What You’ll Learn About Metal Fabrication
- Definition and applications of metal fabrication in various industries.
- Types of metals used and their suitability for different applications.
- Processes involved in metal fabrication such as cutting, bending, welding, finishing, and quality control.
Metal fabrication, also known as metalworking, is the process of creating metal structures through cutting, bending, and assembling processes. It involves the use of various raw materials and techniques such as welding, cutting, forming, and machining. The end products can be similar to those produced through other metalworking processes. Specialties in metal fabrication include casting, powder coating, powder metallurgy, welding, and machining.
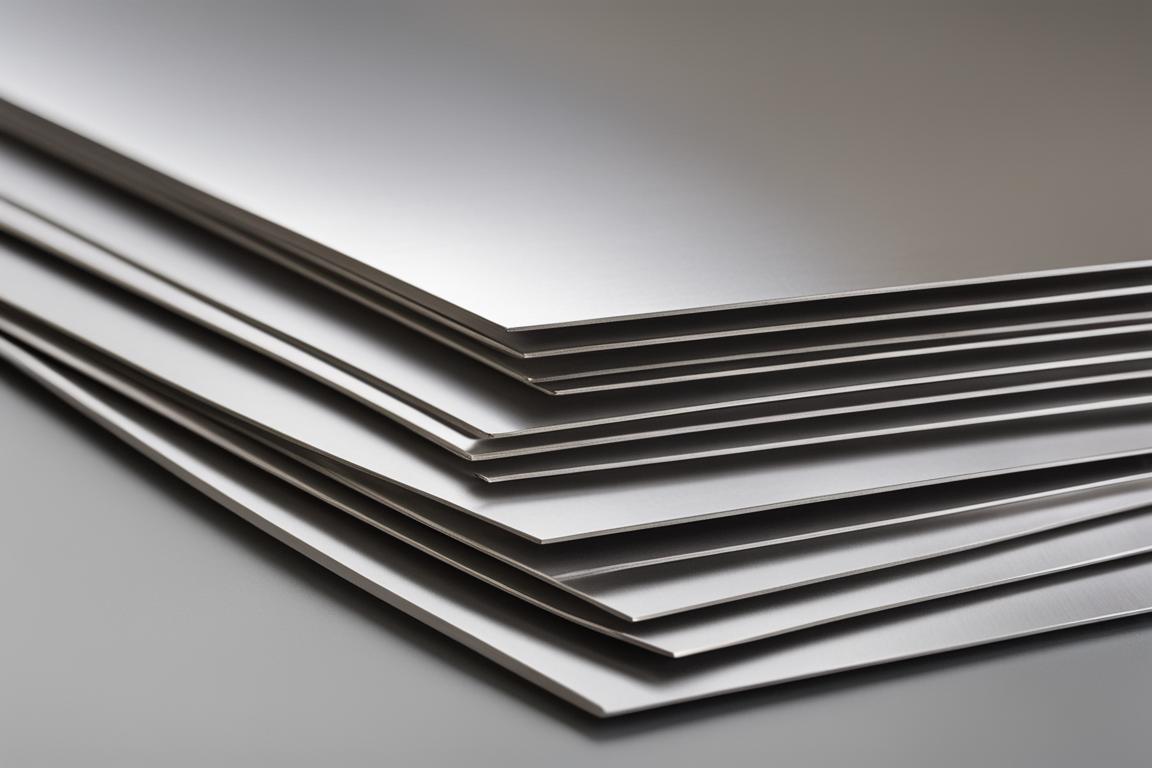
Understanding Metals in Metal Fabrication
Metal fabrication involves working with various types of metals, each with its unique properties and characteristics. The most commonly used metals include stainless steel, aluminum, copper, and titanium. These metals are chosen based on their suitability for specific applications and their inherent properties.
Types of Metals Used
1. Stainless Steel
Stainless steel is a popular choice in metal fabrication due to its corrosion resistance, strength, and aesthetic appeal. It is commonly used in the production of kitchen equipment, medical devices, and architectural structures.
2. Aluminum
Aluminum is known for its lightweight nature and high strength-to-weight ratio. It finds extensive use in the aerospace industry, automotive components, and structural applications.
3. Copper
Copper is valued for its excellent electrical conductivity and malleability. It is widely used in electrical wiring, plumbing, and heat exchangers.
