Learn about Precision Sheet Metal Fabrication
- Definition, significance, and common applications of sheet metal fabrication.
- Types of sheet metal, cutting techniques, bending and forming processes, welding and joining methods, surface finishing, quality control, design considerations, applications, advances, choosing a fabrication partner, and future trends in sheet metal fabrication.
- Importance of precision, strength, durability, compliance, and sustainability in sheet metal fabrication.
Sheet metal fabrication, a crucial process in the manufacturing industry, involves manipulating sheet metal to create various components and products. How does sheet metal fabrication play a vital role in precision engineering and manufacturing industries?
Definition and Significance
Sheet metal fabrication refers to the process of cutting, bending, and assembling metal sheets to form a final product. It involves a range of techniques to transform flat metal sheets into complex structures, making it an essential part of manufacturing in numerous industries.
Importance in Precision Engineering Industry
In the precision engineering industry, where accuracy and quality are paramount, sheet metal fabrication is indispensable. The ability to achieve tight tolerances and intricate designs makes it a preferred method for producing components that demand high precision and consistency.
Common Applications
The applications of sheet metal fabrication are extensive, spanning across various industries. From producing intricate aircraft components in aerospace to creating durable and lightweight car bodies in automotive manufacturing, the versatility of sheet metal fabrication is evident.
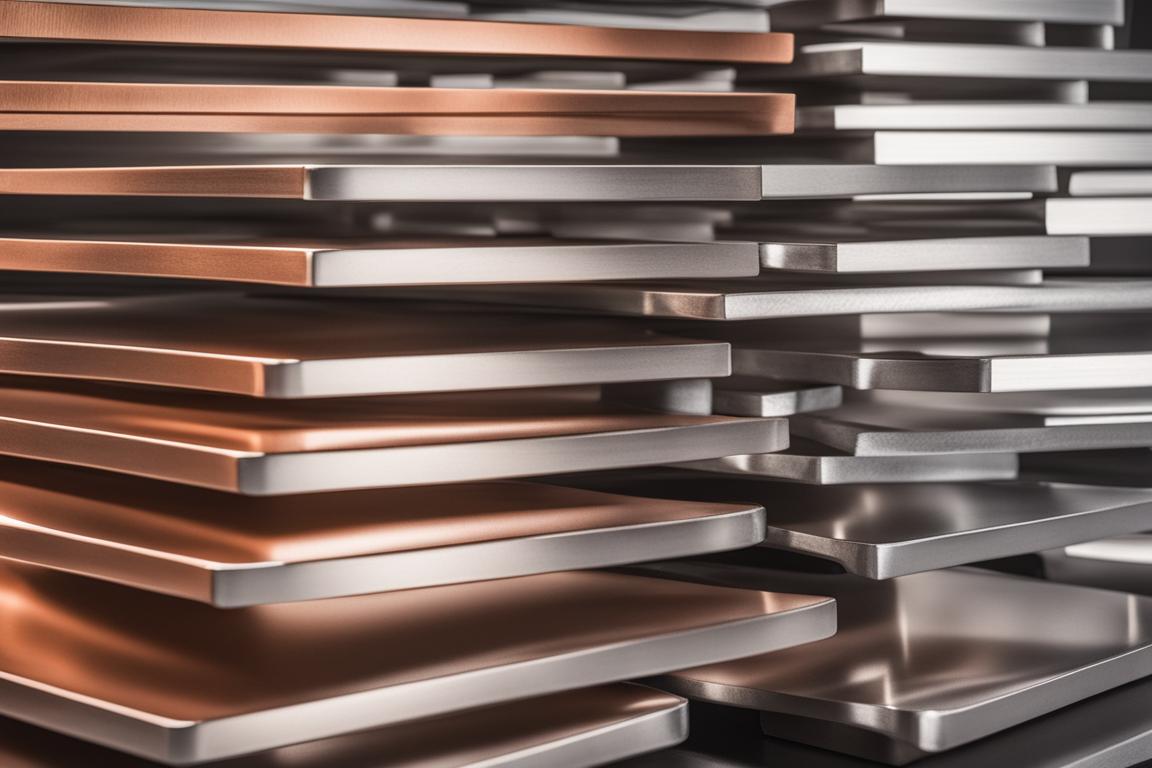
Types of Sheet Metal
Sheet metal comes in various types and alloys, each with unique properties and applications. Understanding the characteristics of different types of sheet metal is crucial for selecting the right material for a specific application.
