What the reader will learn by reading the article:
- The definition and significance of OEM sheet metal fabrication.
- The role of precision in sheet metal fabrication and the advantages of precision fabrication over traditional methods.
- The key steps involved in OEM sheet metal fabrication and the importance of each step.
In the world of manufacturing, OEM (Original Equipment Manufacturer) sheet metal fabrication plays a crucial role. It involves the production of custom-made precision sheet metal components and assemblies that are used in various industries such as aerospace, automotive, electronics, and telecommunications. OEM fabrication ensures that the manufactured products meet the specific requirements and standards of the client. This comprehensive manual will guide you through the process of OEM sheet metal fabrication, highlighting its importance, benefits, and key steps involved.
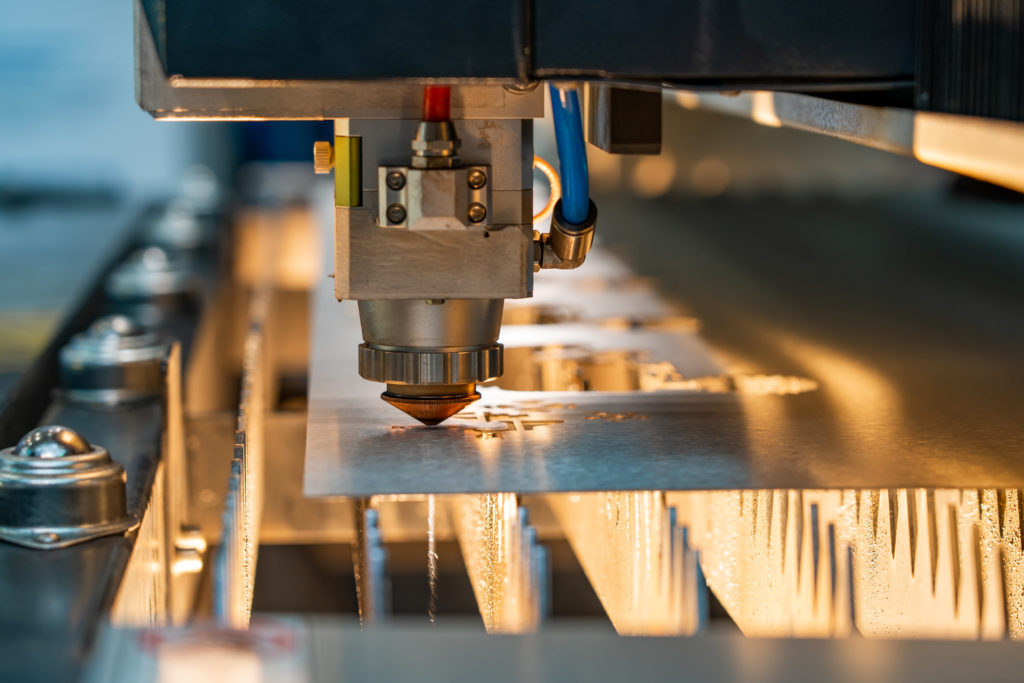
Understanding Precision Sheet Metal Fabrication
Precision sheet metal fabrication is a specialized process that involves the creation of intricate and accurate sheet metal components. It utilizes advanced technology and skilled craftsmanship to transform raw materials into precise and high-quality products. This method offers numerous advantages over traditional fabrication techniques, such as casting and forging.
One of the primary advantages of precision fabrication is the ability to create complex designs with tight tolerances. This level of precision ensures that the fabricated parts fit together seamlessly, resulting in better overall product performance. Additionally, precision fabrication allows for greater design flexibility, enabling the production of unique and customized components.
The use of advanced technology, such as computer-aided design (CAD) software, plays a vital role in achieving precision in sheet metal fabrication. CAD software enables designers and engineers to create detailed 3D models of the desired components, allowing for accurate visualization and analysis before the manufacturing process begins. This technology also facilitates efficient communication between the client and the OEM fabricator, ensuring that the final product meets the client’s specifications.
Skilled craftsmanship is another essential aspect of precision sheet metal fabrication. Experienced technicians and fabricators meticulously handle each step of the process, from material selection to final assembly. Their expertise ensures that the fabricated components are of the highest quality and meet the required standards. With precision sheet metal fabrication, manufacturers can achieve superior product quality, durability, and cost-effectiveness.
