Precision sheet metal fabrication is a critical process in the manufacturing industry, enabling the creation of intricate and high-quality metal components used in various applications. From aerospace and automotive to electronics and beyond, the demand for precision sheet metal fabrication continues to grow, driven by the need for durable, custom, and precisely engineered metal parts.
What You’ll Learn About Precision Sheet Metal Fabrication
By reading this article, you will learn:
– The definition and importance of precision sheet metal fabrication in various industries.
– The process, materials, tools, and equipment used in precision sheet metal fabrication.
– The advantages, applications, industry standards, and future trends in precision sheet metal fabrication.
What is Precision Sheet Metal Fabrication and Why is it Important?
Precision sheet metal fabrication involves shaping, cutting, and assembling metal sheets to create high-precision components and products. This process includes techniques such as cutting, bending, welding, and finishing to achieve the desired specifications and tolerances. It plays a pivotal role in several industries, including aerospace, automotive, electronics, telecommunications, and healthcare.
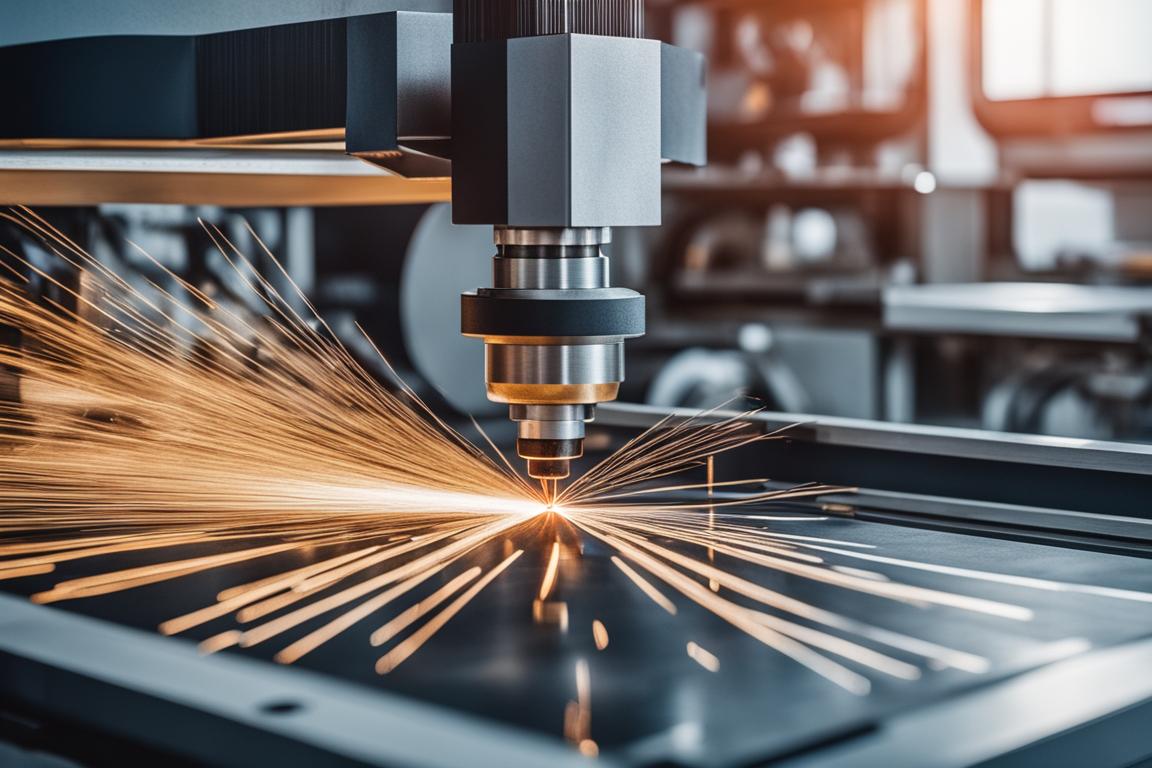
The Process of Precision Sheet Metal Fabrication
Precision sheet metal fabrication involves a series of intricate steps to transform raw metal sheets into finished products that meet exacting specifications.
