Custom enclosures, also known as bespoke enclosures, refer to specifically designed structures that offer housing and protection for critical equipment across various industries. These enclosures are tailored to meet specific requirements, ensuring a perfect fit for the equipment they house. They are engineered to provide protection from environmental factors, ensure equipment safety, and enhance the overall functionality and aesthetics of the housed components.
What You’ll Learn About Custom Enclosures
By reading this article, you will learn:
– The significance and applications of custom enclosures in various industries.
– Design considerations, materials, fabrication techniques, quality control, and assembly methods for custom enclosures.
– The role of custom enclosures in product development, future trends, choosing the right fabrication partner, and regulatory considerations.
Definition and Significance of Custom Enclosures
Custom enclosures refer to precisely engineered structures customized to fit specific equipment or machinery. They are fabricated to provide protection against environmental elements, electromagnetic interference, and physical damage. The significance of custom enclosures lies in their ability to ensure the longevity and optimal performance of the equipment they house.
Applications in Various Industries
Custom enclosures find applications across diverse industries, including electronics, telecommunications, healthcare, automotive, and aerospace. In the electronics industry, custom enclosures protect sensitive electronic components from dust, moisture, and other contaminants. In the telecommunications sector, these enclosures safeguard networking and communication equipment from harsh weather conditions and vandalism. The healthcare industry relies on custom enclosures to house medical devices and equipment, ensuring a sterile and safe environment. Similarly, custom enclosures are crucial in the automotive and aerospace sectors to protect electronics and sensitive components from extreme temperatures, vibrations, and impact.
Importance of Custom Enclosures
Custom enclosures play a vital role in ensuring the protection, safety, and customization options for housed equipment across various industries.
Electronics
In the electronics industry, custom enclosures ensure the protection of delicate electronic components from environmental factors such as dust, moisture, and electromagnetic interference. They also aid in heat dissipation, electromagnetic compatibility, and overall system reliability.
Telecommunications
For the telecommunications industry, custom enclosures are essential for safeguarding networking equipment, fiber optic terminations, and other critical components from weather-related damage, vandalism, and unauthorized access.
Healthcare
Custom enclosures are indispensable in the healthcare industry, providing a secure and sterile environment for housing medical devices and equipment, meeting stringent cleanliness and safety standards.
Automotive
In the automotive sector, custom enclosures protect electronic control units (ECUs), sensors, and other electronic components from extreme temperatures, moisture, vibrations, and impact, ensuring the long-term reliability of the housed electronics.
Aerospace
Aerospace applications demand custom enclosures that can withstand extreme temperatures, pressure differentials, and vibrations while protecting sensitive avionics and electronic systems.
Design Considerations for Custom Enclosures
Designing custom enclosures involves careful consideration of functionality, aesthetics, and customization options to meet the specific needs of the equipment they house.
Functionality
The primary design consideration for custom enclosures is functionality. The enclosure must provide adequate protection, ventilation, and accessibility to the housed equipment while accommodating any necessary wiring and connectors.
Aesthetics
Aesthetics play a crucial role, especially in consumer-facing applications. Custom enclosures should align with the overall product design and branding, enhancing the visual appeal of the equipment while ensuring functional integrity.
Customization Options
Custom enclosures offer a wide range of customization options, including various sizes, shapes, mounting options, and access features, allowing for the seamless integration of the enclosure with the housed equipment and the surrounding environment.
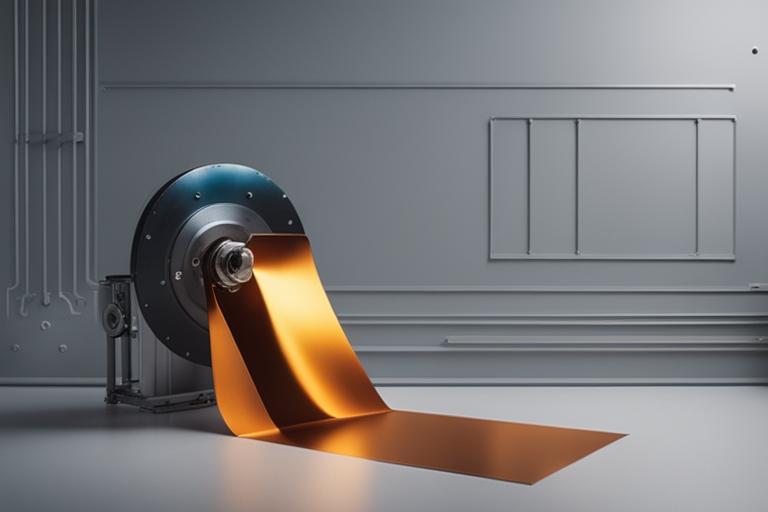
Materials and Fabrication Techniques
Custom enclosures are fabricated using a variety of materials and precision metal crafting techniques to meet the specific requirements of diverse applications.