4. Titanium
Titanium is renowned for its high strength, corrosion resistance, and biocompatibility, making it a preferred material in aerospace, medical implants, and chemical processing equipment.
Properties and Characteristics of Each Metal
Each metal used in fabrication possesses unique mechanical, thermal, and electrical properties that make them suitable for specific applications. Understanding these properties is crucial in ensuring the quality and performance of the fabricated products.
Suitability for Specific Applications
The choice of metal for a particular application depends on factors such as environmental conditions, mechanical stresses, and desired aesthetics. Each metal’s unique properties make it suitable for specific industrial and commercial uses.
By understanding the characteristics and properties of these metals, metal fabricators can make informed decisions regarding material selection, ensuring the optimal performance and longevity of the fabricated products.
Design and Engineering in Metal Fabrication
Design and engineering play a pivotal role in the metal fabrication process. They encompass the conceptualization, prototyping, and finalization of the products, ensuring they meet the desired specifications and quality standards.
Role of Design and Engineering
Design and engineering are essential in creating efficient and functional metal structures. They involve conceptualizing the product, creating detailed drawings, and developing prototypes to test the design’s feasibility.
CAD/CAM Software and Prototyping
Computer-aided design (CAD) and computer-aided manufacturing (CAM) software are integral in the design and engineering phase. They enable precise modeling, simulation, and prototyping, leading to the development of accurate and manufacturable designs.
Design for Manufacturability (DFM) Considerations
Design for Manufacturability (DFM) involves designing products in a way that optimizes the manufacturing process. It focuses on reducing production costs, improving product quality, and minimizing lead times.
The integration of design and engineering in metal fabrication ensures that the fabricated products meet the required specifications, functionality, and performance standards.
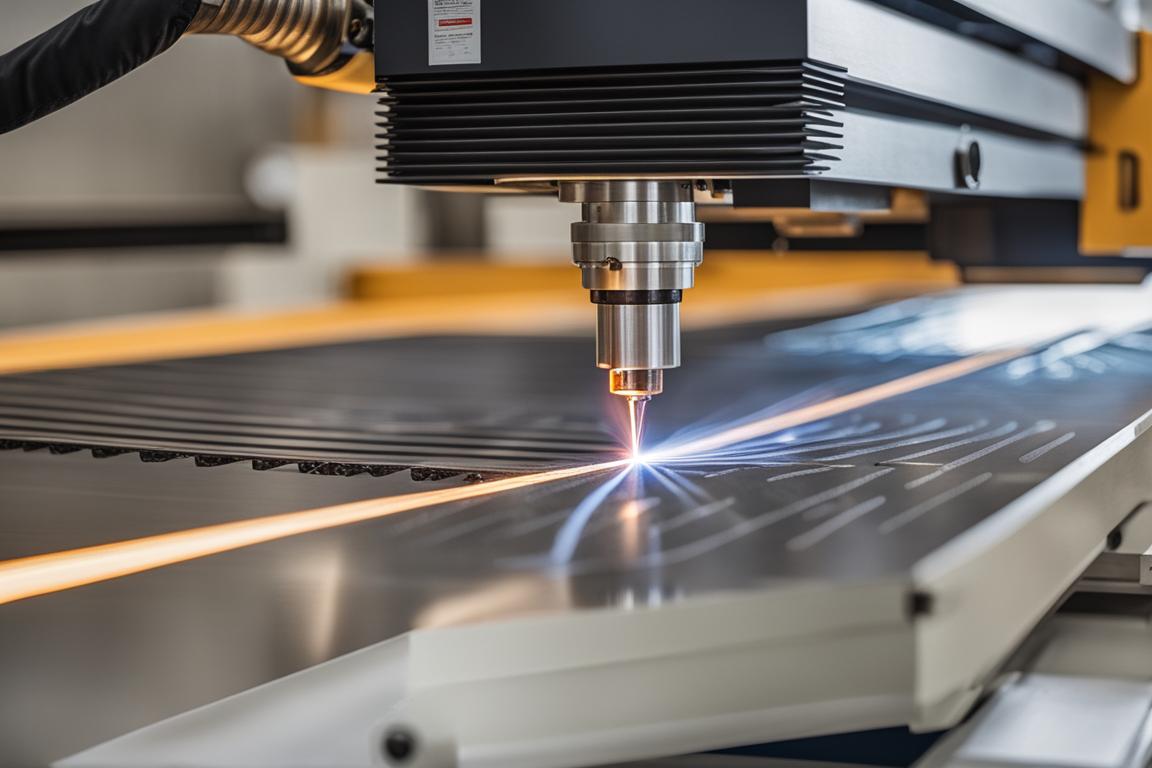
Metal Cutting Processes in Fabrication
Metal cutting is a fundamental aspect of metal fabrication, involving various techniques to shape raw metal into the desired forms and dimensions.