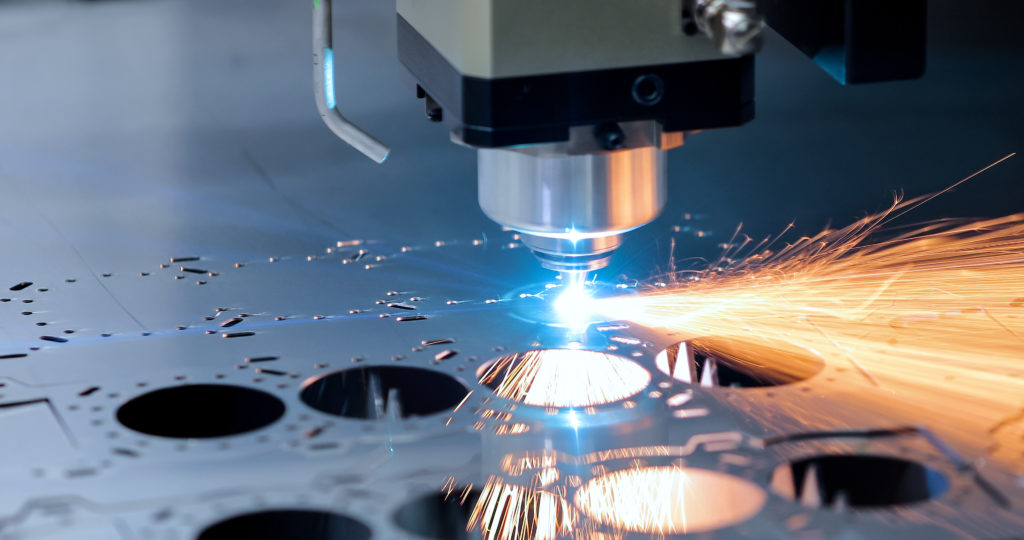
The Role of OEM in Sheet Metal Fabrication
OEM sheet metal fabrication plays a pivotal role in the manufacturing process. As an OEM fabricator, the company specializes in producing sheet metal components based on the client’s design and specifications. This collaboration between the client and the OEM fabricator ensures that the fabricated parts are tailored to meet the specific requirements of the project.
Outsourcing OEM sheet metal fabrication to specialized companies offers several benefits. First and foremost, it allows manufacturers to focus on their core competencies while leaving the fabrication process to the experts. This leads to increased efficiency and productivity, as the OEM fabricator has the necessary experience, equipment, and knowledge to deliver high-quality products.
Working with an OEM fabricator who excels in precision fabrication is particularly advantageous. Precision fabrication ensures that the components are manufactured with the utmost accuracy and attention to detail. This not only enhances the overall product quality but also minimizes the risk of errors or defects. The expertise of an OEM fabricator specializing in precision fabrication can significantly contribute to the success of a project.
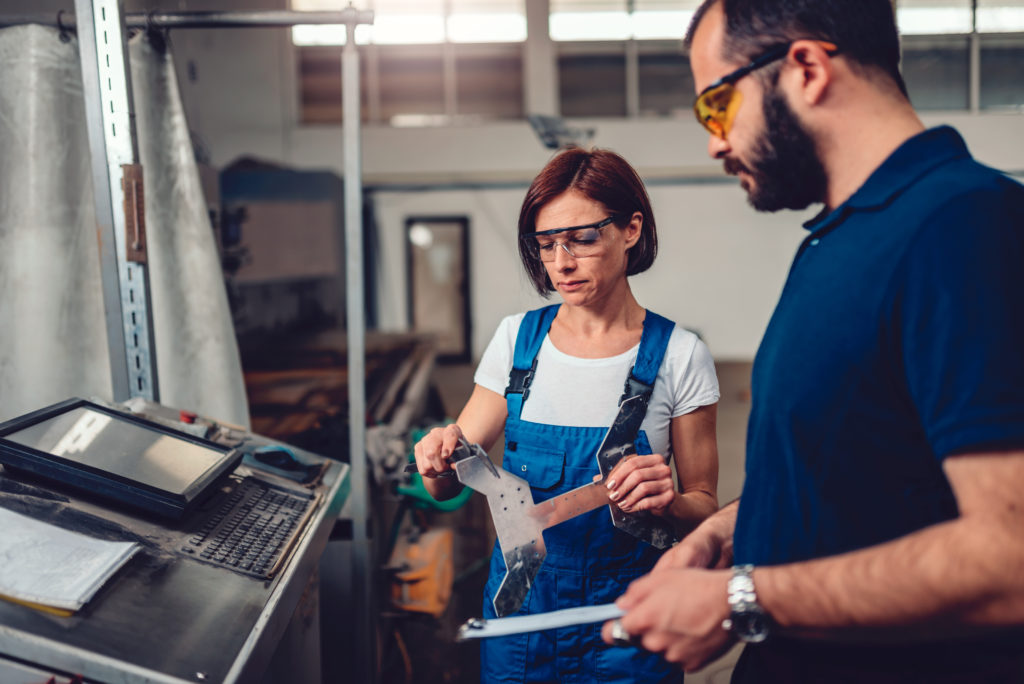
Key Steps in OEM Sheet Metal Fabrication
OEM sheet metal fabrication involves several key steps that are crucial for achieving precise and high-quality results.
