What You Will Learn About Sheet Metal Forming
By reading this article, you will learn: 1. The techniques and processes involved in sheet metal forming, such as bending, stretching, deep drawing, and hydroforming. 2. The types of materials used, including steel, aluminum, copper, and alloys, and how material properties influence the forming process. 3. The significance of quality control measures and the future trends in sheet metal forming.
Sheet metal forming is a highly versatile and widely used manufacturing process that involves shaping metal sheets into the desired parts and products. This intricate process plays a crucial role in various industries, including aerospace, automotive, electronics, and medical equipment manufacturing. Understanding the fundamentals of sheet metal forming is essential for engineers, designers, and manufacturers to create precision components with complex geometries.
Definition and Importance of Sheet Metal Forming
Sheet metal forming, also known as metal fabrication, encompasses a range of techniques for transforming flat metal sheets into diverse shapes and configurations. The significance of sheet metal forming lies in its ability to produce lightweight, durable, and intricate parts that are integral to the functionality and structure of numerous products across industries.
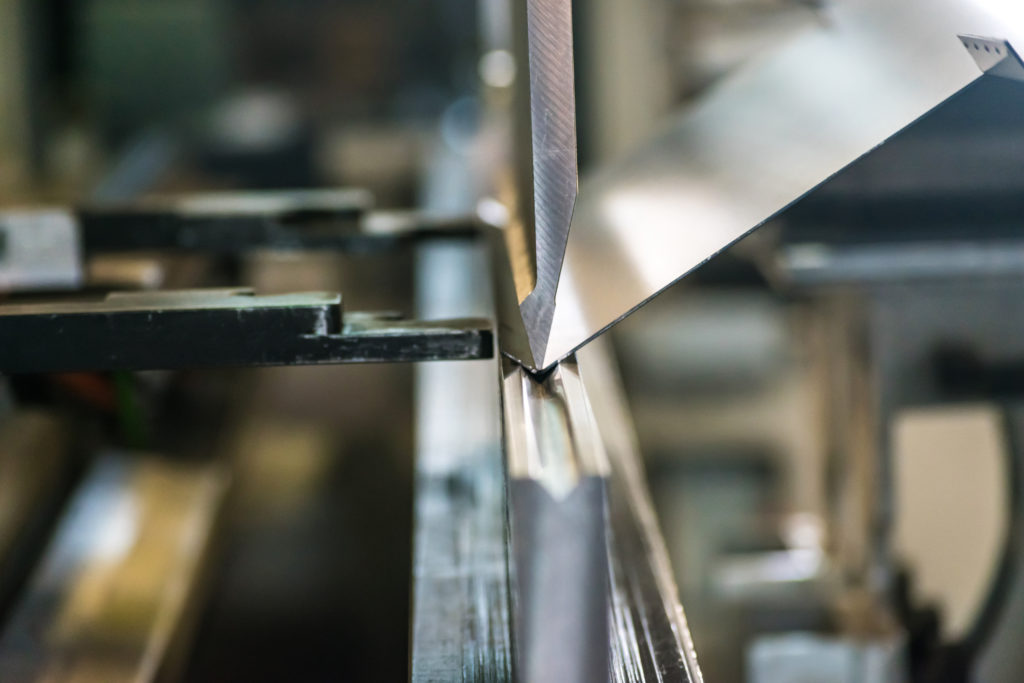
Techniques and Processes
Sheet metal forming involves several key techniques and processes, each tailored to specific applications and desired outcomes. These include:
1. Bending
Bending is a fundamental sheet metal forming process that involves deforming a metal sheet around a straight axis to create angular or curved shapes. This process is commonly used in the fabrication of brackets, enclosures, and structural components.
2. Stretching
Stretching is employed to elongate the metal sheet without failure, often used in the production of automotive body panels and aircraft skins to achieve optimal strength and surface finish.
3. Deep Drawing
Deep drawing is utilized to form cylindrical or box-shaped parts from sheet metal, such as kitchen sinks, aluminum cans, and automotive components like oil filters and hubcaps.
4. Hydroforming
Hydroforming employs high-pressure fluid to shape metal sheets into complex forms, which is particularly advantageous for producing lightweight and structurally robust components in the automotive and aerospace sectors.
