Are you interested in the intricate world of welded assemblies in metal fabrication? Let’s delve into the expertise and artistry required for this vital process.
Atlas Manufacturing, with a rich history since 1962, stands at the forefront of precision sheet metal fabrication, serving diverse industries with unparalleled expertise. Our commitment to quality, innovation, and customer satisfaction drives our approach, offering comprehensive services from engineering and design to assembly and logistics support. At Atlas, we blend advanced manufacturing techniques with a high-touch approach, ensuring each project reflects our dedication to excellence and building long-lasting client relationships. Our ISO 9001:2015 certification underscores our relentless pursuit of quality, positioning us as a premier fabricator in North America.
What You’ll Learn About Welded Assemblies
- Definition and significance in precision sheet metal fabrication
- Types, materials, and techniques used in welded assemblies
- Industry applications, quality control, advancements, and future trends
Welded assemblies are an integral part of metal fabrication, serving as the cornerstone of creating sturdy and complex structures from metal components. In precision sheet metal fabrication, welded assemblies play a vital role in bringing together individual parts to form a unified and functional whole. This process requires expertise, precision, and a deep understanding of the materials and techniques involved.
Definition of Welded Assemblies
Welded assemblies refer to the process of joining multiple metal components together using various welding techniques. This process creates a cohesive structure that is often stronger and more durable than the individual components. Welded assemblies can range from simple joints to intricate structures, depending on the specific requirements of the project.
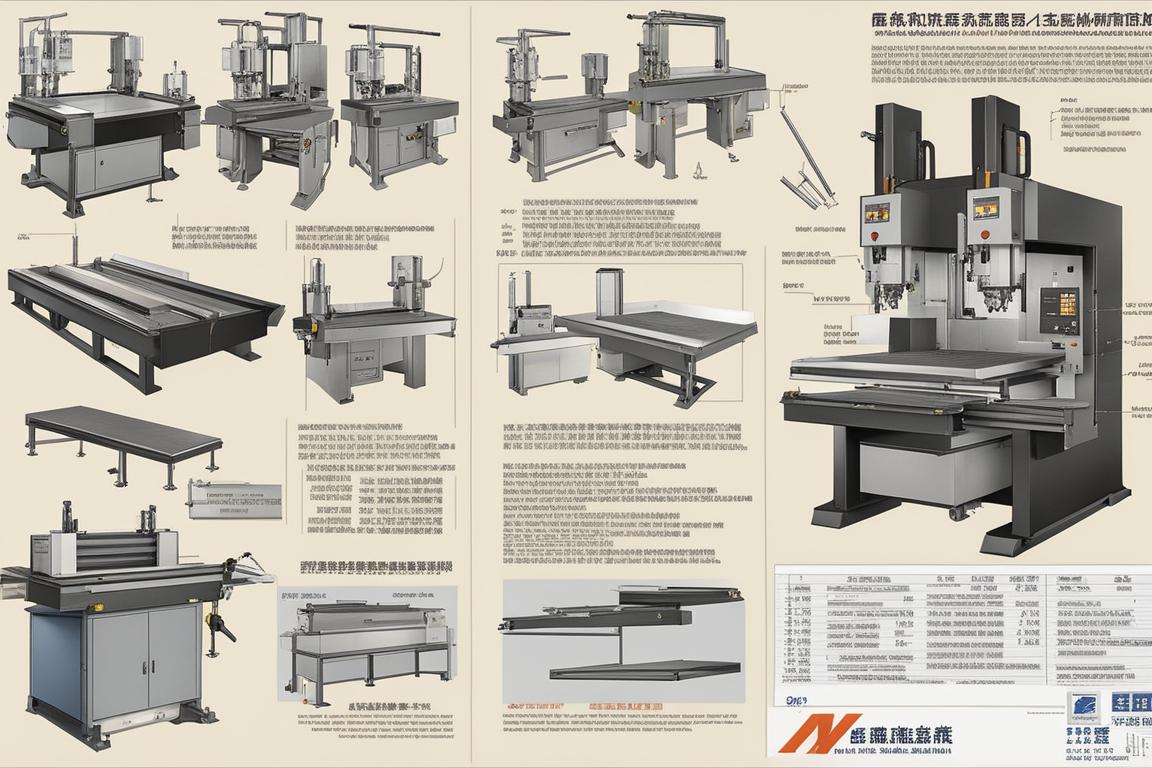
Significance in Precision Sheet Metal Fabrication
In the realm of precision sheet metal fabrication, welded assemblies are essential for creating complex and customized components that meet exact specifications. Whether it’s in the aerospace, automotive, or electronics industry, the ability to fabricate welded assemblies with precision and accuracy is crucial for delivering high-quality, reliable products.
