Are you looking to understand everything about sheet metal punching, from its techniques to its importance and future trends? Look no further. This comprehensive guide aims to provide an in-depth understanding of sheet metal punching, including its techniques, significance, and future trends.
What You Will Learn About Sheet Metal Punching
By reading this article, you will learn:
– The process and importance of sheet metal punching in precision sheet metal fabrication.
– The equipment and materials involved in sheet metal punching, including its advantages and quality control measures.
– Techniques, applications, and future trends in sheet metal punching.
Definition and Significance
Sheet metal punching, also known as metal stamping, involves creating holes, forms, or other features on a metal surface using a punch and die. It is a crucial process in the fabrication industry, enabling efficient production of complex components with high precision and accuracy. The versatility of sheet metal punching makes it indispensable for creating a wide range of products, from intricate electronic enclosures to structural components in the automotive and aerospace industries.
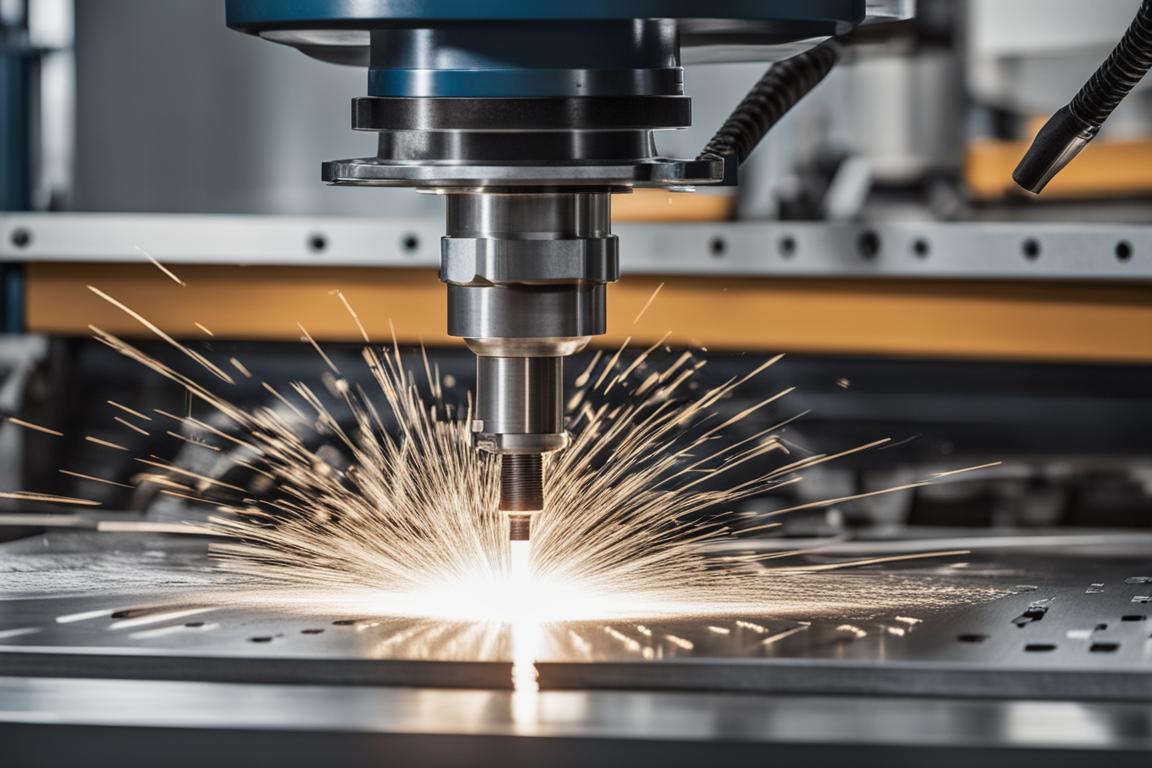
Process of Sheet Metal Punching
The process entails placing a flat metal sheet on a die with a hole that matches the desired feature’s shape and size. A punch rapidly descends and penetrates the material, creating the desired hole or form, with the punched material shearing away and falling through the die. This method is suitable for various materials, including steel, aluminum, and stainless steel, making it a versatile solution for different fabrication needs.