Overview of the Fabrication Process
The process typically includes:
1. Design: Creating precise design specifications using specialized software and tools.
2. Cutting: Cutting metal sheets into the required shapes and sizes using advanced cutting tools.
3. Bending: Bending metal sheets to the desired angles and shapes using press brakes and other bending equipment.
4. Forming: Shaping the metal sheets to achieve the necessary geometries and contours.
5. Welding: Joining metal components using various welding techniques to create a cohesive structure.
6. Finishing: Surface treatment and finishing processes to enhance the appearance and durability of the fabricated components.
Advanced Techniques and Technologies
Advanced techniques and technologies such as computer-aided design (CAD), 3D modeling, and robotic welding have revolutionized precision sheet metal fabrication, enabling greater precision, efficiency, and repeatability in the manufacturing process.
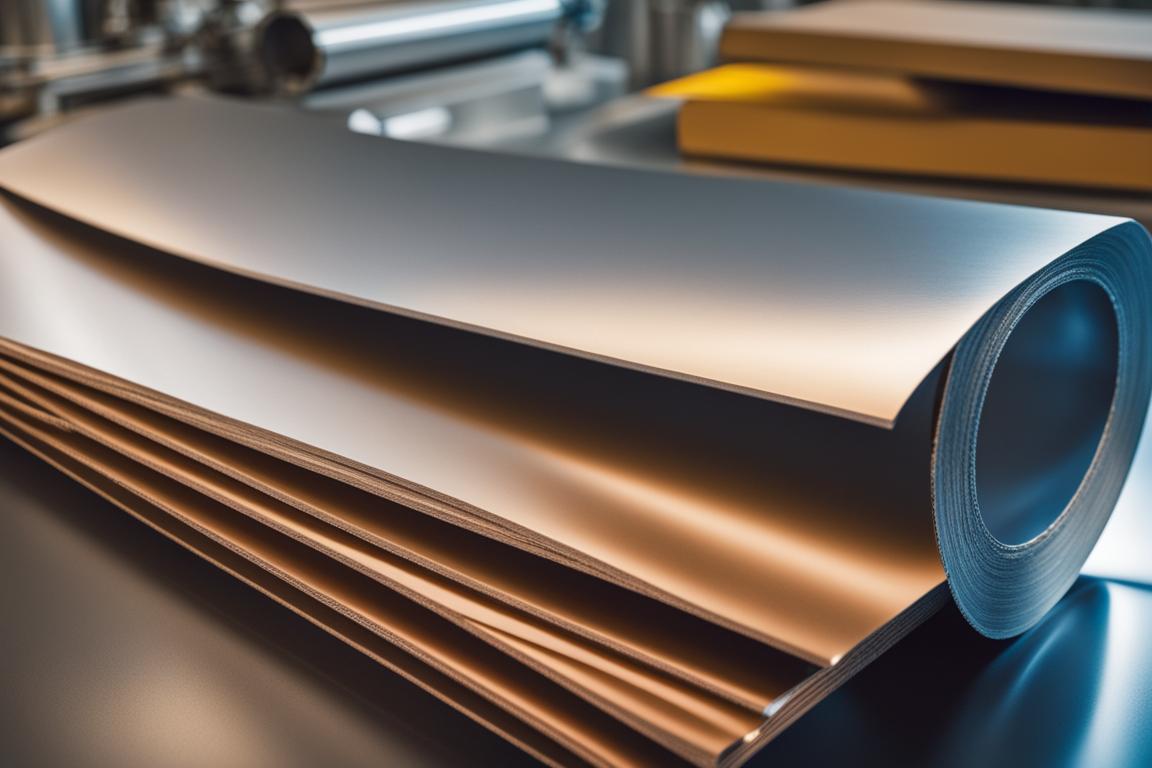
Materials Used in Precision Sheet Metal Fabrication
The choice of metals used in precision sheet metal fabrication is crucial in determining the properties and performance of the fabricated components.
