Introduction
Atlas Manufacturing, a leader in precision fabricated solutions, recently had the opportunity to showcase its advanced manufacturing processes in an insightful interview conducted by Bystronic, a global provider of high-quality solutions for the sheet metal processing business. The interview, held at Atlas Manufacturing’s facility in Chippewa Falls, Wisconsin, and their Minneapolis, Minnesota location, highlighted the significant improvements brought by Bystronic’s technology to Atlas’s operations.
The Challenge Atlas Faced
Patrick Rufledt, the Plant Manager of Atlas Manufacturing, opened the discussion by outlining the diverse industries served by Atlas, ranging from OEM fabrication and medical equipment to high-performance computer components and cooling fan housings. Despite their wide-ranging expertise, Atlas faced a critical challenge: their press brake operation was a bottleneck, especially as experienced employees from the brake department were retiring. They needed a solution to capture this ‘tribal knowledge’ and efficiently train new employees.
Bystronic’s Role in Transforming Atlas’s Operations
Bystronic emerged as the solution provider with their robust and intuitive software that matched Atlas’s brake tool library. This partnership was critical for Atlas in minimizing tool setups, thereby increasing production efficiency with minimal effort required from the press brake operators.
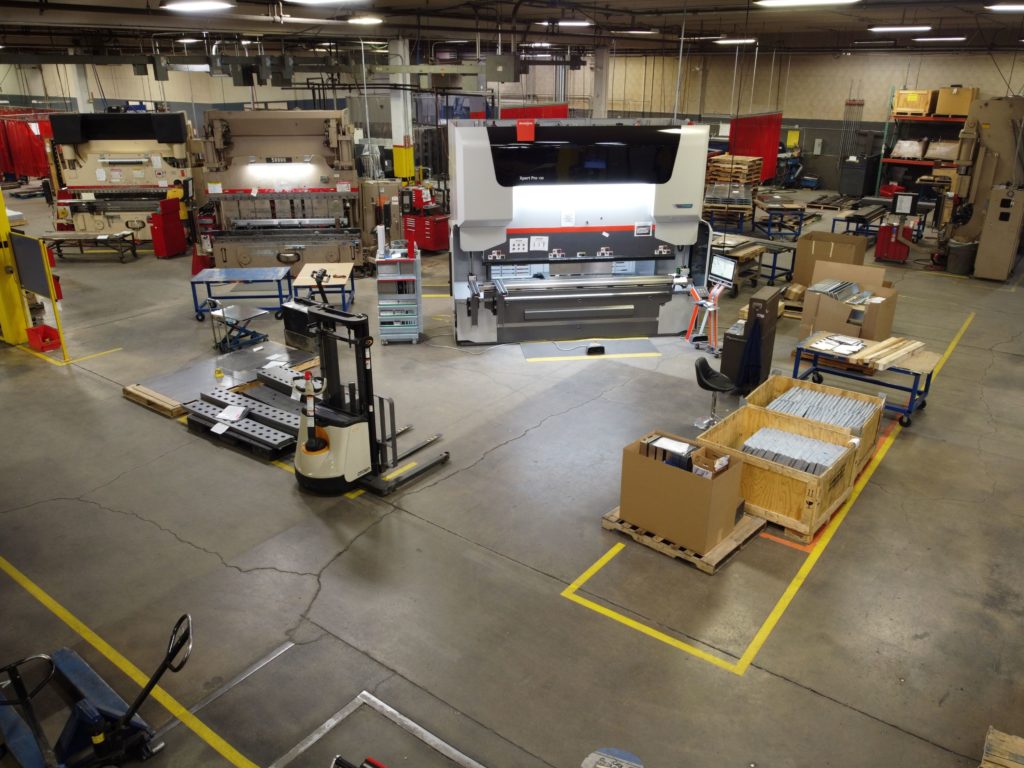
Results and Improvements
The impact of Bystronic’s technology on Atlas’s operations was significant. With Bystronic’s bisoft CAM software, operators, even those without prior CNC experience, could quickly learn to make complex brake parts. This ease of operation, likened to using a smartphone, enabled Atlas to bring in a younger, more computer-savvy generation into their workforce. The results were impressive – a 30% increase in efficiency and a tripling of capacity since installing Bystronic brakes and a fiber laser.
Moreover, Atlas leveraged the synergy of coupling some of their brakes with Bystronic’s mobile bending robot, further enhancing their production capabilities.
Customer Service and Support
The collaboration went beyond just the installation of equipment. Bystronic’s team was lauded for their helpful approach in resolving issues, keeping Atlas informed, and ensuring minimal downtime. This level of support is crucial in maintaining high productivity and operational efficiency.
Enhancing Efficiency with the Top Shelf Tool Systems Tool Tower
In addition to the advancements brought by Bystronic’s technology, Atlas Manufacturing has further optimized their operations with the use of the Top Shelf Tool Systems Tool Tower. This innovative tool storage system, proudly made by Atlas, is designed to enhance shop organization and efficiency. The Tool Tower serves as a mobile, user-friendly storage solution for press brake tooling, offering visual access to all tools and significantly improving job efficiency. Its design is particularly beneficial for storing RFA and Wila/Trumpf press brake tooling, ensuring tools are easily accessible and identifiable. The integration of the Tool Tower into Atlas Manufacturing’s workflow demonstrates their commitment to utilizing top-tier equipment to maximize productivity and streamline operations. To explore more about the Tool Tower and its features, visit Top Shelf Tool Systems.
Conclusion
The interview with Bystronic not only highlighted the technological advancements at Atlas Manufacturing but also underscored the importance of selecting the right partners in business. Bystronic’s solutions have not only alleviated a key bottleneck at Atlas but have also positioned them for future growth and innovation. This partnership is a testament to how the right technology, when applied thoughtfully, can lead to remarkable improvements in manufacturing efficiency and capacity.
For more insights into how Atlas Manufacturing is leveraging technology for innovative solutions, watch the full interview here. Interested in learning more about our services? Contact Atlas Manufacturing today!