a. Requirements Analysis
Before the fabrication process begins, it is essential to clearly define the project requirements. This involves a collaborative approach between the OEM fabricator and the client to understand the project goals, specifications, and any specific industry regulations that must be adhered to. This step ensures that both parties are aligned and have a clear understanding of what needs to be achieved.
b. Design and Engineering
Once the requirements are defined, the next step is design and engineering. Designers and engineers work closely with the client to transform the concepts into feasible sheet metal designs. They utilize computer-aided design (CAD) software to create detailed 3D models of the components, allowing for accurate visualization and analysis. Design reviews and prototyping are essential during this stage to ensure precision, functionality, and manufacturability.
c. Material Selection
The selection of the appropriate material is crucial in OEM sheet metal fabrication. Different materials, such as stainless steel, aluminum, and copper, offer distinct properties and characteristics. The choice of material depends on factors such as product performance requirements, durability, cost considerations, and industry-specific regulations. The OEM fabricator can provide guidance in selecting the most suitable material for the specific application.
d. Manufacturing and Assembly
Once the design and material selection are finalized, the fabrication process begins. This typically involves cutting, bending, welding, and finishing the sheet metal components. Precision machinery and equipment are utilized to ensure accurate and consistent results. Throughout the manufacturing process, quality control measures are implemented to maintain the highest standards of quality. Skilled technicians oversee the assembly of the fabricated components, ensuring that they fit together seamlessly.
e. Quality Assurance and Inspection
Quality assurance is a critical aspect of OEM sheet metal fabrication. The fabricated parts undergo rigorous inspections, measurements, and testing to ensure that they meet the specified requirements. This includes dimensional checks, surface inspections, and performance testing. Quality assurance processes help identify any deviations or defects early on, allowing for necessary adjustments or corrections. This ensures that the final product meets the highest standards of precision and durability.
Case Study: The Power of Precision in OEM Sheet Metal Fabrication
At Smith Manufacturing, a leading OEM sheet metal fabrication company, precision is at the core of their operations. One of their recent projects involved fabricating components for a new generation of electronic enclosures. The client, XYZ Electronics, required precise dimensions and intricate designs to ensure optimal functionality and aesthetics for their products.
During the requirements analysis phase, Smith Manufacturing collaborated closely with XYZ Electronics to understand their project goals and specifications. They organized design reviews and prototyping sessions to ensure that the fabricated components met the client’s expectations in terms of precision and functionality.
Smith Manufacturing utilized advanced computer-aided design (CAD) software to transform the concepts into feasible sheet metal designs. Their team of skilled engineers meticulously worked on every detail, ensuring that the dimensions and tolerances were accurate to the micrometer.
Material selection was a crucial consideration for this project. Smith Manufacturing’s expertise in working with a wide range of materials allowed them to recommend the most suitable options for XYZ Electronics’ electronic enclosures. They considered factors such as product performance, durability, and cost considerations to provide the best solution.
During the manufacturing and assembly phase, Smith Manufacturing employed state-of-the-art machinery and equipment for cutting, bending, welding, and finishing the sheet metal components. Their highly trained technicians meticulously followed the specified dimensions and quality control measures to ensure precise fabrication.