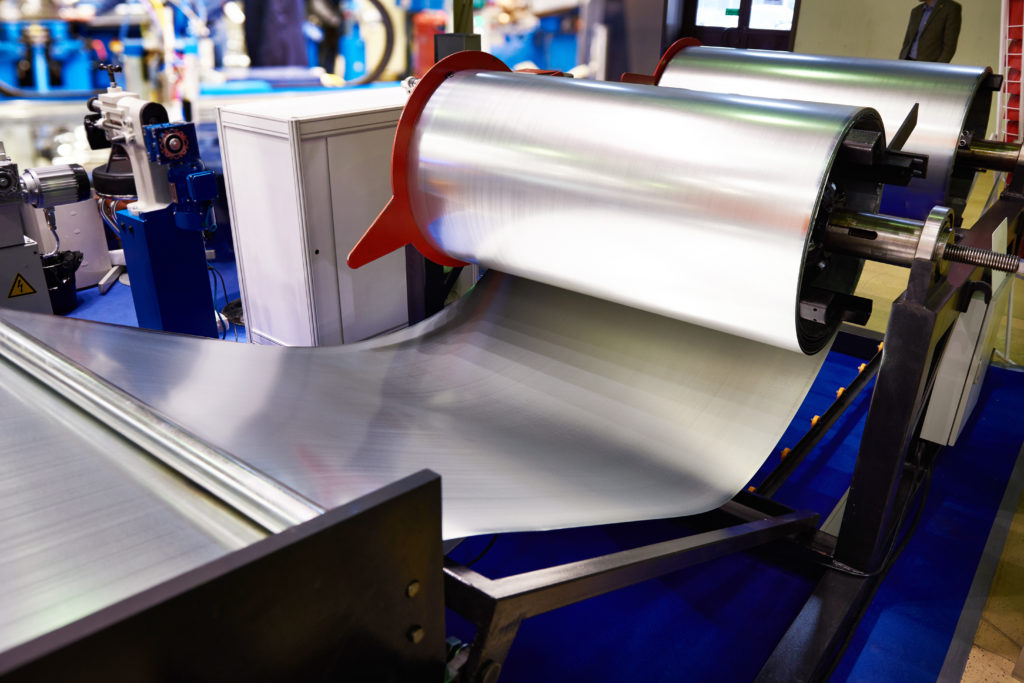
Materials Used in Sheet Metal Forming
Types of Materials Used
Various materials are employed in sheet metal forming to meet diverse functional and aesthetic requirements, including:
1. Steel
Steel is a widely utilized material in sheet metal forming due to its exceptional strength, durability, and formability. It is commonly applied in automotive body panels, structural components, and appliances.
2. Aluminum
Aluminum exhibits lightweight properties and high corrosion resistance, making it a preferred choice for aerospace components, consumer electronics, and packaging materials.
3. Copper
Copper’s excellent electrical conductivity and malleability render it suitable for electrical components, roofing materials, and architectural embellishments.
4. Alloys
Alloys, such as stainless steel and titanium, offer a blend of desirable properties, including corrosion resistance, high temperature strength, and aesthetic appeal, making them ideal for diverse applications in sheet metal forming.
Material Properties and Their Influence on the Forming Process
The material properties, including yield strength, ductility, and work hardening behavior, significantly impact the formability and manufacturability of sheet metal. Engineers and fabricators must carefully consider these properties to optimize the forming process and ensure the integrity of the final components.
Material | Properties and Uses |
---|---|
Steel | – Exceptional strength, durability, and formability – Commonly used in automotive body panels, structural components, and appliances |
Aluminum | – Lightweight properties and high corrosion resistance – Preferred choice for aerospace components, consumer electronics, and packaging |
Copper | – Excellent electrical conductivity and malleability – Suitable for electrical components, roofing materials, and architectural uses |
Alloys | – Offer a blend of desirable properties, including corrosion resistance, high temperature strength, and aesthetic appeal |
Design Considerations in Sheet Metal Forming
Importance of Design in Sheet Metal Forming
Effective design is paramount in sheet metal forming as it directly influences the manufacturability, cost, and performance of fabricated parts. Integrating design principles that account for material behavior and forming processes is essential for achieving high-quality, functional components.
Factors Affecting Manufacturability
1. Material Thickness
The thickness of the metal sheet impacts its formability and the complexity of shapes that can be achieved. Thinner sheets are more conducive to intricate bending and forming, while thicker sheets may require specialized processes to achieve desired shapes.
2. Bend Radius
The bend radius determines the minimum achievable curvature in a metal sheet, influencing the ease of forming and the structural integrity of the final part.
3. Tolerances
Tolerances in sheet metal forming refer to the permissible deviation from specified dimensions, and they play a critical role in ensuring the functionality and assembly of fabricated components.
