The Lean production system has revolutionized production processes for various industries, and we at Atlas Manufacturing use it to maintain our commitment to continuous improvement. We are dedicated to efficiency, safety, and productivity within our operations.
In our ongoing series spotlighting our evolution from “Hidden” Lean to “Visual” Lean, we delve into pivotal improvements that define our commitment to Lean principles. Here, we explore the second chapter of our journey — the adoption of the Custom Library Tool Tree — a critical leap toward a visually oriented Lean environment, underscored by the principles of 5S methodology.
Emphasizing “Shine” and “Standardize” Principles From the 5 S’s

The implementation of the Custom Library Tool Tree at Atlas Manufacturing isn’t just a shift in tool organization; it’s a reflection of our commitment to Lean principles, particularly the “Shine” and “Standardize” elements of the methodology.
At a glance, the custom library tool tree embodies the essence of “Shine” and “Standardize,” integrating these principles seamlessly into our workspace. Its implementation aligns with Lean’s emphasis on cleanliness, visibility, and standardization.
As our tools find a new, visible home on the Tree, they not only become easily accessible but also undergo continuous scrutiny, ensuring a workspace that thrives on efficiency, safety, and continual improvement. Here is a closer look at each relevant principle.
Relevance of Shine (Seiso)
As we embrace the Custom Library Tool Tree, “Shine” becomes integral. Regular cleaning and vigilant inspection are heightened by the visible display and accessible nature of the Tool Tree. With tools readily visible and organized, our teams can maintain a meticulously clean environment effortlessly.
This immediate visibility not only promotes cleanliness but also enables quicker identification of any issues or irregularities in our tool inventory. The Tool Tree’s open design fosters a workspace where tools are not just organized but also maintained at optimal conditions, aligning perfectly with the “Shine” principle.
Influence of Standardize (Seiketsu)
The Standardize principle comes to life with the Custom Library Tool Tree’s implementation. This innovative system isn’t just a one-time change; it’s a standardized approach to tool organization. By establishing this visible and accessible tool organization system, we integrate schedules, procedures, and responsibilities to maintain the new organizational layout.
Every tool’s designated place on the Tree becomes a part of our daily routine, ensuring that the benefits of this system are perpetually realized. This standardization doesn’t merely stop at implementation; it becomes an ingrained part of our work culture, contributing to the sustainability of our Lean transformation.
The Previous System: Punch Tools in Labeled Cabinet Drawers
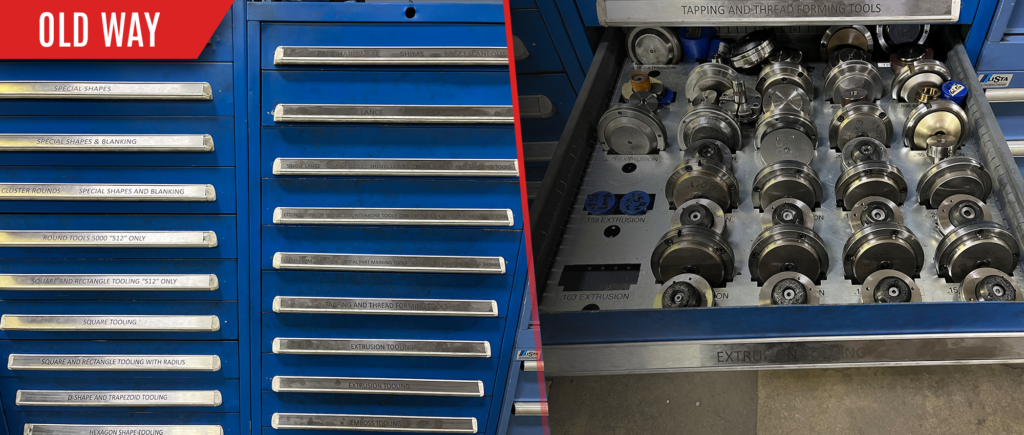
Our previous tool storage system, like other lean manufacturing plants in the industry, comprised of labeled cabinet drawers for punch tools, presented challenges despite its apparent organization. While visually tidy, this setup hindered operational efficiency by concealing tools, leading to prolonged search times and disrupting workflow.
