What You Will Learn About Welded Assemblies
By reading this article, you will learn:
1. The different types and importance of welded assemblies in precision sheet metal fabrication.
2. The selection of materials and welding techniques for welded assemblies.
3. The design considerations, quality control measures, advantages, and applications of welded assemblies.
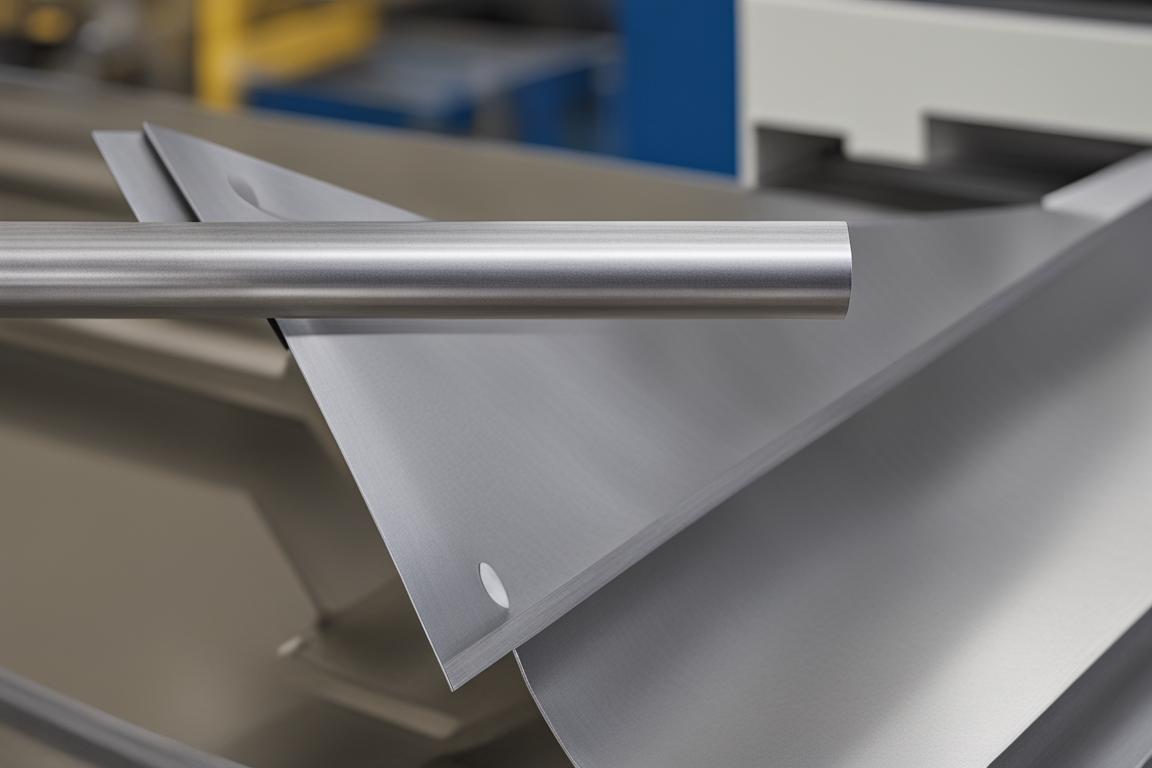
What Are Welded Assemblies and Why Are They Important?
Welded assemblies are a crucial part of modern manufacturing, especially in precision sheet metal fabrication. They play a significant role in providing structural integrity and durability to a wide array of products across various industries. To ensure high-quality welded assemblies that meet industry standards and regulatory requirements, it is essential to understand welding techniques, material selection, and design considerations.
Definition and Types of Welded Assemblies
Welded assemblies involve joining metal components through heat, pressure, or a combination of both to create a cohesive structure. Various types of welded assemblies, such as butt joints, lap joints, corner joints, and T-joints, cater to specific applications based on structural requirements and material characteristics.
