What You’ll Learn About Sheet Metal Punching
- Definition, purpose, and importance of sheet metal punching in precision fabrication.
- Types of sheet metal punching processes, materials used, equipment, precision and tolerance, design considerations, quality control, industry applications, advancements, best practices, case studies, and future trends.
- Comprehensive exploration addressing informational search intent and related questions in precision sheet metal fabrication.
Sheet metal punching is a fundamental process in precision sheet metal fabrication, revolutionizing the manufacturing of intricate and accurate components. This article will provide an in-depth overview of sheet metal punching, covering techniques, materials, equipment, design considerations, quality control, industry applications, advancements, best practices, case studies, and future trends. By delving into these aspects, we aim to cater to the informational search intent while addressing related questions and interests in precision sheet metal fabrication.
Definition and Purpose of Sheet Metal Punching
Sheet metal punching involves the use of a punch and die to create holes, forms, or other features in sheet metal. This process is essential for producing components with intricate designs and high accuracy, making it indispensable in various industries.
Importance in Precision Sheet Metal Fabrication
Precision sheet metal fabrication demands accuracy and consistency in creating components. Sheet metal punching is a key process that enables manufacturers to achieve the required precision while maintaining efficiency.
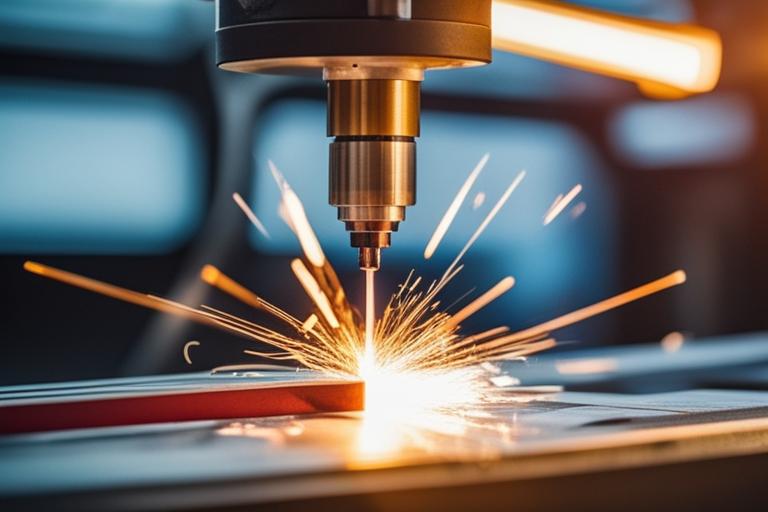
Types of Sheet Metal Punching Processes
Sheet metal punching encompasses various techniques, each offering distinct advantages and considerations.
Turret Punching
Turret punching involves a turret press with multiple punch and die combinations, allowing for rapid tool changes and increased efficiency.
Laser Punching
Laser punching integrates laser cutting and punching capabilities, enabling the creation of complex features with high precision.
CNC Punching
CNC punching utilizes computer numerical control (CNC) technology to automate the punching process, ensuring consistent and accurate component production.
Comparison of Techniques and Methods
Each punching technique has its unique strengths and limitations, influencing factors such as speed, material compatibility, feature complexity, and cost-effectiveness.
Advantages and Disadvantages
The choice of punching technique depends on specific project requirements, considering factors such as material type, component complexity, production volume, and desired precision.
Materials Used in Sheet Metal Punching
The choice of material significantly impacts the sheet metal punching process and the characteristics of the fabricated components.
Aluminum
Aluminum is a lightweight and corrosion-resistant material commonly used in various industries, offering favorable machinability and formability for sheet metal punching applications.
Stainless Steel
Stainless steel exhibits exceptional durability and corrosion resistance, making it suitable for applications requiring robust components produced through precise punching processes.
Carbon Steel
Carbon steel is known for its strength and affordability, often utilized in sheet metal punching for industrial and structural applications, demanding high mechanical properties.
Considerations for Material Selection
The selection of materials for sheet metal punching involves evaluating properties such as ductility, hardness, strength, and corrosion resistance, aligning with the specific performance requirements of the fabricated components.
