Precision sheet metal fabrication is the process of creating high-quality metal parts with tight tolerances and excellent finishes. One of the most important tools in precision sheet metal fabrication is laser cutting. Laser cutting is a precise and high-quality method used in various industries to cut materials using a laser beam. It offers advantages such as easier work holding, reduced contamination, and minimal warping. Different types of lasers and cutting methods are used, and there are different machine configurations available. Flying optics lasers are the fastest type and do not require material clamping. Laser cutting has high power consumption and efficiency varies depending on the laser type and material being cut. The maximum cutting rate is limited by factors such as laser power and material thickness.
In this article, we will explore the top benefits of laser cutting in precision sheet metal fabrication and provide an overview of the different methods, machine configurations, and services available. We will also discuss safety precautions, maintenance routines, and DIY tips for laser cutting.
Benefits of Laser Cutting in Precision Sheet Metal Fabrication
- What laser cutting is and its advantages over traditional methods
- Types of laser cutting methods and machine configurations
- Power consumption, cutting rate, safety, maintenance, and DIY guide for laser cutting
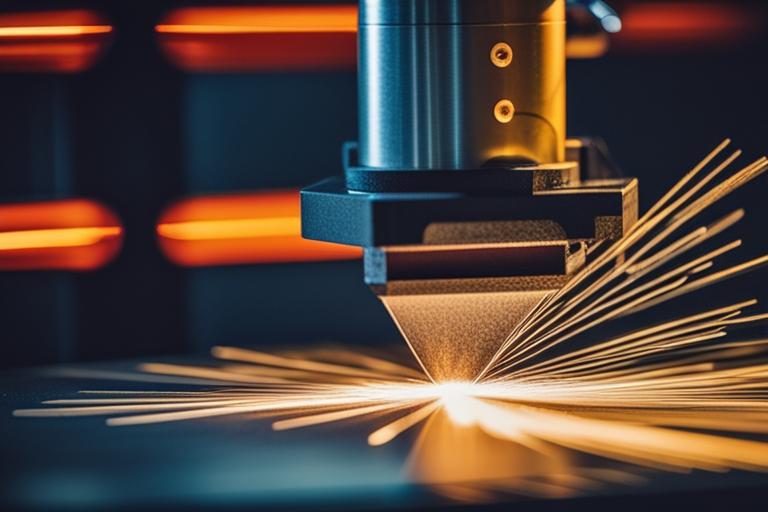
What is Laser Cutting?
Laser cutting is a technology that uses a laser to vaporize materials, resulting in a cut edge. While typically used for industrial manufacturing, it is also starting to be used by schools, small businesses, and hobbyists. It offers advantages over traditional cutting methods such as plasma cutting, waterjet cutting, and mechanical cutting, including the ability to cut complex shapes and intricate designs, excellent precision, and minimal warping.
Brief history of laser cutting technology
The first laser was invented in 1960 by Theodore Maiman, and soon after, laser cutting technology was developed. Initially, CO2 lasers were used for cutting, but in recent years, fiber lasers have become more popular due to their faster cutting speeds, lower power consumption, and more precise cutting capabilities.
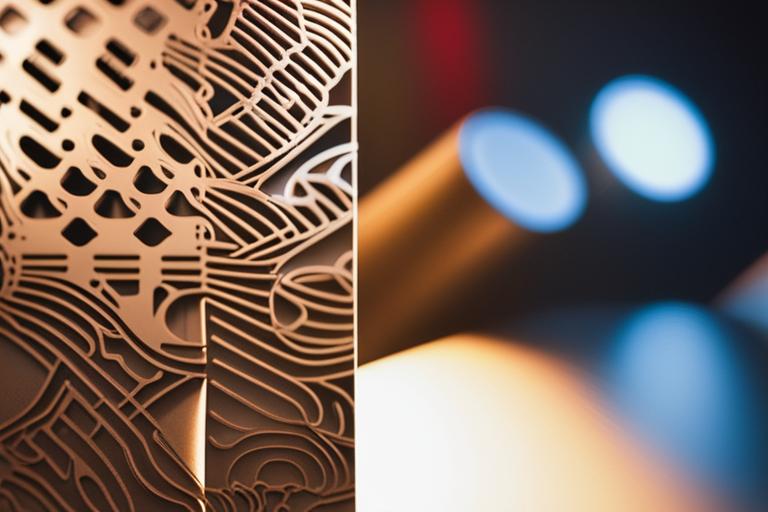
Advantages of laser cutting over traditional cutting methods
One of the main advantages of laser cutting is the precision it offers. Laser cutting machines can cut intricate shapes and designs with high accuracy, making them ideal for precision sheet metal fabrication. Laser cutting also produces a cleaner cut edge with minimal warping, which is important for parts that need to fit together accurately. Additionally, laser cutting is a non-contact process, which means there is little to no tool wear, reducing the need for frequent tool changes and minimizing production downtime.