1. Importance in Precision Sheet Metal Fabrication
In precision sheet metal fabrication, welded assemblies are instrumental in creating complex structures with high dimensional accuracy. Industries such as automotive, aerospace, and electronics rely on precision welding techniques to achieve the desired form, fit, and function of the final product.
2. Key Considerations in Welded Assemblies
To achieve optimal results, a comprehensive understanding of material compatibility, welding techniques, design considerations, and quality control measures is essential. These elements collectively contribute to the structural integrity, reliability, and longevity of welded components.
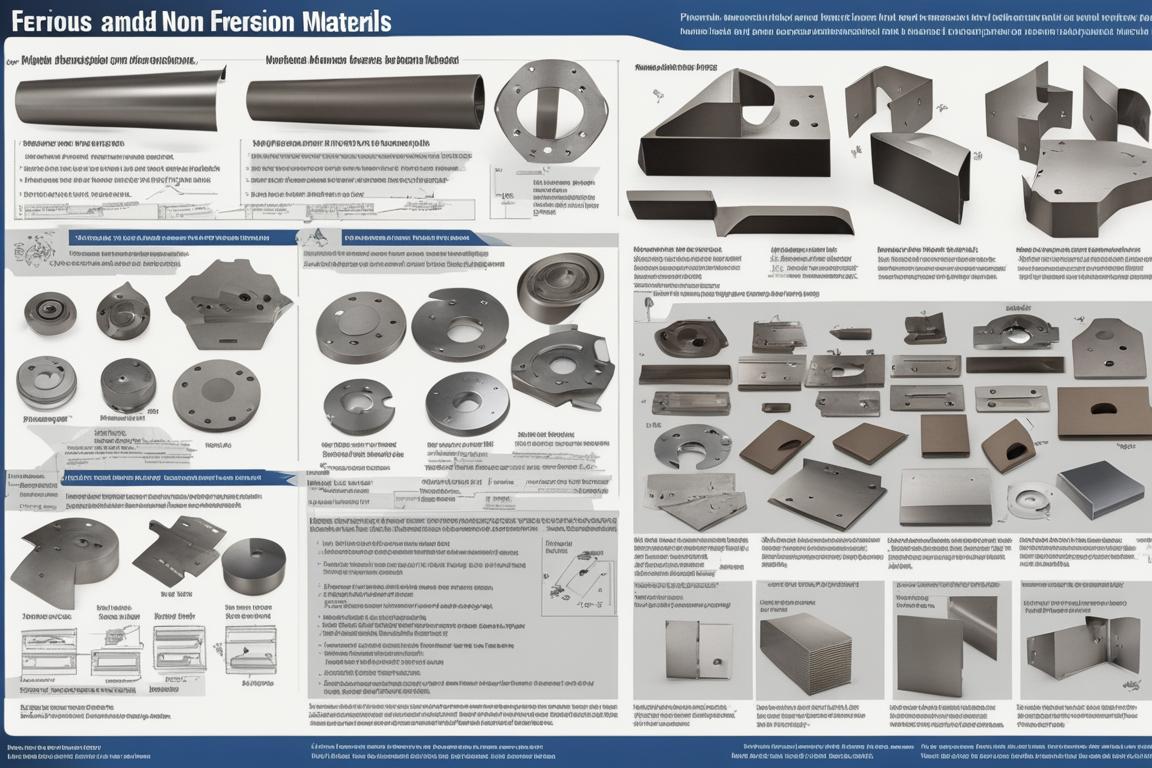
Materials Selection for Welded Assemblies
Ferrous and Non-Ferrous Materials
1. Characteristics and Applications
Ferrous materials like carbon steel and stainless steel offer robust mechanical properties and corrosion resistance, making them widely used in welded assemblies. Non-ferrous materials, including aluminum and copper alloys, provide lightweight and conductive properties suitable for diverse applications in industries like electronics and aerospace.
