What You Will Learn About Metal Fabrication
You will learn:
1. The significance and applications of metal fabrication in various industries.
2. Techniques and considerations involved in precision sheet metal fabrication.
3. Emerging trends and technologies impacting metal fabrication processes.
Metal fabrication is a vital process that involves transforming raw materials into structures, components, or finished products made of metal. It encompasses a wide range of techniques, including cutting, bending, welding, and finishing, to create products with precise specifications. This article explores the world of precision sheet metal fabrication, where skilled craftsmen employ advanced techniques to produce high-quality metal products.
Metal fabrication plays a crucial role in various industries, such as automotive, aerospace, construction, and electronics. From the chassis of a car to the intricate components of an aircraft, metal fabrication is essential for creating durable and functional structures. Its versatility allows for the production of a wide range of products, including machinery parts, enclosures, cabinets, and architectural elements.

Understanding Precision Sheet Metal Fabrication
Precision sheet metal fabrication is a specialized branch of metal fabrication that focuses on working with thin sheets of metal, typically less than 6mm in thickness. This technique requires meticulous attention to detail and high precision to produce complex shapes and tight tolerances. Precision sheet metal fabrication often involves the use of computer-aided design (CAD) software and advanced machinery to ensure accuracy and consistency throughout the manufacturing process.
Overview of precision sheet metal fabrication techniques
Precision sheet metal fabrication encompasses various techniques to shape, cut, join, and finish metal sheets. These techniques include:
- Cutting: Cutting is a fundamental process in precision sheet metal fabrication. Common cutting methods include laser cutting, plasma cutting, and water jet cutting. Each technique offers unique advantages and is suitable for different types of materials and thicknesses.
- Bending: Bending involves the deformation of metal sheets to create angles, curves, or complex shapes. Press brake forming, roll forming, and stretch forming are commonly used bending techniques in precision sheet metal fabrication.
- Joining: Joining techniques are used to connect different metal sheets and create a cohesive structure. Welding methods like TIG (Tungsten Inert Gas) welding, MIG (Metal Inert Gas) welding, and spot welding are commonly employed in precision sheet metal fabrication.
- Finishing: Finishing processes such as grinding, polishing, painting, and powder coating enhance the aesthetic appeal and provide protection against corrosion for the final product.
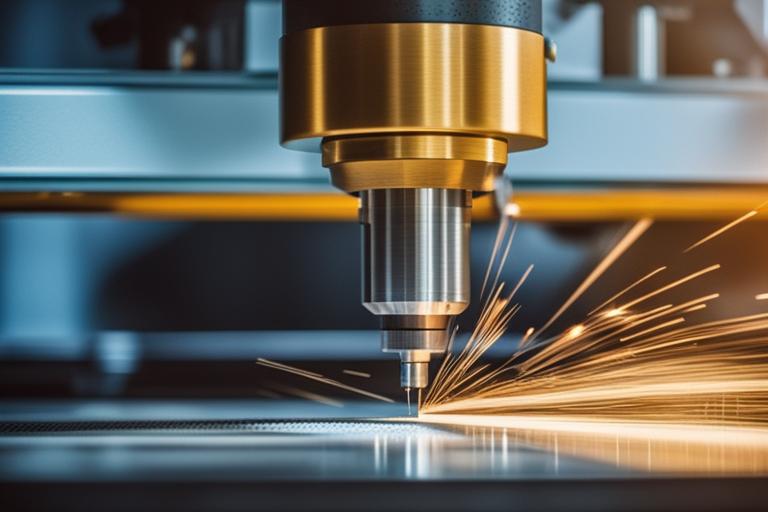
Specialized techniques used in precision sheet metal fabrication
Precision sheet metal fabrication often requires specialized techniques to achieve the desired results. These techniques include:
- CNC Machining: Computer Numerical Control (CNC) machining utilizes computer-controlled machinery to precisely cut, drill, and shape metal sheets. CNC machines offer high accuracy and repeatability, making them ideal for complex projects.
- Punching and Stamping: Punching and stamping techniques use specialized tools to create holes, indentations, or patterns on metal sheets. These techniques are commonly used to create ventilation holes, logos, or decorative features.
- Embossing and Engraving: Embossing and engraving are techniques used to add texture, patterns, or information to metal sheets. They are often employed for branding purposes or to enhance the visual appeal of the product.
