Let’s cut right to the chase: When it comes to electrical enclosure manufacturers, the market is as varied as it is dense. But here’s the unvarnished truth – not all manufacturers are created equal. As someone who has navigated the choppy waters of precision sheet metal fabrication, I’ve seen firsthand the staggering difference between run-of-the-mill providers and those that truly stand out. Among these, Atlas Manufacturing has etched a name that resonates with reliability and quality in the custom electrical enclosure space.
What You’ll Learn About Electrical Enclosure Manufacturers
- Different types of electrical enclosures include NEMA 1, 3R, 4, 4X, 12, and 13.
- Materials used for electrical enclosures include carbon steel, stainless steel, and aluminum.
- Electrical enclosure accessories may include back panels, mounting feet, subpanels, disconnects, window kits, breather drains, vents, rain hoods, and sun shields.
Electrical Enclosures
When we talk about electrical enclosures, we’re not just discussing metal boxes. These are the sentinels that protect electrical components from dust, water, and unauthorized fingers. With years of experience under my belt, I’ve learned that a well-crafted enclosure can be the difference between a smoothly running system and a disaster waiting to happen. It’s the same reason why companies like Atlas Manufacturing don’t just produce; they innovate and tailor solutions that fit like a glove.
Electrical Enclosure Types
Delving into the types of electrical enclosures, we find ourselves amidst a landscape of specifications and standards. It’s a world where one size does not fit all, and where the NEMA ratings dictate the level of protection your components will receive.
NEMA 1 Enclosures
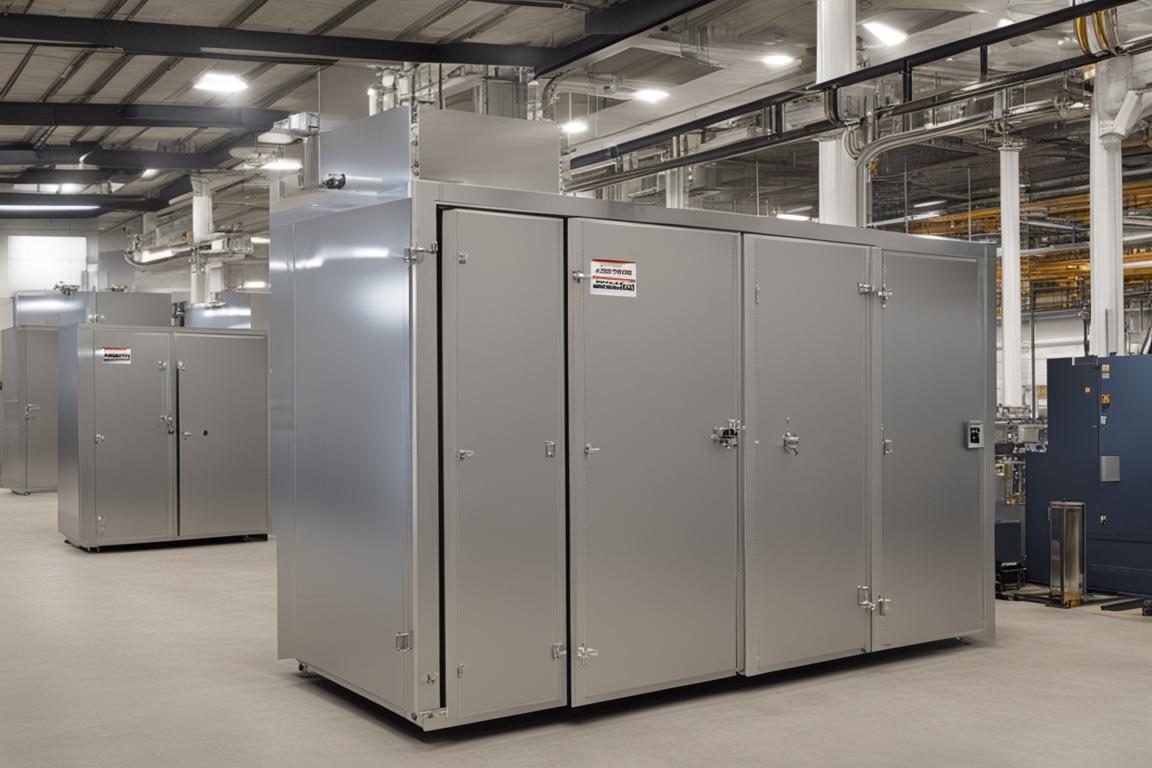
NEMA 1 enclosures are the basic, no-frills guardians of indoor equipment. Designed to prevent contact with live components and to keep out a certain degree of dust, they are your entry-level defense. I recall a project where a client underestimated their need and opted for NEMA 1, only to realize their facility required a more robust solution. It was an expensive lesson in understanding the nuances of NEMA ratings.
