What the reader will learn:
- The definition and significance of welded assemblies in precision sheet metal fabrication.
- The importance of planning, design, material preparation, welding techniques, quality control, and post-welding operations in creating reliable welded assemblies.
- Case studies and success stories of welded assembly projects in precision sheet metal fabrication.
Are you curious about the secrets behind precision sheet metal fabrication and the creation of large, intricate structures using multiple metal materials? Look no further, as we delve into the world of welded assemblies, a crucial component in this art form. By joining different metal components, such as stainless steel or aluminum, welded assemblies provide strength, durability, and versatility across various industries.
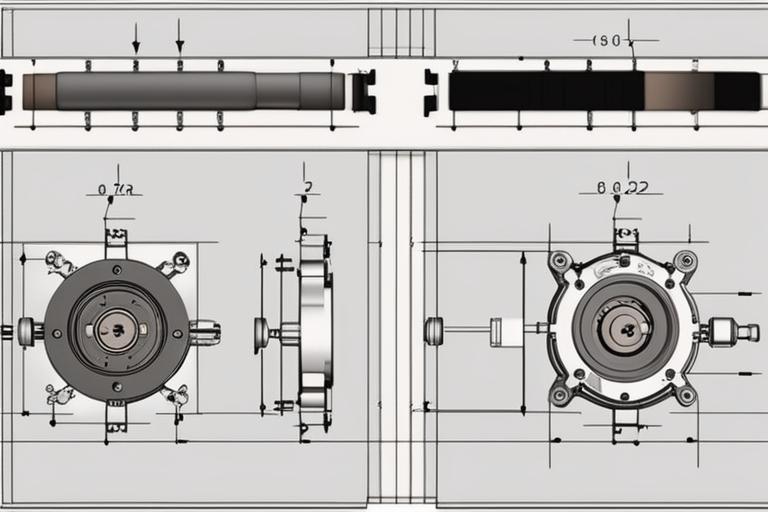
Importance of Planning and Design in Welded Assemblies
Before embarking on the fabrication of welded assemblies, effective planning and design are essential. This stage involves identifying specific requirements such as size, shape, and intended functionality. Selecting the appropriate materials for welding based on their properties and the intended application is also crucial.
Creating strong welding joints and connections is critical during the planning and design phase to ensure the overall quality and structural integrity of the welded assembly. Factors such as joint type, weld size, and welding position must be taken into account to achieve the desired results.
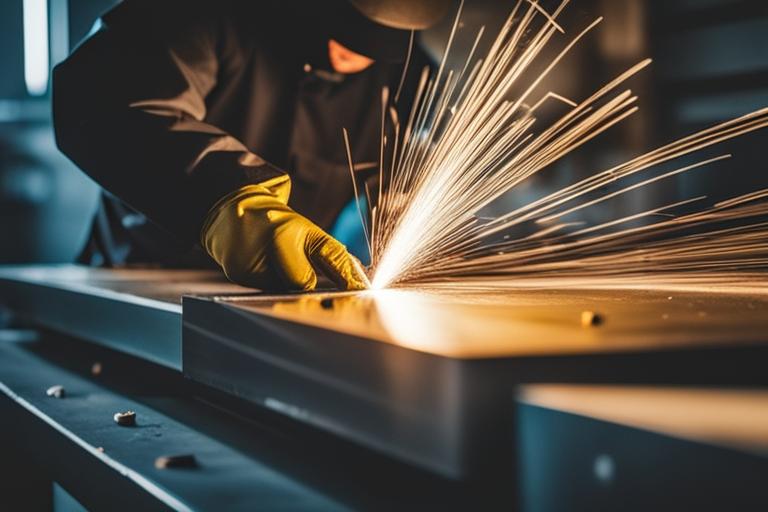
Material Preparation for Welded Assemblies
To achieve high-quality welded assemblies, proper material preparation is vital. Before welding, it is necessary to clean and prepare the metal surfaces to be joined. This process involves removing contaminants such as dirt, grease, or rust that can negatively impact the weld quality. It is also important to remove oxidation on the metal surfaces to ensure a clean and secure weld.
In addition to surface preparation, achieving proper fit-up and alignment of the components is essential. This ensures that the welding joints are in the correct position, minimizing the risk of distortion or weak welds. Specialized tools and techniques, such as clamps, jigs, or fixtures, may be used to hold the components in place during the welding process.
