Learn about Electrical Enclosure Manufacturers
- Importance of electrical enclosures in various industries.
- The manufacturing process, including design, material selection, cutting, bending, welding, finishing, and testing.
- Customer support, compliance, and quality assurance in the production of electrical enclosures.
Are you curious about the intricate processes involved in the manufacturing of electrical enclosures by top electrical enclosure manufacturers? Electrical enclosures serve as crucial components in various industries, providing protection and housing for sensitive electrical equipment. These enclosures play a vital role in safeguarding components from environmental factors, ensuring operational efficiency, and maintaining safety standards. Manufacturers specializing in electrical enclosures employ advanced techniques and high-precision processes to deliver products that meet the diverse needs of their customers. Atlas Manufacturing, with a legacy dating back to 1962, exemplifies excellence in precision sheet metal fabrication, offering a wide range of services from design to logistics support.
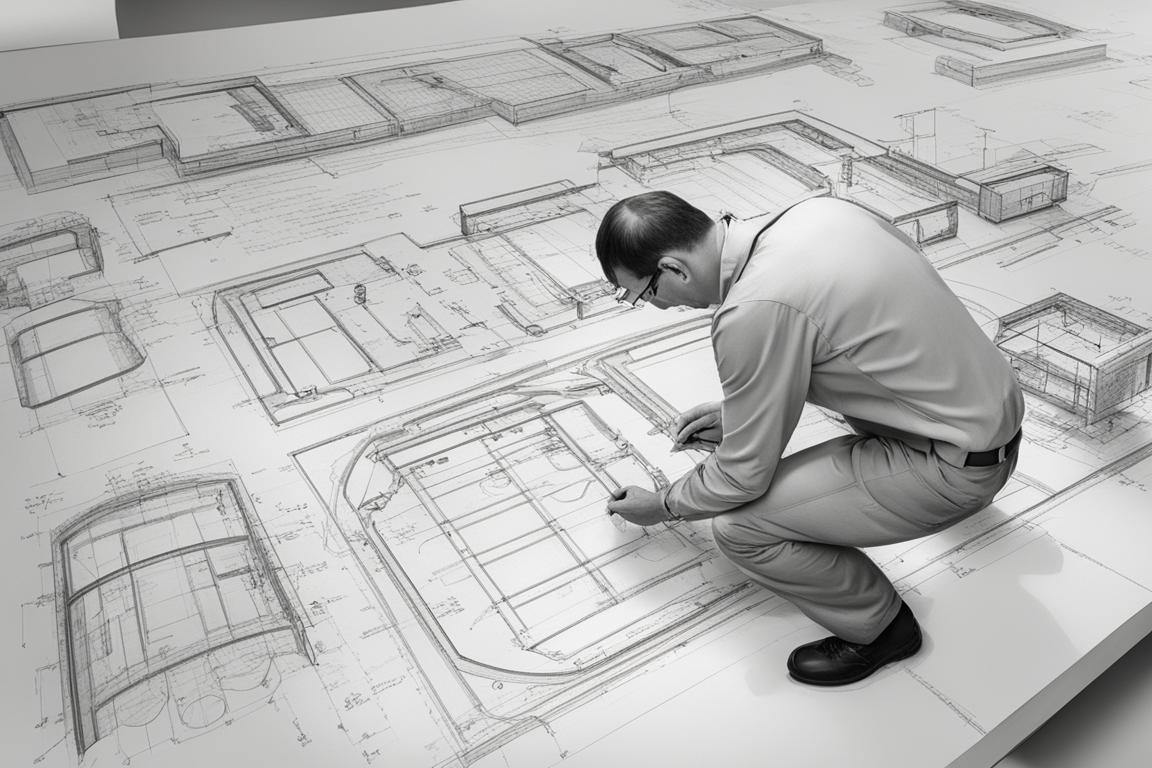
Design and Specification Phase
During the initial phase of electrical enclosure manufacturing, precise design and specification are paramount. Manufacturers collaborate closely with engineers and designers to create detailed drawings and specifications that align with the specific requirements of the project. This phase involves considering factors such as size, material compatibility, environmental conditions, and regulatory standards to ensure the final product meets all necessary criteria.
