Are you having trouble bending sheet metal parts with precision? The Salvagnini Panel Benders offers a reliable and automated solution to form sheet metal parts. This blog post will explain how this panel bender works, the benefits it has over traditional methods of bending sheet metal, and some important technical specifications to consider while purchasing one.
Get ready to learn all about mastering the art of sheet metals bending with the help of a Salvagnini Panel Benders!
Key Takeaways
- The Salvagnini Panel Bender offers reduced set up times and shorter cycle times with more consistent results than with traditional press brakes.
- It features universal bending tools that provide versatility and automation software for easy programming.
- It offers a single operator the ability to perform downstream operations like hardware insertion or spot welding simultaneously during the bend cycle.
The Benefits of Using the Salvagnini Panel Bender
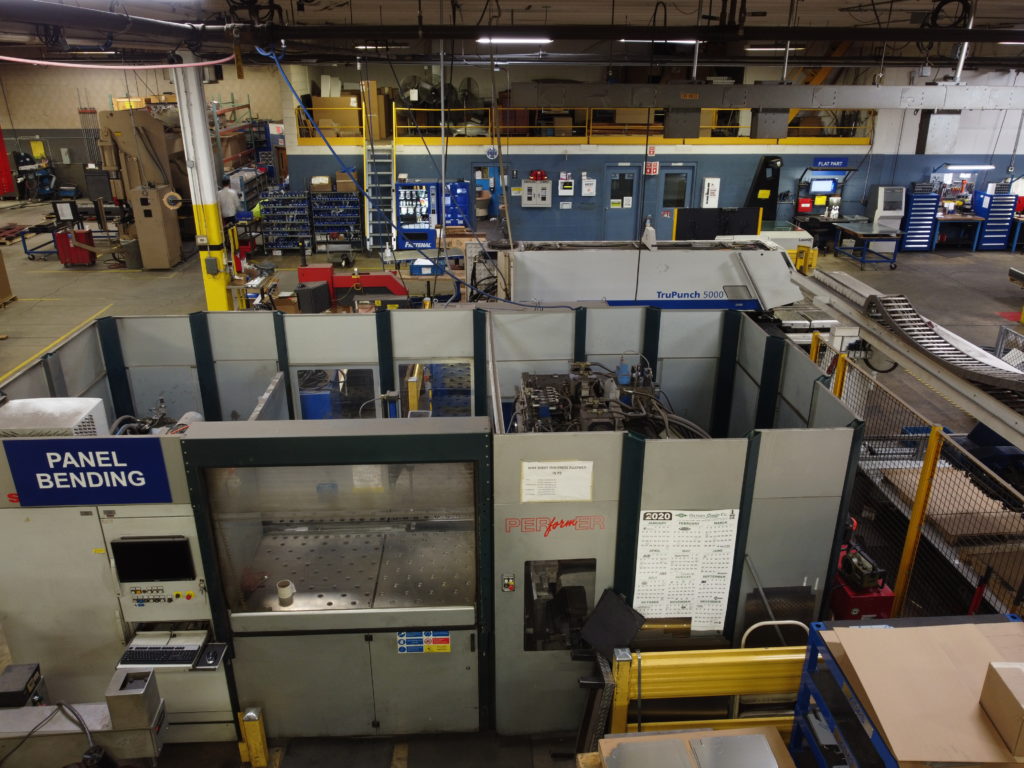
This high-performance bending solution provides sustainable and compact operation, quick production, controlled centering capability and a proprietary formula for consistent results.
Efficient and fast bending solution
The Salvagnini P2 Panel Bender offers an unparalleled level of speed and compactness when it comes to sheet metal bending. Utilizing electro-pneumatic actuators for positioning the work piece and powerful hydraulic bending cylinders driven by efficient brushless motors, makes Salvagnini Panel Benders the go-to choice for many companies including Atlas Precision Sheet Metal Solutions
What sets Salvagnini Panel Benders apart from other traditional sheet metal forming methods is the accuracy, speed and flexibility thanks to Salvagnini’s use of precision controlled centering alignment in combination with a proprietary bending formula that guarantees both consistent product quality as well as efficient production runs; exceeding expectations across all metrics.
The reality of this configuration is not just greater energy efficiency but also tremendous savings on valuable floor space thanks to its incredible compact size.
Simple, quick, and lean operation
Salvagnini Panel Benders offer a simple, quick and lean operation that makes it the ideal sheet metal bending tool for companies looking for precision manufacturing solutions.
The P2 panel bender achieves bending on each side of the sheet through interpolation controlled movements of the forming tools, enabling rapid yet precise production with consistent results.
The intuitive interface also allows users to quickly input parameters directly into the machine, meaning you can get right back to creating complex shapes in no time. This intelligent system ensures superior control over centering accuracy during bending operations as well as offering a proprietary formula designed especially for near perfect bends.
Controlled centering
The Salvagnini P2 Panel Bender, used by Atlas Manufacturing, is equipped with the capability of controlled centering – a feature that sets it apart from other sheet metal forming systems.