Stainless Steel
Stainless steel is a popular choice for sheet metal fabrication due to its corrosion resistance, strength, and aesthetic appeal. Its versatility makes it suitable for a wide range of applications, including kitchen appliances, medical equipment, and architectural elements.
Aluminum
Aluminum sheet metal is known for its lightweight nature, making it ideal for applications where weight reduction is critical. It finds extensive use in the aerospace industry, automotive components, and consumer electronics.
Copper
Copper sheet metal boasts excellent electrical conductivity and is often used in electrical components, roofing, and decorative elements due to its distinctive appearance and malleability.
Other Alloys
Beyond stainless steel, aluminum, and copper, various other alloys such as titanium, brass, and nickel can be employed for specific applications based on their unique properties.
Properties and Applications
Each type of sheet metal possesses distinct properties that make it suitable for particular applications. These properties include strength, corrosion resistance, conductivity, and formability, among others.
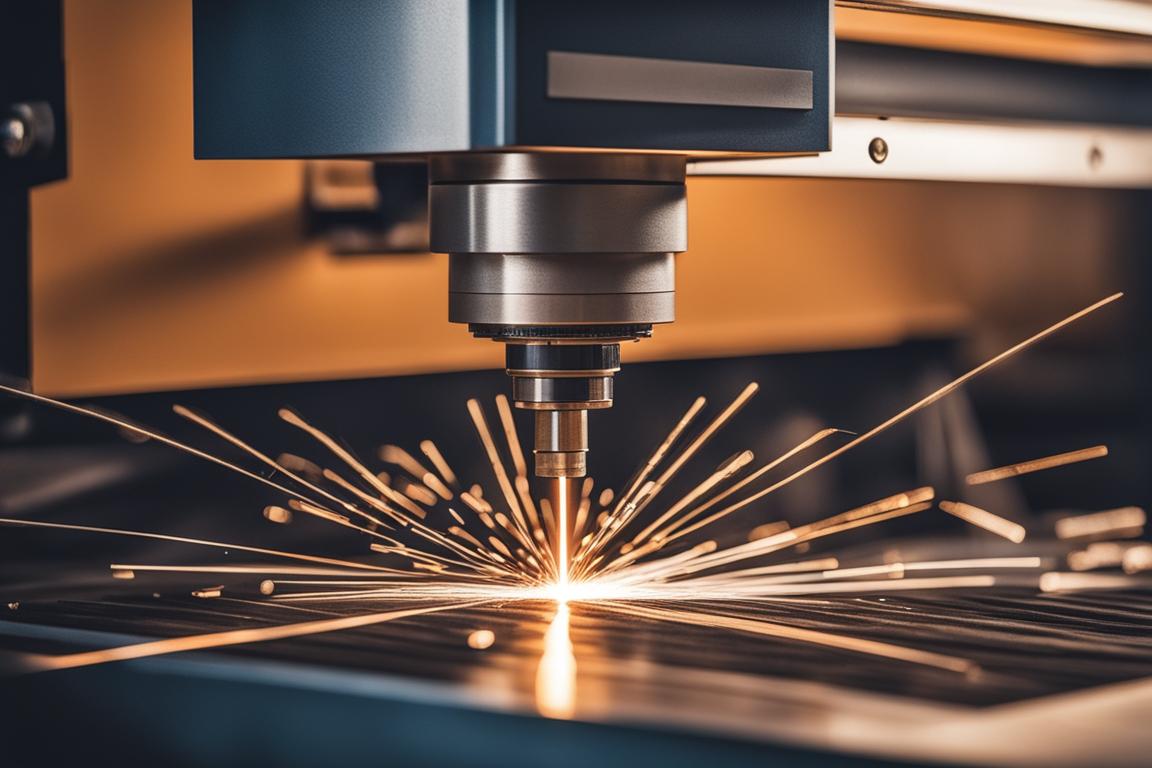
Sheet Metal Cutting Techniques
The cutting of sheet metal is a fundamental step in the fabrication process, and various cutting techniques are employed to achieve precise and accurate results.
