In response to critical challenges within our sheet metal manufacturing processes, we at Atlas Manufacturing identified the need for heightened organization and efficiency. This realization prompted a strategic shift from “Hidden” Lean to “Visual” Lean, symbolizing our journey toward a workspace that prioritizes visual management.
Expanding on the concepts introduced in the second part of our series, where we focused on the integration of a custom library tool tree, this third installment now delves into the implementation of tooling shadow boards. In this segment, we address immediate concerns surrounding tool identification and explore the impact of tooling shadow boards on our efficiency, safety, and quality standards.
The Foundation: Set in Order and Shine in 5S
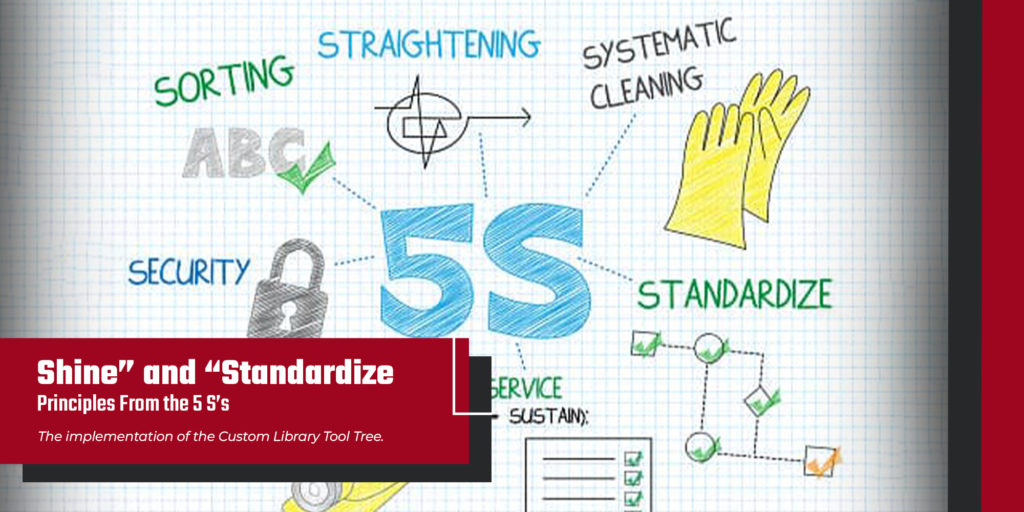
In the context of the 5S methodology, Set in order and Shine play pivotal roles in achieving a visually organized and efficient workspace.
Understanding 5S
Before delving into the specific applications of Set in order and Shine, let’s take a moment to review the broader framework within which these principles operate — the 5S methodology.
5S is a systematic and structured approach to workplace organization first implemented in the Toyota Production System. This Lean thinking concept is derived from five Japanese words: Seiri (Sort), Seiton (Set in order), Seiso (Shine), Seiketsu (Standardize), and Shitsuke (Sustain). Each ‘S’ represents a fundamental principle to optimize efficiency, safety, and quality within the workspace. The methodology serves as a foundation for Lean Manufacturing, emphasizing the creation of an organized and visually oriented environment.
Set in Order
A well-organized workspace is not just desirable in the manufacturing industry; it is indispensable for optimal operational efficiency. The Set in Order principle revolves around the strategic arrangement of tools and materials, creating a layout that facilitates easy identification and access. This scientific management is vital, as it helps eliminate waste of time on tool searches, reduces the risk of errors in tool selection, and optimizes manufacturing resource planning.
At Atlas Manufacturing, we wholeheartedly embrace this principle and recognize that an organized workplace is inherently more productive. By implementing Set in order, we have laid the groundwork for a seamless workflow of a Lean production system.
Shine
The Shine aspect of the 5S methodology places a spotlight on cleanliness and orderliness within the workplace in Lean manufacturing plants. A clean and well-maintained environment goes beyond aesthetics; it ensures that issues are promptly identified, contributing to a safer and more efficient workspace. When harmoniously combined with Set in order, the Shine principle becomes a catalyst for creating a visually oriented Lean environment — precisely what we aspire to achieve at Atlas Manufacturing.
The emphasis on cleanliness not only promotes a more organized workspace but also aligns seamlessly with our overarching goal of cultivating an environment where visual cues enhance efficiency and safety. In essence, Shine contributes significantly to the overall visual cleanliness of the workspace, fostering a culture of excellence at Atlas Manufacturing.
Tooling Shadow Boards: A Visual Revolution at Workstations

In pursuing a Visual Lean environment, Atlas Manufacturing has introduced tooling shadow boards at various workstations. What exactly are tooling shadow boards?
A tool shadow board is a specifically designated and visually marked space where tools find their arrangement in precise shapes and orders that mimic their shadows or outlines. These boards serve as instant references for our operators, providing a visual guide to promptly identify each tool’s location and status. By seamlessly integrating tooling shadow boards into our workspace at Atlas, we have taken a substantial stride toward bolstering efficiency, safety, and quality within our production process.
The Impact on Atlas Manufacturing
Let’s take a look at how the implementation of tooling shadow boards has impacted our commitment to Lean and continuous improvement:
Quick Identification of Tool Location and Usage Status
Among the primary advantages offered by tooling shadow boards is the immediate identification of tool location and usage status. Through a standardized arrangement, our operators can swiftly confirm the availability of each tool with a single glance. This not only reduces the time spent in futile searches but also minimizes the risk of selecting unnecessary tools for a specific task, thereby enhancing precision and reducing errors.
Simplifying Tool Management
Tooling shadow boards streamline tool management by establishing a clear and standardized system for organizing tools. Each tool occupies a designated spot, and the shadows or outlines guide operators in ensuring that each device is returned to its proper place after use. This meticulous approach minimizes the chances of tools being misplaced and contributes to cultivating a cleaner and more organized workspace, aligning with the standard Lean production model.
Reducing Time in Tool Retrieval
Perhaps the most noticeable improvement in productivity brought about by tooling shadow boards is the drastic cut in the time needed to retrieve tools. With the integration of tooling shadow boards, operators can swiftly locate the required tools without prolonged searches. This streamlined process accelerates the manufacturing workflow and fosters a smoother operational rhythm, ultimately eliminating waste and elevating overall productivity levels within Atlas Manufacturing.
A Continued Commitment to Lean Principles

Tooling shadow boards are a powerful tool in the Lean manufacturing arsenal. By focusing on Set in order and Shine, Atlas Manufacturing has not only improved its tool management but has also created a workspace where efficiency, safety, and quality are prioritized. Stay tuned for the final installment in our series, where we explore other workspace improvements and Lean methods that solidify our position as a champion of Lean Manufacturing principles.