Types of Metals
The most commonly used metals include:
1. Aluminum: Favored for its lightweight and corrosion-resistant properties.
2. Stainless Steel: Known for its strength, durability, and resistance to corrosion.
3. Carbon Steel: Offers excellent strength and formability.
4. Titanium: Valued for its high strength-to-weight ratio and exceptional corrosion resistance.
Properties and Applications of Each Metal
Each metal has unique properties that make it suitable for specific applications, and understanding these properties is essential in selecting the right material for precision sheet metal fabrication.
Tools and Equipment | Description |
---|---|
Laser Cutting Machines | Offer precision and versatility for intricate and complex cuts. |
CNC Punching Machines | Enable efficient and accurate hole punching and shaping of metal sheets. |
Press Brakes | Essential for bending and forming metal sheets with precision and consistency. |
Welding Equipment | Advanced welding equipment ensures strong and precise joins between metal components. |
Surface Treatment Tools | Used for sanding, grinding, and coating to enhance the aesthetics and durability of fabricated metal parts. |
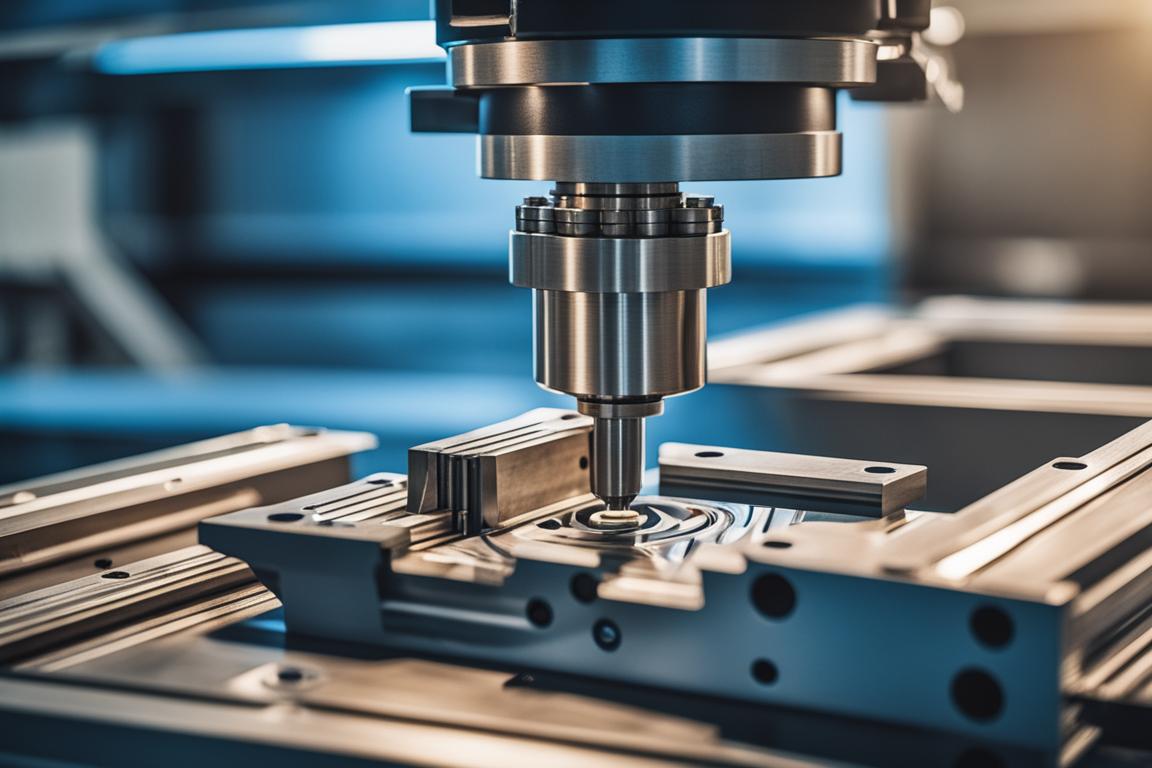
Tools and Equipment
The precision sheet metal fabrication process relies on a variety of specialized tools and equipment to achieve accurate and high-quality results.