Materials Used
Material | Properties |
---|---|
Stainless Steel | Corrosion resistance and durability |
Aluminum | Lightweight, sturdy, excellent thermal conductivity |
Alloys | Enhanced strength, conductivity, or resistance to extreme conditions |
Composite Materials | Lightweight, non-conductive, and corrosion-resistant properties |
Precision Sheet Metal Fabrication
Precision sheet metal fabrication techniques, including laser cutting, bending, welding, and finishing processes, are employed to create custom enclosures with intricate designs and precise specifications.
Quality Control and Testing
Ensuring the quality and reliability of custom enclosures involves rigorous testing and adherence to industry standards.
Durability
Custom enclosures undergo durability testing to assess their ability to withstand environmental stressors, mechanical impacts, and prolonged usage without compromising the integrity of the housed equipment.
Reliability
Reliability testing is conducted to evaluate the enclosure’s ability to maintain consistent performance under varying conditions, ensuring the long-term functionality and safety of the enclosed equipment.
Compliance with Industry Standards
Custom enclosures are manufactured in accordance with industry-specific standards and regulations, ensuring that they meet the required performance, safety, and environmental criteria.
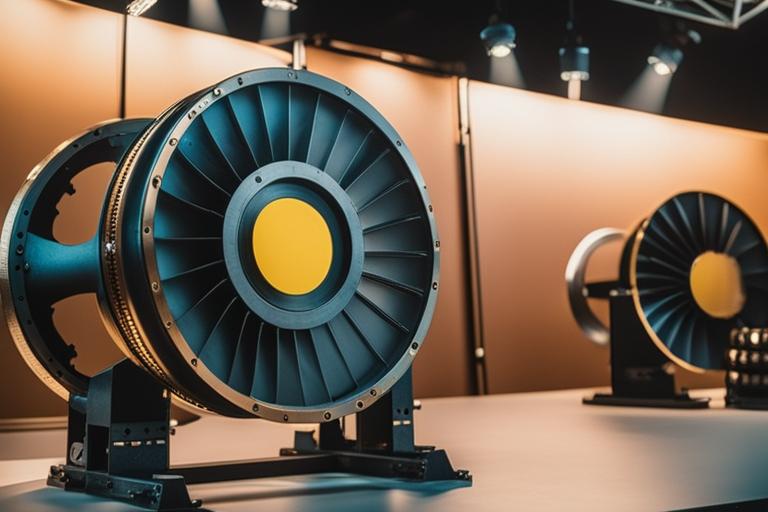
Custom Enclosure Assembly and Finishing
The assembly and finishing processes of custom enclosures are critical in ensuring structural integrity, functionality, and aesthetic appeal.
Assembly Methods
Custom enclosures are assembled using precise techniques to ensure proper alignment of components, secure fastening, and the integration of gaskets and seals for environmental protection.
Finishing Options
Various finishing options, such as paint, powder coating, and surface treatments, are applied to custom enclosures to enhance their appearance, durability, and resistance to corrosion and wear.
Surface Treatments
Surface treatments, including chemical treatments and coatings, are utilized to modify the properties of the enclosure surface, providing additional protection against environmental factors and enhancing the overall performance of the enclosure.
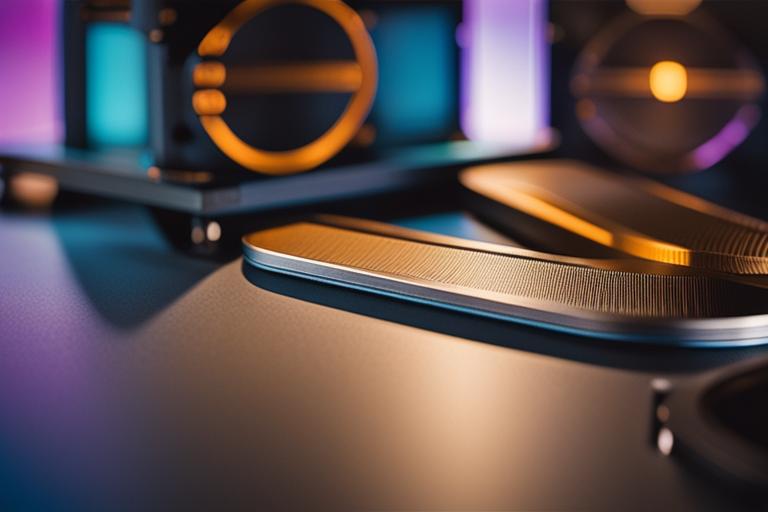
Role of Custom Enclosures in Product Development
Custom enclosures play a pivotal role in product development across industries, offering a range of benefits and innovative solutions.