2. Considerations for Selecting Material
When selecting materials for welded assemblies, factors such as mechanical strength, thermal conductivity, and corrosion resistance must be carefully evaluated. Additionally, considerations for post-weld processes, such as machining and surface finishing, play a crucial role in material selection.
Importance of Material Compatibility in Welded Assemblies
1. Factors Influencing Material Selection
Material compatibility in welded assemblies is essential to prevent issues such as galvanic corrosion, metallurgical incompatibility, and structural weaknesses. Understanding the interaction between dissimilar materials is imperative for creating durable and long-lasting welded joints.
2. Impact of Material Properties on Welding Techniques
Material properties significantly influence the selection of welding techniques and the parameters used during the welding process. Matching the welding method to the material properties ensures the integrity of the welded joint and mitigates the risk of material distortion or failure.
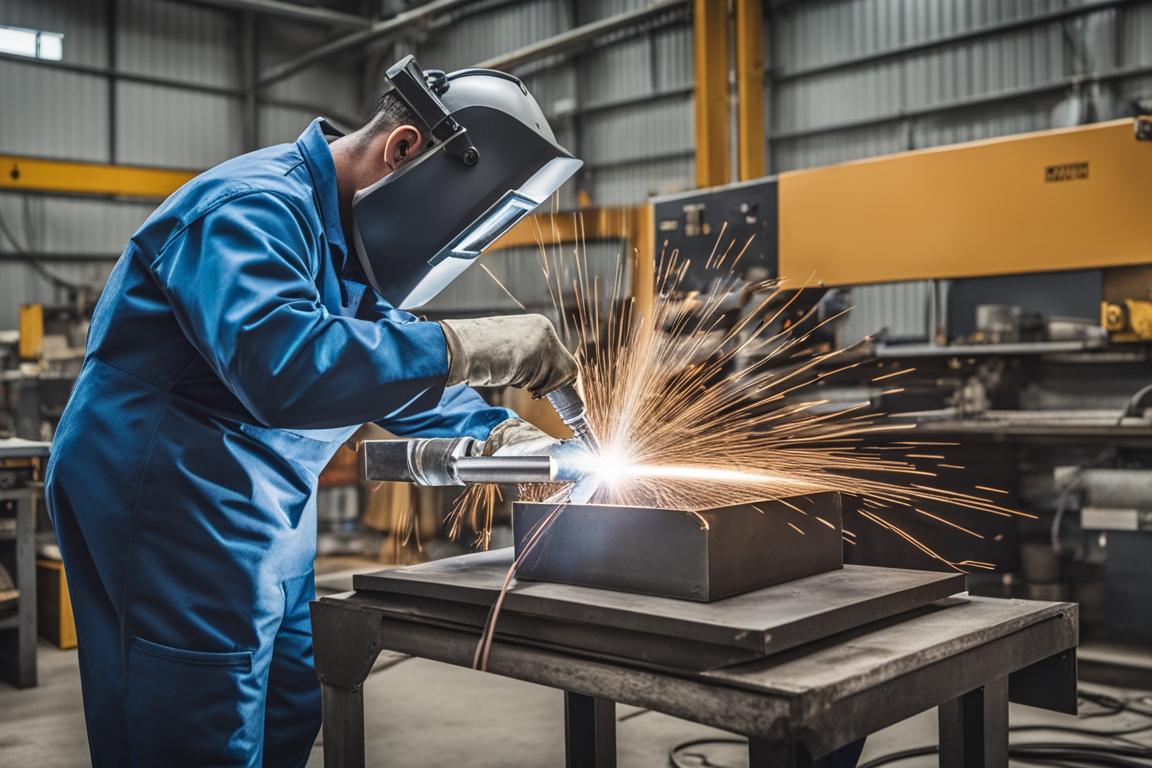
Exploring Welding Techniques for Assemblies
MIG Welding
1. Process Overview and Equipment
MIG (Metal Inert Gas) welding, also known as Gas Metal Arc Welding (GMAW), utilizes a consumable wire electrode and a shielding gas to protect the weld pool from atmospheric contamination. This technique is suitable for a wide range of materials, including steel, aluminum, and stainless steel, making it a versatile choice for welded assemblies.