Importance in Precision Sheet Metal Fabrication
In precision sheet metal fabrication, every step contributes to the final product’s quality. Sheet metal punching’s ability to create precise features with minimal material waste makes it a preferred method for achieving intricate designs and functional components. Its importance becomes evident in the production of items such as brackets, chassis, and electronic enclosures, where accuracy and repeatability are crucial.
Understanding Sheet Metal Punching
Equipment and Machinery for Sheet Metal Punching
Types of Machinery: CNC Punch Presses and Turret Punch Presses
Specialized machinery, including CNC punch presses and turret punch presses, are commonly used for sheet metal punching. These machines can handle a wide range of materials and thicknesses, offering precise control and flexibility in creating punched features.
Precision and Accuracy in Equipment
Modern punch presses utilize advanced CNC technology to ensure high precision and accuracy in the punching process. They can achieve tight tolerances and intricate designs, meeting the demanding requirements of various industries.
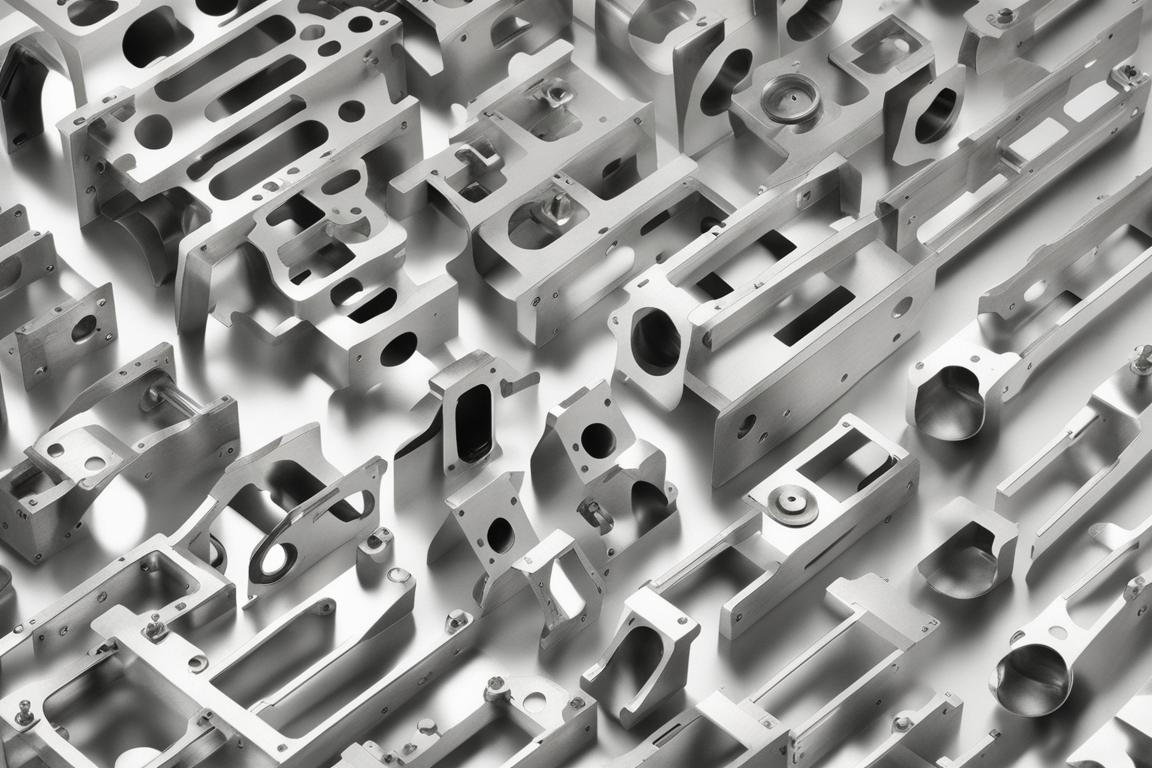
Achieving High-Quality Punched Parts
The combination of precision equipment and skilled operators results in high-quality punched parts that meet the stringent standards of precision sheet metal fabrication. This ensures that the punched components align perfectly with the design specifications, contributing to the overall quality of the fabricated product.
