In the world of manufacturing, efficiency is the name of the game. The ability to streamline processes, reduce wasted resources, and enhance productivity has become the holy grail for manufacturers seeking a competitive edge. One method that has gained prominence in recent years is Lean Manufacturing, which emphasizes continuous improvement and waste reduction.
This four-article series delves into Atlas Manufacturing’s journey from “Hidden” Lean to “Visual” Lean, shedding light on the practical application of the 5S methodology — Sort, Set in order, Shine, Standardize, and Sustain. We will unveil the substantial improvements in efficiency, safety, and productivity through four key operational enhancements: the adoption of sheet metal storage racks, a custom library tool tree, tooling shadow boards, and top shelf tool systems. Today, we begin with part 1: sheet metal storage racks.
Lean Manufacturing and the 5S Methodology
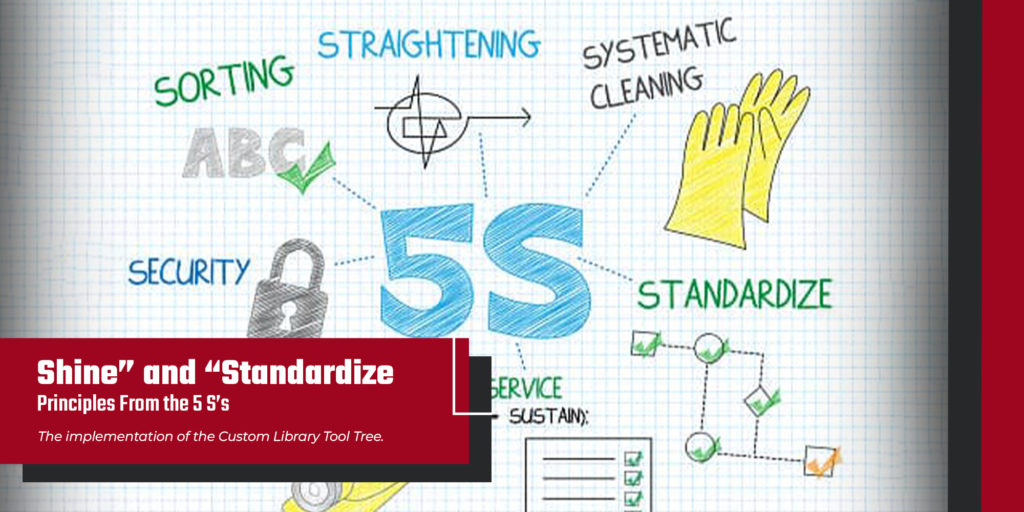
Lean Manufacturing has been hailed as a game-changer in the competitive manufacturing industry, where every second counts and efficiency is the key to success. Lean principles, originally derived from the Toyota Production System (TPS), have found application in various industries, from automotive to healthcare, aiming to maximize value for customers while minimizing waste.
At the core of Lean management systems is a set of principles and practices that emphasize continuous improvement, streamlined processes, and waste reduction: 5S methodology. This Lean thinking framework provides a structured approach to workplace organization and improvement. The 5S methodology consists of five key principles, each contributing to creating a workspace that is organized, efficient, and conducive to productivity. These principles are: Sort, Set in Order, Shine, Standardize, and Sustain.
Sort and Set in Order: The Pillars of Organization
Sort
The first step, Sort, emphasizes eliminating waste, unnecessary items, and clutter from the workplace. This process encourages employees to identify waste and what is essential for their work and remove anything that does not contribute to efficiency or value.
Set in Order
Once the unnecessary items are removed, the focus shifts to organizing the essential elements. This scientific management involves establishing designated storage spaces for tools, equipment, and materials, ensuring quick and easy access. Setting items in order minimizes search times, prevents misplacements, and enhances overall workspace organization in Lean manufacturing plants.
The first two principles, Sort and Set in order, lay the foundation for a more organized and efficient workspace, setting the stage for enhanced productivity.
The Old System: Sheet Metal Stacks on the Floor
Before Atlas Manufacturing embraced Lean methods and adopted the 5S methodology, our sheet metal storage system left much to be desired. Like many traditional manufacturing facilities, sheet metal was stored in stacks on the floor, a system that was plagued by numerous issues that hampered efficiency and posed safety concerns.
Clutter
With sheet metal strewn across the factory floor, locating the specific material needed for a job was challenging. Operators often spent valuable time rummaging through the stacks, leading to delays in production processes and decreased productivity. The lack of organization resulted in an environment filled with clutter, making it difficult for workers to move freely and safely within the workspace.
Safety Hazards
Safety was another major concern with this old storage system. Stacks of sheet metal posed the risk of accidents, such as trips, slips, and falls. Moreover, improperly stored materials could become damaged or distorted, leading to waste and additional costs.