Cutting and Shaping Tools
- Laser Cutting Machines: Offer precision and versatility for intricate and complex cuts.
- CNC Punching Machines: Enable efficient and accurate hole punching and shaping of metal sheets.
- Press Brakes: Essential for bending and forming metal sheets with precision and consistency.
Joining and Finishing Equipment
- Welding Equipment: Advanced welding equipment ensures strong and precise joins between metal components.
- Surface Treatment Tools: Used for sanding, grinding, and coating to enhance the aesthetics and durability of fabricated metal parts.
Quality Control and Inspection
Ensuring the quality and precision of fabricated metal components is paramount in precision sheet metal fabrication.
Importance of Quality Control
Quality control measures are integral to maintaining high standards, minimizing defects, and ensuring compliance with specifications.
Inspection Methods and Technologies
Advanced inspection methods, including coordinate measuring machines (CMM) and non-destructive testing (NDT), are employed to verify the accuracy and integrity of fabricated metal parts.
Compliance with Industry Standards
Adherence to industry standards such as ISO 9001 and AS9100 is essential in guaranteeing the quality and reliability of precision sheet metal fabricated products.
Design Considerations
Effective design considerations are critical in achieving precision and efficiency in sheet metal fabrication.
Tolerances and Precision Requirements
Understanding and accommodating tolerances and precision requirements in the design phase is crucial to achieving accurate and reliable metal components.
Material Selection and Optimization
Selecting the right materials and optimizing designs for manufacturability are essential for streamlining the fabrication process and ensuring the quality of the final products.
Design Software and Prototyping
The use of advanced design software and prototyping techniques allows for iterative refinement and validation of designs before full-scale fabrication, reducing errors and improving efficiency.
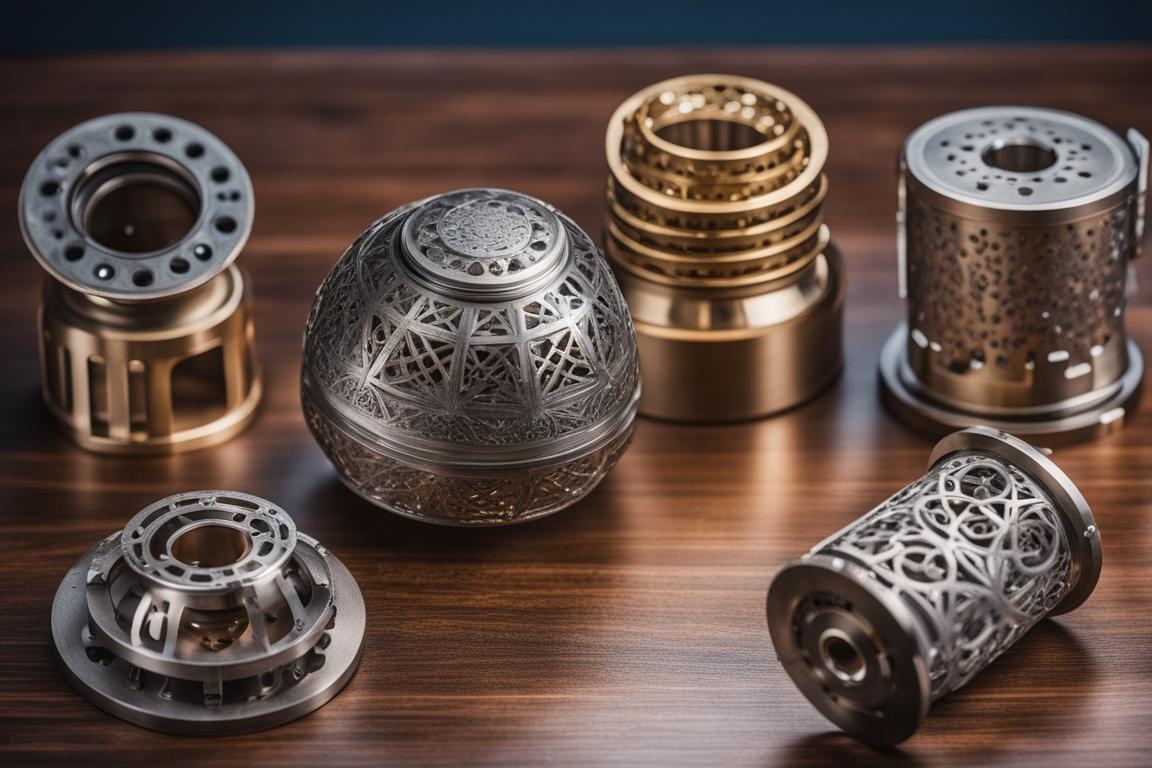
Advantages of Precision Sheet Metal Fabrication
Precision sheet metal fabrication offers numerous advantages that make it indispensable in various industries.