Applications and benefits of precision sheet metal fabrication
Precision sheet metal fabrication finds applications in a wide range of industries, including:
- Electronics: Precision sheet metal fabrication is used to create enclosures, chassis, and components for electronic devices. The precise dimensions and excellent shielding properties of metal make it an ideal choice for electronic products.
- Medical: Medical equipment and devices often require precise fabrication to ensure safety, reliability, and compatibility with other components. Precision sheet metal fabrication enables the production of medical instrument casings, surgical tools, and specialized equipment.
- Automotive: The automotive industry relies heavily on precision sheet metal fabrication for the production of vehicle components, frames, and body panels. The ability to create complex shapes and tight tolerances ensures the structural integrity and safety of automobiles.
- Aerospace: Precision sheet metal fabrication is essential in the aerospace industry, where lightweight yet robust components are required. From aircraft frames to engine parts, precision fabrication techniques ensure the highest standards of quality and performance.
The benefits of precision sheet metal fabrication include:
- High accuracy: Precision sheet metal fabrication techniques allow for the creation of intricate designs and tight tolerances, ensuring a high level of accuracy and consistency in the final product.
- Cost-effectiveness: Precision fabrication techniques optimize material usage and reduce waste, resulting in cost savings. Additionally, the ability to create complex shapes and features in a single process minimizes the need for additional machining operations.
- Durability: Metal fabricated through precision techniques is known for its strength and durability. It can withstand harsh conditions, making it suitable for demanding applications.
- Customization: Precision sheet metal fabrication offers a high degree of customization, allowing manufacturers to meet specific design requirements and produce unique products.
By leveraging the capabilities of precision sheet metal fabrication, manufacturers can achieve unparalleled quality and meet the demands of various industries.
Materials Used in Metal Fabrication
Metal fabrication involves working with a wide range of metals, each with its own unique properties and characteristics. The choice of material depends on the specific application, desired attributes, and budget considerations.

Common types of metals used in metal fabrication
- Steel: Steel is one of the most commonly used metals in metal fabrication due to its strength, versatility, and affordability. It is available in various grades, each offering different properties such as corrosion resistance, hardness, and weldability.
- Aluminum: Aluminum is a lightweight metal that exhibits excellent corrosion resistance and high thermal conductivity. It is widely used in industries such as aerospace, automotive, and construction.
- Stainless Steel: Stainless steel is known for its corrosion resistance and hygienic properties, making it suitable for applications in the food processing, medical, and pharmaceutical industries. It is available in different grades, each offering varying levels of corrosion resistance and strength.
- Copper: Copper is valued for its excellent electrical and thermal conductivity. It finds applications in electrical wiring, plumbing systems, and heat exchangers.
Properties and suitability of metals for specific applications
The choice of metal depends on the specific requirements of the application. Some key factors to consider include:
- Strength: The strength of the metal determines its load-bearing capacity and resistance to deformation. For structural applications, high-strength metals like steel are often preferred.
- Corrosion resistance: Corrosion resistance is crucial, especially for applications exposed to harsh environments or corrosive substances. Stainless steel and aluminum alloys are known for their excellent corrosion resistance.
- Weight: In applications where weight is a critical factor, lightweight metals like aluminum and titanium are preferred.
- Conductivity: Electrical and thermal conductivity are important considerations in industries such as electronics or heating and cooling systems. Copper and aluminum are widely chosen for their excellent conductivity.
Considerations for material selection in metal fabrication projects
When selecting a material for a metal fabrication project, several factors should be considered:
- Application requirements: Consider the specific demands of the application, such as strength, corrosion resistance, conductivity, or compatibility with other materials.
- Cost: Evaluate the cost-effectiveness of the material, considering factors such as availability, production methods, and any additional processing required.
- Manufacturability: Assess the ease of fabrication, including cutting, bending, welding, and finishing processes. Some materials may require specialized equipment or techniques.
- Environmental factors: Consider the environmental conditions the final product will be exposed to, such as temperature, humidity, or exposure to chemicals. Choose a material that can withstand these conditions without degradation.
By carefully selecting the appropriate material for a metal fabrication project, manufacturers can ensure the desired performance, durability, and cost-effectiveness of the final product.
Design and Planning in Metal Fabrication
The design and planning phase of a metal fabrication project is crucial for achieving a successful outcome. It involves collaboration between designers and fabricators to define the product’s specifications, tolerances, and cost-effectiveness.