2. Advantages and Limitations
MIG welding offers high deposition rates, excellent weld bead appearance, and minimal post-weld cleanup, enhancing the efficiency and aesthetics of welded assemblies. However, potential issues with weld spatter and control make it less suitable for thin materials or overhead welding.
TIG Welding
1. Application and Benefits
TIG (Tungsten Inert Gas) welding, or Gas Tungsten Arc Welding (GTAW), involves the use of a non-consumable tungsten electrode and a separate filler material if necessary. This precise and versatile welding method is well-suited for thin materials and exotic alloys, making it ideal for intricate welded assemblies with stringent quality requirements.
2. Comparisons with Other Welding Techniques
In comparison to MIG welding, TIG welding offers superior control over the welding process, resulting in high-quality, clean welds with minimal distortion. However, it requires a higher level of skill and is generally slower than MIG welding, making it more suitable for specialized applications.
Spot Welding
1. Applications and Methodology
Spot welding, a resistance welding process, involves the localized application of heat and pressure to join overlapping metal sheets. This technique is commonly used in the automotive and electronic industries for creating rapid, repetitive welds in sheet metal assemblies.
2. Suitability for Different Material Types
While spot welding is well-suited for ferrous materials, its application to non-ferrous materials may require adjustments in welding parameters to achieve optimal weld strength and integrity.
Comparing and Contrasting Different Welding Techniques
1. Applications and Optimal Use Cases
Each welding technique has its unique applications and optimal use cases based on material type, joint design, and production requirements.
2. Advantages and Disadvantages in Various Scenarios
While MIG welding excels in high-speed production and versatility, TIG welding offers superior precision and quality for intricate assemblies. Spot welding, on the other hand, provides rapid and cost-effective joining of sheet metal components, albeit with limitations on material compatibility.
Design Considerations for Welded Assemblies
Design for Manufacturability (DFM) in Welded Assemblies
1. Integration of Welding Processes in Design
Incorporating welding processes into the design phase is critical for optimizing manufacturing efficiency and ensuring the structural integrity of welded assemblies. Design for Manufacturability (DFM) principles guide the creation of weld-friendly designs that minimize production complexities and reduce manufacturing costs.
2. Optimizing Designs for Manufacturing Efficiency
Efficient designs that account for welding considerations, such as joint accessibility, weld sequence, and fixture requirements, streamline the fabrication process and contribute to the overall quality and consistency of welded assemblies.
Joint Design, Material Thickness, and Welding
1. Impact of Joint Configurations on Structural Integrity
The selection of appropriate joint designs directly influences the structural integrity and load-bearing capacity of welded assemblies. Proper joint design is essential for distributing loads and minimizing stress concentrations within the welded components.
2. Considerations for Varying Material Thicknesses
Differences in material thicknesses require tailored welding approaches to ensure consistent and reliable fusion between dissimilar materials. Understanding the effects of material thickness on heat distribution and weld penetration is vital for producing high-quality welds in assemblies with varying material gauges.
Tolerances and Their Influence on Welded Assemblies
1. Role of Tolerances in Welding Processes
Tolerances play a critical role in welding operations, influencing the fit-up of components, dimensional accuracy, and the overall quality of welded assemblies. Adhering to tight tolerances is essential for achieving precise and repeatable weldments that meet design specifications.
2. Ensuring Precision and Quality in Welded Assemblies
Close attention to tolerances during the fabrication of welded assemblies is paramount for ensuring dimensional accuracy, alignment, and the overall functionality of the final product. Proper tolerance management contributes to the reliability and performance of the welded components in their intended applications.