Laser Cutting
Laser cutting is a versatile and precise method used to cut intricate patterns and shapes in metals. It is commonly employed in industries such as automotive, electronics, and aerospace for its accuracy and efficiency.
Water Jet Cutting
Water jet cutting utilizes high-pressure water mixed with an abrasive substance to cut through metals. This process is suitable for materials sensitive to high temperatures and is known for its ability to produce clean and burr-free edges.
Shearing and Sawing
Shearing and sawing are traditional metal cutting methods suitable for straight cuts and large-scale production. These processes are vital in shaping metal sheets and bars before further fabrication.
Applications and Techniques
Each metal cutting process has its unique applications and techniques, allowing fabricators to achieve precision, speed, and flexibility in creating various metal components and structures.
By employing the appropriate cutting method, fabricators can efficiently transform raw metal materials into precise components, laying the foundation for subsequent fabrication processes.
Metal Bending and Forming Techniques
Bending and forming are essential processes in metal fabrication, enabling the creation of complex shapes and structures from flat metal sheets and bars.
Press Brake Forming
Press brake forming involves using a press brake machine to bend metal sheets into predetermined shapes and angles. This technique is crucial in producing components for machinery, furniture, and architectural elements.
Roll Forming and Folding
Roll forming and folding are methods used to create continuous bends and curves in metal sheets. These processes are commonly employed in the production of roof panels, gutters, and automotive components.
Stamping and Punching
Stamping and punching are utilized to create intricate patterns and perforations in metal sheets. They are essential in the production of decorative elements, electrical enclosures, and appliance components.
Applications and Methods
Each bending and forming technique has specific applications and methods, enabling fabricators to meet diverse design requirements and produce custom metal components with precision and accuracy.
By leveraging these bending and forming techniques, metal fabricators can transform flat metal sheets into three-dimensional structures, meeting the exact design specifications and functional requirements of the products.
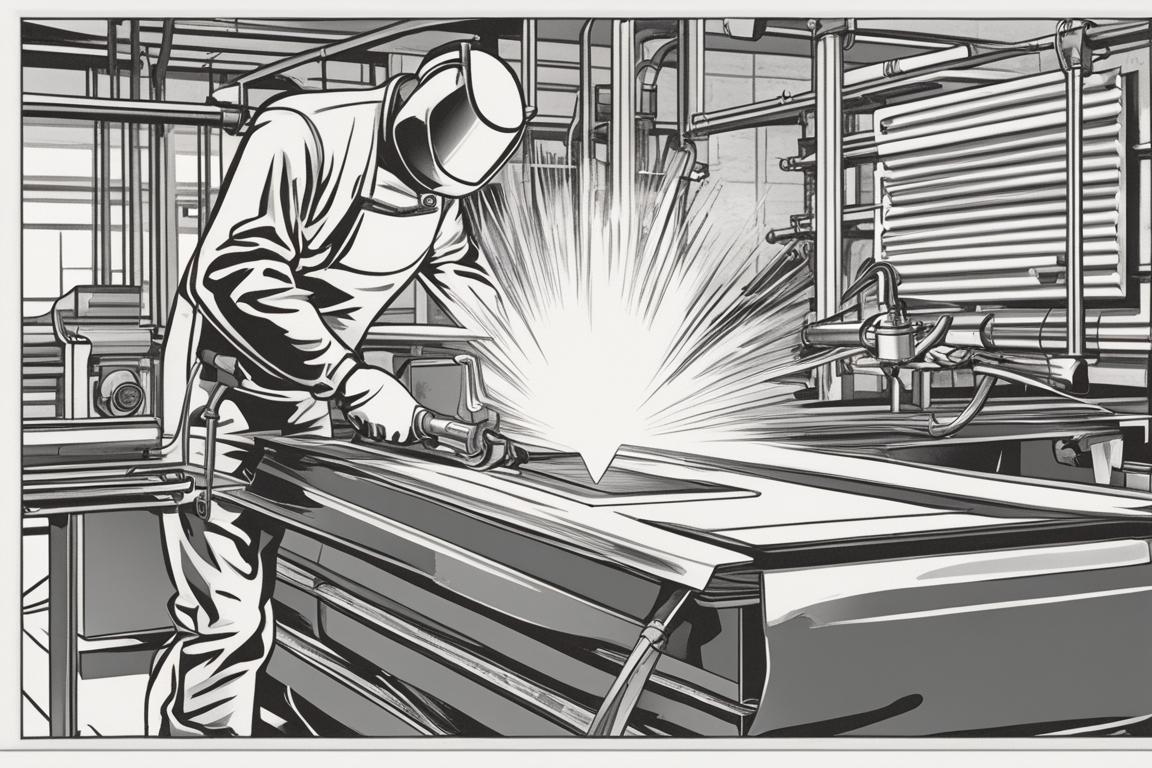
Welding and Joining Methods
Welding and joining are critical processes in metal fabrication, allowing the assembly and joining of metal components to create cohesive and durable structures.