To guarantee the precision and durability of the fabricated parts, Smith Manufacturing implemented a rigorous quality assurance and inspection process. They conducted thorough inspections, measurements, and testing to verify that each component met the specified requirements. This attention to detail ensured that the electronic enclosures manufactured by Smith Manufacturing for XYZ Electronics were of the highest quality.
The success of this project exemplifies the power of precision in OEM sheet metal fabrication. By prioritizing accuracy in every step of the process, Smith Manufacturing was able to deliver components that exceeded their client’s expectations. The collaboration between the OEM fabricator and the client, coupled with advanced technology and skilled craftsmanship, resulted in a successful outcome and a long-lasting partnership between Smith Manufacturing and XYZ Electronics.
Benefits of OEM Sheet Metal Fabrication
There are numerous benefits to outsourcing OEM sheet metal fabrication to specialized companies.
One of the primary advantages is cost-effectiveness. By partnering with an OEM fabricator, manufacturers can avoid the significant upfront investment in equipment, machinery, and skilled labor required for in-house fabrication. The OEM fabricator already possesses the necessary infrastructure and expertise, resulting in reduced costs and improved overall profitability.
Outsourcing OEM fabrication also saves time. Specialized OEM fabricators have streamlined processes in place, enabling faster production and delivery times. This allows manufacturers to meet tight deadlines and respond quickly to market demands.
Quality assurance is another significant benefit of working with OEM fabricators. These companies have extensive experience and expertise in precision fabrication, ensuring that the fabricated parts meet the highest standards of quality and functionality. Additionally, OEM fabricators often have certifications and accreditations that validate their commitment to quality and compliance with industry regulations.
Furthermore, OEM fabricators offer customized solutions to meet specific client requirements. They have the flexibility to accommodate unique designs, materials, and finishing options. This level of customization allows manufacturers to differentiate their products and meet the diverse needs of their customers.
Applications of OEM Sheet Metal Fabrication
OEM sheet metal fabrication finds applications in various industries due to its versatility and precision capabilities. Some of the industries that heavily rely on OEM sheet metal fabrication include:
- Aerospace: OEM fabrication is crucial in the aerospace industry for producing components such as aircraft frames, wings, and engine parts. The precision and durability provided by OEM fabricators are essential for ensuring the safety and efficiency of aerospace systems.
- Automotive: OEM sheet metal fabrication is widely used in the automotive industry to manufacture components such as body panels, chassis, and exhaust systems. The ability to produce complex designs with tight tolerances makes OEM fabrication ideal for automotive applications.
- Electronics: The electronics industry relies on OEM fabrication for manufacturing components such as enclosures, brackets, and heat sinks. The precise and intricate nature of these components requires the expertise of OEM fabricators to ensure proper functionality and compatibility.
- Telecommunications: OEM sheet metal fabrication is essential in the telecommunications industry for producing components such as antenna mounts, enclosures, and racks. The ability to create customized solutions that meet specific telecommunications requirements is a significant advantage of OEM fabrication.
These are just a few examples of the industries that benefit from OEM sheet metal fabrication. The versatility and precision capabilities of OEM fabricators make them indispensable in many manufacturing sectors.
