Are you looking to understand the intricacies of sheet metal punching in precision fabrication? Look no further. Sheet metal punching is a crucial process in precision sheet metal fabrication, playing a vital role in creating a wide array of finished and semi-finished products. This technique involves using a punch tool to impress a form on a metal surface through pressure or percussion. Atlas Manufacturing, a pioneer in the sheet metal fabrication industry since 1962, offers invaluable insights into the world of sheet metal punching.
Learn about Sheet Metal Punching in Precision Fabrication
- Sheet metal punching is the process of creating holes and shapes in sheet metal using a punch and die.
- Readers will learn about the process, equipment, materials, optimization, quality control, applications, and future trends in sheet metal punching.
- The article highlights the importance of sheet metal punching in creating finished and semi-finished products for various industries.
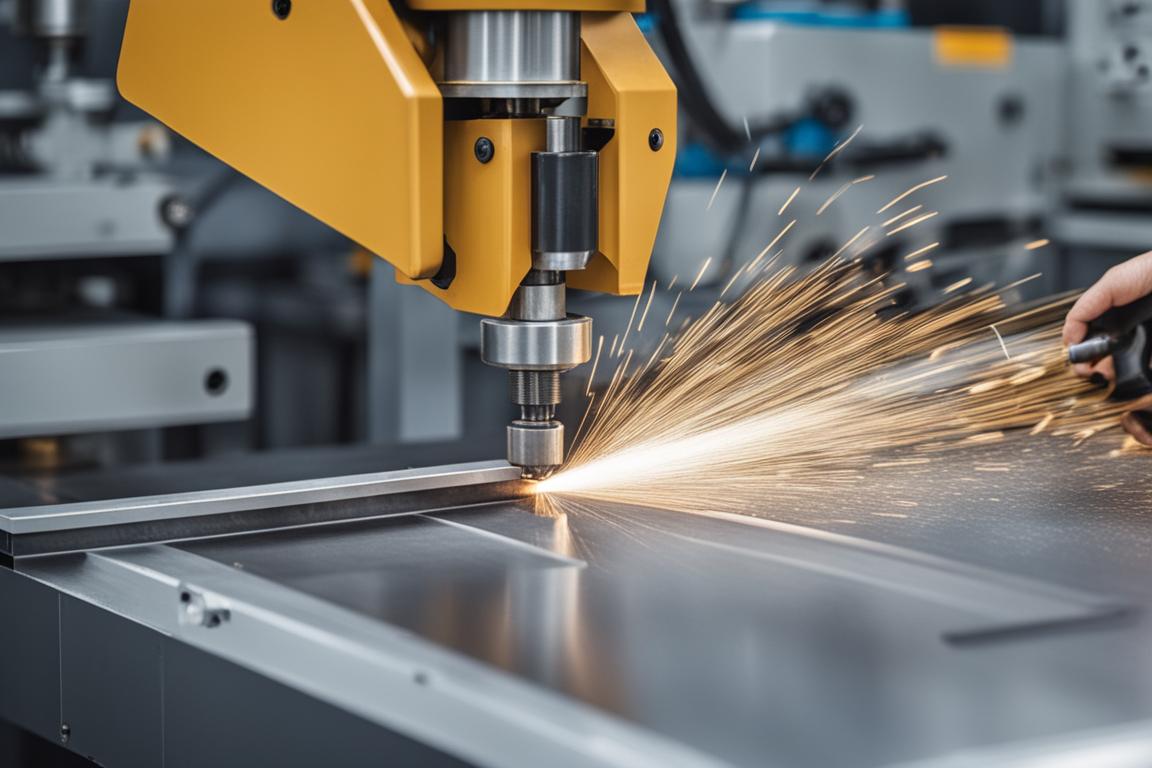
Process of Sheet Metal Punching
Mechanism and Methodology
Sheet metal punching begins with preparing a sheet metal workpiece, which is then placed onto a die. A punch tool is then driven into the sheet metal, creating a hole, cavity, or other forms as required. This process can be performed manually or using advanced CNC punching machines for enhanced precision and efficiency.
Key Components and Tooling
The components involved in sheet metal punching, including the punch, die, and stripper, along with the sheet metal workpiece, determine the quality and accuracy of the punched features.
Impact on Material Integrity and Surface Finish
When executed with precision, sheet metal punching can produce clean, burr-free holes and forms without compromising the structural integrity of the workpiece.
Precision and Accuracy in Forming Metal Surfaces
The precision and accuracy achieved through sheet metal punching make it indispensable for the fabrication of intricate and complex metal components.