Types of Laser Cutting Methods
CO2 vs. fiber lasers
CO2 lasers have been used for cutting for several decades and are still popular today. They are the most common type of laser cutting machine and are suitable for cutting a wide range of materials, including metals, plastics, and wood. However, they have some disadvantages, including higher power consumption, lower cutting speeds, and less precise cutting capabilities than fiber lasers.
Fiber lasers, on the other hand, are relatively new to the market but have quickly gained popularity. They use a solid-state laser to generate the laser beam, which is then delivered through a fiber-optic cable to the cutting head. Fiber lasers require less power than CO2 lasers, are more energy-efficient, and have faster cutting speeds. They also offer better cutting precision, making them ideal for precision sheet metal fabrication.
Flying optics vs. fixed optics lasers
Flying optics lasers are the fastest type of laser cutting machine and are ideal for cutting thin materials at high speeds. They do not require material clamping, which makes them more efficient than fixed optics lasers. Fixed optics lasers, on the other hand, are slower but more accurate. They are ideal for cutting thicker materials and can produce cleaner, more precise cuts than flying optics lasers.
Advantages and disadvantages of each method
Each laser cutting method has its own advantages and disadvantages. CO2 lasers are more versatile and can cut a wider range of materials than fiber lasers. However, they are less precise and have slower cutting speeds. Fiber lasers are faster and more precise but are limited in the materials they can cut. Flying optics lasers are the fastest type of laser cutting machine but are not as precise as fixed optics lasers.
Machine Configurations
Flatbed vs. rotary machines
Flatbed laser cutting machines are the most common type and are ideal for cutting flat sheet metal. They use a large, flat cutting bed to hold the material while the laser cuts it. Rotary laser cutting machines, on the other hand, are designed for cutting tube and pipe. They use a rotating cutting head to cut the material, which allows for more complex shapes and designs to be cut.
Differences between the two configurations
The main difference between flatbed and rotary laser cutting machines is the type of material they can cut. Flatbed machines are designed for cutting flat sheet metal, while rotary machines are designed for cutting tube and pipe. They also differ in the way they hold the material while cutting. Flatbed machines use a large cutting bed, while rotary machines use a rotating cutting head.
Which configuration is best suited for different types of sheet metal cutting
Choosing the right machine configuration depends on the type of sheet metal cutting required. Flatbed machines are ideal for cutting flat sheet metal, while rotary machines are better suited for cutting tube and pipe. For precision sheet metal fabrication, flatbed machines are the most commonly used.
Power Consumption and Efficiency
How power consumption affects the cost and efficiency of the laser cutting process
Power consumption is a major factor in the cost and efficiency of the laser cutting process. CO2 lasers require more power than fiber lasers, which means they are less energy-efficient and more expensive to operate. However, they are more versatile and can cut a wider range of materials. Fiber lasers, on the other hand, require less power and are more energy-efficient, but are limited in the materials they can cut.
Efficiency of different laser types
The efficiency of different laser types varies depending on the material being cut and the type of laser used. CO2 lasers are less efficient than fiber lasers, but are more versatile. Fiber lasers are more efficient and faster than CO2 lasers, but are limited in the materials they can cut.