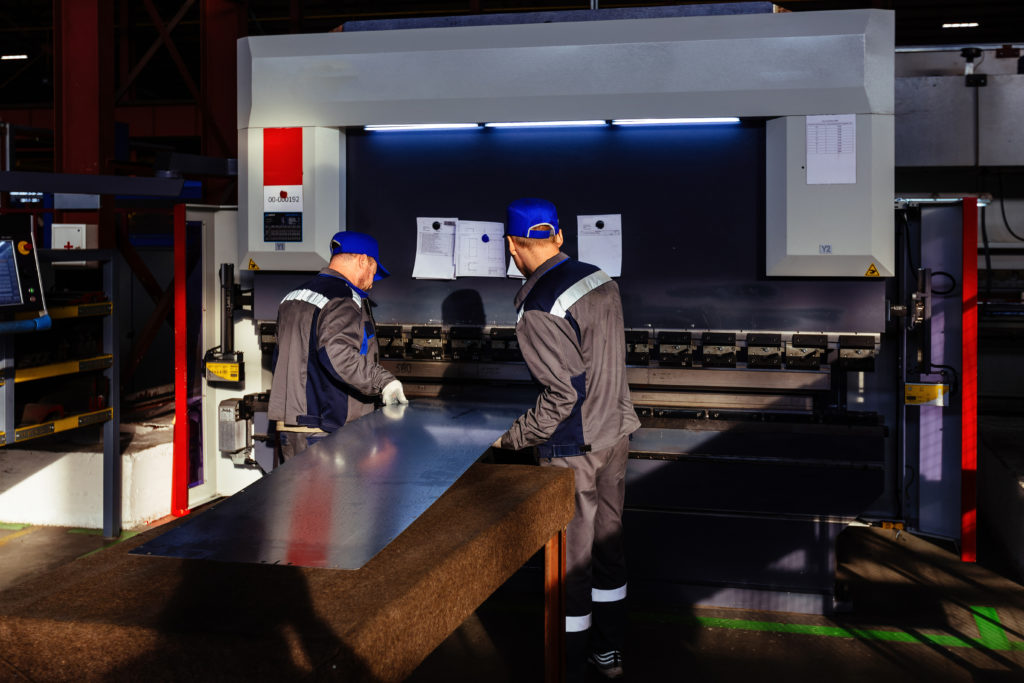
How to Choose the Right OEM Sheet Metal Fabrication Company
Choosing the right OEM sheet metal fabrication company is crucial for the success of your project. Here are some key factors to consider:
- Experience: Look for an OEM fabricator with a proven track record and extensive experience in the industry. A company with a long history of successful projects demonstrates reliability and expertise.
- Capabilities: Evaluate the capabilities of the OEM fabricator. Ensure that they have the necessary equipment, technology, and skilled workforce to handle your specific project requirements.
- Certifications: Verify if the OEM fabricator holds relevant certifications, such as ISO 9001 for quality management systems. Certifications indicate the company’s commitment to quality and adherence to industry standards.
- Reputation: Read customer reviews and testimonials to gauge the reputation of the OEM fabricator. Positive feedback
Benefit | Description |
---|---|
Design Flexibility | OEM sheet metal fabrication allows for greater design flexibility, enabling the production of unique and customized components. This flexibility is crucial in industries where specific requirements and specifications need to be met. |
Scalability | OEM fabricators have the capacity to scale production according to the client’s needs. This scalability is beneficial for manufacturers who experience fluctuations in demand or who need to quickly ramp up production for new product launches. |
Faster Time to Market | Outsourcing OEM fabrication to specialized companies can significantly reduce the time it takes to bring a product to market. OEM fabricators have streamlined processes in place, allowing for faster production and delivery times. |
Access to Expertise | Working with an OEM fabricator provides access to specialized expertise and knowledge in precision fabrication. These fabricators have experience in handling complex designs and materials, ensuring that the final product meets the highest standards of quality and functionality. |
Cost Savings | Outsourcing OEM fabrication eliminates the need for manufacturers to invest in expensive equipment, machinery, and skilled labor. This results in cost savings and improved overall profitability. |
Risk Mitigation | OEM fabricators have quality assurance processes in place to identify and rectify any deviations or defects early on in the fabrication process. This helps mitigate the risk of costly errors or rework. |
Common Questions
Who provides OEM sheet metal fabrication services?
Trusted manufacturers and suppliers offer OEM sheet metal fabrication services.
What is precision sheet metal fabrication?
Precision sheet metal fabrication is the process of creating complex metal parts with high accuracy and tight tolerances.
How does OEM sheet metal fabrication work?
OEM sheet metal fabrication involves cutting, bending, and assembling metal sheets to create custom parts based on specific requirements.
Who handles large-scale OEM sheet metal fabrication orders?
Experienced manufacturers specialize in handling large-scale OEM sheet metal fabrication orders efficiently and effectively.
What are the benefits of precision sheet metal fabrication?
Precision sheet metal fabrication ensures high-quality, durable parts that meet precise specifications and reduce overall production costs.
How can I address concerns about the quality of OEM sheet metal fabrication?
Look for manufacturers with certifications, a strong track record, and positive customer reviews to ensure top-notch quality.