Aspect | Sheet Metal Punching | Laser Cutting | Stamping | Bending |
---|---|---|---|---|
Cost-effectiveness | High | Moderate | Moderate | Low |
Precision and Accuracy | High | High | Moderate | High |
Suitability for Various Material Thicknesses | High | Low | High | Moderate |
Handling Complex Designs | Moderate | High | Low | High |
Comparison with Other Fabrication Techniques
Contrasting Sheet Metal Punching with Other Techniques
In comparison to laser cutting, stamping, and bending, sheet metal punching offers unique advantages in terms of cost-effectiveness, precision, and suitability for various material thicknesses.
Advantages and Limitations
Sheet metal punching excels in producing medium to large quantities of simple geometries or formed features with high precision. However, it may have limitations in handling highly intricate or complex designs better suited for laser cutting or other advanced fabrication methods.
Applications and Suitability
The versatility of sheet metal punching makes it suitable for a wide range of project requirements, from creating ventilation holes in enclosures to forming custom shapes in automotive components.
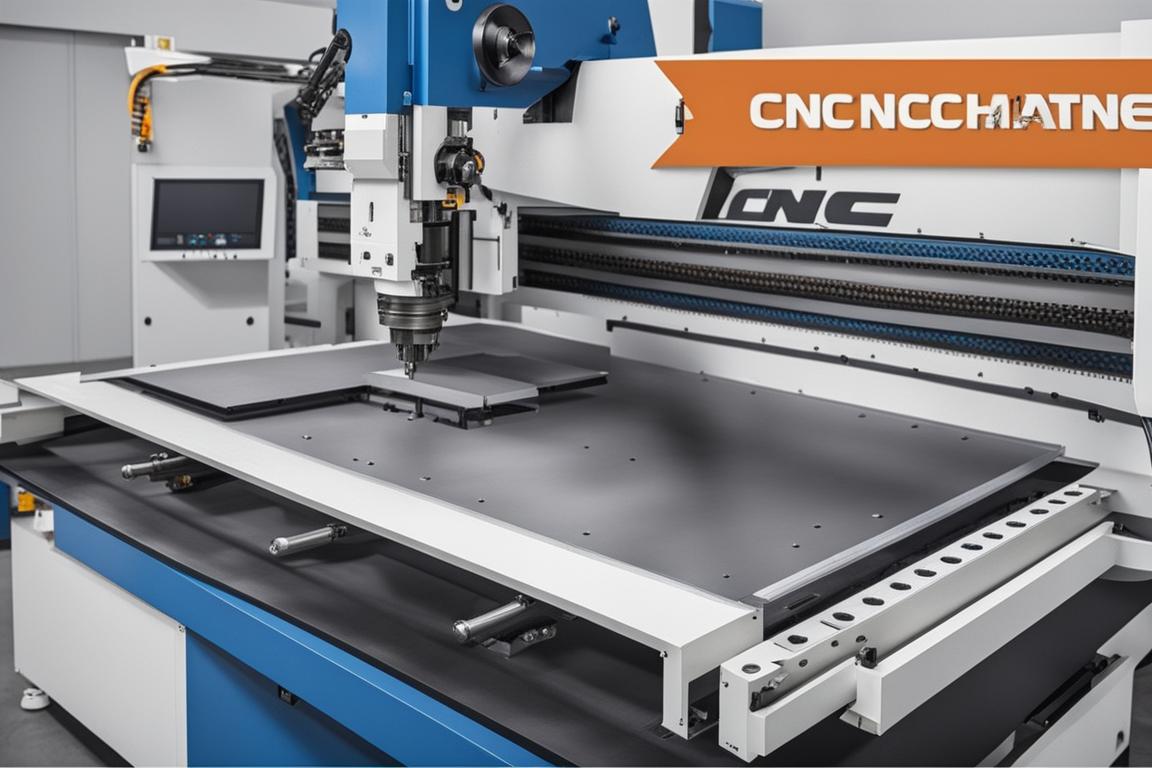
Equipment and Technology in Sheet Metal Punching
Overview of Machinery and Equipment
In modern sheet metal fabrication facilities, sheet metal punching is carried out using advanced CNC punching machines equipped with multiple tool stations and sophisticated control systems.
Role of CNC Punching Machines
CNC punching machines play a pivotal role in achieving high precision and efficiency in sheet metal punching, capable of executing complex punching operations with minimal setup times and exceptional repeatability.
Tool Stations and CAD/CAM Programming
The availability of multiple tool stations in CNC punching machines allows for the execution of diverse punching operations in a single setup. Additionally, CAD/CAM programming ensures seamless translation of design specifications into precise punching instructions.