Laser Cutting
Laser cutting is a highly precise and efficient method that uses a focused laser beam to cut through the metal sheet. It is favored for its ability to produce intricate designs with minimal material waste.
Water Jet Cutting
Water jet cutting involves the use of a high-pressure jet of water mixed with an abrasive substance to cut through sheet metal. This method is suitable for cutting a wide range of materials, including those that are heat-sensitive.
Plasma Cutting
Plasma cutting utilizes a high-velocity jet of ionized gas to melt and remove metal from the sheet. This method is known for its speed and is commonly used for cutting thick metal sheets.
CNC Machining
Computer Numerical Control (CNC) machining involves the use of pre-programmed computer software to control the movement and operation of cutting tools. This precise and automated method is widely employed in sheet metal fabrication for complex cutting tasks.
Bending and Forming Processes
Bending and forming are essential processes in sheet metal fabrication, allowing the creation of complex shapes and structures from flat sheets of metal.
Press Brake Forming
Press brake forming involves the use of a machine press to bend and form metal sheets. This method allows for precise control over the angles and dimensions of the bends, making it suitable for creating components with specific geometric requirements.
Roll Forming
Roll forming is a continuous bending process where a long strip of metal is passed through sets of rolls to gradually shape it into the desired cross-section. This method is often used for producing components with consistent profiles and long lengths.
Stamping