Cost-effectiveness and Efficiency
The precise and efficient nature of the fabrication process leads to cost savings and enhanced production efficiency for manufacturers.
High Precision and Accuracy
The ability to achieve tight tolerances and high precision in fabricated metal components ensures consistent quality and performance.
Complex Geometry Capabilities
Precision sheet metal fabrication enables the creation of intricate and complex geometries, expanding the design possibilities for engineers and designers.
Strength and Durability of Components
Fabricated metal components exhibit exceptional strength and durability, meeting the stringent requirements of diverse applications.
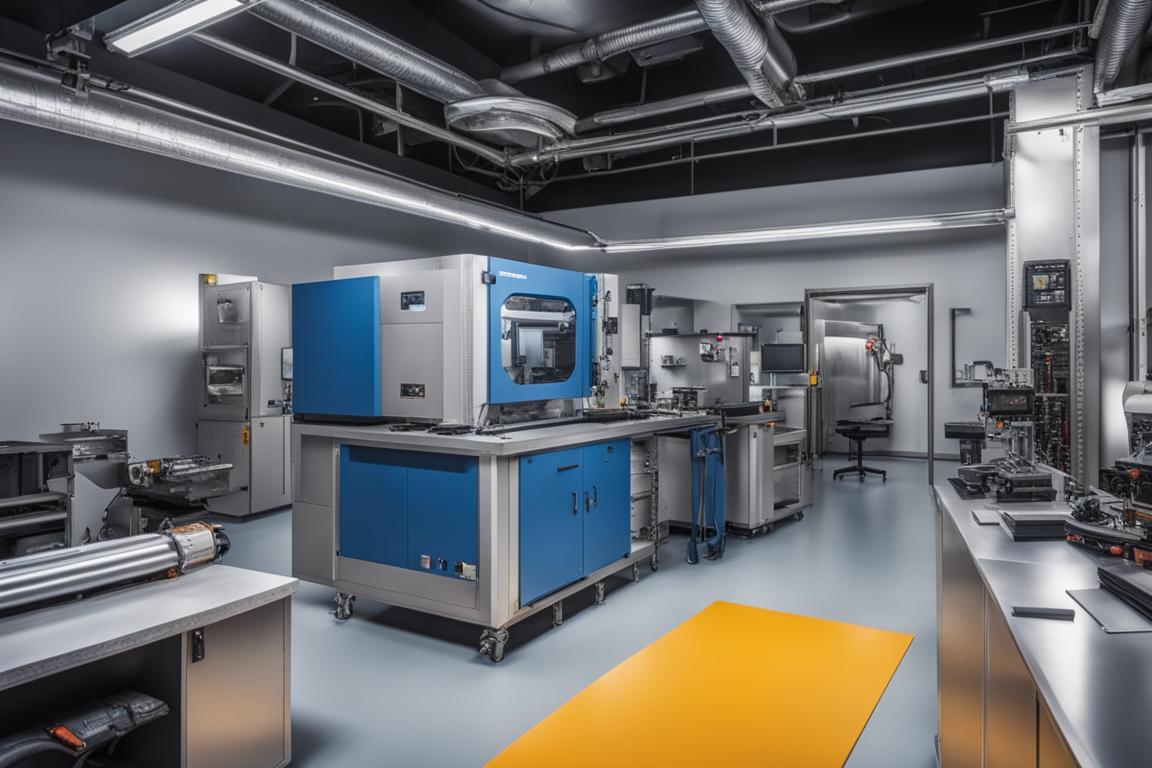
Applications of Precision Sheet Metal Fabrication
Precision sheet metal fabrication finds diverse applications across a wide range of industries and use cases.