Incorporating these design considerations and understanding their impact on the forming process is essential for optimizing the production of intricate and high-quality sheet metal parts.
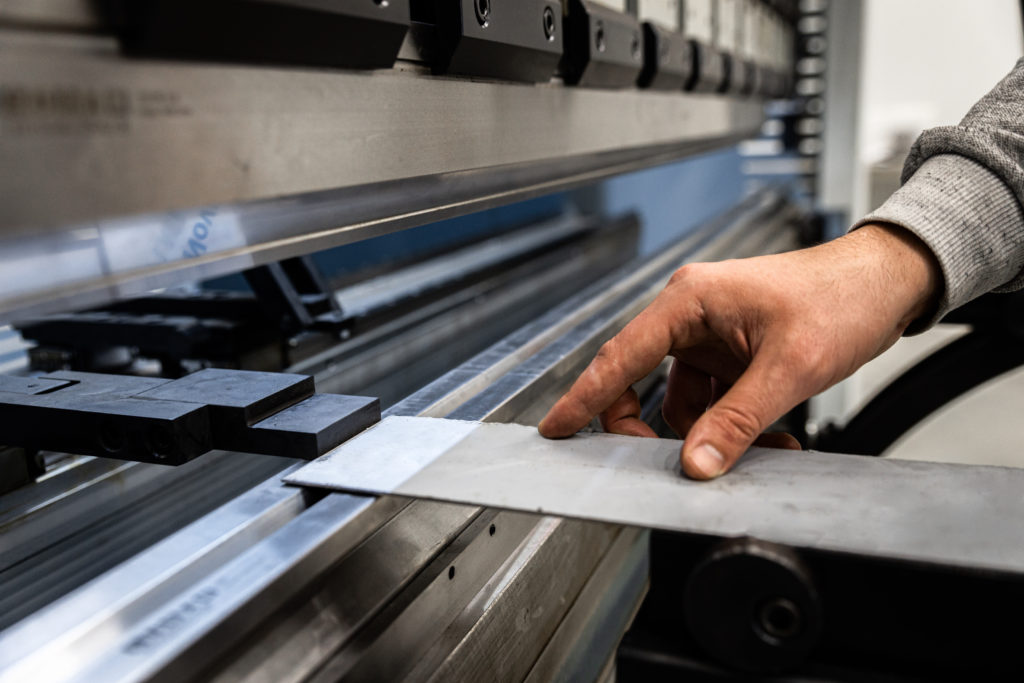
Tooling and Equipment for Sheet Metal Forming
Specialized Tools for Sheet Metal Forming
The successful execution of sheet metal forming relies on specialized tools and equipment, including:
1. Press Brakes
Press brakes are essential for bending metal sheets by exerting controlled force, and facilitating the creation of precise angles and shapes.
2. Stamping Presses
Stamping presses are utilized for blanking, piercing, and forming operations, enabling the mass production of intricate sheet metal components.
3. Dies
Dies, available in various forms such as blanking dies and forming dies, are crucial for shaping and cutting metal sheets with high precision.
Utilization of Tools for Specific Forming Processes
Different forming processes require specific tooling and equipment tailored to the unique characteristics of each technique. Understanding the capabilities and limitations of these tools is vital for achieving the desired outcomes in sheet metal forming.
Precision and Tolerances in Sheet Metal Forming
Importance of Precision in Sheet Metal Forming
Precision is a defining factor in sheet metal forming, as it directly influences the functionality, fit, and assembly of fabricated components. Achieving precise dimensions and geometries is essential for ensuring the optimal performance and interchangeability of parts.
Achieving Tight Tolerances in Sheet Metal Fabrication
The attainment of tight tolerances in sheet metal fabrication demands meticulous control of forming processes, tooling, and material properties. Employing advanced manufacturing techniques and quality control measures is imperative for consistently meeting stringent tolerance requirements in precision sheet metal components.
Quality Control in Sheet Metal Forming
Significance of Quality Control Measures in Sheet Metal Forming
Quality control is paramount in sheet metal forming to guarantee the reliability, safety, and performance of fabricated parts. Implementing robust quality control measures throughout the forming process is essential for detecting defects, ensuring dimensional accuracy, and upholding material integrity.
Inspection Techniques and Testing Procedures in Precision Fabrication
An array of inspection techniques, including coordinate measuring machines (CMM), optical profilometry, and non-destructive testing, are employed to assess the dimensional accuracy and material properties of sheet metal components. These rigorous testing procedures are crucial for validating the quality and reliability of formed parts.