NEMA 3R Enclosures
The step-up to NEMA 3R enclosures brings added protection against the elements, making them suitable for outdoor use. They’re engineered to withstand rain, sleet, and even the formation of ice on the enclosure’s exterior. I’ve watched these enclosures stand resilient in the face of harsh Minnesota winters, a testament to their design.
NEMA 4 Enclosures
Transitioning to NEMA 4 enclosures, we’re talking about watertight fortresses. They’re built to handle not just rain but hose-directed water, making them ideal for washdown areas in food and beverage facilities. I’ve seen these enclosures shine in seafood processing plants, where saltwater and high-pressure cleaning are daily occurrences.
NEMA 4X Enclosures
NEMA 4X takes it further, offering corrosion resistance alongside the waterproof capabilities. This variant is often crafted from stainless steel, standing up to corrosive environments like chemical plants. I once witnessed a NEMA 4X enclosure emerge unscathed from a chemical spill that would have otherwise spelled disaster.
NEMA 12 Enclosures
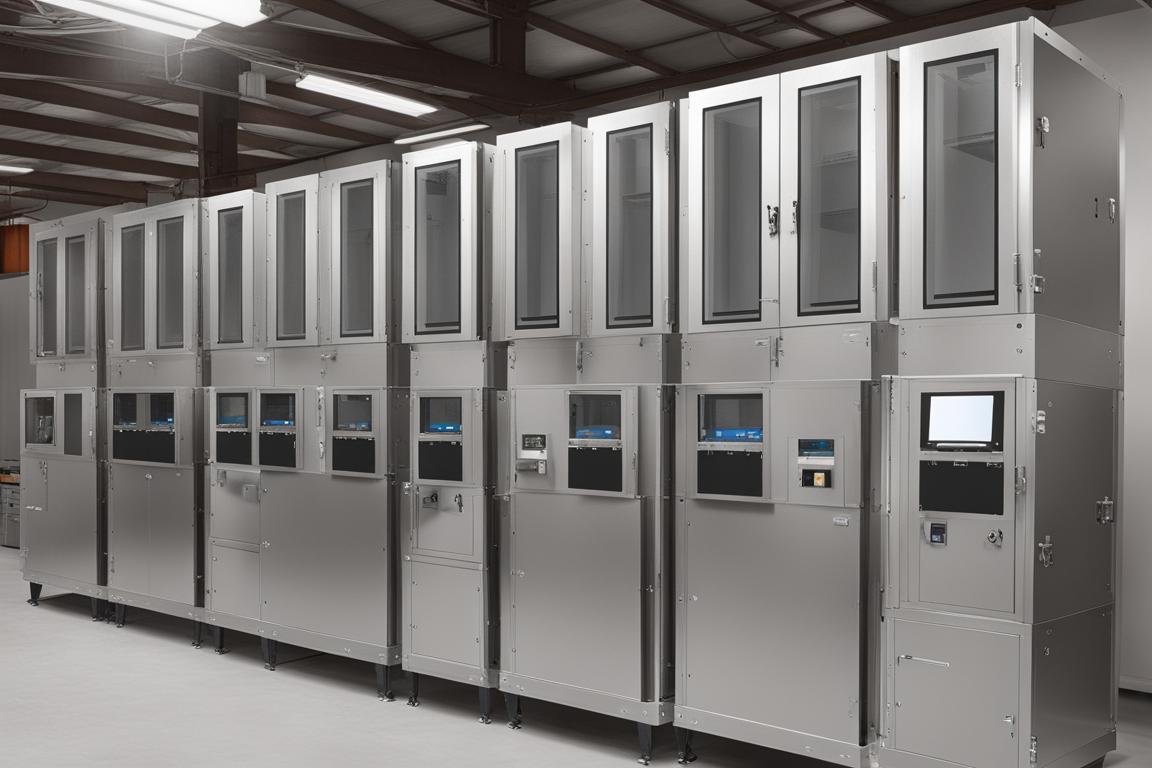
For industrial settings laden with oil and dust, NEMA 12 enclosures are the go-to. They offer protection from these contaminants, ensuring that the enclosures do their job without interruption. I remember a factory floor so thick with airborne particles that you could taste the dust, but the NEMA 12 enclosures installed there just kept on ticking.