Stamping is a process that involves forming or cutting metal sheets using a die and a press. It is a versatile method capable of producing complex shapes with high precision and repeatability.
Importance in Achieving Precise Dimensions and Shapes
Bending and forming processes are crucial for achieving the precise dimensions and shapes required for a wide range of components and products. These processes enable the creation of structural elements, enclosures, and intricate parts with the necessary geometrical integrity.
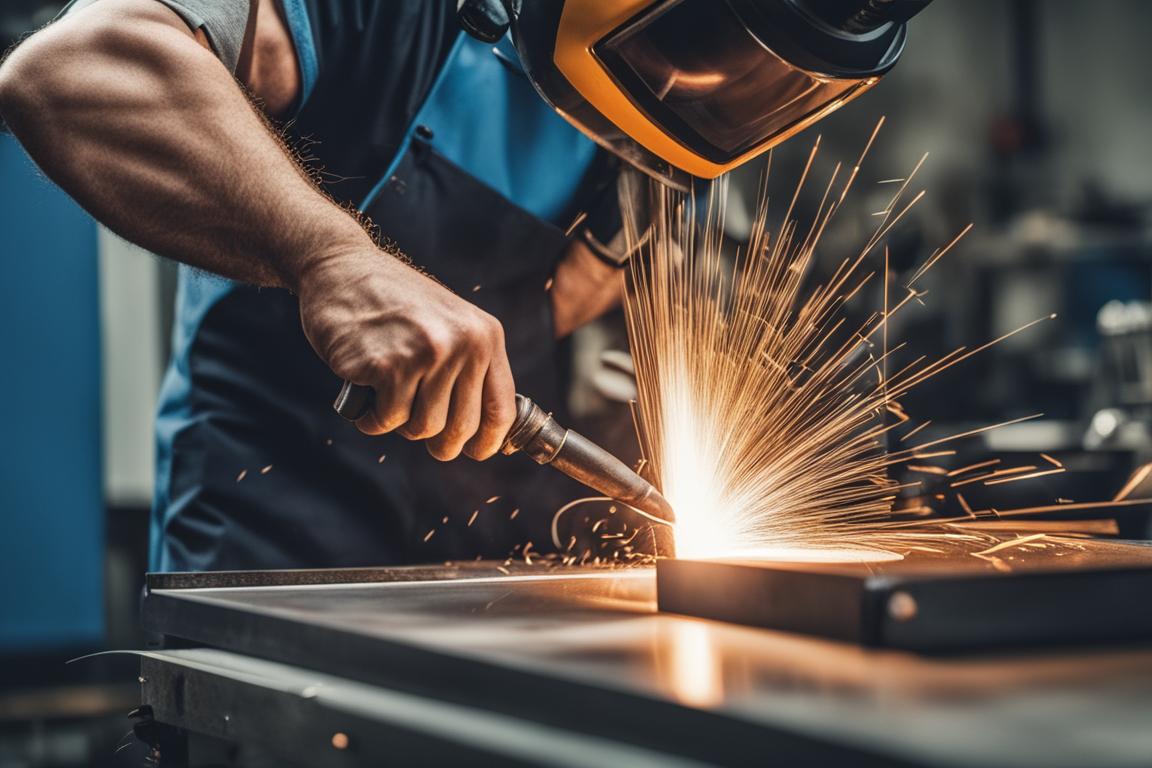
Welding and Joining Methods
Welding and joining techniques are integral to sheet metal fabrication, allowing multiple metal components to be combined into a single, cohesive structure.
TIG Welding
Tungsten Inert Gas (TIG) welding is a precise welding method that uses a non-consumable tungsten electrode to create the weld. It is valued for its ability to produce high-quality welds with minimal distortion.
MIG Welding
Metal Inert Gas (MIG) welding, also known as Gas Metal Arc Welding, utilizes a consumable wire electrode to join metal components. It is a versatile and efficient welding method suitable for a wide range of applications.
Spot Welding
Spot welding involves the use of electrodes to apply pressure and heat to the metal sheets, creating localized welds. This method is commonly used for joining thin metal sheets and is favored for its speed and cost-effectiveness.
Adhesive Bonding
Adhesive bonding is a non-invasive joining method that uses adhesives to bond metal components. It is valued for its ability to create strong and durable bonds while maintaining the integrity of the metal surfaces.
Impact on Product Precision and Strength