Industries and Sectors Utilizing Precision Sheet Metal
Industries such as aerospace, automotive, electronics, telecommunications, and healthcare rely on precision sheet metal fabrication for critical components and assemblies.
Specific Applications and Use Cases
- Custom Enclosures: Creating custom enclosures for electronic devices, industrial equipment, and machinery.
- Brackets and Supports: Essential for securely mounting and supporting various components and structures.
- Panels and Casings: Crucial in industries requiring robust and aesthetically pleasing enclosures for equipment and machinery.
- Machinery and Equipment Components: Including gears, housings, and frames manufactured using precision sheet metal fabrication techniques.
Industry Standards and Certifications
Adherence to industry standards and certifications is fundamental in ensuring the quality and reliability of precision sheet metal fabricated products.
ISO 9001 and Quality Management
ISO 9001 certification signifies a commitment to quality management systems, demonstrating a manufacturer’s ability to consistently deliver products that meet customer and regulatory requirements.
AS9100 and Aerospace Requirements
AS9100 certification is specifically tailored to the aerospace industry, emphasizing additional quality and safety requirements for aerospace components and systems.
Compliance and Regulatory Standards
Compliance with regulatory standards such as RoHS (Restriction of Hazardous Substances) ensures the environmental and safety compliance of fabricated metal products.
Continuous Improvement and Best Practices
Embracing continuous improvement initiatives and best practices in precision sheet metal fabrication is essential for enhancing efficiency and maintaining high product quality.
Future Trends in Precision Sheet Metal Fabrication
The future of precision sheet metal fabrication is shaped by emerging technologies and sustainable practices that are poised to transform the industry.
Additive Manufacturing and 3D Printing
The integration of additive manufacturing and 3D printing technologies into precision sheet metal fabrication processes offers new avenues for creating complex geometries and reducing material waste.
Automation and Robotics in Fabrication
The adoption of automation and robotics in fabrication processes enhances efficiency, reduces production times, and improves workplace safety in precision sheet metal fabrication facilities.
Sustainable Practices and Material Innovations
The industry is witnessing a shift towards sustainable practices and material innovations, emphasizing the use of eco-friendly materials and energy-efficient processes in precision sheet metal fabrication.
Questions & Answers
Question: What is precision sheet metal fabrication?
Answer: Precision sheet metal fabrication is the process of shaping and manipulating sheet metal to create high-quality, accurate metal parts and components.
Question: Who can benefit from precision sheet metal fabrication?
Answer: Industries such as aerospace, automotive, electronics, and medical equipment can benefit from precision sheet metal fabrication for custom parts and components.
Question: How is precision sheet metal fabrication different from regular fabrication?
Answer: Precision sheet metal fabrication focuses on extremely accurate and detailed shaping of sheet metal, often using advanced techniques such as laser cutting and CNC machining.
Question: What makes precision sheet metal fabrication cost-effective?
Answer: While precision sheet metal fabrication may have higher initial costs, it can ultimately save money through reduced material waste and improved efficiency in production processes.
Question: How can I ensure the precision of my sheet metal fabrication project?
Answer: To ensure precision, work with experienced fabricators who use advanced equipment, have a thorough quality control process, and offer precise measurements and tolerances.
Question: What if my project has complex design requirements?
Answer: For complex designs, choose a precision sheet metal fabrication company with a proven track record of handling intricate projects and providing innovative solutions to meet specific design requirements.