Product Enhancement
Custom enclosures enhance the overall functionality and reliability of the equipment they house, contributing to the improvement of the end product.
Innovative Solutions
Custom enclosures enable the implementation of innovative design concepts, space-saving solutions, and advanced features that enhance the performance and usability of the enclosed equipment.
Integration with Industry 4.0
In the era of Industry 4.0, custom enclosures facilitate the integration of smart technologies, IoT devices, and connectivity solutions, enabling seamless integration with digital systems and processes.
Case Studies and Examples
Custom enclosures have diverse applications, as evidenced by their use in electronic, automotive, medical, and aerospace equipment.
Electronic Enclosures
Custom enclosures are utilized to house sensitive electronic components, control panels, and communication equipment, ensuring protection and optimized performance.
Car Audio Enclosures
Custom enclosures for car audio systems provide acoustically optimized spaces for speakers, subwoofers, and amplifiers, enhancing the audio experience within vehicles.
Medical Equipment Enclosures
Custom enclosures in the healthcare sector are tailored to house medical devices such as diagnostic equipment, patient monitoring systems, and laboratory instruments, meeting stringent regulatory and safety requirements.
Aerospace Enclosures
Aerospace-grade custom enclosures protect avionics, communication systems, and navigation equipment, ensuring reliable operation in demanding flight conditions.
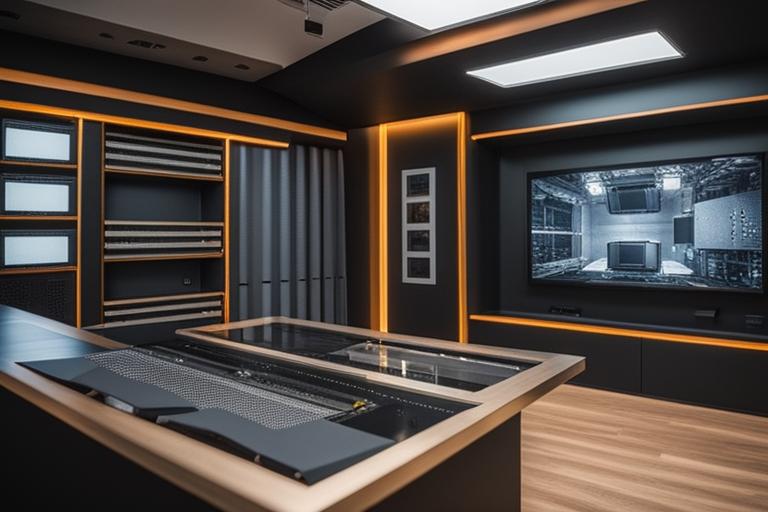
Future Trends in Custom Enclosure Design
Advancements in materials, smart technologies, and sustainable design practices are shaping the future of custom enclosure design.
Advanced Materials
The use of advanced materials, including nanocomposites, lightweight alloys, and conductive polymers, is expected to drive innovations in custom enclosure design, offering enhanced performance and durability.
Smart Enclosure Designs
Smart enclosures equipped with sensors, connectivity features, and integrated cooling systems are anticipated to become increasingly prevalent, enabling real-time monitoring and adaptive functionality.
Sustainable Design Innovations
The integration of sustainable materials, energy-efficient manufacturing processes, and recyclable enclosure solutions will play a significant role in reducing the environmental footprint of custom enclosure production.
Choosing the Right Fabrication Partner
Selecting a reliable fabrication partner is essential for ensuring the successful design and production of custom enclosures.
Expertise and Experience
Look for a fabrication partner with extensive expertise and experience in custom enclosure design, fabrication techniques, and industry-specific requirements.
Quality Assurance
Ensure that the fabrication partner has robust quality control measures in place to guarantee the precision, durability, and compliance of custom enclosures with relevant standards.
Project Management
Effective project management capabilities, including clear communication, adherence to timelines, and collaborative problem-solving, are crucial factors in choosing the right fabrication partner for custom enclosure projects.
Maintenance, Servicing, and Troubleshooting
Proper maintenance, servicing, and troubleshooting practices are essential for ensuring the longevity and optimal performance of custom enclosures.
Cleaning and Inspection
Regular cleaning and inspection of custom enclosures are necessary to prevent the accumulation of contaminants, ensure proper ventilation, and identify any signs of wear or damage.
Repairs and Upgrades
Timely repairs and upgrades, such as replacing worn seals, addressing surface corrosion, or integrating new features, help maintain the functionality and protection provided by custom enclosures.