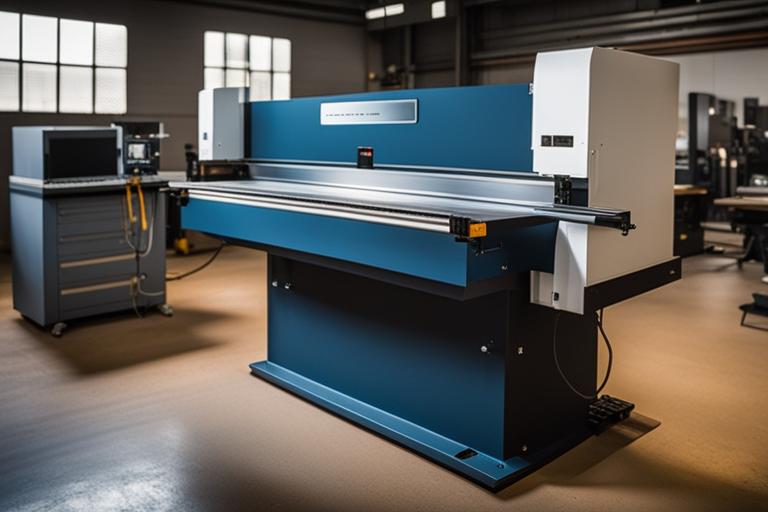
Equipment and Tools for Sheet Metal Punching
Efficient sheet metal punching relies on specialized machinery and tools designed for precision and reliability.
Machinery Overview
Punching machinery encompasses turret presses, laser-punch combination machines, and CNC punching equipment, each tailored to accommodate diverse production needs.
Press Brakes
Press brakes complement sheet metal punching processes by enabling precise bending and forming of punched components, contributing to the overall fabrication workflow.
Punch Presses
Punch presses are essential for executing the punching operation, leveraging the force and precision required to create intricate features with exceptional accuracy.
Dies and Other Essential Tools
Dies, punches, and tooling play a critical role in determining the form and dimensions of punched features, necessitating the use of high-quality tooling to ensure consistency and repeatability in the punching process.
Precision and Tolerance in Sheet Metal Punching
The pursuit of precision and tolerance is central to the quality of fabricated parts, underpinning their functionality and performance.
Importance in Fabricated Parts Quality
Sheet metal punching directly influences the dimensional accuracy and feature integrity of fabricated components, impacting their fit, assembly, and overall functionality.
Impact on Design and Applications
Designing for precise sheet metal punching involves considerations such as feature tolerances, material behavior, and tooling capabilities, shaping the manufacturability and performance of the final components.
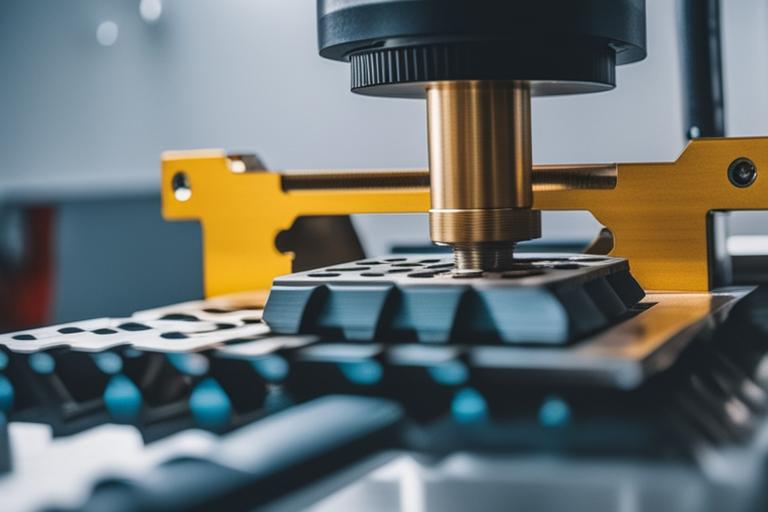
Design Considerations for Sheet Metal Punching
Designing for sheet metal punching entails strategic planning to optimize component manufacturability and performance.
