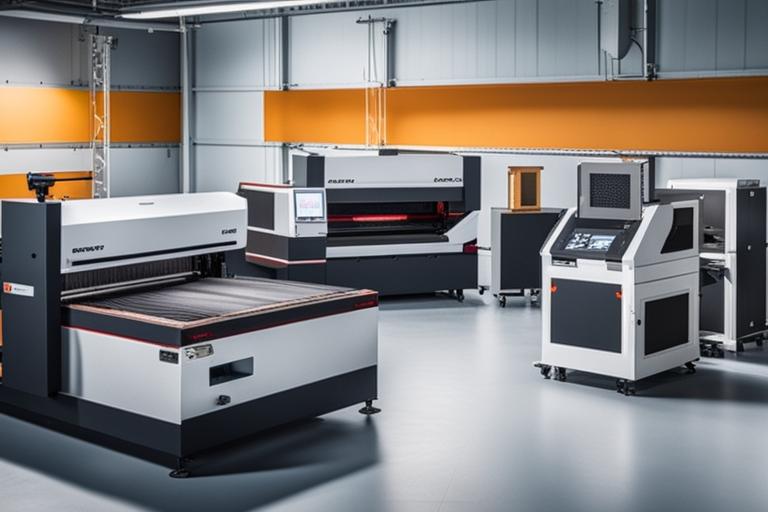
Laser Cutting Machine Configurations
Laser cutting machines come in different configurations, each with its own set of advantages and limitations. The most common configurations include flying optics, hybrid, and galvo systems.
Flying optics lasers are the fastest type of laser cutting machines. They utilize a stationary cutting bed, while the laser beam is moved using mirrors and lenses. This configuration allows for high-speed and precise cutting, as the material does not need to be clamped down during the process.
Hybrid laser cutting machines combine the advantages of both CO2 lasers and fiber lasers. They can switch between the two types of lasers to optimize cutting efficiency for different materials. This flexibility makes them suitable for a wide range of applications.
Galvo systems, also known as galvanometer-based systems, use mirrors to direct the laser beam. They are commonly used for marking, engraving, and cutting applications that require high precision and speed. Galvo systems are ideal for small-scale production or prototyping.
When choosing a laser cutting machine for precision sheet metal fabrication, it is important to consider factors such as the desired cutting speed, material compatibility, and the level of automation required. Regular maintenance and calibration are essential to ensure optimal performance and longevity of the machine.
Material | Laser Cutting Suitability | Considerations |
---|---|---|
Stainless Steel | Suitable | May require specialized techniques for reflective surfaces |
Aluminum | Suitable | – |
Copper | Suitable | Requires additional precautions for high thermal conductivity |
Alloys | Suitable | – |
Highly reflective materials | Not suitable | Laser beam may bounce back and cause damage |
Materials with high thermal conductivity | Requires additional precautions | May require specialized techniques during cutting process |

Material Considerations for Laser Cutting
Laser cutting can be used to cut a wide range of materials, including stainless steel, aluminum, copper, and various alloys. However, there are certain limitations to be aware of. For example, laser cutting is not suitable for materials with highly reflective surfaces, as the laser beam may bounce back and cause damage to the machine or operator. Similarly, materials with high thermal conductivity, such as copper, may require specialized techniques or additional precautions during the cutting process.
Choosing the right laser cutting parameters is crucial for achieving optimal results. Factors such as laser power, cutting speed, and focus position need to be adjusted based on the material being cut. A higher laser power may be required for thicker materials, while a lower power setting can be used for thinner materials to prevent excessive melting or burning.
It is also important to handle different materials with care during the laser cutting process. Some materials may produce toxic fumes or dust when cut, requiring proper ventilation or extraction systems. Operators should wear appropriate personal protective equipment (PPE) to ensure their safety.

Laser Cutting Applications in Precision Sheet Metal Fabrication
Laser cutting finds numerous applications in precision sheet metal fabrication. One of its key advantages is the ability to create intricate designs and cut complex shapes with high precision. This makes it an ideal choice for industries such as automotive, aerospace, and electronics, where intricate components and tight tolerances are required.
Case studies and examples can illustrate the successful application of laser cutting in precision sheet metal fabrication. For example, in the automotive industry, laser cutting is used to create precise body panels and structural components. In the aerospace industry, laser cutting enables the production of lightweight yet strong aircraft parts. The electronics industry relies on laser cutting for precise circuit board manufacturing.
With advancements in laser cutting technology, the potential applications are expanding into emerging industries as well. For instance, laser cutting is being used in the renewable energy sector to fabricate components for solar panels and wind turbines. The versatility and accuracy of laser cutting make it a valuable tool in pushing the boundaries of precision sheet metal fabrication.