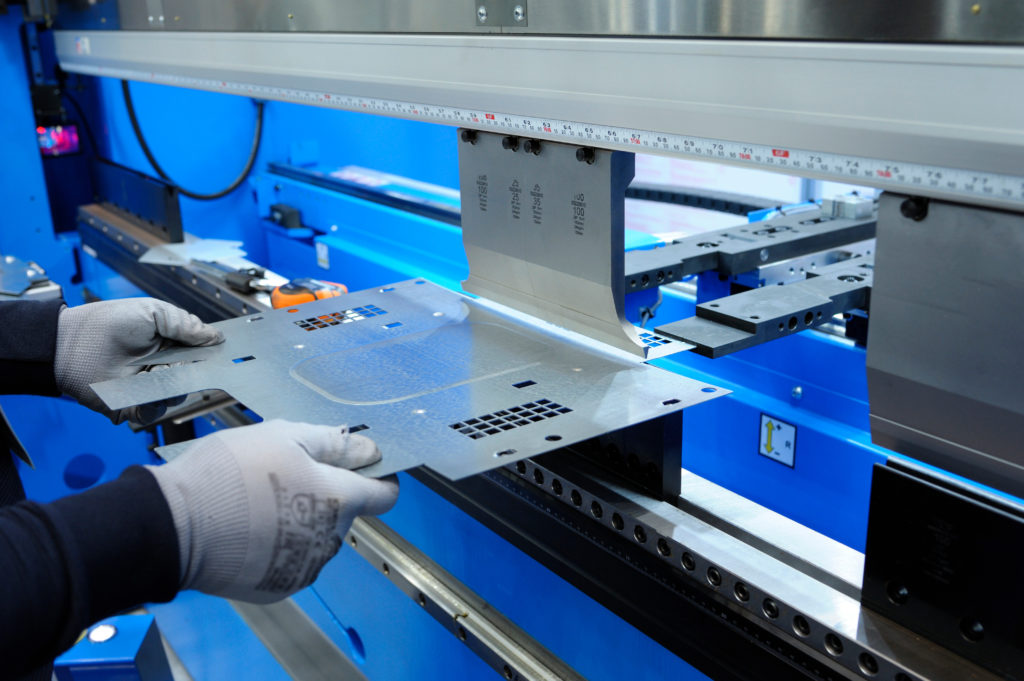
Applications and Industries of Sheet Metal Forming
Sheet Metal Forming in Aerospace Industry
The aerospace industry extensively relies on sheet metal forming for producing lightweight and aerodynamic components, such as fuselages, wings, and engine parts, to enhance fuel efficiency and structural integrity.
Automotive Applications of Sheet Metal Forming
Automotive manufacturers leverage sheet metal forming to fabricate body panels, chassis components, and exhaust systems, enabling the production of vehicles with optimal strength-to-weight ratios and aesthetic appeal.
Sheet Metal Forming in Electronics Manufacturing
The electronics industry utilizes sheet metal forming to create enclosures, heat sinks, and connectors, meeting the demand for lightweight and durable components in consumer electronics and industrial equipment.
Medical Equipment Fabrication Using Sheet Metal Forming
Sheet metal forming plays a pivotal role in manufacturing medical equipment, encompassing the production of surgical instruments, diagnostic devices, and enclosures for medical devices, ensuring precision, cleanliness, and biocompatibility.
Utilization of Sheet Metal Forming in Various Industries
Sheet metal forming finds applications across diverse industries, including architecture, energy, and consumer goods, demonstrating its versatility and adaptability in meeting diverse manufacturing needs.