How to optimize power consumption and efficiency
To optimize power consumption and efficiency, it is important to choose the right laser type for the material being cut. CO2 lasers are ideal for cutting thicker materials, while fiber lasers are better suited for cutting thinner materials. Additionally, it is important to maintain the laser cutting machine regularly to ensure it is operating at peak efficiency.
Maximum Cutting Rate
Factors that affect the maximum cutting rate
The maximum cutting rate is affected by several factors, including laser power, material thickness, cutting speed, and the type of laser used. CO2 lasers have a slower cutting speed than fiber lasers, which means they have a lower maximum cutting rate. Thicker materials also require more laser power, which can affect the cutting rate.
How to calculate maximum cutting rate
The maximum cutting rate can be calculated by dividing the thickness of the material being cut by the cutting speed of the laser. This will give you the maximum cutting rate for that material.
How to optimize cutting speed without compromising quality
To optimize cutting speed without compromising quality, it is important to choose the right laser type and power level for the material being cut. Additionally, it is important to adjust the cutting speed based on the thickness of the material. Thinner materials can be cut at higher speeds, while thicker materials require slower cutting speeds to ensure a clean cut.
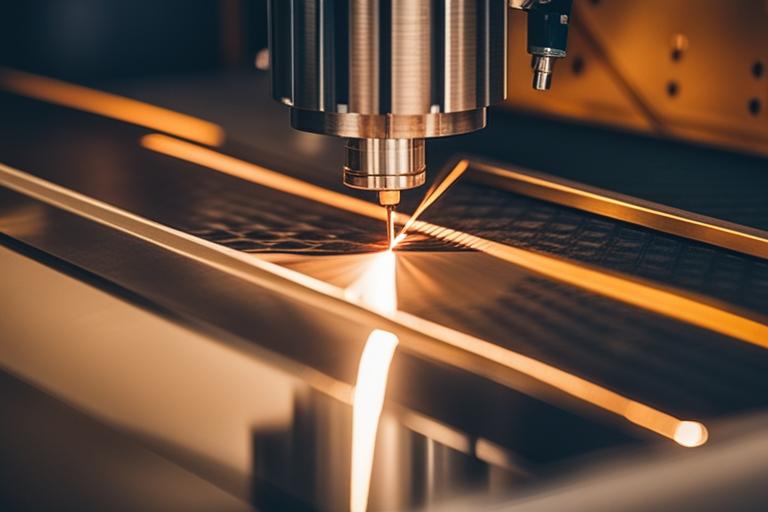
Laser Cutting Services
Overview of some of the most reputable and experienced companies in the field
There are several reputable and experienced laser cutting companies in the field, including Ponoko, The Laser Cutting Company, and Xometry. These companies offer a range of services, including laser cutting, forming, and prototyping.
Services offered by laser cutting companies
Laser cutting companies offer a range of services, including laser cutting, forming, and prototyping. They can cut a wide range of materials, including metals, plastics, and wood. They also offer different machine configurations, such as flatbed and rotary machines, to accommodate different types of sheet metal cutting.
How to choose the right laser cutting service
When choosing a laser cutting service, it is important to consider factors such as the company’s experience, reputation, and range of services offered. It is also important to consider the type of material being cut and the machine configuration required for the job.
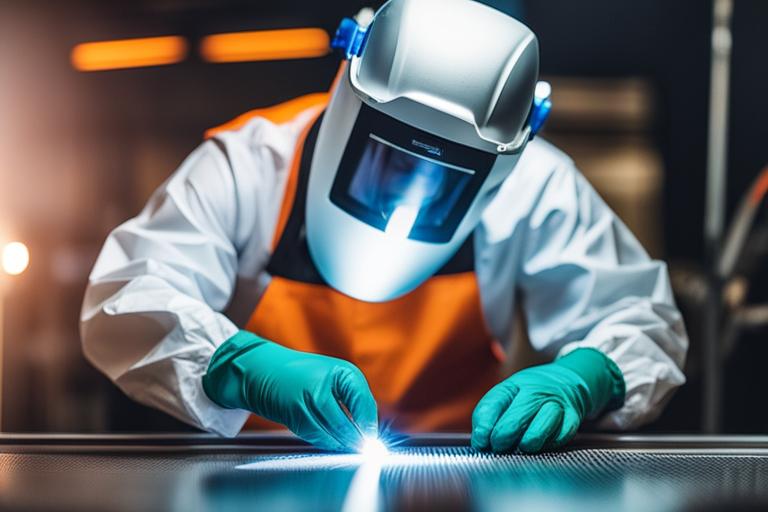
Laser Cutting Safety
Safety precautions when operating laser cutting machines
Laser cutting machines can be dangerous if proper safety precautions are not taken. It is important to wear appropriate personal protective equipment (PPE), such as safety glasses and gloves, when operating a laser cutting machine. It is also important to follow all safety guidelines and procedures provided by the manufacturer.