Choosing a Laser Cutting Service Provider
For businesses or individuals who do not have the resources or expertise to invest in a laser cutting machine, outsourcing the cutting process to a professional service provider is a viable option. However, choosing the right laser cutting service provider is crucial to ensure quality results and timely delivery.
When selecting a laser cutting service provider in the precision sheet metal fabrication niche, consider factors such as their experience, capabilities, turnaround time, and customer reviews. Look for providers that specialize in the specific materials and designs you require. Reputable providers often have a portfolio of successful projects and can provide references upon request.
Some popular laser cutting service providers in the precision sheet metal fabrication industry include Ponoko, The Laser Cutting Company, and Xometry. These companies offer a range of services, from laser cutting and forming to prototyping and custom fabrication.
Personal Story: From Prototype to Production: How Laser Cutting Transformed Our Business
In the early stages of our business, my partner Mark and I faced numerous challenges in the production of precision sheet metal parts. We struggled with achieving intricate designs and complex shapes, often resulting in high material wastage and time-consuming secondary finishing processes. That was until we discovered the power of laser cutting.
One particular project stands out in my mind. We were tasked with creating a prototype for a new medical device. The design was incredibly intricate, with multiple small cutouts and intricate patterns. Our previous methods of cutting simply couldn’t achieve the level of precision and accuracy required.
After researching various cutting techniques, we decided to give laser cutting a try. We found a reputable laser cutting service provider that specialized in precision sheet metal fabrication. They had state-of-the-art laser cutting machines and a team of experienced operators.
The difference was remarkable. The laser cutting machine effortlessly cut through the sheet metal, creating the intricate design with incredible precision. There were no burrs or distortions, eliminating the need for secondary finishing processes. The efficiency and accuracy of laser cutting saved us valuable time and reduced material wastage significantly.
Impressed with the success of the prototype, we decided to partner with the laser cutting service provider for our production needs as well. They were able to handle large-scale production runs with the same level of precision and efficiency. Laser cutting allowed us to meet tight deadlines and deliver high-quality products to our clients consistently.
Since then, laser cutting has become an integral part of our business. It has enabled us to take on more complex projects and expand into new industries. The versatility of laser cutting technology has opened doors for us in the automotive, aerospace, and electronics sectors.
Our experience with laser cutting has been nothing short of transformative. It has revolutionized our precision sheet metal fabrication processes, allowing us to achieve levels of precision and quality that were once unimaginable. I encourage anyone in the industry to explore the potential of laser cutting and experience the benefits firsthand.
Safety Considerations in Laser Cutting
Safety is of utmost importance when working with laser cutting machines. Operators and technicians should follow strict safety precautions to prevent accidents and ensure a safe working environment.
Personal protective equipment (PPE) is essential for anyone operating or working near laser cutting machines. This can include safety glasses, gloves, and protective clothing to shield against potential laser hazards and flying debris. Proper training and certification should be provided to operators to ensure they are knowledgeable about the safe operation of laser cutting machines.
Additionally, laser cutting byproducts, such as fumes and dust, should be handled and disposed of safely. Proper ventilation systems and extraction equipment should be in place to minimize exposure to harmful substances. Regular maintenance and inspection of the laser cutting machine are necessary to identify any potential safety issues and ensure compliance with regulations.
Conclusion
Laser cutting is a powerful and versatile technique that has revolutionized precision sheet metal fabrication. Its ability to achieve intricate designs, superior precision, and minimal material wastage make it an invaluable tool in various industries. By understanding the technology, machine configurations, material considerations, applications, and safety precautions, you can master the art of laser cutting in precision sheet metal fabrication. Whether you are an engineer, designer, or artist, this comprehensive guide equips you with the knowledge and resources to excel in the world of laser cutting.
Answers To Common Questions
What is laser cutting and how does it work?
Laser cutting is a precise method of cutting materials using a focused laser beam.
Who can benefit from laser cutting services?
Industries like automotive, aerospace, and electronics can benefit from laser cutting services.
How accurate is laser cutting in precision sheet metal fabrication?
Laser cutting offers high accuracy, with tolerances as low as +/- 0.1mm.
What materials can be laser cut in precision sheet metal fabrication?
Laser cutting can be used on various materials, including stainless steel, aluminum, and copper.
How does laser cutting improve efficiency in sheet metal fabrication?
Laser cutting enables faster production, reduces material waste, and eliminates the need for additional machining processes.
What if I have complex designs for precision sheet metal fabrication?
Laser cutting is perfect for complex designs, allowing for intricate cuts and detailed patterns.