Sheet metal forming, a versatile manufacturing process that transforms flat metal sheets into complex and intricate shapes, is a crucial aspect of modern engineering. This article, written by experts in the field of sheet metal forming, provides an in-depth overview of the process, its types of processes, materials used, and the tools and equipment involved. By delving into this comprehensive guide, readers will gain valuable insights into the world of sheet metal forming.
What You Will Learn About Sheet Metal Forming
By reading this article, you will learn:
1. The different types of sheet metal forming processes such as bending, stretching, and deep drawing.
2. The materials used in sheet metal forming, including commonly used metals, alloys, and composites.
3. The importance of precision, tolerances, and formability in sheet metal forming.
Definition and Significance
Sheet metal forming, encompassing techniques such as bending, stretching, and deep drawing, plays a pivotal role in creating lightweight yet durable components essential for modern engineering applications.
Transformation of Sheet Metal into Complex Shapes
Through the use of specialized equipment and tools, flat sheet metal is transformed into complex shapes and structures, catering to the specific requirements of diverse industries.
Role in Precision Sheet Metal Fabrication
Precision sheet metal fabrication heavily relies on forming processes to achieve the desired geometries and tolerances required for intricate components, assemblies, and products.
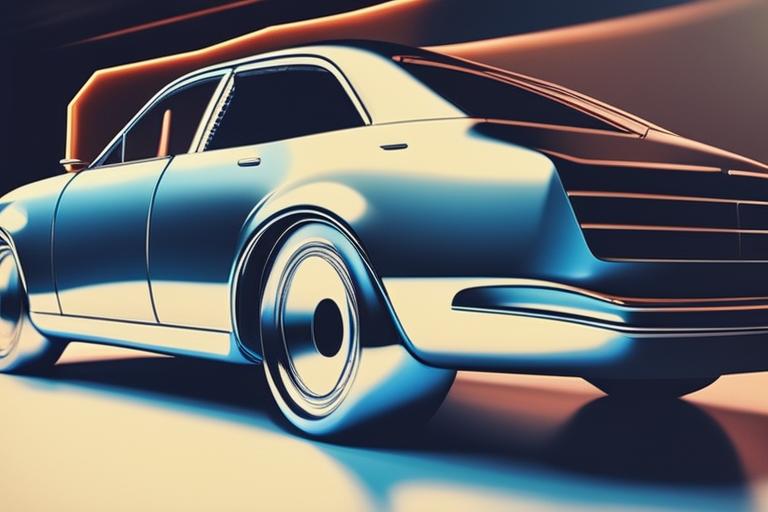
Common Sheet Metal Forming Applications
Sheet metal forming finds applications in various industries, showcasing its versatility and adaptability to diverse manufacturing needs.
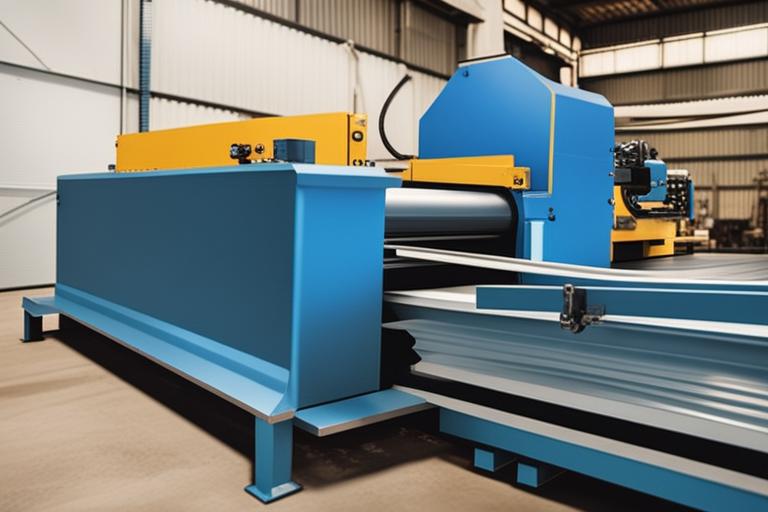
Types of Sheet Metal Forming Processes
Bending
Bending involves the deformation of a metal sheet along a straight axis, resulting in angular changes and the creation of U-shapes, V-shapes, and other bend configurations.