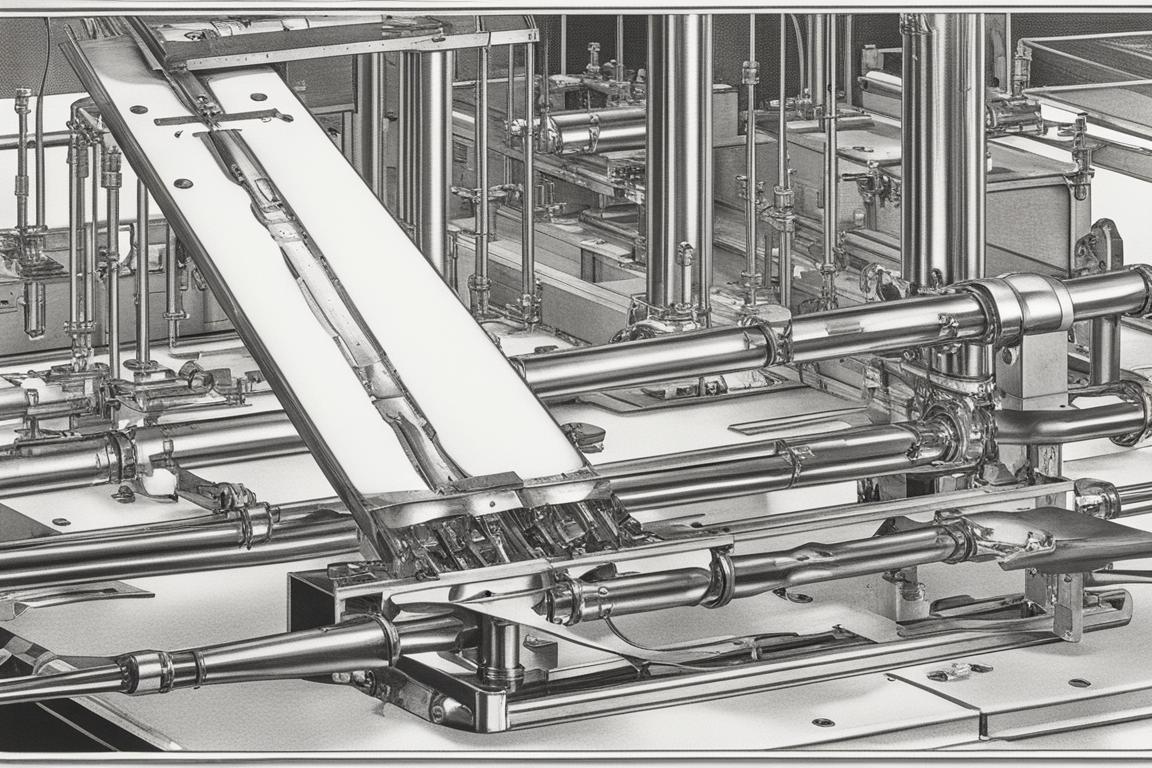
Quality Control and Inspection in Welded Assemblies
Significance of Quality Control Measures
1. Ensuring Weld Integrity and Structural Strength
Quality control measures are indispensable for verifying the integrity of welded joints, detecting defects, and ensuring the structural strength and durability of welded assemblies. Thorough quality control processes mitigate the risk of weld discontinuities and material imperfections that could compromise the performance of the assemblies.
2. Importance of Quality in Welded Assemblies
The significance of quality in welded assemblies extends beyond compliance with industry standards and customer requirements. High-quality welds contribute to the overall reliability, safety, and longevity of the products in which welded assemblies are incorporated.
Non-Destructive Testing Methods for Welded Assemblies
1. Overview of Inspection Techniques
Non-destructive testing (NDT) methods, such as radiographic testing, ultrasonic testing, and magnetic particle inspection, offer non-invasive means of evaluating weld quality and detecting internal defects without compromising the integrity of the welded assemblies.
2. Ensuring Quality and Reliability
The application of NDT methods ensures the detection of imperfections, such as porosity, cracks, and incomplete fusion, enabling corrective actions to be taken to maintain the quality and reliability of welded assemblies.