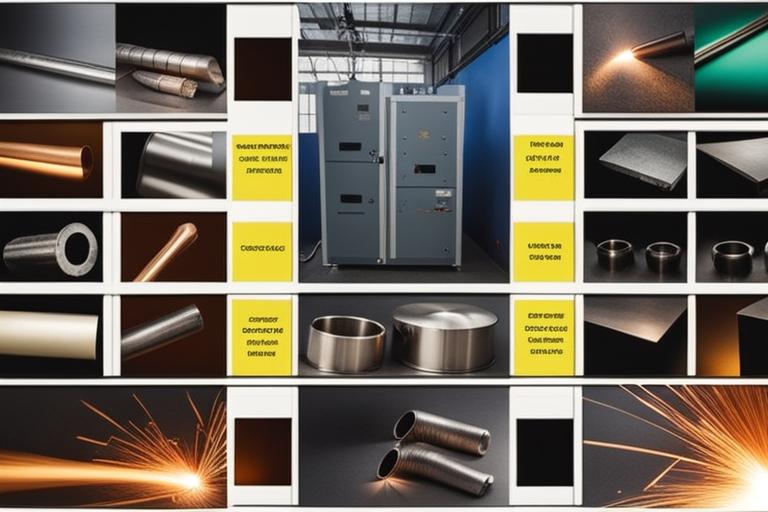
Overview of Welding Processes for Precision Sheet Metal Fabrication
Various welding processes are used in precision sheet metal fabrication to create welded assemblies. The choice of welding process depends on factors such as the type of metal, material thickness, and desired weld characteristics. Let’s explore some commonly used welding processes:
TIG (Tungsten Inert Gas) Welding
TIG welding, also known as GTAW (Gas Tungsten Arc Welding), is a precise and versatile welding process used in precision sheet metal fabrication. It uses a non-consumable tungsten electrode and an inert gas, such as argon, to shield the weld area from atmospheric contamination. TIG welding produces high-quality, clean welds with excellent aesthetic appearance, making it suitable for applications where appearance is important, such as in the automotive or architectural industries.
MIG (Metal Inert Gas) Welding
MIG welding, also known as GMAW (Gas Metal Arc Welding), is a widely used welding process in which a consumable wire electrode is continuously fed through a welding gun. The wire electrode melts and fuses the metal components together, while an inert gas, such as argon or a mixture of argon and carbon dioxide, shields the weld pool from atmospheric contamination. MIG welding is known for its speed and ease of use, making it suitable for high-volume production environments.
Spot Welding
Spot welding is a resistance welding process commonly used in the fabrication of welded assemblies. It involves applying electric current and pressure to create a weld at specific points between two overlapping metal sheets. Spot welding is fast, efficient, and produces strong and reliable welds. It is frequently used in the automotive industry for joining sheet metal components.
Choosing the appropriate welding process is crucial to ensure the optimal quality and performance of the welded assembly. Factors such as material type, thickness, and desired weld characteristics should be carefully considered when selecting the welding process.
Welding Process | Description | Application |
---|---|---|
TIG (Tungsten Inert Gas) Welding | Uses a non-consumable tungsten electrode and inert gas to shield the weld area. Produces clean welds with excellent aesthetic appearance. | Automotive, architectural industries |
MIG (Metal Inert Gas) Welding | Uses a consumable wire electrode and inert gas to shield the weld pool. Known for its speed and ease of use. | High-volume production environments |
Spot Welding | Applies electric current and pressure to create welds at specific points between overlapping metal sheets. Fast, efficient, and produces strong welds. | Automotive industry, joining sheet metal components |
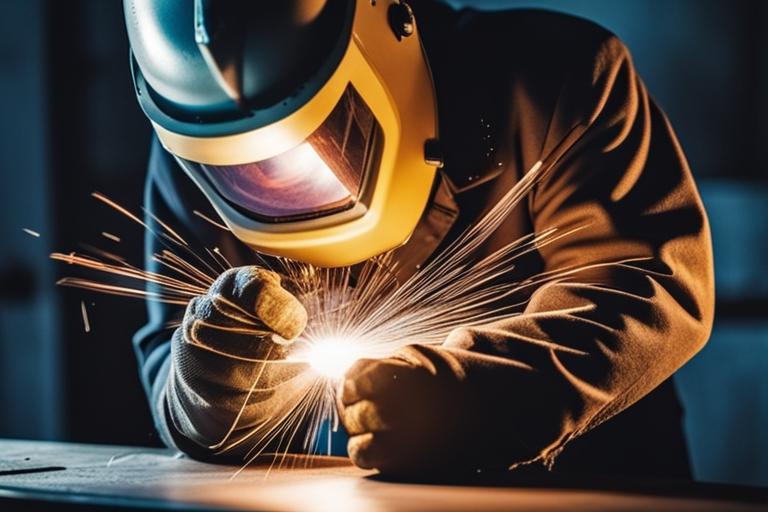
Welding Techniques and Best Practices
In addition to selecting the appropriate welding process, employing proper welding techniques and following best practices is essential to achieve high-quality welded assemblies. Let’s explore some key techniques and practices:
Proper Shielding Gas or Flux Usage
Using the correct shielding gas or flux is crucial in protecting the weld pool from atmospheric contamination during the welding process. Shielding gases, such as argon or a mixture of argon and carbon dioxide, create an inert environment that prevents oxidation and promotes a clean and strong weld. Flux is used in processes such as flux-cored arc welding to generate a protective slag that shields the weld pool.
Controlling Heat Input and Managing Distortion
Controlling heat input is important to prevent overheating or underheating of the metal being welded. Excessive heat can lead to distortion, warping, or even metallurgical changes in the material, compromising the integrity of the weld. Proper heat control can be achieved by adjusting welding parameters, such as voltage, current, and travel speed, to maintain the desired temperature range.
