Are you looking to understand the intricacies of OEM sheet metal fabrication, from its definition to practical application? This comprehensive guide explores the world of precision OEM sheet metal fabrication and uncovers its significance in the manufacturing industry, providing insights into its practical application through real-life examples and case studies.
What You’ll Learn About OEM Sheet Metal Fabrication
You’ll learn about precision OEM sheet metal fabrication, including processes like laser cutting, CNC punching, welding, and forming, and commonly used materials like stainless steel, aluminum, and titanium.
– Precision OEM sheet metal fabrication processes.
– Commonly used materials in OEM sheet metal fabrication.
– Importance of choosing the right fabrication partner.
OEM sheet metal fabrication refers to the process of creating custom sheet metal components and assemblies for Original Equipment Manufacturers (OEMs). These components are specifically designed and manufactured to meet the unique requirements of OEMs, ensuring a precise fit and optimal performance within their end products. This specialized form of fabrication demands a high degree of precision, as the components often serve as integral parts of larger machinery, equipment, or consumer products.
Importance of OEM Sheet Metal Fabrication in Manufacturing
OEM sheet metal fabrication is crucial as OEMs rely on these specialized fabrication services to produce components that align with their exact specifications and quality standards. Whether it’s for automotive, aerospace, electronics, or other industries, precision sheet metal fabrication ensures that OEMs can deliver products that meet stringent performance and safety requirements.
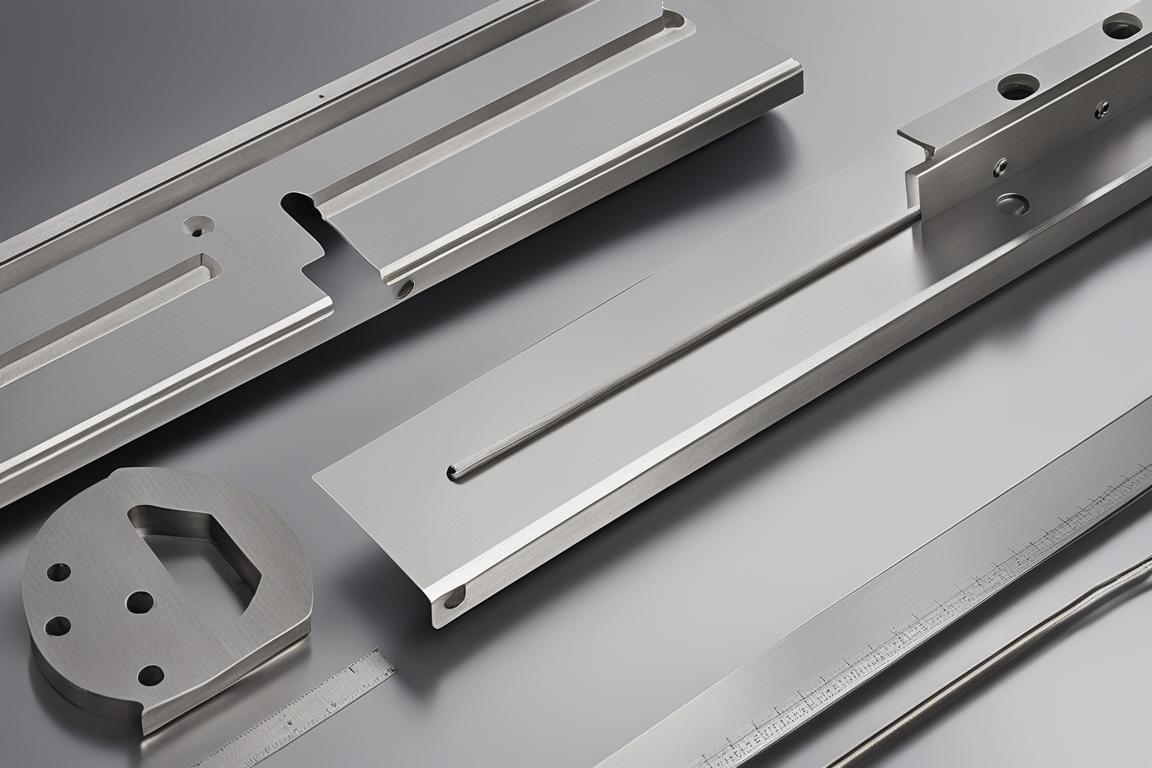
Understanding Precision Sheet Metal Fabrication
Precision sheet metal fabrication involves a series of intricate processes and techniques aimed at creating high-quality custom components. Let’s take a closer look at the nuances of this specialized manufacturing approach, with practical examples and case studies highlighting its application.