The choice of welding and joining methods has a significant impact on the precision and strength of the final product. Proper selection and execution of these techniques are critical for ensuring the structural integrity and performance of fabricated components.
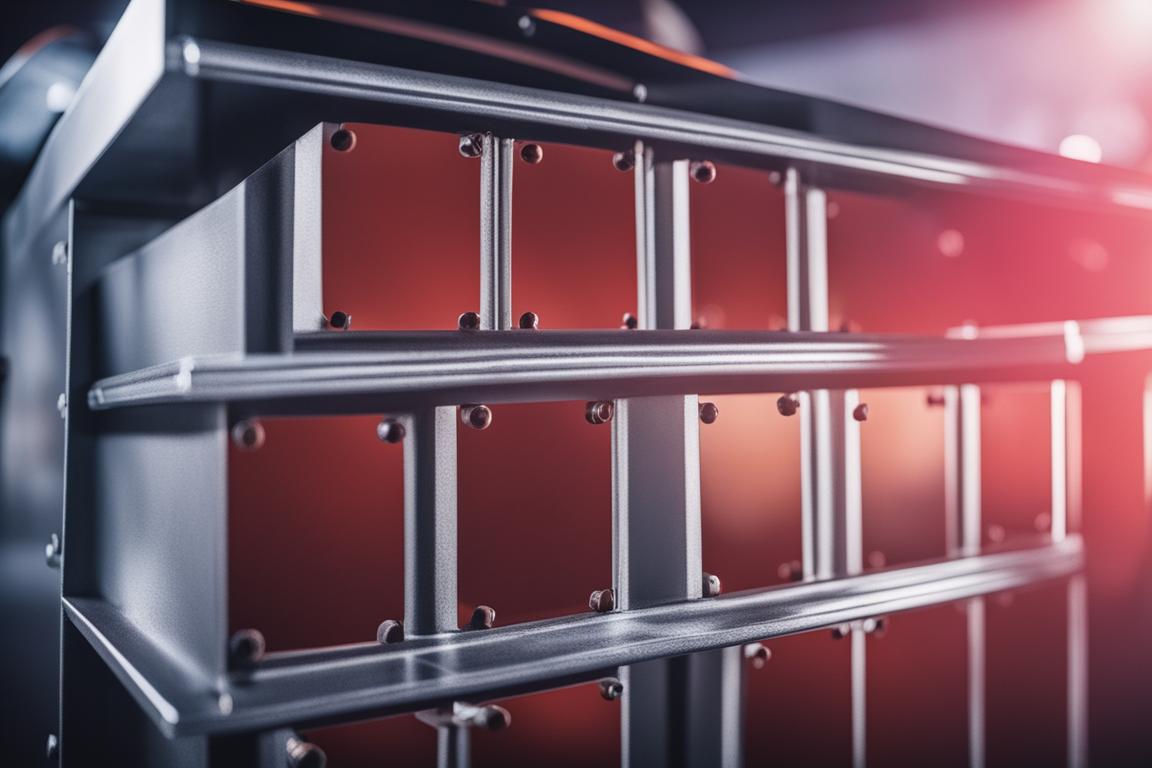
Surface Finishing and Coating
Surface finishing and coating processes are essential for enhancing the appearance, durability, and corrosion resistance of sheet metal components.
Powder Coating
Powder coating involves the application of dry powder onto the metal surface, which is then cured to form a durable and protective layer. This method offers a wide range of colors and finishes while providing excellent corrosion resistance.
Anodizing
Anodizing is an electrochemical process that creates a protective oxide layer on the surface of aluminum. This process improves the metal’s resistance to corrosion and wear while providing a decorative finish.
Plating
Metal plating involves the deposition of a thin layer of metal onto the surface of a substrate, enhancing its appearance and properties. Common plating materials include chrome, nickel, and zinc, each offering unique benefits.
Cleaning and Deburring
Cleaning and deburring processes are essential for removing contaminants, sharp edges, and imperfections from metal surfaces. These processes contribute to the overall quality and precision of fabricated components.
Contribution to Precision and Durability
Surface finishing and coating play a crucial role in enhancing the precision and durability of sheet metal components. These processes not only improve the aesthetic appeal but also provide protection against environmental factors, ensuring the longevity of the fabricated products.
