Atlas is not sitting idle while manufacturing costs escalate. With this adversity comes creativity and change. A metal fabricator has three inputs into the process: material, human labor, and machine time. We see material continuing to increase and it has not plateaued yet. Human labor is pressuring for increased wages and benefits which add to the pricing pressure. But, our customers want costs to be contained and stable prices. To help combat the rising costs of material and labor, speed is our ally. Humans augmented with collaborative robots like Baxter and industrial robots help with labor costs. We currently utilize both technologies and carefully plan more implementation in 2018.
Investing in the machines that make the parts seems to be one input that can control costs. Over the last several years, Atlas has aggressively invested in automated Trumpf punching technology in both facilities, now boasting 4 Trumpf punch systems, three of them fully automated. This technology is the fastest punching technology in the world. The only variable we can control is to build the parts faster so that the machine run time costs less.
Once again, we are embarking on change by installing a 4kw fiber laser. With cut speeds up to 5x faster than CO2 technology, we plan to use this tool to help combat rising costs. The software to nest parts on the flat sheet is also key to minimizing scrap and obtaining maximum sheet density. We are also implementing Radan nesting software on the laser and punches so that our engineers can get the best sheet utilization possible.
We are diligently investing in technology to control production costs and combat the tariff increase.
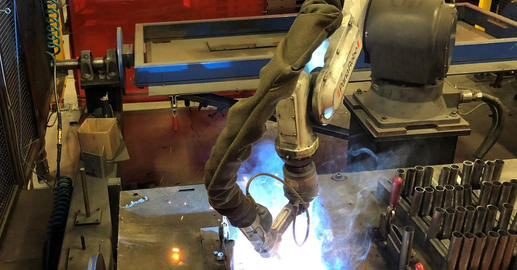