Material Selection
The choice of materials for electrical enclosures is a critical decision that impacts the enclosure’s durability, performance, and longevity. Manufacturers typically offer enclosures made from materials like carbon steel, stainless steel, aluminum, and plastic. Each material has distinct properties that influence factors such as corrosion resistance, conductivity, and weight. By understanding the unique characteristics of each material, manufacturers can recommend the most suitable option based on the project’s requirements.
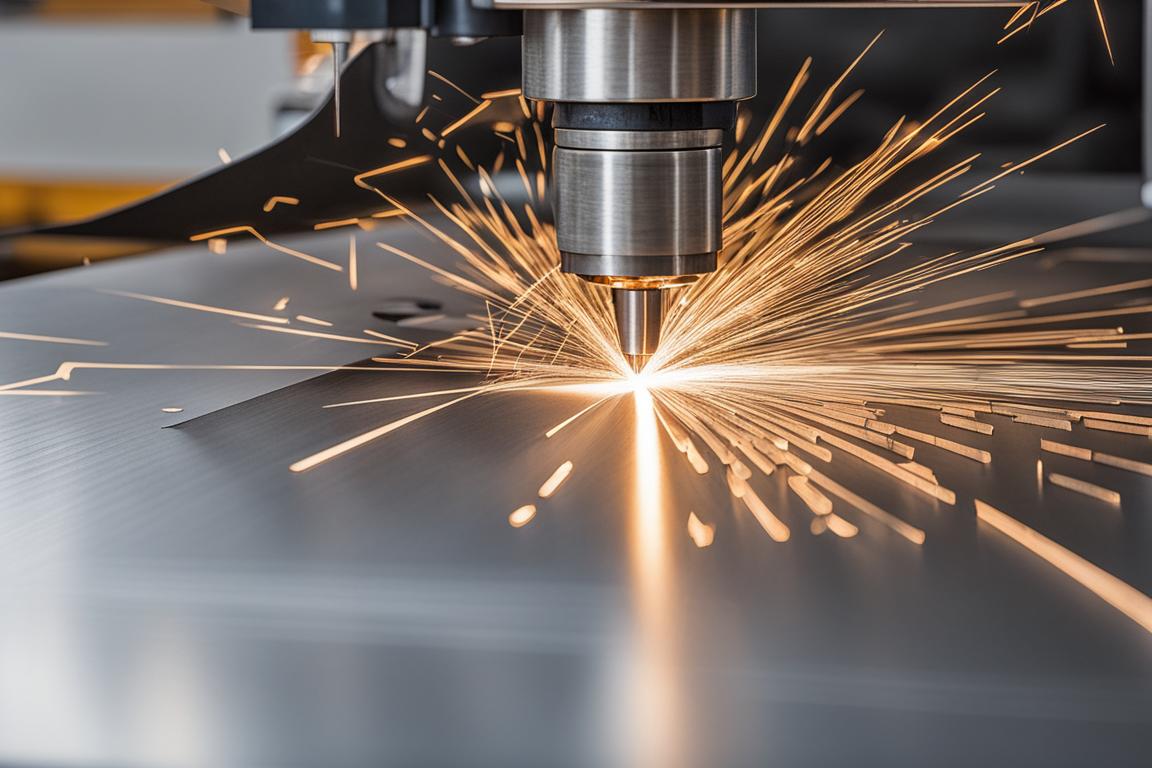
Cutting and Blanking
Once the materials are selected, manufacturers utilize advanced machinery such as laser cutters and punches to shape the raw materials. Cutting and blanking involve shearing the material to the required sizes and shapes for various enclosure components. Precision in this phase is crucial to ensure that the components fit together seamlessly during assembly, ultimately contributing to the enclosure’s functionality and aesthetics.
Bending and Forming
Bending and forming processes play a key role in transforming flat sheets of metal into 3D shapes that make up the enclosure’s structure. Manufacturers use press brakes to accurately bend the metal to achieve the desired shapes and angles. Precision in bending is essential to maintain the structural integrity of the enclosure and ensure that components fit together snugly, allowing for proper functionality and ease of assembly.
Aspect | Description |
---|---|
Equipment | Utilization of press brakes for bending operations |
Importance of Precision | Ensuring accurate bends to meet design specifications |
Skilled Operators | Requirement of trained personnel for operating press brakes effectively |
Impact on Structural Integrity | Maintaining the structural integrity of the enclosure through precise bending |
Contribution to Functionality | Facilitating proper fitting of components for functional and aesthetic assembly |
Precision in Press Brakes Operations
Press brakes are essential tools in the manufacturing of electrical enclosures, allowing for precise bending of metal sheets. Manufacturers rely on skilled operators and advanced machinery to achieve accurate bends that meet the enclosure’s design specifications.