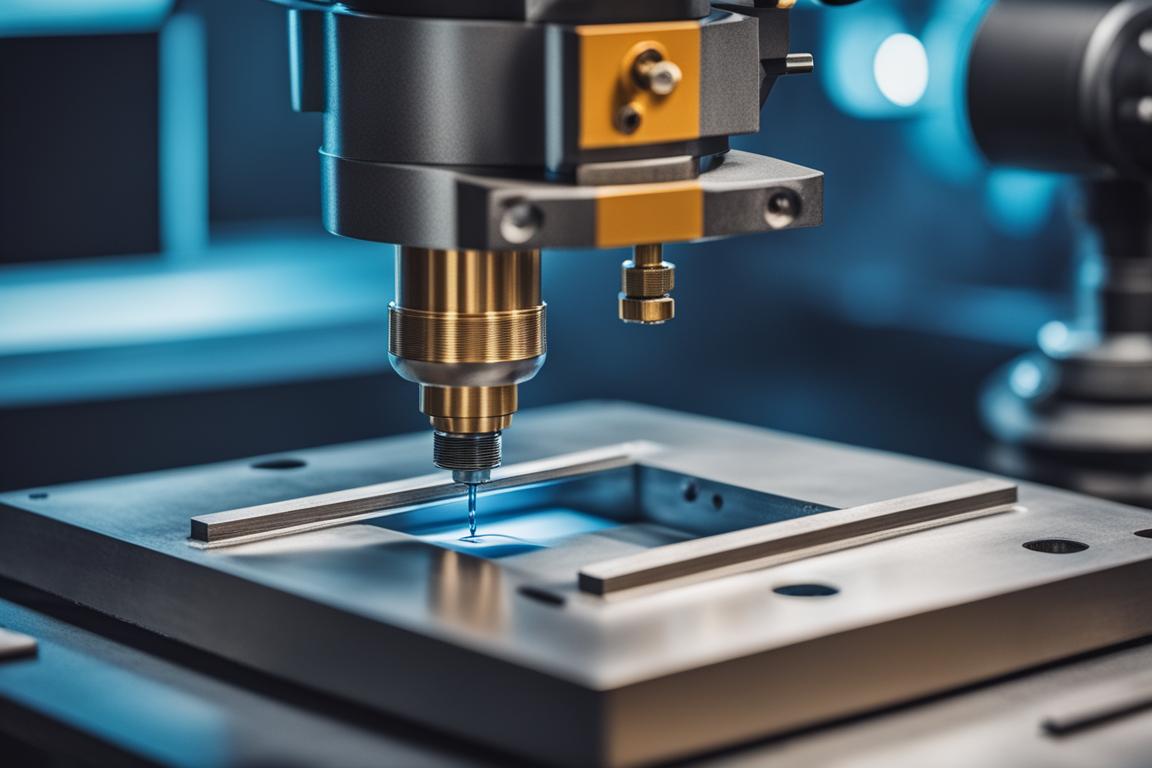
Quality Control and Inspection
Quality control and inspection are vital aspects of sheet metal fabrication, ensuring that fabricated components meet stringent quality standards and specifications.
Dimensional Inspection
Dimensional inspection involves the precise measurement and verification of the physical dimensions of fabricated components to ensure compliance with design specifications.
Visual Inspection
Visual inspection is carried out to identify surface imperfections, defects, and irregularities that may affect the functionality and aesthetics of the fabricated parts.
Non-Destructive Testing
Non-destructive testing methods such as ultrasonic testing and X-ray inspection are employed to assess the integrity and internal quality of fabricated components without causing damage.
Importance in Precision Fabrication and Compliance Standards
Quality control and inspection processes are essential for maintaining precision in fabrication and ensuring compliance with industry standards and customer requirements. These processes are integral to delivering products of the highest quality and reliability.
Design Considerations for Sheet Metal Fabrication
Design considerations play a crucial role in the successful fabrication of sheet metal components, influencing factors such as material selection, manufacturability, and prototyping.
Material Selection
The selection of the appropriate sheet metal material is critical and depends on factors such as mechanical properties, corrosion resistance, and formability. Understanding the characteristics of different materials is essential for making informed decisions.
Tolerances and Allowances
Designing for specific tolerances and allowances is essential for ensuring that fabricated components meet precise dimensional requirements. Incorporating suitable tolerances into the design is crucial for achieving functional and reliable products.
Design for Manufacturability Principles
Designing for manufacturability involves creating product designs that are optimized for efficient and cost-effective fabrication processes. This principle aims to streamline production while maintaining the integrity of the design.
Prototyping and Design Validation
Prototyping and design validation are integral to the design process, allowing for the testing and refinement of product designs prior to full-scale production. Prototyping helps identify and address potential issues early in the fabrication process.
Applications and Industries
Sheet metal fabrication finds widespread use across numerous industries, each with specific requirements and applications for fabricated components.
Aerospace
In the aerospace industry, sheet metal fabrication is crucial for producing aircraft components, structural elements, and specialized parts that require high strength-to-weight ratios and precision.