Influence on Precision and Efficiency in Fabrication
The integration of advanced machinery and technology elevates the precision and efficiency of sheet metal punching, enabling fabricators to meet stringent quality standards and deliver complex punched features with remarkable accuracy.
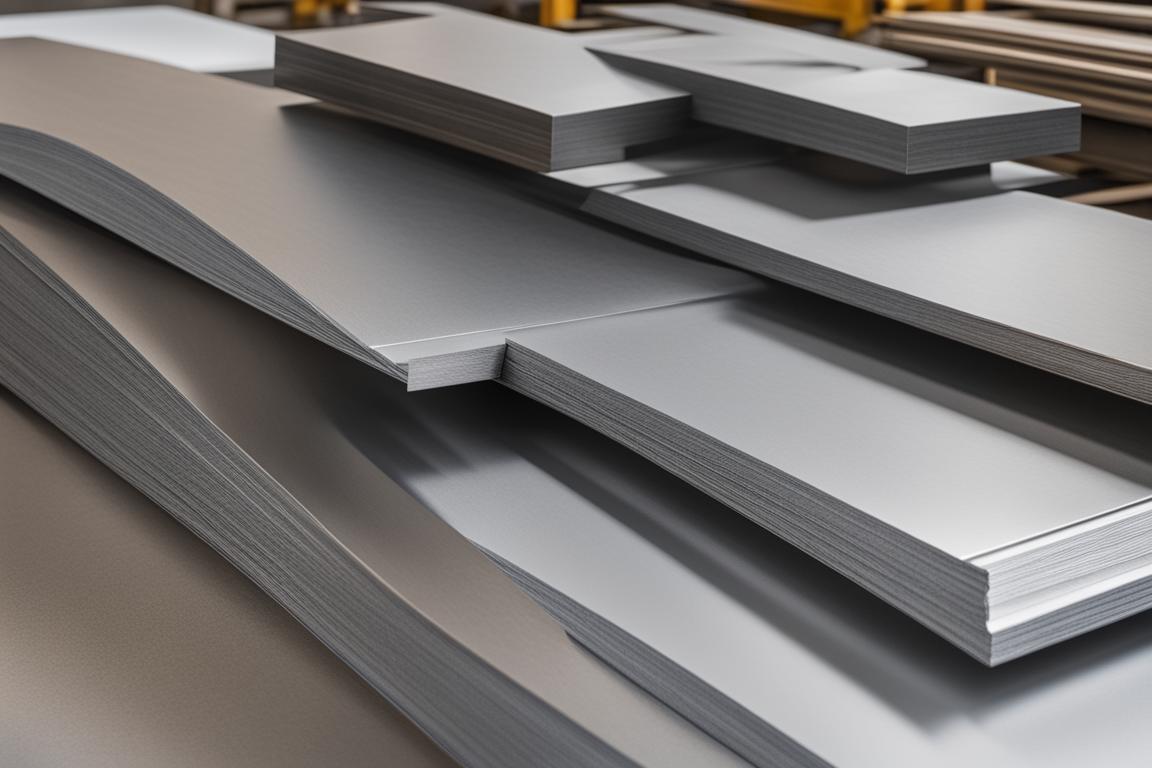
Materials and Capabilities for Sheet Metal Punching
Types of Materials Suitable for Punching
Sheet metal punching is suitable for a wide range of materials, including steel, aluminum, copper, and various alloys, making it a go-to method for fabricating components across diverse industries.
Effective Punching of Steel, Aluminum, Copper, and Alloys
The capability of sheet metal punching to effectively process steel, aluminum, copper, and alloys underscores its significance in addressing the fabrication needs of various industrial sectors.
Range of Capabilities
Sheet metal punching can accommodate varying material thicknesses, hole sizes, and complex geometries, making it a versatile and adaptable process for meeting diverse design requirements.
Process Optimization in Sheet Metal Punching
Strategies for Enhancing Efficiency and Quality
Optimizing the sheet metal punching process involves implementing strategies to enhance efficiency, minimize material waste, and improve the overall quality of punched components.
Considerations for Tooling, Programming Techniques, and Material Handling
Effective tooling selection, advanced programming techniques, and optimized material handling are essential considerations in the pursuit of process optimization for sheet metal punching.
Cost-Effectiveness and Waste Reduction Measures
By implementing efficient process management and waste reduction measures, fabricators can achieve cost-effectiveness and sustainability in sheet metal punching operations.