Visual Inspections and Standards Compliance
1. Visual Examination for Weld Quality
Visual inspections, encompassing weld profile examination, surface finish assessment, and weld discontinuity detection, provide valuable insights into the overall quality and workmanship of welded assemblies.
2. Meeting Industry Standards and Regulations
Adhering to industry standards, such as those outlined by organizations like the American Welding Society (AWS) and the International Organization for Standardization (ISO), is essential for ensuring compliance and upholding the quality and safety of welded assemblies.
Advantages and Applications of Welded Assemblies
Structural Strength and Durability
1. Influence of Welding Techniques on Structural Integrity
The application of advanced welding techniques contributes to the enhancement of structural strength and durability in welded assemblies. Proper weld selection, joint design, and process control directly impact the load-bearing capacity and resistance to mechanical stresses.
2. Longevity and Reliability of Welded Assemblies
Well-executed welded assemblies exhibit longevity and reliability, meeting the demands of diverse applications, from heavy-duty industrial equipment to intricate electronic devices. The inherent strength of welded joints ensures the sustained performance and operational safety of the assembled components.
Cost-Effectiveness and Efficiency
1. Economic Advantages of Welded Assemblies
Welded assemblies offer cost-effective solutions for joining metal components, reducing material waste, and minimizing the need for additional fastening hardware. The efficiency and speed of welding processes contribute to cost savings and streamlined production workflows.
2. Efficiency in Production and Assembly Processes
The efficient integration of welded assemblies into manufacturing processes optimizes production efficiency, assembly line throughput, and overall operational productivity. These advantages make welded assemblies a preferred choice in industries that emphasize lean manufacturing and just-in-time delivery practices.
Design Flexibility and Customization
1. Tailoring Welded Assemblies to Specific Applications
The versatility of welding techniques allows for the customization and adaptation of welded assemblies to meet specific design requirements and functional objectives. From complex structural frameworks to intricate component assemblies, welding facilitates the realization of diverse design concepts.
2. Adapting Designs to Varied Functional Requirements
The adaptability of welded assemblies enables the accommodation of varying functional requirements, such as load-bearing capacity, thermal conductivity, and electrical insulation, across a spectrum of industrial applications.
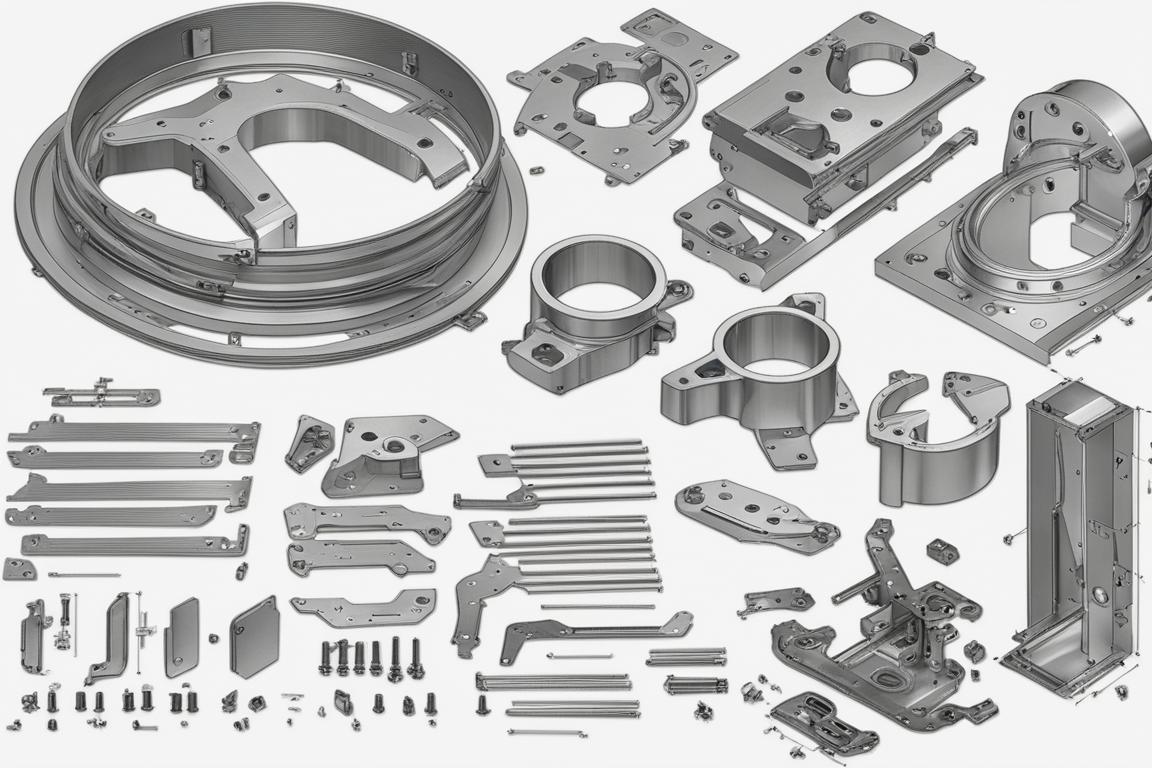
Case Studies and Applications of Welded Assemblies
Automotive Industry
1. Specific Applications and Case Examples
In the automotive industry, welded assemblies are integral to the fabrication of vehicle chassis, body frames, and powertrain components. The use of advanced welding techniques, such as robotic spot welding and laser welding, ensures the structural integrity and crashworthiness of automotive assemblies.