Automotive
Automotive manufacturing relies on sheet metal fabrication for producing body panels, chassis components, and various structural elements that demand high precision and durability.
Electronics
The electronics industry utilizes sheet metal fabrication for creating enclosures, heat sinks, and intricate components that require precise dimensions and thermal management properties.
Construction
The construction industry employs sheet metal fabrication for manufacturing architectural elements, structural components, and building systems that require durability and aesthetic appeal.
Real-World Examples and Case Studies
Real-world examples and case studies demonstrate the diverse applications of sheet metal fabrication across different industries, showcasing its role in enabling innovation and progress.
Application/Industry | Specific Component/Use | Advances/Innovations |
---|---|---|
Aerospace | Aircraft components, structural elements | Additive manufacturing for complex geometries, Industry 4.0 automation |
Automotive | Body panels, chassis components | 3D scanning for prototyping, robotics for assembly |
Electronics | Enclosures, heat sinks | Digital manufacturing for intricate designs, sustainable materials |
Construction | Architectural elements, building systems | Sustainable practices, advanced surface treatments |
Advances and Innovations in Sheet Metal Fabrication
The field of sheet metal fabrication continues to evolve, driven by advances in technology, automation, and digital manufacturing principles.
Automation and Robotics
Automation and robotics have revolutionized sheet metal fabrication, leading to increased efficiency, precision, and the ability to handle complex tasks with minimal human intervention.
Digital Manufacturing Technologies
Digital manufacturing technologies, such as 3D scanning and modeling, have streamlined the design and production processes, allowing for rapid prototyping and the creation of intricately designed components.
Industry 4.0 Principles
The adoption of Industry 4.0 principles, including interconnected systems, data analytics, and smart manufacturing, has transformed sheet metal fabrication by optimizing production processes and resource utilization.
Additive Manufacturing in Sheet Metal Fabrication
Additive manufacturing, or 3D printing, has expanded the possibilities in sheet metal fabrication, enabling the creation of highly complex and lightweight structures with unprecedented design freedom.
Choosing a Sheet Metal Fabrication Partner
Selecting the right sheet metal fabrication partner is crucial for the success of any project, requiring careful consideration of various factors.
Expertise and Experience
Partnering with a fabrication company with extensive expertise and experience ensures that the fabrication process is executed with precision and adherence to industry standards.
Equipment Capabilities and Technology
The availability of advanced equipment and technology is essential for ensuring that the fabrication partner can handle complex and diverse fabrication requirements.
Quality Standards and Certifications
Adherence to quality standards and certifications, such as ISO certifications and industry-specific quality benchmarks, demonstrates the commitment of the fabrication partner to delivering high-quality products.
Project Management Capabilities and Communication
Effective project management capabilities and clear communication channels are vital for ensuring that the fabrication partner can meet project timelines and address any concerns or requirements.
Sustainability and Future Trends in Sheet Metal Fabrication
The future of sheet metal fabrication is shaped by a focus on sustainability, technological advancements, and the exploration of new materials and processes.
Sustainable Practices and Materials
The adoption of sustainable practices, including recycling and the use of eco-friendly materials, is becoming increasingly important in sheet metal fabrication to minimize environmental impact.
Material Advancements and Recyclability
Advancements in materials science are leading to the development of new alloys and composites with enhanced properties, as well as improved recyclability of sheet metal materials.
Emerging Technologies and Processes
Emerging technologies, such as nanotechnology and advanced surface treatments, are poised to revolutionize sheet metal fabrication by offering unprecedented capabilities and performance.
In conclusion, sheet metal fabrication is a critical process with a broad range of applications and significant implications for various industries. Embracing technological advancements and sustainable practices, while maintaining a focus on precision and quality, will continue to shape the future of sheet metal fabrication.
By incorporating real-world examples, insights from industry professionals, and case studies, this article provides a comprehensive understanding of sheet metal fabrication, showcasing its practical applications and experiences in the industry.