TIG Welding
Tungsten Inert Gas (TIG) welding is a precise and clean welding method that produces high-quality welds. It is commonly used in applications requiring superior aesthetics and weld integrity.
MIG Welding
Metal Inert Gas (MIG) welding is a versatile and efficient welding process suitable for a wide range of metals and thicknesses. It is widely utilized in automotive, construction, and industrial fabrication.
Resistance and Spot Welding
Resistance and spot welding employ electrical currents and pressure to join metal components. These methods are ideal for mass production and are commonly used in automotive and appliance manufacturing.
Joining Techniques in Metal Fabrication
Each welding and joining technique offers distinct advantages, enabling fabricators to create strong and reliable connections between metal components, ensuring the structural integrity and performance of the fabricated products.
By employing the appropriate welding and joining methods, fabricators can assemble metal components with precision and strength, meeting the structural and functional requirements of the final products.
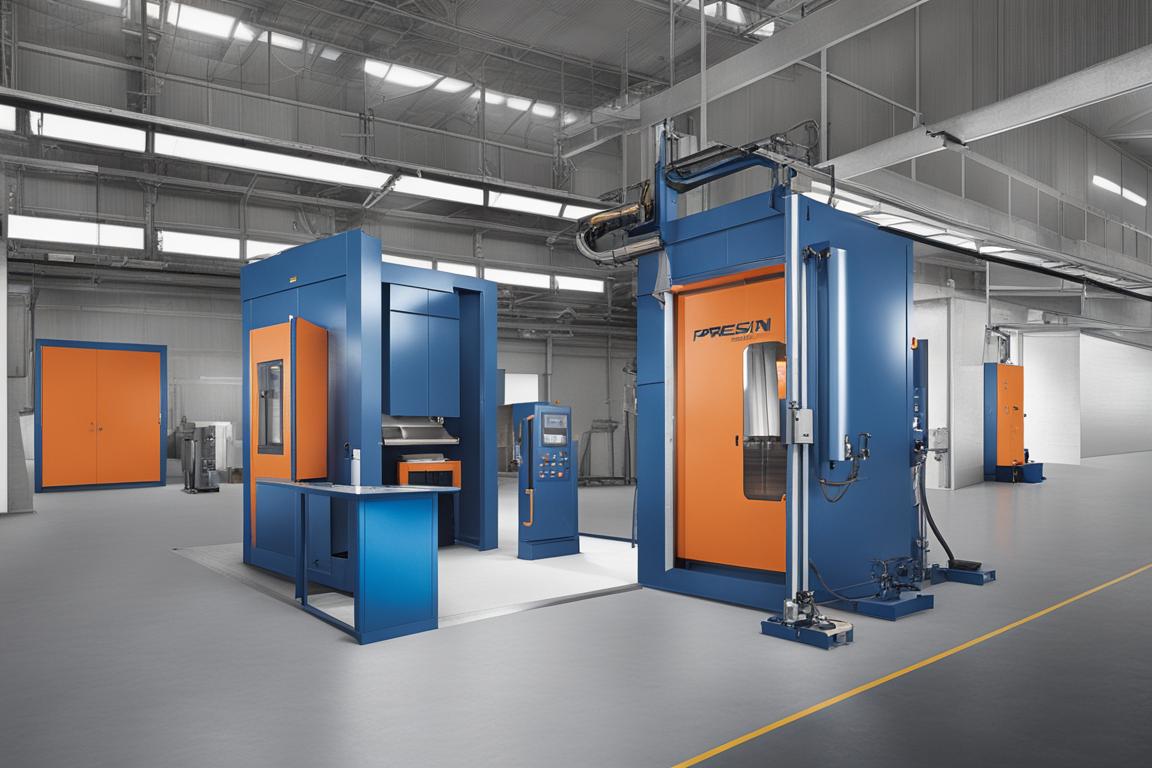
Finishing Processes in Metal Fabrication
Finishing processes are essential in metal fabrication, enhancing the aesthetic appeal, durability, and corrosion resistance of the fabricated products.