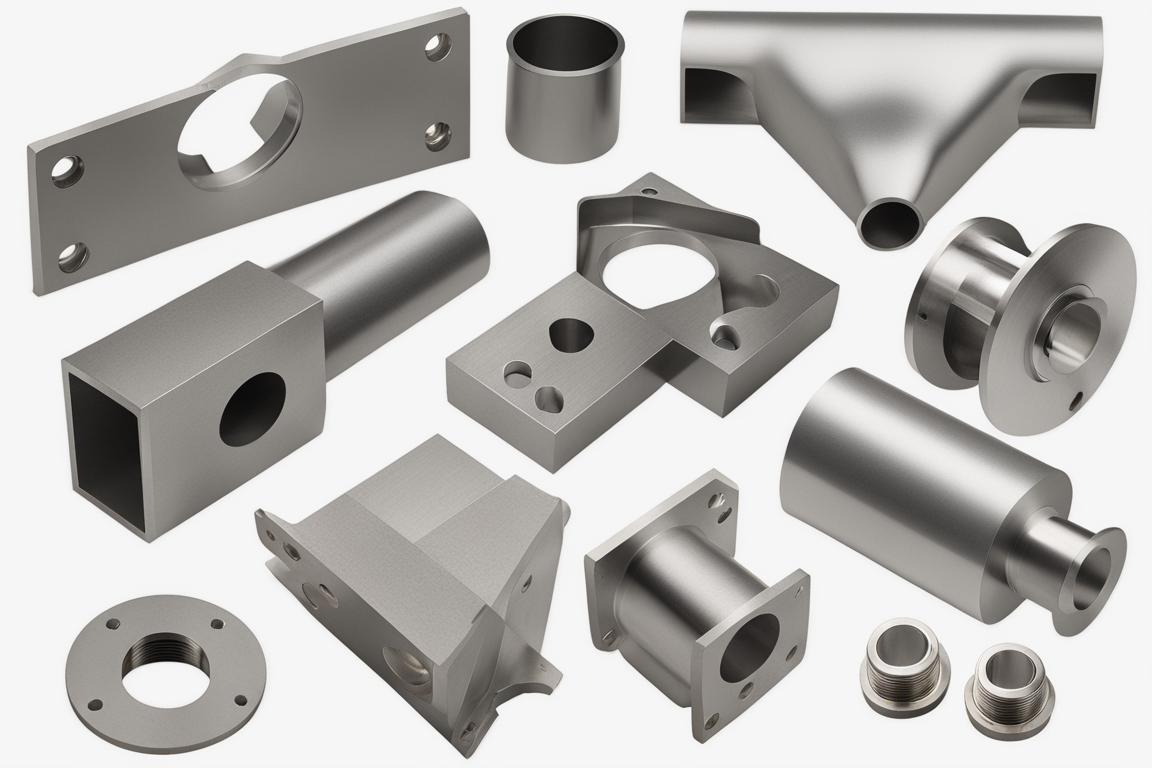
Types of Welded Assemblies
The art of welding encompasses various types of joints and structures, each serving a specific purpose in metal fabrication. Understanding these different types is crucial for fabricating welded assemblies with the desired strength and integrity.
T-Joints
T-joints are formed when two metal components intersect perpendicularly, creating a “T” shape. These joints are commonly used to connect two components at right angles and are prevalent in a wide range of applications, from structural frameworks to machinery.
Lap Joints
Lap joints involve overlapping two metal components and welding them together along the overlapping sections. This type of joint is particularly useful for joining large surfaces or components that require additional strength and stability.
Butt Joints
Butt joints are formed by aligning the edges of two metal components and welding them together at the seam. This type of joint is commonly used to create continuous and seamless connections between components, ensuring structural integrity.
Corner Joints
Corner joints are created when two metal components meet at a 90-degree angle and are welded together to form a corner. These joints are widely used in constructing frames, enclosures, and other structural elements.