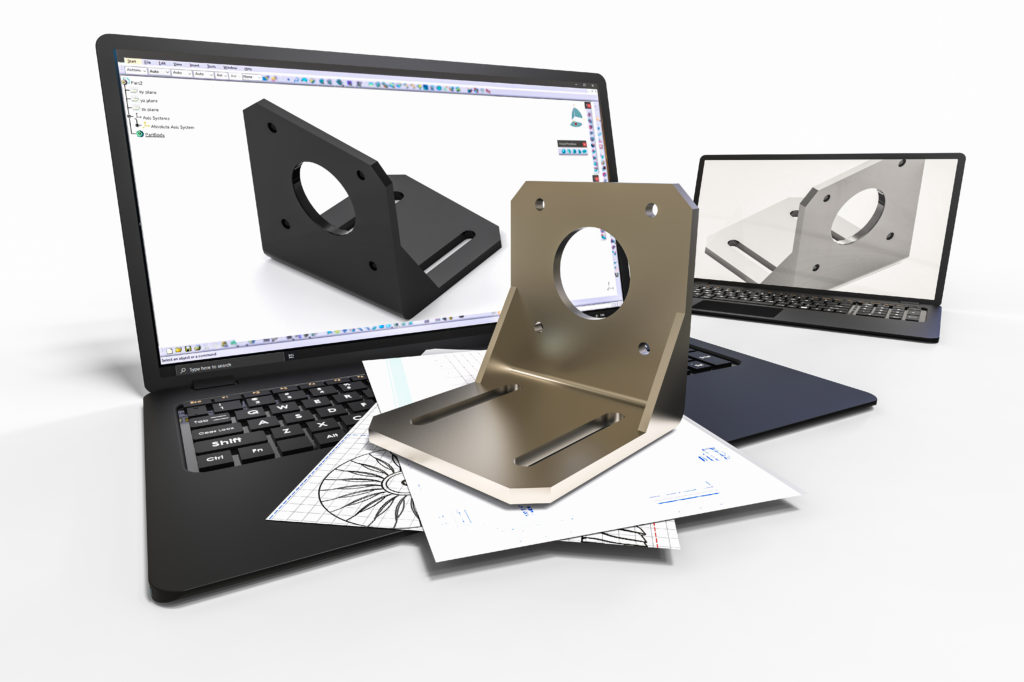
Advancements and Technologies in Sheet Metal Forming
Integration of Computer-Aided Design (CAD) in Sheet Metal Forming
The integration of computer-aided design (CAD) software facilitates the creation of intricate sheet metal part geometries, enabling designers to visualize and optimize components prior to fabrication.
Simulation Software for Sheet Metal Forming Processes
Simulation software allows engineers to predict and analyze the behavior of metal sheets during forming processes, optimizing tooling designs and material utilization while reducing lead times and costs.
Automated Forming Processes and Robotics in Sheet Metal Fabrication
The incorporation of automated forming processes and robotics enhances the efficiency and repeatability of sheet metal fabrication, reducing manual labor and increasing production throughput.
Improvement in Efficiency and Precision through Advanced Technologies
Advancements in laser cutting, additive manufacturing, and material science contribute to enhancing the efficiency, precision, and material utilization in sheet metal forming, fostering innovation and sustainability in the manufacturing industry.
Case Studies and Examples in Sheet Metal Forming
Real-World Examples of Sheet Metal Forming Projects
Real-world projects showcase the application of sheet metal forming in diverse industries, illustrating the versatility and adaptability of the process in producing complex and high-performance components.
Demonstrating Successful Application of Sheet Metal Forming
Case studies highlight successful applications of sheet metal forming, emphasizing the achievement of intricate geometries, material optimization, and cost-effective production in various manufacturing scenarios.
Versatility and Capabilities in Producing Complex Parts through Sheet Metal Forming
The versatility of sheet metal forming is exemplified through the production of complex and lightweight components, ranging from intricate architectural elements to high-strength aerospace structures, demonstrating the process’s capabilities in meeting diverse industry requirements.
Future Trends in Sheet Metal Forming
Integration of Additive Manufacturing Techniques in Sheet Metal Forming
The integration of additive manufacturing, such as 3D printing, with traditional sheet metal forming processes presents opportunities for creating complex, lightweight, and customized components with enhanced design freedom and material efficiency.
Advancements in Material Science for Sheet Metal Forming
Ongoing advancements in material science lead to the development of innovative alloys and composites tailored for sheet metal forming, offering superior strength, corrosion resistance, and formability for next-generation applications.
Impact of Industry 4.0 on Precision Sheet Metal Fabrication and Forming Processes
The implementation of Industry 4.0 technologies, including IoT-enabled manufacturing, machine learning, and digital twinning, revolutionizes precision sheet metal fabrication, enhancing process monitoring, automation, and adaptability in response to dynamic production requirements.
Conclusion
Summarization of Key Points in Sheet Metal Forming and Precision Fabrication
Sheet metal forming is a fundamental process in precision fabrication, encompassing diverse techniques, materials, and applications crucial for meeting the evolving demands of modern manufacturing.
Ongoing Evolution of Sheet Metal Forming Processes
The continuous evolution of sheet metal forming processes, driven by technological advancements and material innovations, underscores the importance of staying abreast of emerging trends and capabilities in the field of precision fabrication.
.