Powder Coating and Painting
Powder coating and painting provide protective and decorative finishes to metal components, offering resistance to corrosion, UV exposure, and wear. These processes are crucial in automotive, architectural, and consumer goods applications.
Anodizing and Plating
Anodizing and plating are surface treatment methods that enhance the durability and appearance of metal parts. They are widely used in aerospace, electronics, and jewelry manufacturing.
Surface Texturing and Polishing
Surface texturing and polishing techniques impart unique textures and mirror-like finishes to metal surfaces, adding aesthetic value and tactile appeal to the fabricated products.
Impact on Final Product Quality
The application of finishing processes significantly impacts the final product quality, enhancing its appearance, functionality, and longevity. These processes add value to the fabricated products, making them suitable for diverse industrial and consumer applications.
By incorporating finishing processes, fabricators can ensure that the fabricated products meet the desired aesthetic and functional requirements, enhancing their marketability and appeal to end-users.
Quality Control and Standards in Metal Fabrication
Quality control is a critical aspect of metal fabrication, ensuring that the fabricated products meet the specified quality standards, tolerances, and regulatory requirements.
Importance of Quality Assurance
Quality assurance is paramount in metal fabrication to ensure that the products meet the desired performance, safety, and reliability standards, instilling confidence in end-users and stakeholders.
Inspection Methods and Testing
Inspection methods and testing protocols are employed to verify the quality and integrity of fabricated products, encompassing dimensional checks, material testing, and non-destructive testing.
Tolerance Standards and Compliance
Tolerance standards define the acceptable variations in dimensions and material properties, ensuring that the fabricated products conform to the specified design and performance criteria.
Industry Regulations and Certifications
Adherence to industry regulations and certifications, such as ISO standards and AWS certifications, demonstrates a fabricator’s commitment to quality, safety, and compliance with international best practices.
By implementing robust quality control measures, fabricators can ensure the consistent production of high-quality products, meeting the stringent requirements of diverse industries and applications.
It’s crucial for fabricators to adhere to rigorous quality control standards and certifications to ensure the reliability, safety, and performance of the fabricated products, meeting the stringent demands of various industries and applications.
Case Studies in Metal Fabrication
Case studies provide real-world examples of metal fabrication applications, showcasing the diverse processes and techniques employed to create innovative and functional metal structures and components.
Real-World Examples and Applications
Real-world case studies highlight the versatility and adaptability of metal fabrication in addressing unique engineering and design challenges across different industries and sectors.
Showcase of Diverse Metal Fabrication Processes
Case studies demonstrate the diverse range of metal fabrication processes, from intricate laser-cut designs to large-scale structural components, exemplifying the creativity and technical expertise of metal fabricators.
By analyzing case studies, engineers, designers, and industry professionals can gain valuable insights into the practical applications and benefits of metal fabrication in addressing complex design and engineering requirements.