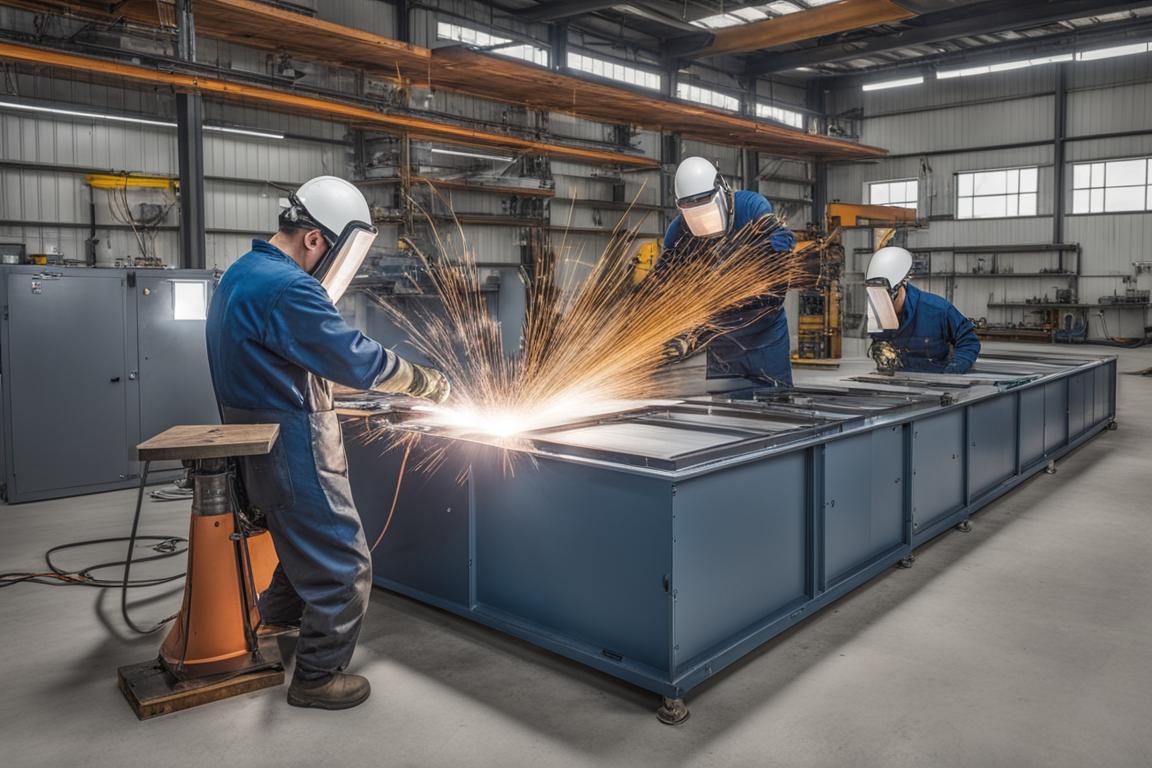
Welding and Assembly
Welding is a critical process in the assembly of enclosure components, where parts are joined together using techniques like MIG, TIG, or spot welding. Welding ensures structural integrity and durability, providing a secure enclosure for sensitive electrical equipment. In addition to welding, manufacturers perform assembly tasks such as attaching doors, hinges, gaskets, and mounting brackets to complete the enclosure’s construction.