Stretching
Stretch forming elongates the metal sheet over a die, increasing its surface area without thinning the material, making it suitable for producing curved or contoured parts.
Deep Drawing
Deep drawing transforms a flat sheet metal blank into a hollow shape through the use of a punch and die, commonly utilized in the production of cans, enclosures, and automotive components.
Roll Forming
Roll forming utilizes a series of continuous bending operations to progressively shape the metal sheet into the desired profile, making it ideal for producing long lengths of consistent cross-sectional profiles.
Superplastic Forming
Superplastic forming enables the shaping of intricate and lightweight components by heating the metal sheet to a specific temperature range, allowing for high elongation and complex geometries.
Incremental Sheet Forming
Incremental sheet forming is a flexible and cost-effective method for producing complex shapes by deforming the metal sheet incrementally using a CNC-controlled tool.
Comparison of Different Forming Processes
Each forming process offers unique advantages and limitations, influencing the selection based on material properties, production volume, and geometric complexities.
Principles and Applications of Each Process
Understanding the principles and applications of each process is crucial for optimizing sheet metal forming operations to achieve the desired part geometries and mechanical properties.
Material | Properties | Common Applications |
---|---|---|
Steel | High strength, durability, formability | Automotive components, construction, appliances |
Aluminum | Lightweight, corrosion-resistant, malleable | Aerospace, automotive, packaging |
Stainless Steel | Corrosion-resistant, high strength, aesthetic appeal | Food processing, medical equipment, architectural |
Advanced Alloys | Tailored properties for specific applications | Aerospace, defense, high-performance industries |
Composites | Lightweight, high strength-to-weight ratio | Aerospace, automotive, sporting goods |
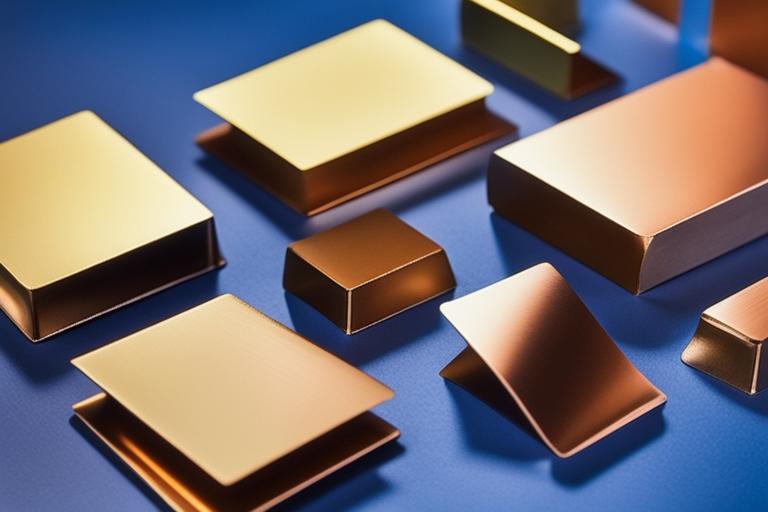
Materials Used in Sheet Metal Forming
Commonly Used Metals
Materials such as steel, aluminum, and stainless steel are commonly utilized in sheet metal forming due to their exceptional formability, strength, and corrosion resistance.
Alloys and Composites
Advanced alloys and composite materials exhibit tailored properties suitable for specific applications, expanding the capabilities of sheet metal forming in diverse industries.
Influence of Material Properties on Forming Processes
Material properties such as ductility, tensile strength, and work hardening behavior directly influence the formability and processing parameters in sheet metal forming operations.
Material Selection Criteria for Sheet Metal Forming
The selection of materials is guided by factors such as mechanical properties, corrosion resistance, weight considerations, and cost-effectiveness, aligning with the performance requirements of the end-use applications.