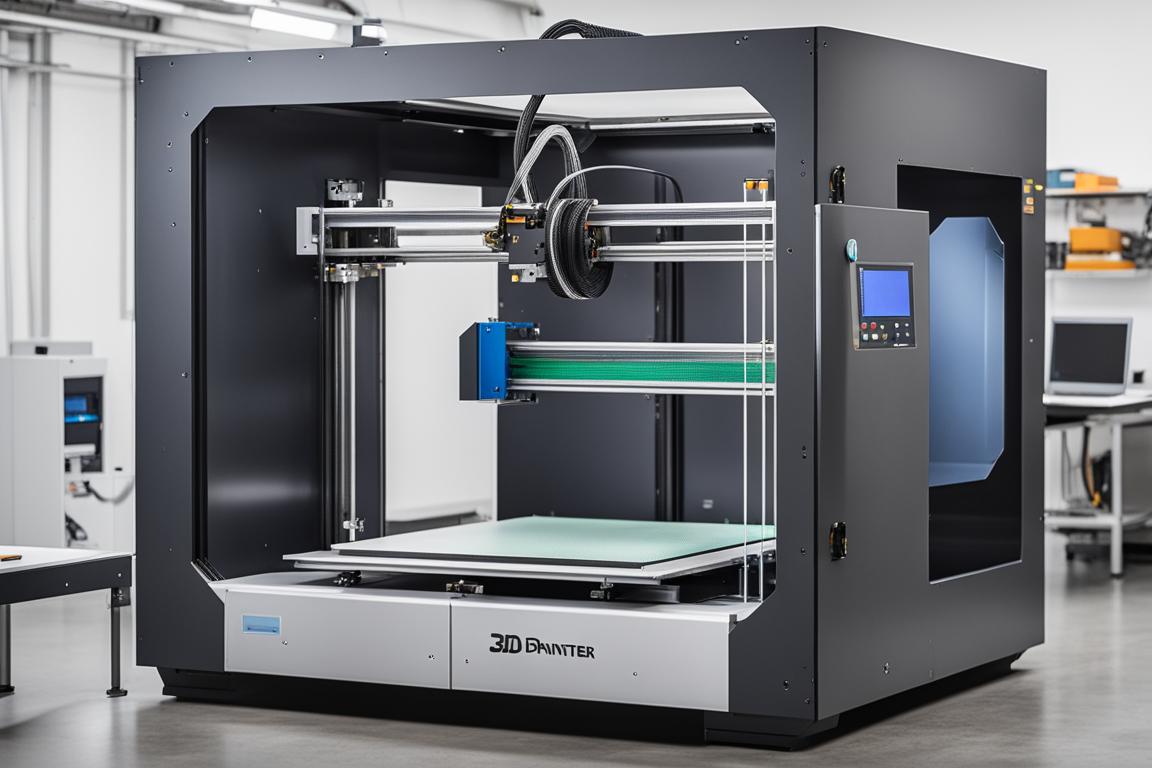
Emerging Trends in Metal Fabrication
The metal fabrication industry is continually evolving, driven by technological advancements and innovative practices that shape the future of metal fabrication processes and applications.
Additive Manufacturing and 3D Printing
Additive manufacturing and 3D printing are revolutionizing metal fabrication, enabling the production of complex geometries, lightweight structures, and customized components with enhanced design freedom.
Automation and Robotics
Automation and robotics are transforming metal fabrication with increased efficiency, precision, and productivity, leading to streamlined production processes and reduced lead times.
Impact on the Metal Fabrication Industry
These emerging trends are reshaping the metal fabrication industry, offering new avenues for design innovation, cost-effective production, and sustainable manufacturing practices.
The adoption of emerging trends in metal fabrication is poised to revolutionize the industry, driving efficiency, sustainability, and innovation in the production of metal components and structures.
Industry Insights and Perspectives
Industry insights and perspectives from experts and professionals offer valuable knowledge and foresight into the evolving landscape of metal fabrication and its implications for various sectors.
Expert Interviews and Contributions
Insights from industry experts and thought leaders provide in-depth analysis and commentary on the current state and future of metal fabrication, offering valuable foresight to industry stakeholders.
Valuable Insights and Future Considerations
Valuable insights and future considerations elucidate the trends, challenges, and opportunities shaping the metal fabrication industry, guiding strategic decisions and investments in technology and talent.
By incorporating diverse perspectives and expert insights, this guide aims to provide a comprehensive understanding of the current and future landscape of metal fabrication, offering valuable foresight and strategic guidance to industry professionals and stakeholders.
Training, Education, and Career Opportunities in Metal Fabrication
Metal fabrication offers diverse opportunities for individuals seeking career paths in manufacturing, engineering, design, and skilled trades, with a range of training programs and educational resources available to support skill development and career advancement.
Training Programs and Apprenticeships
Training programs and apprenticeships provide hands-on learning experiences and mentorship opportunities, equipping individuals with the practical skills and knowledge required for a successful career in metal fabrication.