Importance of proper design and planning in metal fabrication
Proper design and planning are essential in metal fabrication for several reasons:
- Optimizing material usage: Effective design can minimize material waste and reduce costs. By considering the intended use and structural requirements, designers can optimize the design to ensure efficient material usage.
- Meeting tolerances: Designers must understand the manufacturing capabilities and limitations of the fabrication processes. By specifying appropriate tolerances, designers can ensure that the final product meets the required specifications.
- Streamlining the manufacturing process: An efficient design can simplify the manufacturing process, reducing production time and costs. By minimizing the number of operations and tool changes, designers can improve efficiency and productivity.
Considerations for material selection, tolerances, and cost-effectiveness
During the design and planning phase, several factors should be considered:
- Material selection: As discussed earlier, the choice of material depends on factors such as strength, corrosion resistance, weight, and conductivity. Designers must select a material that meets the application requirements while considering cost constraints.
- Tolerances: Tolerances define the acceptable variation in dimensions and ensure the proper fit and functionality of the final product. Designers need to specify appropriate tolerances based on the fabrication processes and the product’s intended use.
- Cost-effectiveness: Designers should consider the cost implications of the design choices. Complex designs or tight tolerances may increase production costs, so designers must strike a balance between functionality and cost-effectiveness.
Collaboration between designers and fabricators in the design process
Collaboration between designers and fabricators is crucial for a successful metal fabrication project. An open line of communication and mutual understanding of each other’s requirements and constraints can lead to a more efficient and cost-effective design.
Designers should consult fabricators early in the design process to gain insights into the fabrication techniques, material limitations, and cost implications. Fabricators, on the other hand, should provide feedback and suggestions to optimize the design for manufacturability.
By fostering collaboration between designers and fabricators, metal fabrication projects can benefit from the expertise of both parties, resulting in better overall outcomes.
In the next section, we will explore the various cutting and shearing techniques employed in metal fabrication.
Cutting and Shearing Techniques in Metal Fabrication
Cutting and shearing are fundamental processes in metal fabrication, enabling the transformation of metal sheets into desired shapes and sizes. Different cutting techniques offer unique advantages and are suited for specific applications.

Laser cutting in metal fabrication
Laser cutting is a widely used cutting technique in metal fabrication. It involves the use of a high-powered laser beam to melt, burn, or vaporize the material, allowing for precise and clean cuts. Laser cutting offers several advantages:
- High precision: Laser cutting provides exceptional accuracy, enabling the creation of intricate designs and tight tolerances.
- Versatility: Laser cutting can be used on a wide range of materials, including metals, plastics, wood, and ceramics.
- Non-contact process: Laser cutting is a non-contact process, minimizing the risk of material deformation or damage.
- Minimal heat-affected zone: Laser cutting produces a small heat-affected zone, reducing the chances of material warping or distortion.
Laser cutting is commonly used in industries where precision and intricate designs are crucial, such as electronics, automotive, and aerospace.
Plasma cutting in metal fabrication
Plasma cutting is a cutting technique that utilizes a high-velocity plasma jet to melt and remove the material. Plasma cutting offers the following benefits:
- High cutting speed: Plasma cutting is known for its fast cutting speeds, making it suitable for projects that require high productivity.
- Ability to cut thick materials: Plasma cutting can effectively cut through thick materials, making it ideal for heavy-duty applications.
- Versatility: Plasma cutting can be used on a wide range of conductive materials, including steel, stainless steel, aluminum, and copper.
Plasma cutting is commonly employed in industries such as construction, automotive, and shipbuilding, where rapid cutting of thick materials is required.
Water jet cutting in metal fabrication
Water jet cutting utilizes a high-pressure stream of water mixed with abrasive particles to cut through materials. It offers the following advantages:
- Versatility: Water jet cutting can effectively cut through a wide range of materials, including metals, composites, glass, stone, and plastics.
- No heat-affected zone: Water jet cutting is a cold cutting process, eliminating the risk of heat-induced material distortion or warping.
- Ability to cut intricate shapes: Water jet cutting can accurately cut complex shapes and patterns, making it suitable for projects that require high precision.
Water jet cutting is widely used in industries that require intricate and precise cutting, such as aerospace, automotive, and art fabrication.
.