The obscured storage not only impeded productivity but also raised safety concerns due to potential mishandling during hurried searches. Additionally, the lack of immediate visibility into tool availability and usage patterns clashed with our aspirations for lean methods that promoted an efficient, well-informed production process.
Recognizing the limitations of the standard lean production model prompted our transition to the Custom Library Tool Tree. This pivotal shift addressed inefficiencies and emphasized our commitment to Lean principles.
Introduction of the Visible Library Tool Tree System
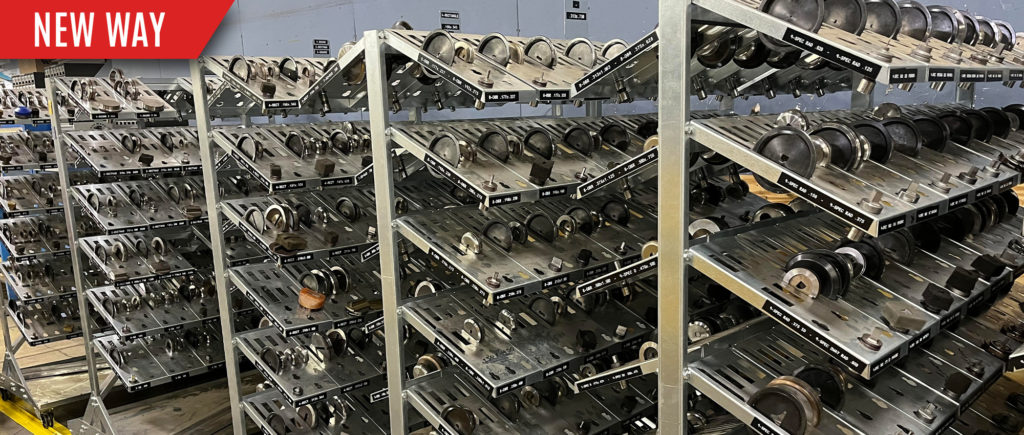
The adoption of the visually striking Custom Library Tool Tree marked a pivotal departure from conventional tool storage. This innovative system brought immediate visibility and accessibility to our tools, contrasting with the previously concealed drawers.
With every tool now openly displayed and easily identifiable, the Tool Tree’s design streamlined access, offering a visual cue for tool availability and usage. This transformation aligned seamlessly with our pursuit of Lean thinking and efforts to improve quality, emphasizing the efficiency of productive processes and promoting visual organization.
Advantages
Implementing lean manufacturing with the Custom Library Tool Tree immediately transformed our workspace:
Immediate Visibility: Streamlining Access
Its design ensured instant visibility of tools, drastically reducing search times and enhancing access. This shift minimized disruptions in workflow, fostering a more efficient operational environment.
Indication of Tool Usage: Accountability and Workflow Efficiency
Beyond visibility, the Tool Tree provided a visual cue for tool usage. This feature promoted accountability among teams and facilitated better coordination. Clear indications of tools in use or available for deployment minimized delays, optimizing workflow efficiency.
Enhanced Operational Efficiency: Optimized Productivity
The seamless integration of the Custom Library Tool Tree translated into enhanced operational efficiency. Tasks progressed smoothly with readily available tools, fostering a more productive and organized work environment. This systematic approach aligned seamlessly with Lean principles, exemplifying our commitment to efficiency and waste reduction.
Conclusion: A Commitment to the Lean Production System and Continuous Improvement
The implementation of the Custom Library Tool Tree stands as a testament to our dedication to proper Lean management and ongoing improvement. This transformation embodies our pledge to efficiency and safety, reinforcing our commitment to refining our practices and fostering a culture of continuous enhancement.
At Atlas Manufacturing, this transition marks a milestone in our pursuit of a visually Lean workspace. Join us on this transformative journey as we continually strive to shape an environment that embodies efficiency, safety, and innovation.