Quality Control and Inspection in Sheet Metal Punching
Ensuring Dimensional Accuracy and Surface Finish
Quality control and inspection play a critical role in ensuring the dimensional accuracy and surface finish of punched components, essential for meeting precise engineering specifications.
Role of Inspection and Testing Methods
Utilizing advanced inspection and testing methods enables fabricators to maintain high standards of quality in sheet metal punching.
Maintaining Overall Part Quality and Integrity
The rigorous application of quality control and inspection processes ensures that the overall part quality and integrity are upheld throughout the sheet metal punching process.
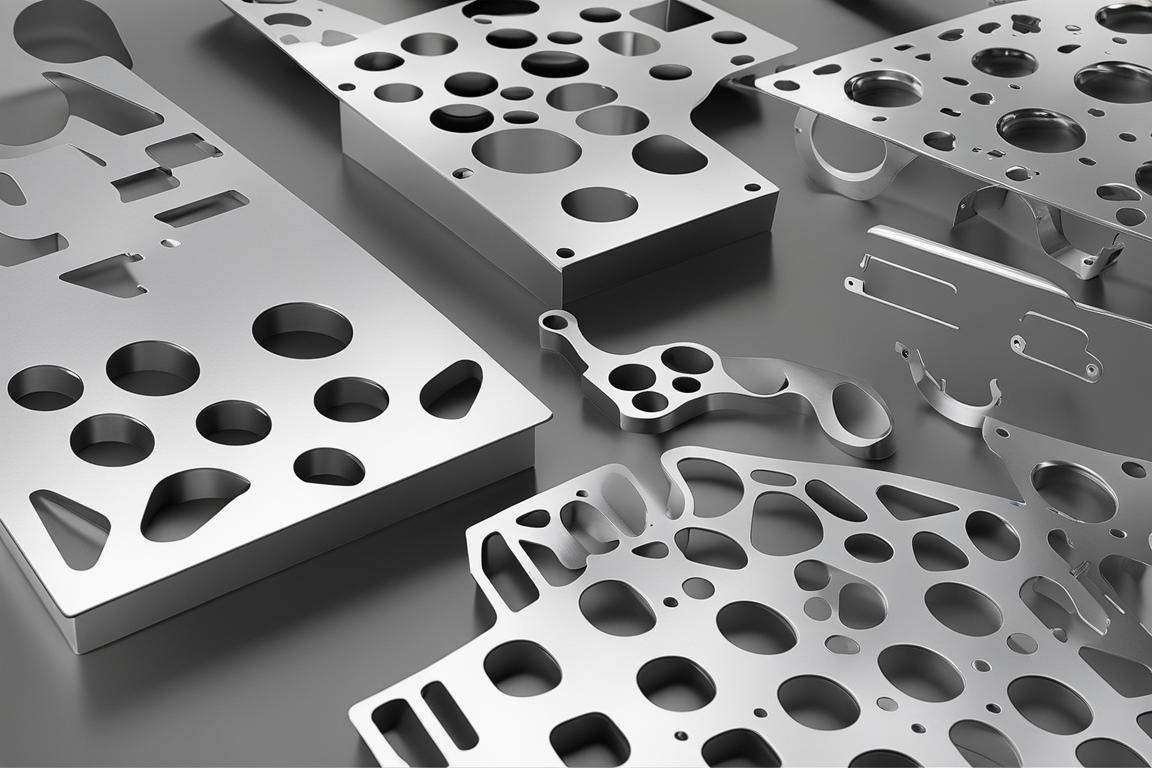
Applications and Case Studies of Sheet Metal Punching
Real-World Examples Highlighting Diverse Applications
Numerous real-world examples demonstrate the extensive applications of sheet metal punching in industries such as electronics, automotive, aerospace, and consumer goods manufacturing.
Case Studies Demonstrating Precision Fabrication Projects
Case studies showcasing precision fabrication projects underscore the critical role of sheet metal punching in delivering complex, high-quality components for diverse applications.
Versatility and Adaptability
The versatility and adaptability of sheet metal punching make it indispensable for fabricating components across diverse industries and product types.