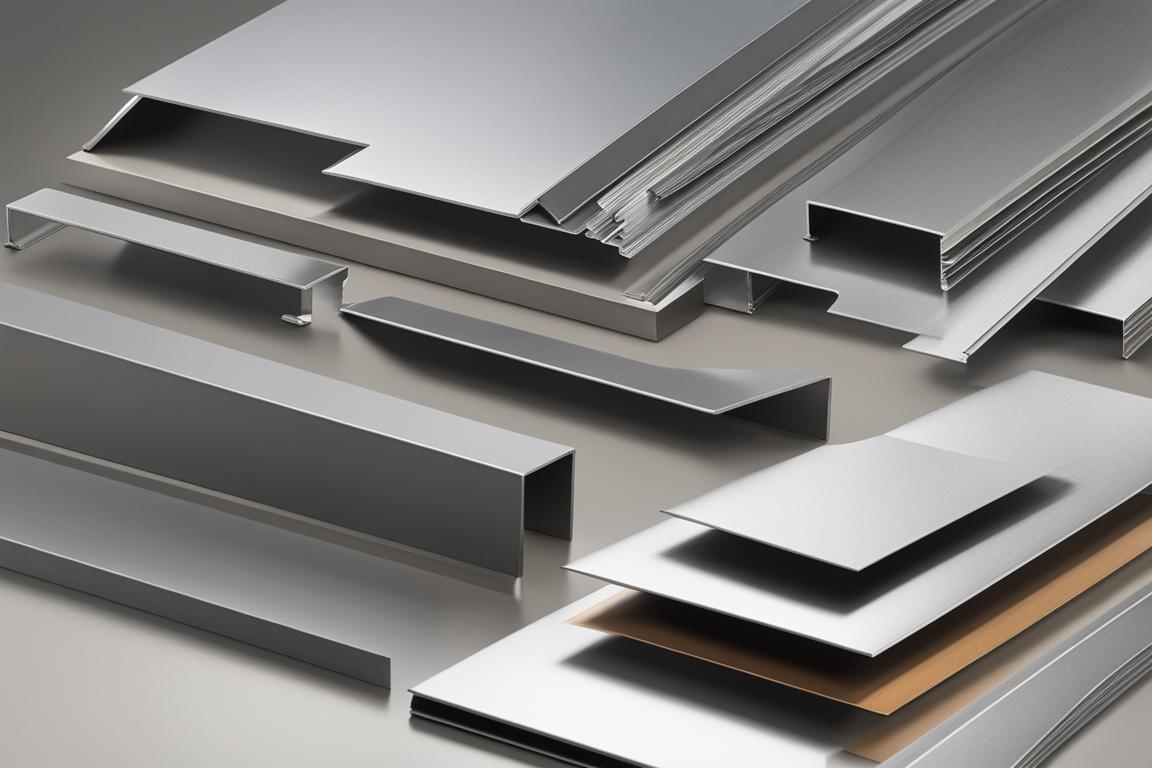
Materials and Thickness in Sheet Metal Punching
Range of Materials: Steel, Aluminum, Stainless Steel
Sheet metal punching can be applied to a diverse range of materials, including steel, aluminum, and stainless steel, allowing fabricators to work with different materials based on specific product requirements.
Limitations and Capabilities
While sheet metal punching offers great versatility, understanding the material’s behavior during punching, especially in terms of ductility and hardness, is crucial for achieving optimal results.
Types of Features Created
Sheet metal punching can create a variety of features, including holes, louvers, and formed shapes, expanding its applicability across a wide spectrum of industries and applications.