2. Welding Techniques and Innovations in Automotive Assembly
Innovations in welding technologies, including the integration of lightweight materials and advanced joining methods, contribute to the development of fuel-efficient and environmentally sustainable vehicles. The continuous evolution of welding solutions enhances the safety, performance, and manufacturing efficiency in the automotive sector.
Aerospace Industry
1. Welded Assembly Requirements and Challenges
The aerospace industry demands welded assemblies with uncompromising precision, structural reliability, and material integrity to withstand extreme environmental conditions and dynamic loads. Welding plays a critical role in the fabrication of aircraft structures, propulsion systems, and avionics components.
2. Advanced Welding Applications in Aerospace
Advanced welding applications, such as friction stir welding and electron beam welding, enable the production of lightweight, high-strength assemblies that meet the stringent performance and safety standards of the aerospace industry. These innovative welding methods contribute to the development of next-generation aircraft and space exploration technologies.
Electronics Industry
1. Precision Welding in Electronics Manufacturing
In the electronics industry, micro welding techniques, including laser welding and resistance spot welding, are utilized for creating miniature interconnects, hermetic seals, and fine wire assemblies. These precision welding methods ensure the reliability and functionality of electronic devices in diverse consumer and industrial applications.
2. Micro Welding Techniques and Applications
The application of micro welding techniques extends to the fabrication of medical devices, sensors, and microelectromechanical systems (MEMS), where the miniaturization and precision of welded assemblies are critical for achieving optimal performance and functionality.
Industry Trends and Innovations in Welded Assemblies
Latest Trends in Welding Processes
1. Advancements in Welding Technologies
The welding industry continues to witness advancements in welding automation, additive manufacturing, and hybrid welding processes, enhancing the efficiency, precision, and sustainability of welded assemblies.
2. Emerging Trends Shaping Welded Assemblies
Emerging trends, such as the integration of artificial intelligence (AI) for weld process optimization and the adoption of digital twin technology for virtual welding simulations, are reshaping the landscape of welded assemblies, paving the way for enhanced productivity and quality in manufacturing.
Technological Innovations in Welding Equipment
1. Automation and Robotics in Welding
The integration of robotic welding systems and automated welding cells streamlines production workflows, improves process consistency, and mitigates manual labor requirements, contributing to the advancement of Industry 4.0 principles in welding operations.