Certifications and Skill Development
Certifications and skill development initiatives enable individuals to enhance their expertise in specific areas of metal fabrication, demonstrating their competency and proficiency to employers and clients.
Educational Resources and Institutions
Educational institutions and industry organizations offer a wealth of resources, including courses, workshops, and technical publications, to support continuous learning and professional development in metal fabrication.
Career Paths and Opportunities in Metal Fabrication
Metal fabrication presents diverse career paths, including welding, machining, engineering, and management, with opportunities for professional growth, specialization, and entrepreneurship within the industry.
By providing access to comprehensive training, education, and career development resources, individuals can pursue rewarding and impactful careers in metal fabrication, contributing to the advancement of the industry and its technological capabilities.
Partnering with a Metal Fabrication Company
Businesses and individuals seeking metal fabrication services must consider various factors when partnering with a fabricator, including capacity, expertise, reputation, and sustainability practices.
Considerations for Businesses and Individuals
Partnership considerations encompass evaluating the fabricator’s capabilities, portfolio, and commitment to quality, safety, and customer satisfaction to ensure a successful collaboration.
Capacity, Expertise, and Project Management
Assessing a fabricator’s capacity, technical expertise, and project management capabilities is crucial in determining their suitability for meeting the project requirements and timelines.
Reputation, Experience, and Client Testimonials
Reviewing a fabricator’s reputation, industry experience, and client testimonials provides valuable insights into their track record of delivering high-quality products and exceptional service.
Partnering with a reputable and experienced metal fabrication company is essential for businesses and individuals seeking reliable and high-quality fabrication services, ensuring the successful realization of their projects and products.
Sustainability in Metal Fabrication
Sustainability practices in metal fabrication focus on minimizing environmental impact, conserving resources, and promoting energy-efficient and eco-friendly manufacturing processes.
Sustainable Practices and Environmental Impact
Implementing sustainable practices, such as waste reduction, energy conservation, and recycling, minimizes the environmental footprint of metal fabrication operations.
Recycling and Waste Management
Recycling metal scrap and implementing efficient waste management strategies reduce the environmental burden of metal fabrication, contributing to a circular and sustainable production cycle.
Energy-Efficient Processes and Green Initiatives
Adopting energy-efficient processes and green initiatives, such as renewable energy integration and eco-friendly material sourcing, further enhances the sustainability of metal fabrication operations.
By prioritizing sustainability in metal fabrication, fabricators can reduce their environmental impact, conserve resources, and contribute to a more sustainable and responsible manufacturing industry.
FAQs about Metal Fabrication
Addressing common concerns and queries related to metal fabrication helps individuals and businesses gain clarity on cost estimation, lead time considerations, customization options, and material choices.
Cost Estimation and Lead Time Considerations
Clarifying cost estimation factors and lead time considerations provides transparency and clarity, enabling informed decision-making for fabrication projects.
Customization and Material Options
Explaining customization possibilities and material options empowers individuals and businesses to make informed choices that align with their design requirements and performance expectations.
Answering frequently asked questions about metal fabrication enables individuals and businesses to make well-informed decisions when embarking on fabrication projects, ensuring clarity and confidence in the process.
Conclusion
Metal fabrication is a dynamic and versatile process that plays a crucial role in producing high-quality and functional metal structures and components. As the industry continues to evolve, embracing emerging trends, sustainability practices, and technological innovations, the future of metal fabrication holds immense potential for shaping industries and driving innovation across diverse sectors.
By providing a comprehensive overview of metal fabrication and its multifaceted applications, this guide aims to equip readers with a holistic understanding of the industry, empowering them to make informed decisions, pursue rewarding careers, and leverage the capabilities of metal fabrication to drive innovation and progress.
In conclusion, metal fabrication stands at the intersection of art, science, and engineering, offering endless opportunities for creativity, ingenuity, and impactful contributions to the manufacturing landscape. As the industry continues to advance, embracing new technologies and sustainable practices, the art of precision sheet metal fabrication is poised to shape a future defined by innovation, efficiency, and excellence.
If you have any questions or are interested in exploring how metal fabrication can benefit your projects, please don’t hesitate to contact us. Our team of experts is ready to assist you in harnessing the power of metal fabrication for your specific needs and goals.