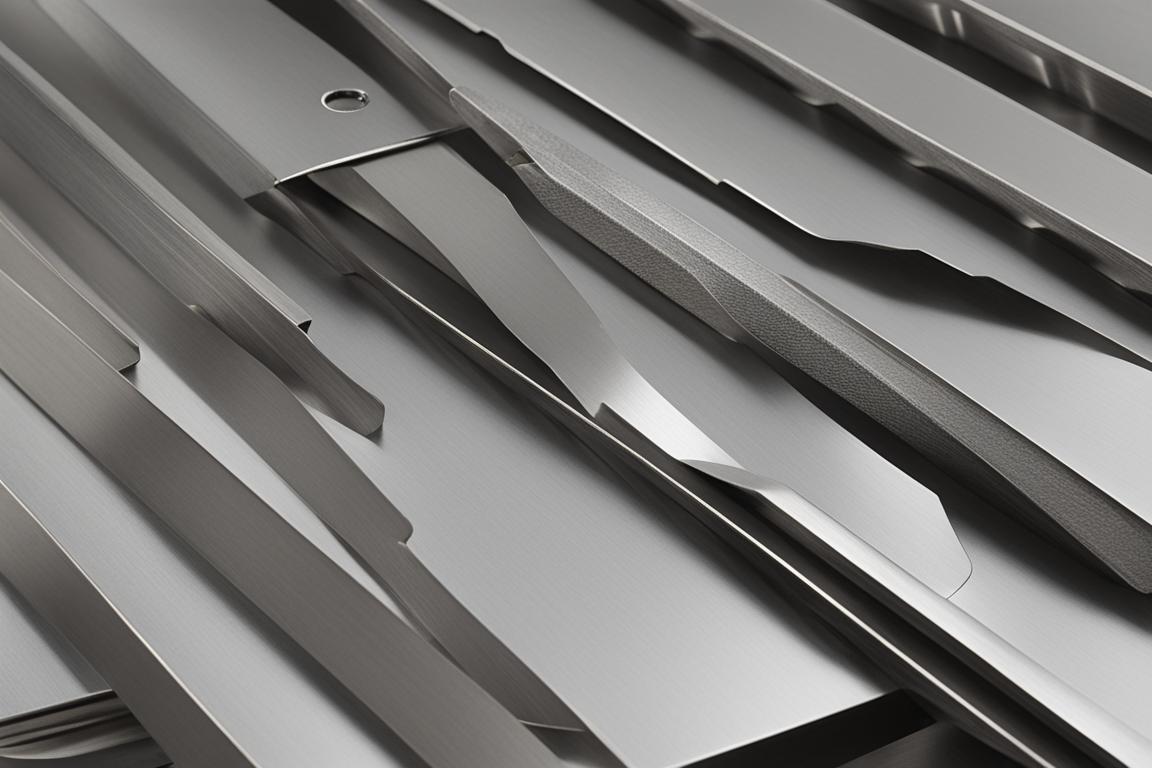
Materials Used in Welded Assemblies
The choice of materials in welded assemblies is critical and directly impacts the strength, durability, and performance of the final product. Different materials present unique challenges and considerations in the welding process.
Stainless Steel
Stainless steel is a popular choice for welded assemblies due to its corrosion resistance and durability. Welding stainless steel requires specific techniques to prevent distortion and maintain the material’s properties.
Aluminum
Aluminum is valued for its lightweight and high strength-to-weight ratio, making it suitable for various applications. However, welding aluminum demands precise control of the welding parameters to ensure proper penetration and avoid defects.
Carbon Steel
Carbon steel is widely used in welded assemblies due to its strength and affordability. Welding carbon steel requires careful consideration of preheating and post-weld heat treatment to mitigate the risk of cracking and distortion.
Unique Considerations for Each Material
Each material used in welded assemblies presents distinct challenges and requirements during the welding process. Understanding these nuances is essential for achieving high-quality and durable welded structures across different materials.