Controlled centering allows for consistent quality by minimizing cycle time and ensuring precision in the bending process. In addition to reducing labor requirements and simplifying the set-up process, this technology also increases productivity in batch-one or kit productions.
The benefits of controlled centering go beyond just efficiency; thanks to its proprietary bending formula, it produces superior results with traditional bend geometry as well as larger radius bends formed by bump forming —all without sacrificing accuracy.
Proprietary bending formula
The Salvagnini P2 Panel Bender offers its users a truly unique and proprietary bending formula for calculating bending parameters and checking press-brake set-ups. This exclusive software uses mathematics, physics, and mechanics principles to optimize the movements of the machine’s universal tooling, providing accurate results while reducing time and costs.
The variables within the proprietary formula can be adjusted easily in order to get different angles with just one click of a mouse. As compared to traditional set-ups using mechanical methods such as correction factors or compensation tables, this system yields far more consistent results since it measures in real time different parameters such as speed during movement, force applied on bent profile sections or clamp position variations when forming parts along multiple bends curves.
What’s more is that thanks to its flexibility, users of these panel benders can now customize their projects according to specific requirements without having any concerns about accuracy or precision!
Intelligent system for consistent quality
The Salvagnini P2 Panel Bender utilizes an intelligence system along with its proprietary bending formula to ensure consistent quality and accuracy during sheet metal bending process. This proprietary formula continuously monitors and adjusts the bending parameters, adapting to different panel geometries and thicknesses for optimal results.
This intelligence system and proprietary bend formula eliminates the need for retooling based on bend allowance, thus saving time as well as reducing chances of errors. As a result, production becomes more efficient with increased productivity in sheet metal work for the aerospace or medical device manufacturers where precision is crucial..
Companies that produce precision Sheet Metal components like Atlas Manufacturing rely on the Salvagnini Panel Bender’s intelligent system to ensure high levels of consistency that meets their needs.
How the Salvagnini Panel Bender Works
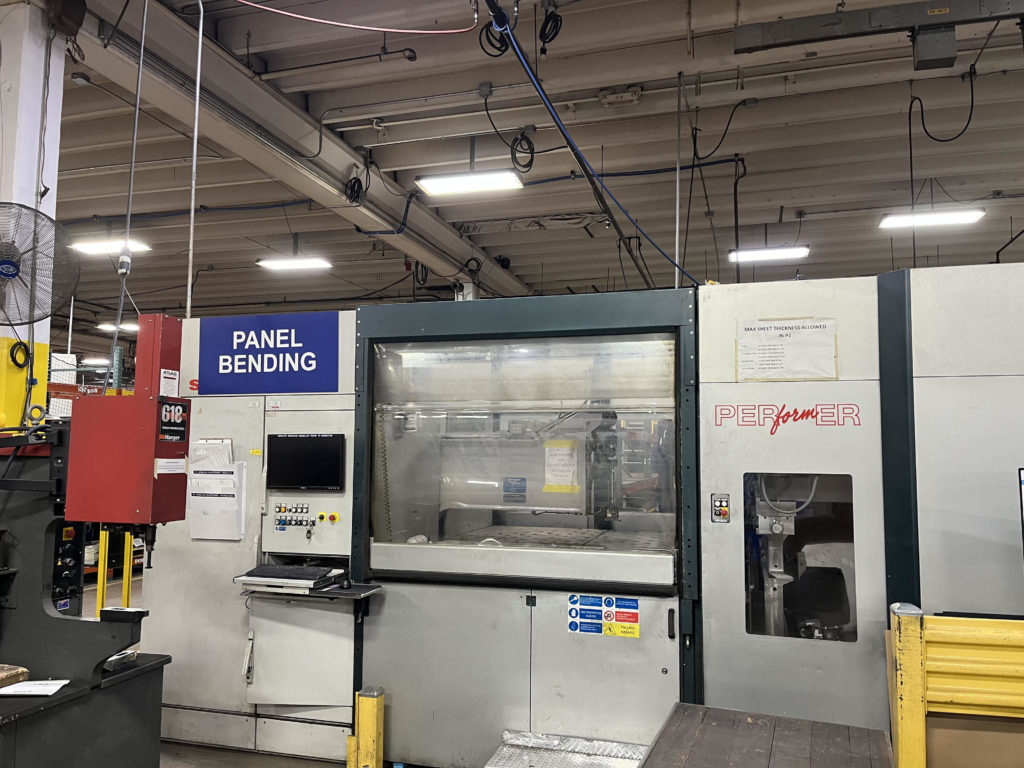
Universal bending tool
All Salvagnini Panel Benders feature universal bending tools similar to the tooling used an a manual box and pan brake also known as a finger folder which contribute to its versatility and productivity. This tool, allows for sheet metal to be bent into a wide range of shapes with precision and consistency.
It also offers efficient operation due to the intelligent system it operates on – a proprietary algorithm that ensures quality bends every time regardless of the shape or complexity.