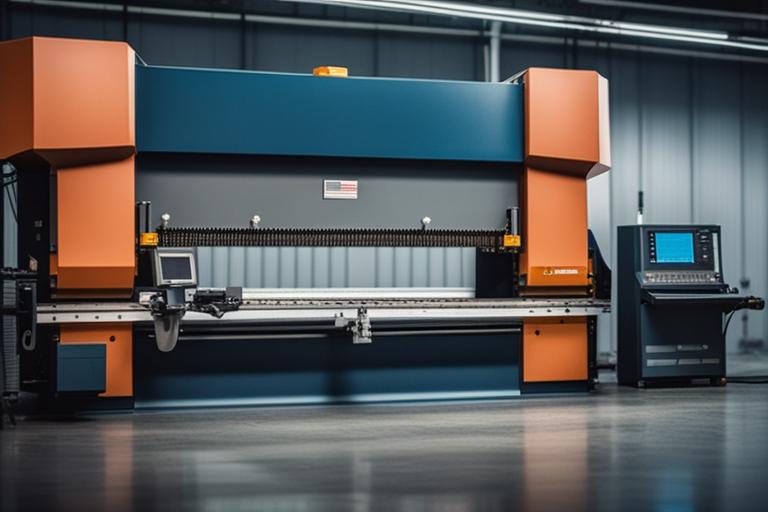
Tools and Equipment for Sheet Metal Forming
Press Brakes
Press brakes are essential for bending operations, allowing precise control over the bending angle and ensuring accurate geometries in formed parts.
Stamping Presses
Stamping presses enable high-speed and high-precision forming operations, making them suitable for mass production of sheet metal components.
Dies and Punches
Dies and punches play a critical role in shaping the metal sheets, providing the necessary contours and features required for specific part geometries.
Rollers and Roll Forming Machines
Rollers and roll forming machines are employed for continuous shaping of metal sheets, particularly for producing long lengths of consistent profiles.
Laser and Waterjet Cutting Machines
Cutting machines utilizing laser and waterjet technologies offer precise cutting capabilities, allowing for the creation of intricate shapes and contours in sheet metal components.
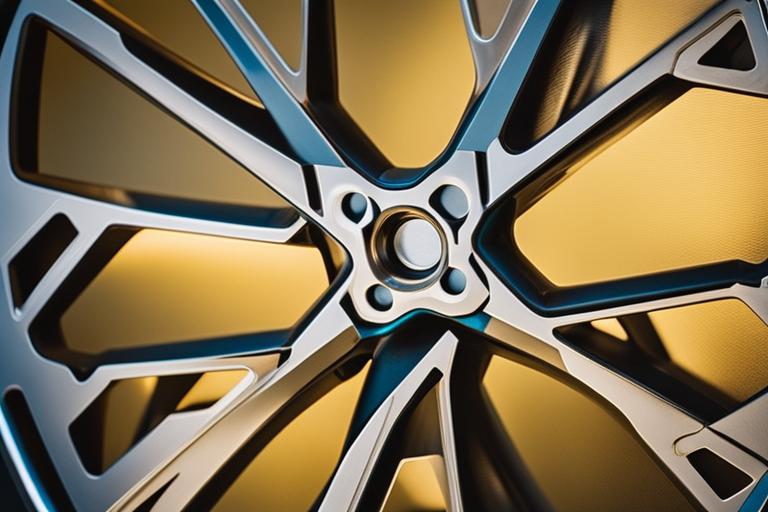
Practical Examples and Case Studies
Including real-world examples or case studies related to sheet metal forming would enhance the reader’s understanding and demonstrate practical experience in the subject matter, providing valuable insights into the application of sheet metal forming principles in actual manufacturing scenarios.
By understanding the various processes, materials, and equipment involved in sheet metal forming, manufacturers can optimize their operations to meet the demands of diverse industries, producing high-quality components with precision and efficiency.
FAQ
What is precision sheet metal fabrication?
Precision sheet metal fabrication is the process of shaping and forming sheet metal to create high-quality, custom parts and products.
How does sheet metal forming differ from other fabrication methods?
Sheet metal forming involves using specialized tools and techniques to shape flat sheets of metal into complex and precise components.
Who can benefit from precision sheet metal fabrication services?
Industries such as aerospace, automotive, electronics, and medical equipment rely on precision sheet metal fabrication for custom, high-quality parts.
What are the advantages of precision sheet metal fabrication?
Precision sheet metal fabrication allows for the creation of intricate, customized parts with tight tolerances and high-quality finishes.
How can I ensure the accuracy of sheet metal forming for my project?
Work closely with experienced fabricators who utilize advanced equipment and have a proven track record of delivering precise results.
Isn’t precision sheet metal fabrication expensive compared to other methods?
While initial costs may be higher, the precision and quality of the parts produced often lead to long-term cost savings and improved product performance.