Types of personal protective equipment (PPE) required
The types of PPE required when operating a laser cutting machine include safety glasses, gloves, and a face shield. It is important to choose PPE that is appropriate for the specific laser cutting machine being used.
How to handle hazardous materials
Some materials used in laser cutting can be hazardous, such as metals containing lead or cadmium. It is important to handle these materials with care and follow all safety guidelines and procedures when handling and disposing of them.
Laser Cutting Maintenance
Regular maintenance routines for laser cutting machines
Regular maintenance is important for keeping laser cutting machines in good working condition. It is important to clean the machine regularly and replace any worn or damaged parts. Additionally, it is important to perform regular inspections to ensure the machine is functioning properly.
Tips for keeping machines in good working condition
To keep laser cutting machines in good working condition, it is important to perform regular maintenance and cleaning. It is also important to follow all manufacturer guidelines and procedures for operating and maintaining the machine.
Troubleshooting common problems
Common problems with laser cutting machines include poor cutting quality, material warping, and machine malfunctions. It is important to troubleshoot these problems as soon as they arise to prevent production downtime and ensure the machine is operating at peak efficiency.
Case Study: Increased Precision and Efficiency with Laser Cutting
When John started his sheet metal fabrication business, he relied on traditional cutting methods like saws and plasma cutters. But as his business grew, he started to encounter problems with precision and efficiency. The saws left rough edges and the plasma cutters produced too much heat, warping the metal.
He decided to invest in a laser cutting machine and was amazed at the difference it made. With the laser cutter, he was able to achieve much higher precision and accuracy, with clean edges that required minimal finishing. The laser cutting process also produced less waste and used less energy, making it more efficient and cost-effective in the long run.
One project in particular stands out in John’s mind. A client needed a complex bracket made out of stainless steel, with a tight tolerance of only 0.005 inches. With traditional cutting methods, this would have been a difficult and time-consuming task. But with the laser cutter, John was able to produce the bracket quickly and accurately, meeting the client’s specifications without any issues.
Overall, John has found that laser cutting has transformed his business, allowing him to take on more complex projects with greater efficiency and precision. He recommends it to anyone looking to improve their sheet metal fabrication process.
DIY Guide for Laser Cutting
Overview of the settings involved in laser cutting
The settings involved in laser cutting include power, speed, frequency, and resolution. These settings can be adjusted to achieve successful cuts without damaging the material.
Importance of adjusting settings based on the material being cut
It is important to adjust the laser cutting settings based on the material being cut to ensure a clean cut without damaging the material.
Tips for successful DIY laser cutting
To achieve successful DIY laser cutting, it is important to choose the right laser type and power level for the material being cut. It is also important to adjust the cutting speed and other settings based on the material being cut.
.
Questions
Who uses laser cutting in sheet metal fabrication?
Manufacturers, engineers and designers.
What type of metals can be laser cut?
Steel, stainless steel, aluminum, copper, and brass.
How precise is laser cutting in sheet metal fabrication?
Laser cutting is extremely precise, with tolerances of +/- 0.005 inches.
What is the advantage of using laser cutting over traditional cutting methods?
Laser cutting provides a clean, precise cut with minimal distortion and no tool wear.
How does laser cutting handle complex designs?
Laser cutting can handle intricate designs and shapes with ease.
What if I need a large quantity of parts?
Laser cutting is a cost-effective solution for large production runs.