NEMA 13 Enclosures
Lastly, NEMA 13 enclosures bring it home with protection against dust, spraying of water, oil, and non-corrosive coolants. It’s an all-rounder that I’ve recommended time and again for clients in machining and manufacturing environments.
Electrical Enclosure Materials
The core of any enclosure’s resilience lies in its material. The choice of metal not only determines the enclosure’s durability but also its suitability for certain environments.
Carbon Steel Electrical Enclosures
Carbon steel enclosures serve as the sturdy backbone for countless applications. Their strength is unparalleled, making them a common sight in general industrial environments. I’ve hammered, drilled, and cut into this material, and each time I’m reminded of its unyielding nature.
Stainless Steel Electrical Enclosures
For environments where cleanliness and corrosion resistance are paramount, stainless steel enclosures are the shining knights. Their gleaming surfaces are not just for show; they resist oxidation and can be sanitized to meet stringent hygiene standards. In the medical field, stainless steel is as ubiquitous as the white coat.
Aluminum Electrical Enclosures
Aluminum enclosures, on the other hand, offer a lightweight yet robust alternative. They’re a dream to work with, being easy to modify and resistant to corrosion. I’ve often recommended them for marine applications where their rust-resistant properties and lighter weight give them the edge.
Electrical Enclosure Accessories
An enclosure is more than its shell; the accessories can make or break its functionality.
Back Panels
Back panels are the unsung heroes, providing a sturdy mounting surface for components within the enclosure. I’ve seen panels so meticulously organized they could pass for modern art.
Mounting Feet
Mounting feet may seem trivial, but they’re essential for securing enclosures to various surfaces. A solid installation can resist vibrations that would otherwise rattle lesser enclosures apart.
Subpanels
Subpanels divide the interior space, allowing for better organization and component segregation. It’s a feature that I’ve found invaluable when dealing with complex wiring and multiple circuit assemblies.
Disconnects and Handles
Disconnects and handles offer an added layer of safety and convenience, ensuring that power can be cut swiftly and that the enclosures are accessible when necessary. I’ve personally felt the relief that comes with an easily accessible disconnect during an emergency shutdown.
Window Kits
Window kits allow for visual inspections without exposing the enclosure’s contents to external factors. It’s an elegant solution to maintain protection while still keeping an eye on the components inside.
Breather Drains and Vents
Breather drains and vents are critical in maintaining the internal pressure and moisture levels, preventing condensation that could lead to electrical faults. I’ve seen equipment saved by these seemingly minor components during sudden temperature changes.
Rain Hoods and Sun Shields
And don’t get me started on rain hoods and sun shields. These accessories protect against environmental factors that could otherwise lead to overheating or water ingress. They are, quite literally, the enclosure’s first line of defense.