Flexible automation
Flexible automation with the Salvagnini Panel Bender revolutionizes the sheet metal bending process for companies seeking precision fabrication. This sustainable and compact bending solution boasts a simple, quick, and lean operation as well as the proprietary bending formula that drives controlled centering that provides consistent quality results.
Additionally, its intelligence system minimizes machine downtime and manual re-tooling while upgrading labor productivity, part accuracy, speed of production, and efficiency.
Salvagnini Panel Benders are trusted by top organizations around the world due to its unmatched production capabilities – making it number one amongst all types of panel benders worldwide today.
Advantages Over Press Brakes
Salvagnini Panel Benders offer industry-leading customization, consistent quality, and flexible production capabilities far superior to traditional press brakes.
Industry-leading customization
Salvagnini Panel Benders offer unprecedented customization options for sheet metal bending. The panel bender utilizes advanced CNC technology to automate the bending process and offer superior customization capabilities. Thanks to the Salvanini P2 Panel Benders high level of reliable automation multiple bends on multiple different planes can be completed without an operator handling the parts multiple times freeing up the operator to preform multiple downstream operations like hardware insertion, spot welding, labeling and packaging , or even subcomponent assembly during the bending cycle.
Unlike press brakes, the panel bender allows users to control the operating functions of each associated axis from a centralized individual console – providing various options for positions and shapes that are impossible to recreate with other machines.
By using this new automation system, businesses can achieve very unique bends quickly and efficiently at an impressive level of accuracy and consistency. With its ability to intelligently capture data, create simulations in real-time, monitor status updates continually, you can trust it will provide the highest quality bends every time while eliminating wasted material caused by trial-and-error iterations due to manual operation processes or complicated programming constrictions characteristic of traditional press brakes.
Consistent quality
The Salvagnini Panel Bender ensures consistency in sheet metal bending through the use of its proprietary bending formula and controlled centering technology. This intelligent system has been adapted for maximum precision to ensure consistently high-quality results, fast operation, and lean production capabilities.
Flexible production capabilities
Salvagnini Panel Benders offer unbeatable flexibility in production, allowing for the bending of panels to exact specifications and at high speed. The Universal Bending Tools adjust automatically to panel geometry, resulting in improved productivity and reduced downtime due to machine retooling set up.
Moreover, its flexible automation capabilities reduce the need for multiple tools normally used with press brakes. This lean and efficient production makes it an ideal choice for companies that require precision sheet metal manufacturing services.
With the Salvagnini Panel Bender providing consistently-high quality results and faster turnaround times even on complex parts, it’s no wonder why it is one of the most popular solutions within the sheet metal subcontractor industry today.
#1 in panel benders worldwide
Salvagnini panel benders are widely recognized and highly revered as the #1 panel bender in the world. Founded over 40 years ago, with a legacy of innovation, expertise and quality, Salvagnini has thousands of installations around the globe in 76 countries.
Salvagnini panel benders make for an incredibly useful asset for companies that require maximum production output without sacrificing quality or cutting corners on safety protocols for their advanced precision formed sheet metal parts.
Contact Atlas Manufacturing
For high-precision sheet metal fabrication services, Atlas Manufacturing is the perfect partner. Their industry-leading customization capabilities provide consistent quality of production and results every time they take on a project.
A Precision Sheet Metal Fabricator
Atlas Manufacturing is a renowned name in precision sheet metal manufacturing with decades of expertise and the latest technology. Through its state-of-the-art Salvagnini Panel Bender, Atlas offers sustainable and compact bending solutions with simple, quick, and lean operating mode for controlled centering as well intuitive system for consistent quality.
With a detail oriented approach towards precision sheet metal fabrication services along with powder coating, The devoted team at Atlas Manufacturing are dedicated to providing customers reliable products that meet their needs perfectly whether it be small scale or large production runs.
Why choose Atlas Manufacturing for your sheet metal forming needs
Atlas Manufacturing is an industry leader in precision sheet metal forming solutions. Their commitment to quality and mastery of sheets metal bending makes them the ideal partner for companies looking to create high-quality, custom products.
With their Salvagnini Panel Bender technology, Atlas has revolutionized the entire process by utilizing universal bending tools which simplify production with minimal re-tooling and lengthen product life with consistent results over time.
By partnering with Atlas Manufacturing, businesses benefit from a wide range of services including bending, curling, ironing, laser cutting hydroforming and punching – perfect for any modern manufacturing needs.
FAQs
1. What is the Salvagnini P2 Panel Bender?
The Salvagnini P2 Panel Bender is a cutting-edge sheet metal bending machine with precise mechanical and software capabilities for forming complex shapes with accuracy and ease.
2. How does the Salvagnini Panel Bender work?
The machine works by clamping material onto an X-axis table that moves the work around a table to position the work piece properly between a stationary bar that acts as an anvil and a series of mechanical tools that bend the unclamped portion of work material into the desired bend shape.