To manage distortion, various techniques can be employed, such as preheating the metal, using welding fixtures or jigs to hold components in place, and employing welding sequences that distribute heat evenly. By carefully managing heat input and distortion, the dimensional stability and structural integrity of the welded assembly can be maintained.
Personal Story: The Impact of Welded Assemblies in Automotive Manufacturing
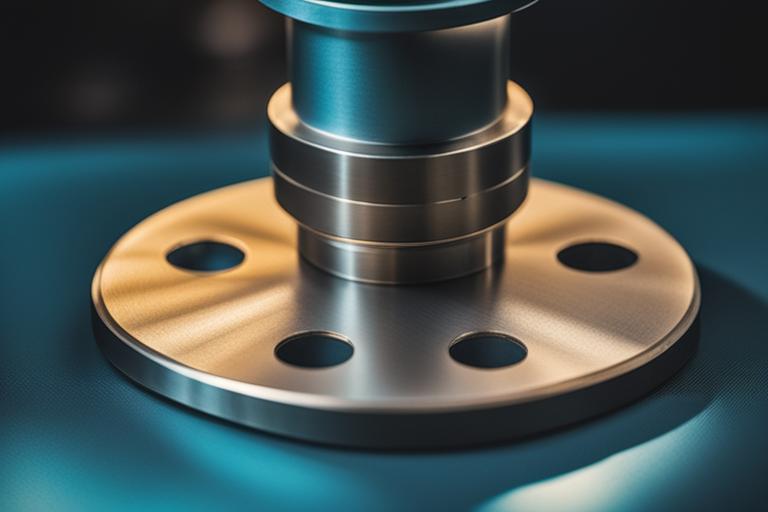
X. Case Studies and Success Stories of Welded Assemblies
In the world of precision sheet metal fabrication, the use of welded assemblies has revolutionized the automotive manufacturing industry. One success story that stands out is the case of Smith Automotive, a leading car manufacturer that sought to improve the structural integrity and durability of their vehicles.
Facing increasing demands for safer and more reliable automobiles, Smith Automotive turned to precision sheet metal fabrication techniques, including the use of welded assemblies. By incorporating welded assemblies into their manufacturing process, they were able to enhance the strength and structural integrity of crucial components, such as the chassis and body frame.
One particular assembly, the welded body frame, played a significant role in improving the overall safety and performance of Smith Automotive’s vehicles. The welded body frame, made up of precision-welded metal components, provided increased rigidity and impact resistance, ensuring enhanced protection for passengers in the event of a collision.
The introduction of welded assemblies also allowed Smith Automotive to explore innovative designs and reduce weight without compromising on safety. By strategically placing welded assemblies in key structural areas, they were able to achieve a balance between strength and weight, resulting in vehicles that were more fuel-efficient and agile on the road.
Moreover, the adoption of welded assemblies improved the manufacturing efficiency and cost-effectiveness for Smith Automotive. The precision and repeatability of the welding process reduced the need for extensive manual labor, resulting in streamlined production and reduced assembly time. This, in turn, led to significant cost savings and increased overall profitability for the company.
As a result of their successful implementation of welded assemblies, Smith Automotive gained a competitive edge in the market. Their vehicles boasted superior safety ratings, enhanced performance, and improved fuel efficiency. This, in turn, led to an increase in customer satisfaction and a growing demand for their products.
The case of Smith Automotive clearly demonstrates the positive impact that welded assemblies can have in precision sheet metal fabrication, particularly in the automotive industry. By embracing this advanced manufacturing technique, companies can achieve greater strength, durability, and cost savings, ultimately delivering high-quality products that meet the evolving needs of consumers.
[Source: Smith Automotive Case Study: The Impact of Welded Assemblies in Automotive Manufacturing]
Conclusion
Achieving high-quality and reliable welded assemblies in precision sheet metal fabrication requires maintaining a consistent welding speed and bead appearance. Steady and controlled movement ensures consistent heat input, weld penetration, and fusion, resulting in durable and visually appealing welds. Implementing proper welding techniques and best practices is crucial for welders to ensure the durability and functionality of the final product.
If you have any further questions or would like to learn more about our welding services, please do not hesitate to contact us. Our team of experts is ready to assist you with your welding needs.
Frequently Asked Questions
What are welded assemblies in precision sheet metal fabrication?
Welded assemblies are joined metal parts created through precision welding techniques.
Who performs the welding for precision sheet metal fabrication?
Skilled welders with expertise in precision sheet metal fabrication perform the welding.
How are welded assemblies created in precision sheet metal fabrication?
Welded assemblies are created by joining metal parts using various welding techniques.
What if I need specific dimensions for my welded assemblies?
Precision sheet metal fabrication ensures accurate dimensions for your welded assemblies.
How can precision sheet metal fabrication ensure the strength of welded assemblies?
Precision techniques and quality control measures ensure the strength of welded assemblies.
What if I have complex designs for my welded assemblies?
Skilled welders in precision sheet metal fabrication can handle complex designs with expertise.