Overview of Precision Sheet Metal Fabrication
Precision sheet metal fabrication encompasses the manufacturing of intricate parts and components from various sheet metal materials. This process demands meticulous attention to detail and a deep understanding of material properties and fabrication techniques to achieve the desired specifications.
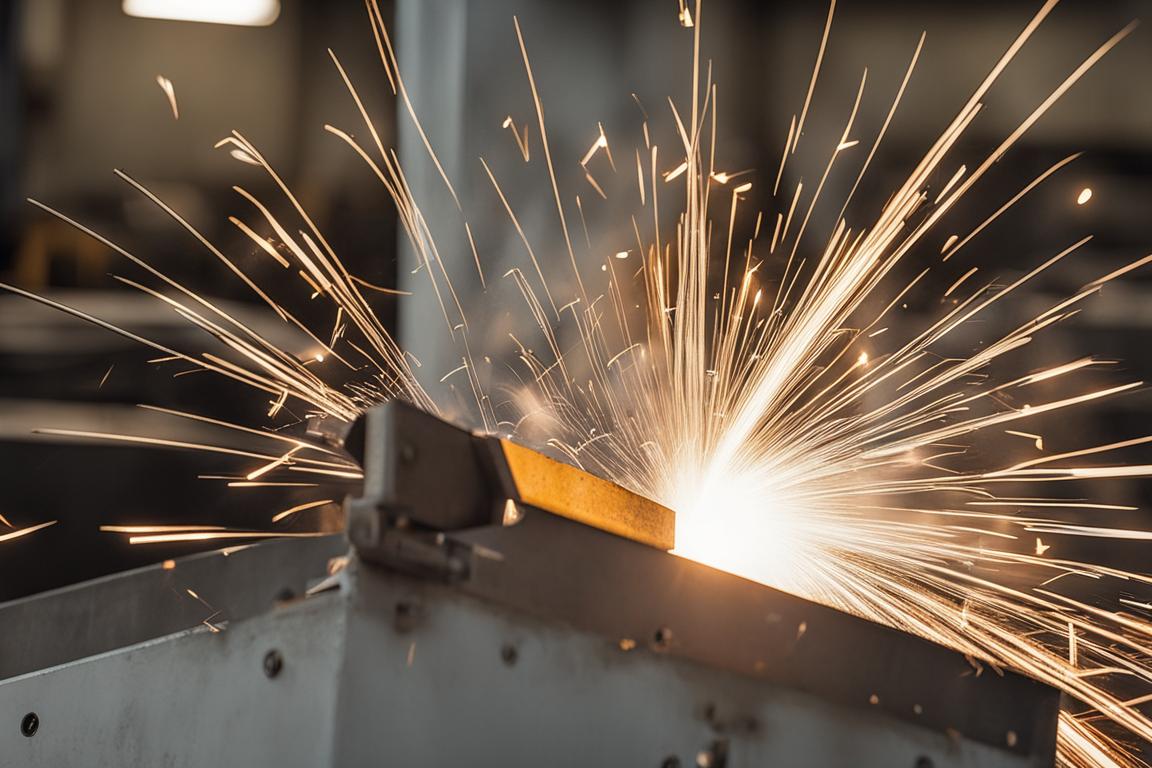
Processes and Techniques in OEM Sheet Metal Fabrication
Laser Cutting
Laser cutting is a key process in precision sheet metal fabrication, offering exceptional accuracy and the ability to cut intricate shapes from different types of sheet metal. For instance, in the aerospace industry, laser-cut sheet metal components are vital for lightweight structures in aircraft.
CNC Punching
Computer Numerical Control (CNC) punching enables the creation of precise perforations, patterns, and forms in sheet metal, allowing for the production of complex and customized components. An example is the production of custom enclosures for electronic devices, where CNC punching ensures precise cutouts for connectors and interfaces.
Welding
Welding plays a crucial role in joining metal parts to create assemblies, ensuring structural integrity and durability in the finished products. A case study demonstrating the use of welding in fabricating structural components for heavy machinery would provide a practical example.
Forming
Forming processes such as bending, folding, and deep drawing are used to shape sheet metal into the desired configurations, meeting the specific dimensional and structural requirements of OEMs. An example could be the production of custom brackets for automotive applications, showcasing the use of forming techniques to meet precise dimensional specifications.