2. Digitalization and Industry 4.0 in Welded Assemblies
Digitalization initiatives, including the implementation of welding data analytics and real-time monitoring systems, drive the digital transformation of welding processes, fostering data-driven decision-making and predictive maintenance strategies in welded assembly manufacturing.
Selecting a Manufacturing Partner for Welded Assemblies
Factors to Consider in Choosing a Partner
1. Expertise and Experience in Welded Assemblies
When selecting a manufacturing partner for welded assemblies, evaluating their expertise in welding techniques, material knowledge, and industry experience is paramount for ensuring the successful realization of your welded assembly requirements.
2. Equipment Capabilities and Technological Resources
Assessing the manufacturing partner’s equipment capabilities, technological resources, and quality assurance processes provides insight into their ability to deliver high-quality welded assemblies that align with your specifications and performance expectations.
Quality Certifications and Compliance
1. Importance of Quality Standards and Certifications
Partnering with a manufacturer that holds relevant quality certifications, such as ISO 9001 and AWS D1.1, demonstrates their commitment to upholding rigorous quality standards and industry best practices in welded assembly manufacturing.
2. Ensuring Regulatory Compliance and Quality Assurance
Ensuring that the manufacturing partner complies with industry regulations, customer specifications, and product safety standards is essential for mitigating risks and maintaining the integrity of welded assemblies throughout their lifecycle.
Conclusion
Summary of Key Insights on Welded Assemblies
In summary, the comprehensive understanding of welding techniques, material selection, design considerations, and quality control measures is essential for achieving high-quality welded assemblies that meet the stringent requirements of modern manufacturing industries.
1. Recap of Essential Aspects Covered
Throughout this exploration of welded assemblies, we’ve delved into the critical aspects of material selection, welding techniques, design considerations, quality control, and the practical advantages and applications of welded assemblies across diverse industries.
2. Significance of Welded Assemblies in Modern Manufacturing
The significance of welded assemblies in modern manufacturing cannot be overstated, as they form the backbone of structural integrity, product durability, and design flexibility in precision sheet metal fabrication and various industrial sectors.
The Crucial Role of Welded Assemblies in Precision Sheet Metal Fabrication
1. Impact of Welding Techniques on Sheet Metal Fabrication
Welded assemblies play a pivotal role in achieving the precision, structural integrity, and functional versatility required in the fabrication of complex sheet metal components and assemblies.
Conclusion
The future of welded assemblies holds great promise for advancements in welding processes, materials, and digital technologies, which will enhance the quality, efficiency, and sustainability of manufacturing. Mastering the art and science of welded assemblies requires continuous learning, innovation, and a steadfast commitment to delivering excellence in modern manufacturing practices.
To deepen your understanding of welded assemblies and welding techniques, consider authoritative sources and industry expertise. Two valuable resources for gaining insights into welded assemblies and precision manufacturing include AMG Industries and Industry Welding Journal. Continuing to explore these resources will offer valuable perspectives and in-depth knowledge to further enhance your proficiency in the realm of welded assemblies and precision welding techniques.
To learn more about how AMG Industries can support your welded assembly needs, or to explore the latest welding techniques and industry trends, feel free to contact us today.
Questions & Answers
Who uses precision sheet metal welded assemblies?
Various industries such as automotive, aerospace, and electronics utilize these assemblies.
What are the advantages of precision sheet metal welded assemblies?
They offer high strength, precise tolerances, and complex geometries for different applications.
How are precision sheet metal welded assemblies fabricated?
They are fabricated using advanced welding techniques such as TIG, MIG, or laser welding for precise results.
What if I need custom designs for welded assemblies?
Our fabrication process allows for custom designs to meet specific requirements and dimensions.
How do precision sheet metal welded assemblies ensure quality?
Each assembly undergoes rigorous quality checks and inspections to meet industry standards.
What materials can be used for precision sheet metal welded assemblies?
Various materials such as stainless steel, aluminum, and carbon steel can be used for these assemblies.