Advantages of Sheet Metal Punching
Pros | Cons |
---|---|
Cost-effective in high-volume production | Not suitable for very large or complex shapes |
Rapid production rates | Limited flexibility for rapid design changes |
Ability to create complex shapes | Initial tooling costs can be high |
Quality Control Measures | Inspection Techniques |
---|---|
Dimensional checks | Visual inspection |
Surface quality assessment | Coordinate measuring machine |
Material thickness verification | Optical profilometer |
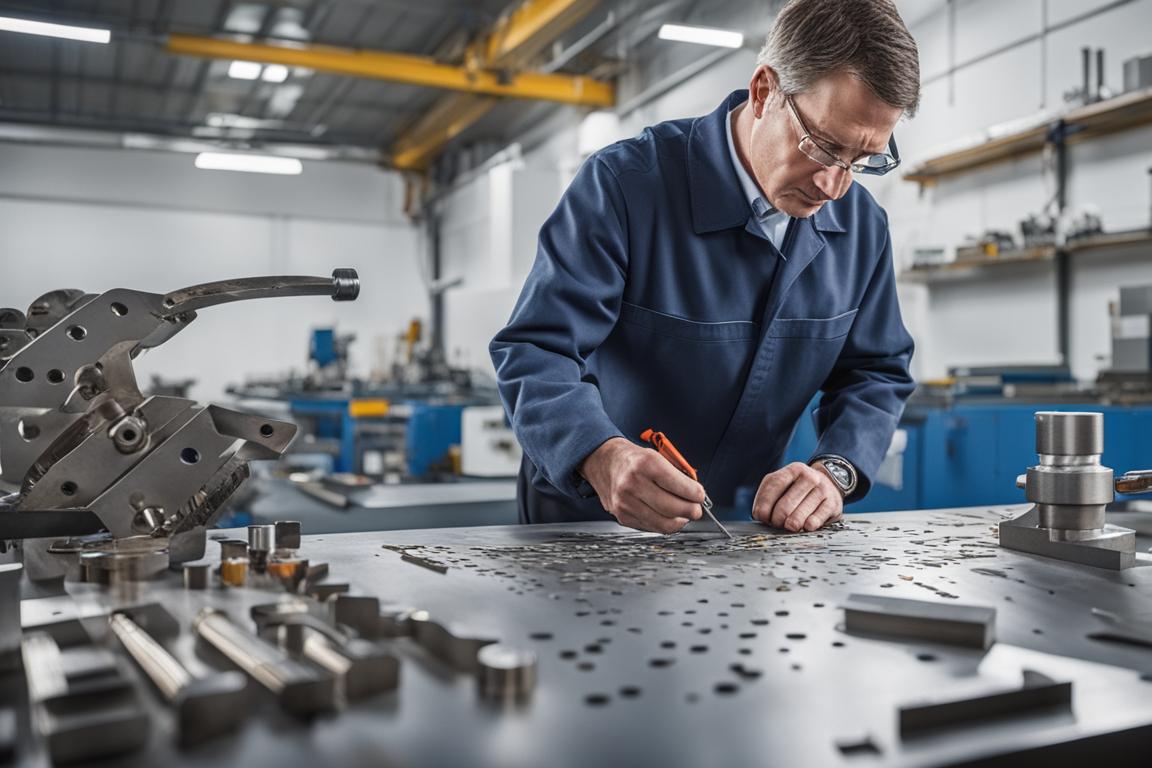
Quality Control and Inspection in Sheet Metal Punching
Implementing stringent quality control measures and regular inspections throughout the punching process is essential to maintain consistency and reliability. Rigorous inspection processes verify that punched features adhere to specified tolerances, guaranteeing a precise fit and functionality.
Including real-life examples or case studies of precision sheet metal punching projects would add depth to the content and provide practical insights. Providing information about the author’s background or credentials in the field of precision sheet metal punching would enhance the expertise aspect of the content.
This guide provides a comprehensive overview of precision sheet metal punching, emphasizing its significance, techniques, and quality control measures. Understanding the process and its advantages is crucial for achieving high-quality, precise components in metal fabrication.
Frequently Asked Questions
Question: Who uses sheet metal punching in precision sheet metal fabrication?
Answer: Precision sheet metal fabricators use punching to create precise holes and shapes in sheet metal.
Question: What is sheet metal punching in precision sheet metal fabrication?
Answer: Sheet metal punching is the process of using a punch and die to create holes and shapes in sheet metal with high precision.
Question: How does sheet metal punching differ from other fabrication methods?
Answer: Sheet metal punching is a fast and cost-effective method for creating precise holes and shapes in sheet metal compared to laser cutting or drilling.
Question: What are the advantages of sheet metal punching over other methods?
Answer: Sheet metal punching offers high production speeds, low tooling costs, and excellent precision in creating complex hole patterns.
Question: How to ensure accurate results in sheet metal punching?
Answer: To ensure accuracy, fabricators use advanced CNC machines and carefully designed tooling for consistent and precise sheet metal punching.
Question: Isn’t sheet metal punching limited in the types of shapes it can produce?
Answer: While historically limited, modern sheet metal punching machines can produce a wide range of complex shapes and patterns with high precision.