Welding Technique | Description |
---|---|
TIG Welding | Tungsten Inert Gas (TIG) welding, or Gas Tungsten Arc Welding (GTAW), is a precise and versatile welding process. |
MIG Welding | Metal Inert Gas (MIG) welding, or Gas Metal Arc Welding (GMAW), is known for its efficiency and ease of use. |
Resistance Welding | Involves passing current through the metal components to generate heat, forming a weld at the point of contact. |
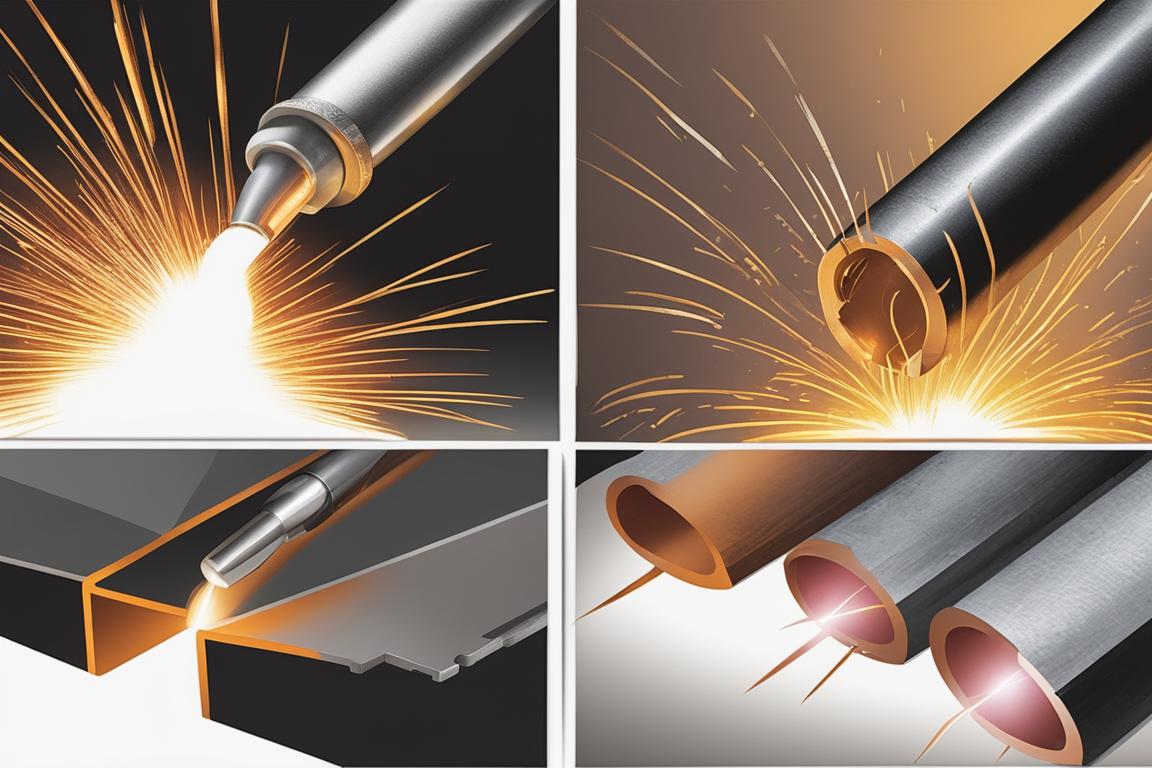
Welding Techniques for Assembling Metal
The art of welding encompasses a range of techniques, each suited to specific applications and materials. Choosing the right welding technique is crucial for ensuring the integrity and quality of welded assemblies.
TIG Welding
Tungsten Inert Gas (TIG) welding, also known as Gas Tungsten Arc Welding (GTAW), is a precise and versatile welding process suitable for a wide range of materials. TIG welding produces clean and high-quality welds, making it ideal for intricate and detailed assemblies.
MIG Welding
Metal Inert Gas (MIG) welding, or Gas Metal Arc Welding (GMAW), is known for its efficiency and ease of use. MIG welding is well-suited for high-volume production and can be applied to various materials, making it a popular choice for welded assemblies in diverse industries.
Resistance Welding
Resistance welding involves passing current through the metal components to generate heat, forming a weld at the point of contact. This technique is ideal for joining thin metal sheets and is commonly used in the automotive and electronics industries.
By incorporating specific examples, case studies, and insights from industry professionals, we can enhance the expertise conveyed in the article. Providing real-world scenarios and their successful resolutions would further demonstrate practical expertise in welded assemblies, elevating the content to offer a comprehensive understanding of the topic.
Answers To Common Questions
What are welded assemblies in precision sheet metal fabrication?
Welded assemblies are metal components joined together using welding techniques.
Who performs the welding in precision sheet metal fabrication?
Skilled welders with expertise in various welding techniques perform the welding.
How are welded assemblies inspected for quality in sheet metal fabrication?
Welded assemblies are inspected using non-destructive testing methods to ensure quality.
What makes welded assemblies a cost-effective solution?
Welded assemblies provide cost efficiencies by reducing the need for additional fasteners.
How can precision in welded assemblies be assured?
Precision in welded assemblies is assured through advanced equipment and skilled craftsmanship.
Isn’t welding prone to distortion in precision sheet metal fabrication?
Skilled welders and precision fixtures help minimize distortion in welded assemblies.