Hole Size, Shape, and Layout
Careful consideration of hole dimensions, shapes, and arrangement is essential to ensure efficient punching operations and the functionality of the fabricated components.
Design Consideration | Description |
---|---|
Hole Size | Careful consideration of the diameter of holes to ensure compatibility with tooling and component functionality. |
Hole Shape | Evaluation of the shape of holes to optimize punching operations and component performance. |
Hole Layout | Strategic arrangement of holes to enhance punching efficiency and align with assembly requirements. |
Quality Control and Inspection in Sheet Metal Punching
Stringent quality control measures are imperative to uphold the integrity and precision of punched components.
Measures During and After Punching
In-process inspections and post-punching evaluations are conducted to verify dimensional accuracy, feature integrity, and material conformity, ensuring compliance with design specifications.
Ensuring Integrity of Fabricated Parts
Quality control procedures encompass material verification, feature validation, and adherence to dimensional tolerances, guaranteeing the reliability and performance of punched components.
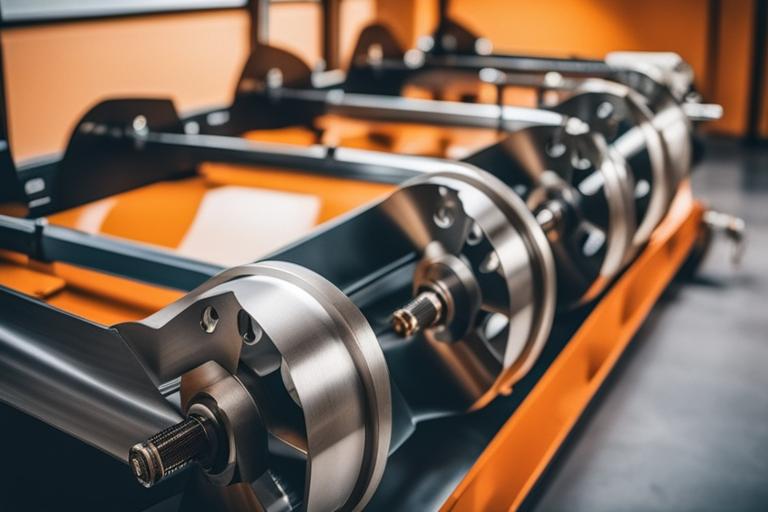
Applications and Industries of Sheet Metal Punching
Sheet metal punching finds extensive application across diverse industries, contributing to the production of critical components for various sectors.
Automotive
The automotive industry relies on sheet metal punching for producing precision parts used in vehicles, encompassing body panels, chassis components, and structural elements.
Aerospace
Aerospace applications demand high-precision components, driving the utilization of sheet metal punching for manufacturing intricate parts used in aircraft structures and systems.
Electronics
Electronics manufacturing leverages sheet metal punching to create housings, enclosures, and mounting structures for electronic devices, catering to the industry’s stringent dimensional and aesthetic requirements.
Versatility and Relevance in Various Industries
Beyond these sectors, sheet metal punching serves a wide array of applications, including furniture production, machinery fabrication, and architectural components, showcasing its versatility and relevance across industries.
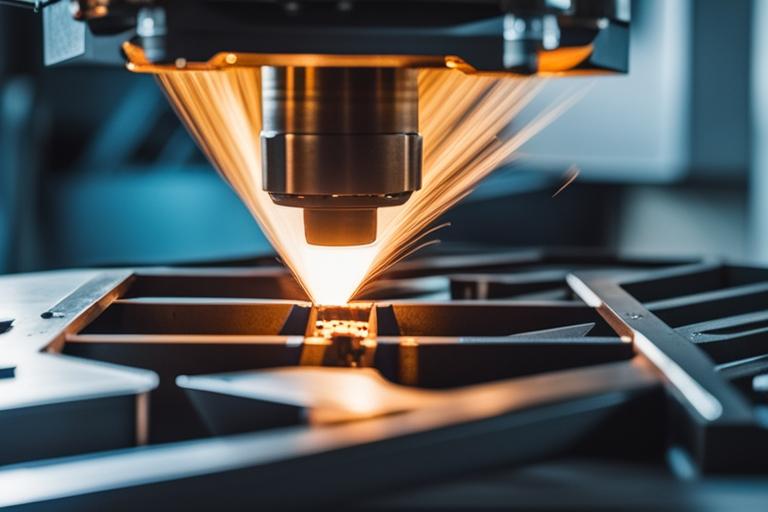
Advancements and Innovations in Sheet Metal Punching
The evolution of sheet metal punching is characterized by technological advancements and innovative practices that enhance efficiency and precision.