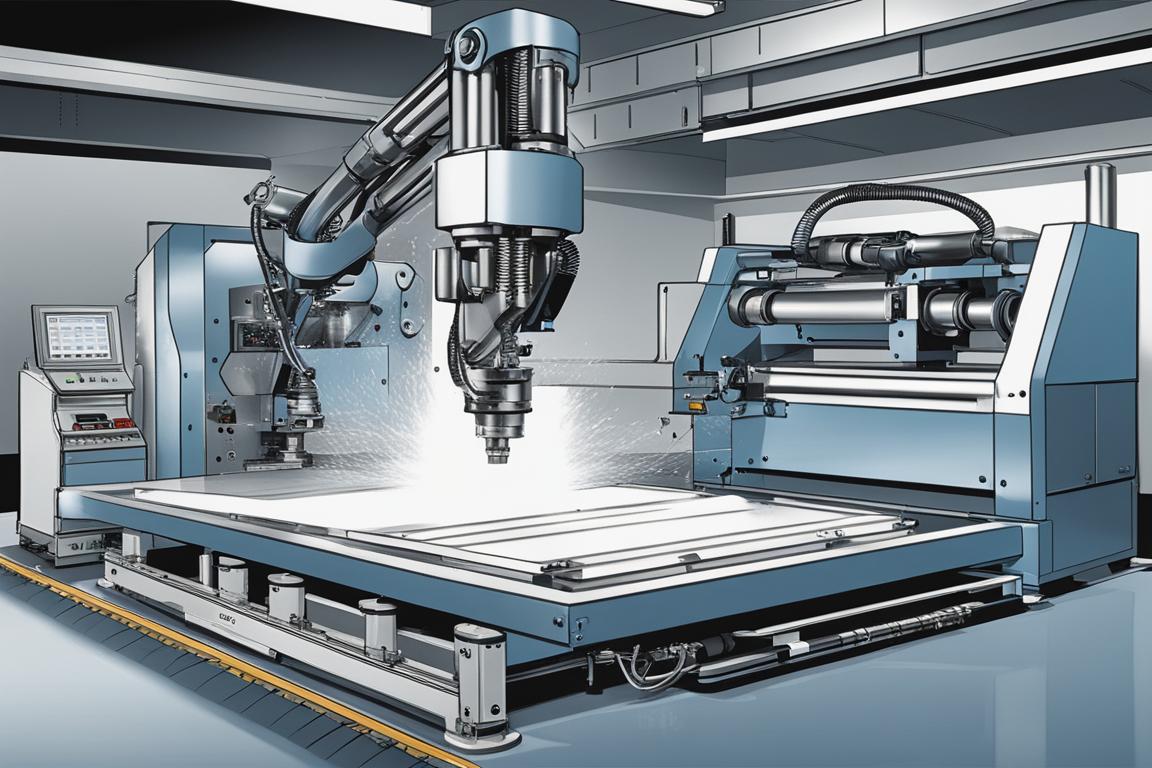
Future Trends and Advancements in Sheet Metal Punching
Emerging Trends and Advancements
The future of sheet metal punching is poised for advancements in technology, including the integration of automation, robotics, and digital manufacturing solutions for enhanced productivity and precision.
Integration of Automation, Robotics, and Digital Manufacturing Solutions
The integration of automation, robotics, and digital manufacturing solutions holds the potential to revolutionize sheet metal punching, leading to greater efficiency and flexibility in fabrication processes.
Enhanced Precision, Productivity, and Sustainability
Future trends in sheet metal punching are expected to focus on achieving enhanced precision, productivity, and sustainability through the adoption of cutting-edge technologies and process innovations.
Conclusion and Industry Insights
Sheet metal punching stands as a cornerstone of precision sheet metal fabrication, offering unparalleled versatility, precision, and efficiency in creating a diverse range of metal components. As the industry continues to evolve, the relevance and impact of sheet metal punching are expected to endure, driving innovation and excellence in precision fabrication.
Atlas Manufacturing has been a pioneer in the sheet metal fabrication industry since 1962. The company’s expertise and history make it a reliable source of information and guidance in the field.
Answers To Common Questions
Who uses sheet metal punching in precision sheet metal fabrication?
Sheet metal punching is used by manufacturers to create precise holes and shapes in sheet metal for various products.
What is sheet metal punching in precision sheet metal fabrication?
Sheet metal punching is a process that uses a punch and die to cut holes, forms, or shapes in sheet metal with high accuracy.
How does sheet metal punching contribute to precision sheet metal fabrication?
Sheet metal punching allows for efficient production of precise holes and shapes in sheet metal, contributing to accurate fabrication.
What if I need complex shapes in my sheet metal parts?
Sheet metal punching can produce complex shapes with multi-step punching processes, ensuring precise fabrication of complex parts.
How can I ensure the accuracy of sheet metal punching?
To ensure accuracy, use precision tools, maintain proper punch and die clearance, and regularly inspect and maintain punching equipment.
What are the benefits of sheet metal punching in fabrication?
Sheet metal punching offers cost-effective production, high precision, and rapid manufacturing of sheet metal parts, contributing to efficient fabrication processes.