Material | Characteristics | Applications |
---|---|---|
Stainless Steel | Corrosion resistance, strength, polished finish | Medical equipment components, food processing equipment |
Aluminum | Lightweight, robust, strength, weight-saving | Aerospace components, automotive parts, consumer electronics |
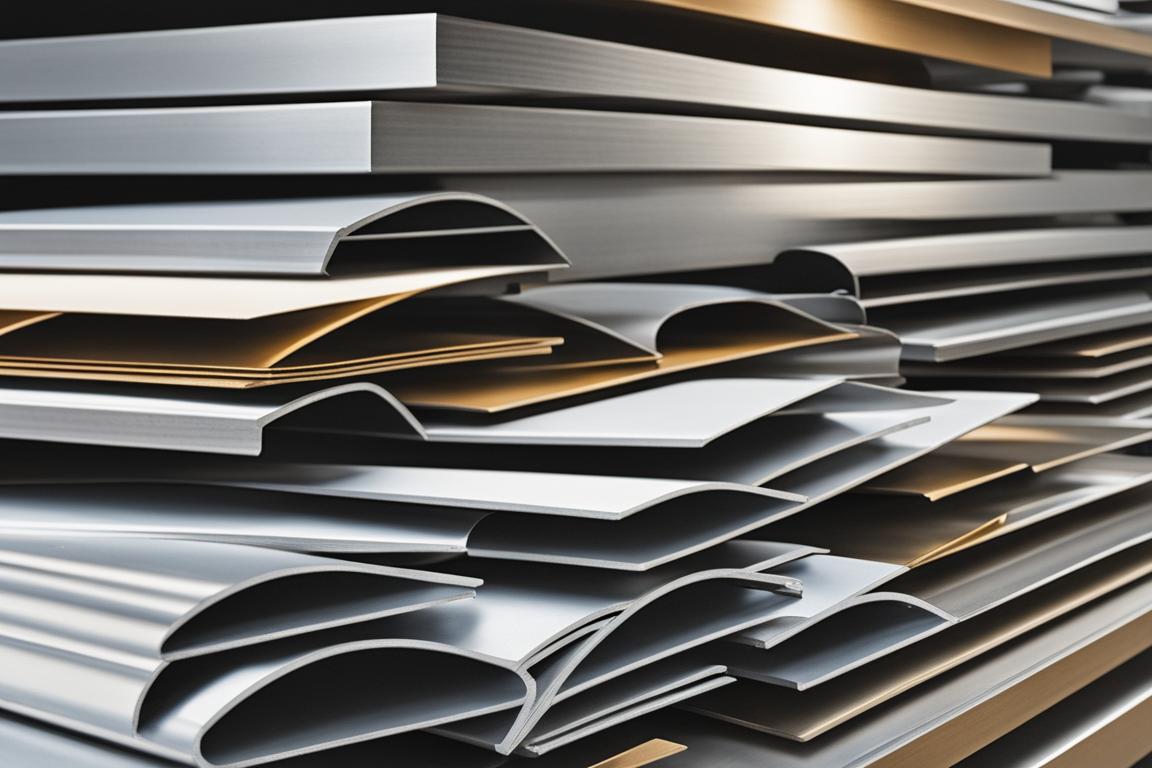
Commonly Used Materials in OEM Sheet Metal Fabrication
Precision OEM sheet metal fabrication utilizes a variety of materials to meet diverse industry needs. Some of the most commonly used materials include:
- Stainless Steel: Favored for its corrosion resistance and strength, making it an ideal choice for applications requiring durability and a polished finish. For example, the fabrication of medical equipment components often utilizes stainless steel for its hygienic properties and longevity.
- Aluminum: Aluminum’s lightweight yet robust nature makes it a popular material for fabricating components in aerospace, automotive, and consumer electronics industries. An example could be the production of lightweight components for electric vehicles, where aluminum’s strength and weight-saving properties are crucial.
By understanding the intricacies of precision OEM sheet metal fabrication and its practical applications, manufacturers can make informed decisions when selecting fabrication partners and optimizing their component production processes.
Questions
Q: Who provides OEM sheet metal fabrication services?
A: OEM sheet metal fabrication services are provided by specialized manufacturers.
Q: What is precision sheet metal fabrication?
A: Precision sheet metal fabrication is the process of creating metal parts with high accuracy and quality.
Q: How is OEM sheet metal fabrication different from standard fabrication?
A: OEM sheet metal fabrication is tailored to specific equipment or products, ensuring precise fit and function.
Q: What are the advantages of precision sheet metal fabrication?
A: Precision sheet metal fabrication ensures high-quality, custom parts for specialized applications.
Q: How can I ensure the quality of OEM sheet metal fabrication?
A: You can ensure quality by choosing a manufacturer with proven expertise and a strong track record.
Q: What if I need customization for my OEM sheet metal parts?
A: Many OEM sheet metal fabrication services offer customization options to meet specific requirements.