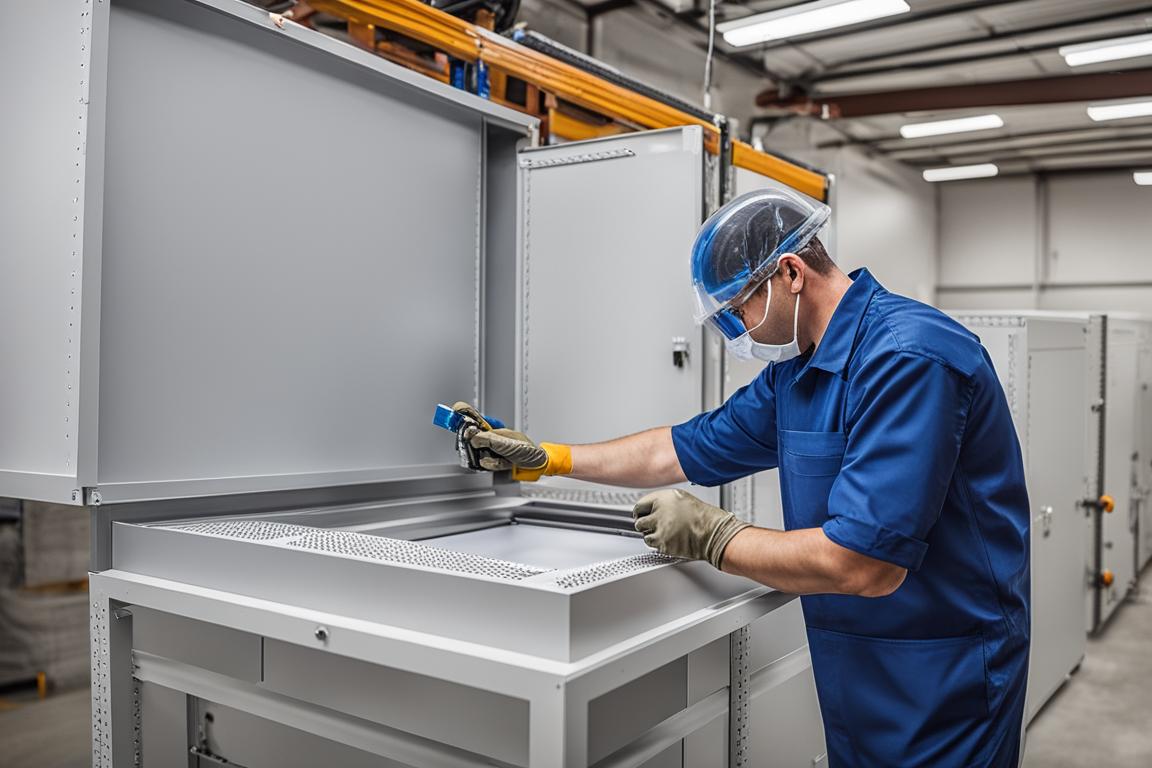
Finishing and Coating
After assembly, the enclosure undergoes finishing processes to enhance its appearance and durability. Surface finishes like powder coating, painting, or anodizing are applied to provide protection against corrosion, wear, and environmental factors. Manufacturers adhere to industry standards to ensure that the finish is not only aesthetically pleasing but also durable and resistant to external conditions.
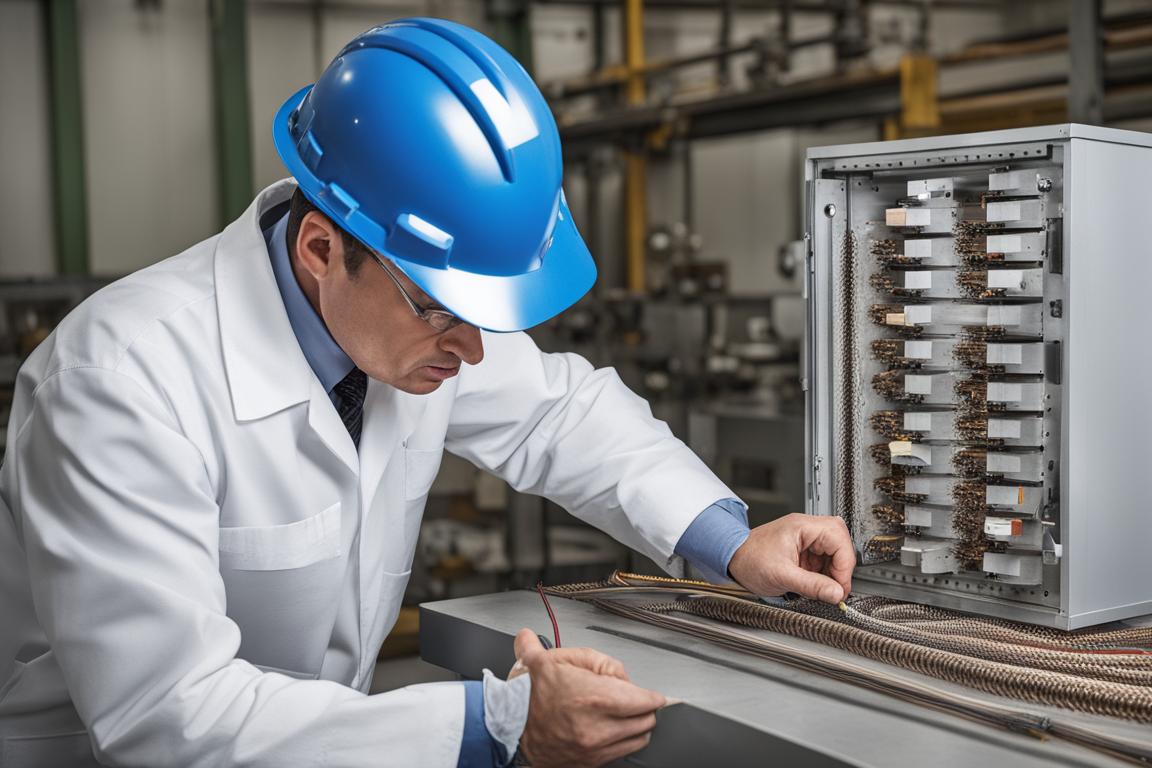
Quality Control and Testing
Maintaining high quality throughout the manufacturing process is a top priority for electrical enclosure manufacturers. Rigorous quality control measures are implemented at various stages of production to identify and rectify any defects or inconsistencies. Testing procedures, including pressure testing to assess structural integrity and electrical conductivity testing to ensure safety, are conducted to guarantee that the enclosure meets all necessary standards.
Certifications and Compliance
Obtaining certifications such as NEMA, IP, UL, CE, or RoHS is essential for electrical enclosure manufacturers to demonstrate compliance with industry regulations and standards. These certifications provide assurance to customers regarding the quality, safety, and performance of the enclosures. Manufacturers invest in meeting and maintaining these certifications to build trust with their clients and uphold their reputation for excellence.
Packaging and Shipping
Once the manufacturing process is complete, careful packaging is essential to protect the finished enclosures during shipping and delivery. Manufacturers employ secure packaging methods to prevent damage and ensure that the enclosures reach their destination in optimal condition. Efficient coordination with logistics partners facilitates timely and reliable shipping, allowing customers to receive their products promptly.
Customer Support and After-Sales Service