Custom Electrical Enclosures
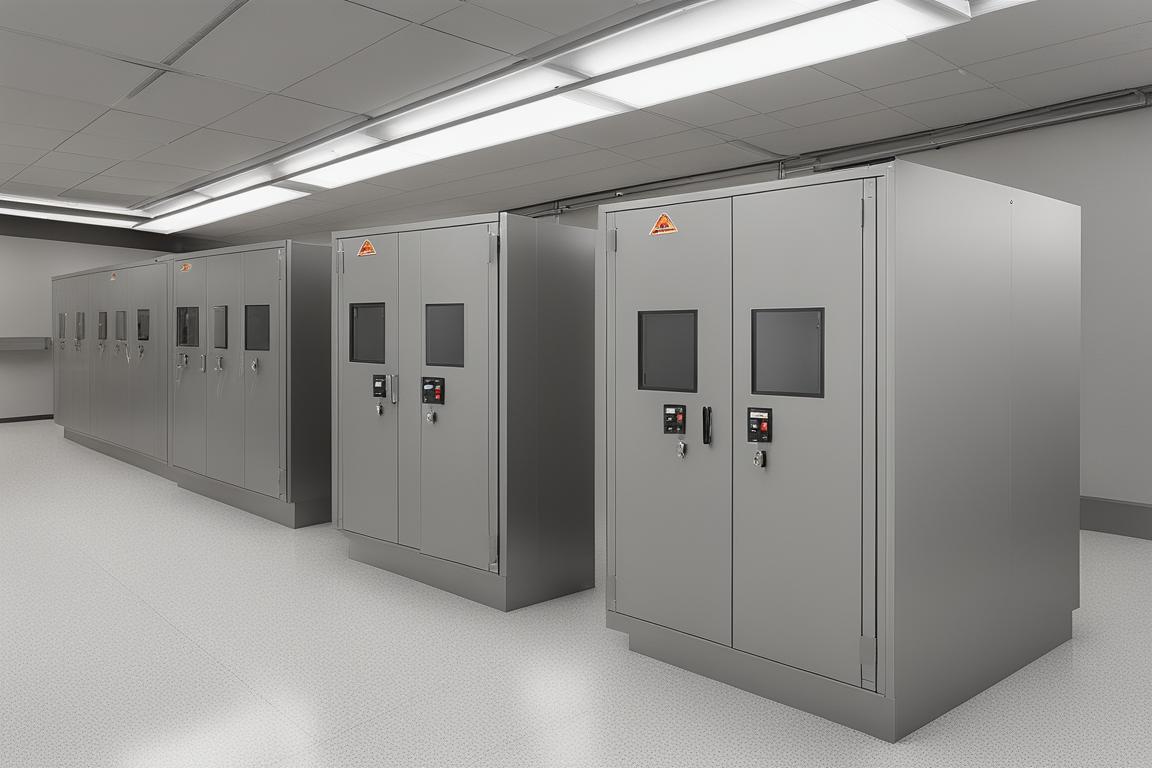
Now, let’s talk about the pièce de résistance: custom electrical enclosures. This is where precision sheet metal fabrication shines, and where manufacturers like Atlas Manufacturing distinguish themselves. Customization is not just about dimensions; it’s about understanding the unique challenges and requirements of each application.
Insider Tip: When considering a custom solution, always discuss the environment and specific use-case with the manufacturer. It’s the details that dictate the difference between a standard solution and a custom-fit masterpiece.
In my career, I’ve witnessed the rise of bespoke solutions that cater to the increasingly complex demands of industries. From bespoke dimensions that fit into odd spaces to specialized cutouts for unique interfaces, these custom enclosures embody the convergence of form and function.
Insider Tip: Don’t overlook the finish and aesthetics of your enclosure. In customer-facing environments, the enclosure can contribute to the overall perception of quality and attention to detail.
I’ve shared countless handshakes over enclosures that not only met the technical specifications but also elevated the look and feel of the equipment they housed. It’s a testament to the craftsmanship that can, and should, go into every custom enclosure.
In conclusion, the world of electrical enclosures is vast and varied. But the true measure of a manufacturer isn’t just in their ability to produce; it’s in their capacity to understand and deliver on the unique needs of their clients. The custom electrical enclosures from Atlas Manufacturing are not just products; they are the culmination of expertise, experience, and a keen understanding of what it means to protect and serve the heart of electrical systems.
Questions & Answers
Q: Who are some top electrical enclosure manufacturers?
A: Some top electrical enclosure manufacturers include Hammond Manufacturing, Hoffman, and Rittal.
Q: What is precision sheet metal fabrication?
A: Precision sheet metal fabrication is the process of cutting, bending, and assembling sheet metal to create precise and complex parts.
Q: How do electrical enclosure manufacturers ensure quality?
A: They ensure quality through rigorous testing, adherence to industry standards, and using high-quality materials and fabrication processes.
Q: Who should consider precision sheet metal fabrication?
A: Companies in industries such as electronics, telecommunications, and renewable energy can benefit from precision sheet metal fabrication.
Q: What are the advantages of custom electrical enclosures?
A: Custom electrical enclosures can be tailored to specific needs, offer better fit and function, and can optimize space and functionality.
Q: How do electrical enclosure manufacturers address unique requirements?
A: Manufacturers have the capability to work closely with clients to design and fabricate custom enclosures that meet unique specifications and needs.