Atlas has been using laser cutters since 1993 and now has entered the third generation of technology since installing their first laser. Laser cutting technology continues to evolve as new sources are developed for beam generation and delivery. The evolution has resulted in improved cut quality and speed.
What matters the most are the cost and quality of the cut. Everything else is marketing and packaging. Our customers are concerned about delivered cost of a high-quality part. Using a comprehensive 22-point evaluation system and time studies of 4 different part nests, 10 different laser models were rigorously analyzed. The result: A Trumpf laser was selected as the best match to our customer’s needs.
Over the next six months, Atlas is installing a fully automated 40 shelf tower system with material handling carts that will deliver flat sheet to either the high speed TruPunch 5000 punching machine or the laser. Cut or punched parts are automatically removed from the machines during continuous processing of flat sheets. This investment allows Atlas to run 24 x 7 continuously processing sheet into punched or laser cuts parts.
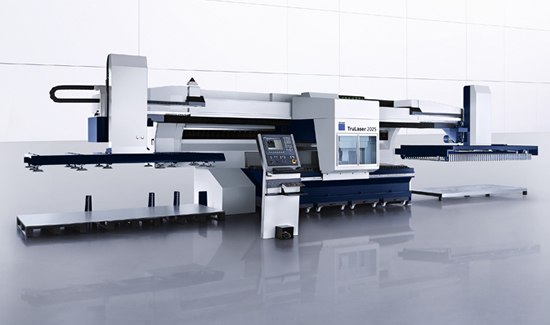