Providing exceptional customer support and after-sales service is a hallmark of leading electrical enclosure manufacturers. Manufacturers offer technical assistance, customization options, and installation guidance to help customers make the most of their enclosures. Additionally, warranty services, maintenance support, and access to spare parts ensure that customers receive ongoing support and assistance even after the sale is complete.
Conclusion
In conclusion, the manufacturing process of electrical enclosures by top manufacturers is a sophisticated endeavor that integrates design, material selection, fabrication, testing, and customer service. By placing emphasis on quality, compliance, and customer satisfaction, manufacturers such as Atlas Manufacturing consistently deliver enclosures that not only meet but exceed the highest industry standards and customer expectations. Through their precision sheet metal fabrication techniques and unwavering commitment to excellence, these manufacturers play a crucial role in providing reliable and cutting-edge solutions to a variety of industries.
To learn more about the intricacies of electrical enclosure manufacturing, we encourage you to reach out to us. Contact us for further insights and information on how our expertise can benefit your specific needs.
Answers To Common Questions
Q. Who are some top electrical enclosure manufacturers in precision sheet metal fabrication?
A. Some top manufacturers include Hoffman, Rittal, and Hammond.
Q. What materials are commonly used by precision sheet metal manufacturers for electrical enclosures?
A. Common materials used include stainless steel, aluminum, and galvanized steel.
Q. How can I ensure the electrical enclosure meets my specifications?
A. You can provide detailed drawings and specifications to the manufacturer for custom fabrication.
Q. What if I need a custom design that is not listed by the manufacturer?
A. Many manufacturers offer custom design services to meet specific requirements.
Q. How long does it typically take for electrical enclosure manufacturers to produce a custom order?
A. The production time varies but usually ranges from 2 to 6 weeks for custom orders.
Q. What if I have specific requirements for the finish of the electrical enclosure?
A. Many manufacturers offer a variety of finishes including powder coating, painting, and plating to meet specific needs.