Inefficient Space Utilization
The floor-based storage system also squandered valuable floor space that could have been used for other productive purposes, which limited the layout possibilities within the factory, preventing the company from optimizing the floor plan for more efficient workflows.
Transition to SteelStack Sheet Metal Storage Racks
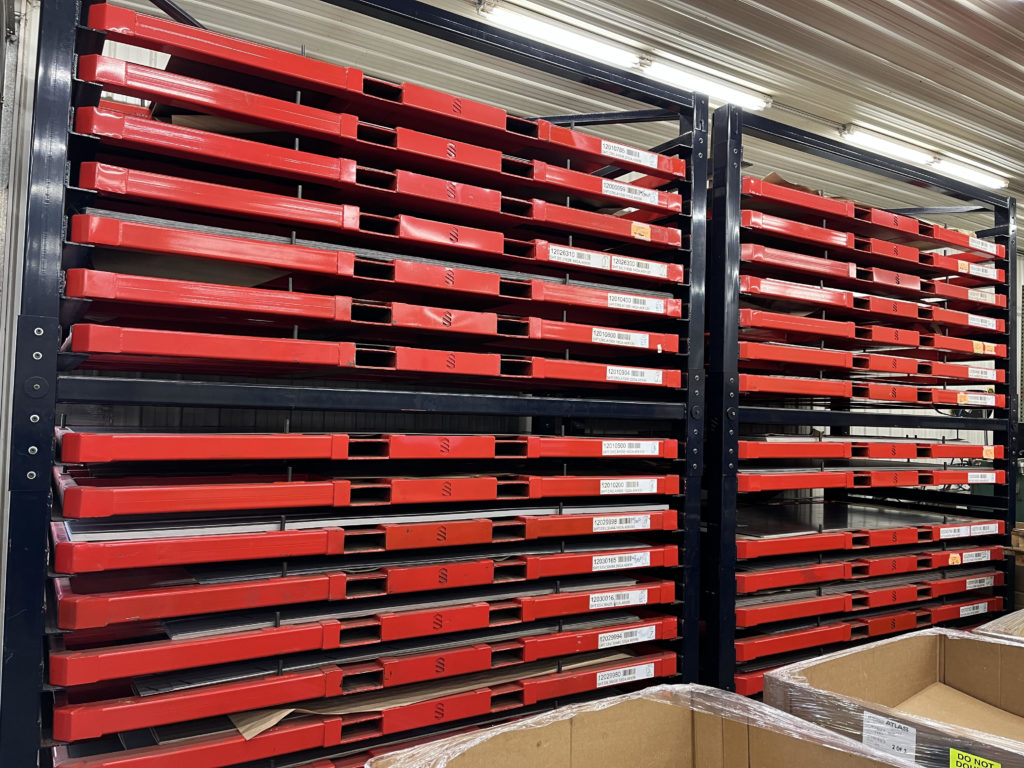
After realizing that our sheet metal storage system was in dire need of an upgrade, we turned to the principles of Lean Manufacturing for guidance. The answer to our problems came in the form of SteelStack sheet metal storage racks — a transformation representing a shift from chaos to order, from inefficiency to productivity.
Benefits of SteelStack Sheet Metal Storage Racks
Speed in Locating the Correct Sheet Metal
With the new storage racks, sheet metal was no longer strewn across the factory floor. Instead, sheets found a designated place on the shelves, organized by type and size. This meant operators could swiftly locate the specific sheet metal needed, reducing search times and streamlining productive processes.
Ease of Access for Operators
The sheet metal storage racks were designed to be accessible. Operators could now access the material without straining or engaging in potentially hazardous actions. Removing sheet metal stacks from the floor also reduced the risk of accidents, and the racks provided a safer and more organized storage solution, ensuring that materials were stored securely and operators were out of harm’s way.
Reduced Clutter Leading to Increased Production Speeds
By utilizing vertical space with the racks, we were able to eliminate waste and make the most of the available floor space, allowing us to reconfigure our factory layout for better workflow and optimization of the production process. A clean, organized workspace fosters a more efficient work environment, increasing productivity.
Final Thoughts
The transformation from an old, inefficient sheet metal storage system to SteelStack sheet metal storage racks marked the beginning of Atlas Manufacturing’s journey toward a ‘Visual’ Lean production system. The principles of Sort and Set in order were put into action, resulting in a more organized, efficient, and safe workspace. The benefits of this transition were evident in speed, accessibility, reduced clutter, and improved safety.
In the next part of our series, we will delve into implementing a custom library tool tree, another crucial element in Atlas Manufacturing’s evolution towards a Lean, efficient, and visually organized manufacturing process. Stay tuned as we continue to explore the practical application of Lean principles and the 5S methodology, shedding light on the remarkable improvements these changes have brought to the world of sheet metal manufacturing.