Troubleshooting Tips
Establishing troubleshooting protocols and readily available support for addressing issues such as electrical faults, environmental damage, or connectivity issues is critical for minimizing downtime and ensuring equipment safety.
Regulatory and Compliance Considerations
Adhering to industry-specific regulations, safety standards, and certification requirements is imperative in the design and fabrication of custom enclosures.
Industry-Specific Regulations
Different industries have specific regulations governing the design, material selection, and performance criteria for custom enclosures, necessitating compliance with relevant standards.
Safety Standards
Safety standards related to electrical insulation, environmental protection, and fire resistance must be carefully considered in the design and fabrication of custom enclosures to ensure the safety of personnel and equipment.
Certification Requirements
Obtaining certifications such as UL listing, CE marking, or industry-specific approvals may be necessary to validate the performance and safety of custom enclosures for their intended applications.
Cost Considerations and Budgeting
Understanding the cost components and budgeting for custom enclosure projects is essential for effective project planning and management.
Material Costs
Material costs, including the selection of suitable metals, coatings, and additional components, contribute significantly to the overall budget for custom enclosure fabrication.
Fabrication Costs
Fabrication costs encompass the expenses associated with precision metal crafting, finishing processes, assembly, and quality control measures implemented during enclosure production.
Total Project Budgeting
Comprehensive project budgeting should account for material costs, fabrication expenses, testing and certification fees, and any additional requirements for custom enclosure projects.
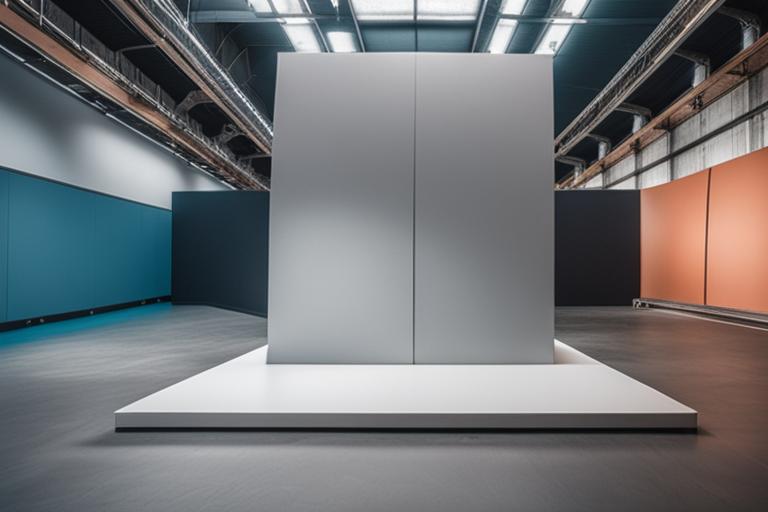
Environmental Impact and Sustainability
Considering the environmental impact of custom enclosure production and adopting sustainable design practices is becoming increasingly important in modern manufacturing.
Sustainable Materials
The use of recyclable metals, eco-friendly coatings, and sustainable composite materials contributes to reducing the environmental impact of custom enclosure fabrication.
Energy-Efficient Processes
Implementing energy-efficient manufacturing processes minimizes the carbon footprint associated with custom enclosure production.
This comprehensive guide highlights the importance and diverse applications of custom enclosures, the intricate design and fabrication processes, and the evolving trends shaping the future of custom enclosure design and production. Selecting the right fabrication partner and adhering to quality control, regulatory compliance, and sustainability considerations are crucial for the successful development and deployment of custom enclosures across various industries. Moreover, incorporating insights and case studies from industry experts and professionals with first-hand experience in custom enclosure projects would further enrich the understanding and practical application of the discussed concepts. Integrating interactive elements such as videos, images, or 3D models showcasing the fabrication processes and finished custom enclosures would provide a more engaging and immersive experience for the readers.
Common Questions
Who specializes in creating custom enclosures?
Precision sheet metal fabrication companies specialize in creating custom enclosures.
What materials are used for custom enclosures?
Custom enclosures are typically made from materials like steel, aluminum, and stainless steel.
How are custom enclosures designed and fabricated?
Custom enclosures are designed using CAD software and then fabricated using precision sheet metal techniques.
What makes custom enclosures a better choice?
Custom enclosures offer tailored solutions to fit specific equipment and environmental requirements.
How can I ensure the custom enclosure fits my needs?
Work closely with the fabrication team to provide detailed specifications and requirements for the custom enclosure.
What if I have a unique design in mind?
Precision sheet metal fabrication allows for the realization of unique and complex custom enclosure designs.