Automation in Punching Processes
Automated punching systems integrate robotics and advanced control systems to streamline production, reduce cycle times, and enhance process reliability, meeting the demands of modern manufacturing.
Software Integration for Enhanced Precision
Software solutions facilitate the optimization of tool paths, nesting strategies, and material utilization, elevating the precision and efficiency of sheet metal punching operations.
Industry 4.0 Initiatives and Impact
Industry 4.0 principles, encompassing connectivity, data-driven insights, and smart manufacturing, are driving transformative changes in sheet metal punching, fostering agile and responsive fabrication workflows.
Best Practices and Tips for Sheet Metal Punching
Adhering to best practices and safety guidelines is essential for achieving optimal results in sheet metal punching operations.
Tool Maintenance
Regular maintenance and inspection of punching tools and machinery are crucial to sustaining their performance and longevity, ensuring consistent and reliable punching outcomes.
Material Handling and Safety
Safe handling of sheet metal and adherence to material-specific guidelines are vital for mitigating risks and maintaining a secure working environment during punching operations.
Efficient Production Workflows
Streamlining production workflows, optimizing tooling setups, and embracing lean manufacturing principles contribute to enhanced efficiency and productivity in sheet metal punching processes.
Case Studies and Success Stories in Sheet Metal Punching
Real-world examples demonstrate the impact and potential of sheet metal punching in driving successful fabrication outcomes.
Real-World Examples of Successful Applications
Illustrative case studies showcase the diverse applications of sheet metal punching, highlighting its role in realizing complex designs and meeting stringent industry standards.
Impact on Precision Sheet Metal Fabrication
The success stories underscore the pivotal role of sheet metal punching in achieving precision, reliability, and cost-effective production of fabricated components.
Future Outlook of Sheet Metal Punching
Anticipating future trends and developments is essential for aligning with the evolving landscape of sheet metal punching.
Emerging Technologies
Advancements in machine learning, additive manufacturing, and material science are poised to revolutionize sheet metal punching, unlocking new possibilities for precision fabrication.
Sustainability Initiatives in Metal Fabrication
The industry’s focus on sustainable practices and environmental responsibility is driving the adoption of eco-friendly materials, energy-efficient processes, and waste reduction strategies in sheet metal punching.
By incorporating real-world experiences and industry standards, this article aims to provide a comprehensive and authoritative resource on precision sheet metal punching, catering to the informational needs of professionals and enthusiasts in the field.
Questions
Q. What is sheet metal punching?
A. Sheet metal punching is a process that uses a punch and die to create holes or shapes in sheet metal.
Q. Who uses sheet metal punching?
A. Manufacturers and fabricators in various industries use sheet metal punching for creating precise holes and shapes in metal sheets.
Q. How does sheet metal punching work?
A. Sheet metal punching works by placing the metal sheet on a die and using a punch to apply force and create the desired hole or shape.
Q. What are the benefits of sheet metal punching?
A. Sheet metal punching is cost-effective, produces precise results, and allows for high production rates.
Q. How precise is sheet metal punching?
A. Sheet metal punching is highly precise, with the ability to create accurate holes and shapes within tight tolerances.
Q. What if I need complex shapes in my sheet metal?
A. For complex shapes, techniques like laser cutting or waterjet cutting may be more suitable, depending on the specific requirements.