In the dynamic landscape of manufacturing, the pursuit of efficiency is a relentless journey. At Atlas Manufacturing, we have long been reshaping the contours of precision sheet metal fabrication, establishing us as a venerable entity in the industry since 1962. One transformative innovation we’ve adopted is top shelf tool systems.
Beyond being technological marvels that elevate fabrication shop organizations, these systems embody our unwavering commitment to Lean Manufacturing principles. In this final part of our series of articles, we will emphasize how top shelf tool systems highlight the roles of “Standardize” and “Sustain.”
Embracing Principles of the Lean Production System
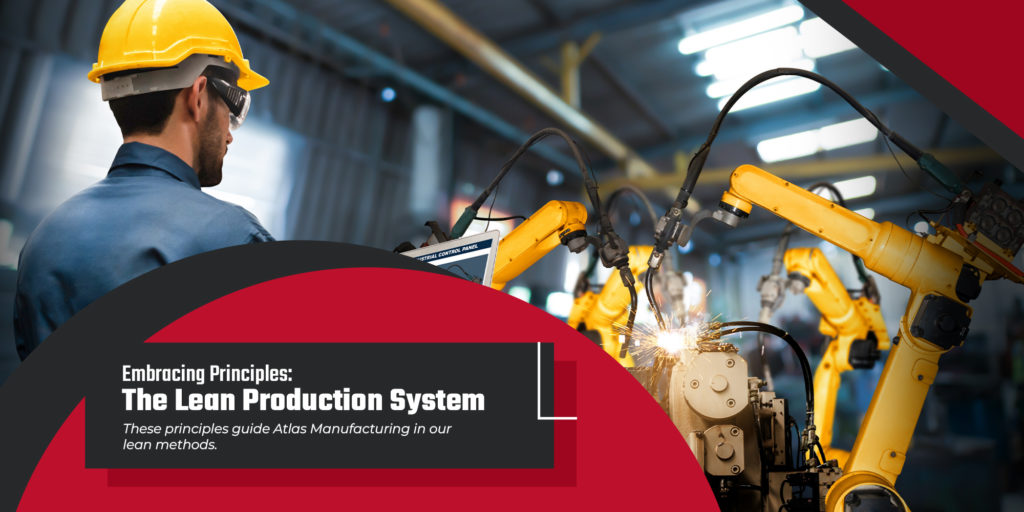
In Lean Manufacturing, associated with the Toyota Production System (TPS) given its origin in the automotive industry, two principles are crucial: Standardize and Sustain. As part of an efficient framework of scientific management, these principles guide Atlas Manufacturing in our lean methods.
Standardize: The Pillar of Consistency
Atlas Manufacturing’s adoption of the “Standardize” or “seiketsu” principle is a commitment to unwavering consistency. From the meticulous arrangement of tools in the new top shelf tool systems to the establishment of protocols, schedules, and responsibilities, standardization becomes a symphony that orchestrates daily operations.
By setting uniform guidelines and procedures, Atlas ensures that the gains achieved through our innovative tool systems aren’t fleeting victories but enduring assets. It’s not about a one-time organization overhaul, but instead about weaving efficiency and order into the fabric of our daily routines.
Sustain: Nurturing the Seeds of Efficiency
“Sustain” or “shitsuke” is a continuous stride towards maintaining excellence. At Atlas Manufacturing, our dedication to Lean principles does not waver once the systems are in place. We nurture a culture where orderliness, safety, and efficiency become second nature.
Through “Sustain,” Atlas ingrains the practice of the 5S methodology into the company’s ethos. We foster discipline, ensuring that the 5S system is not just a set of guidelines but a way of life, cultivating a workforce that instinctively upholds the principles of Lean Manufacturing and making the identification of waste or anomalies an instinctive act.
The Challenge With Traditional Rack and Shelf Systems
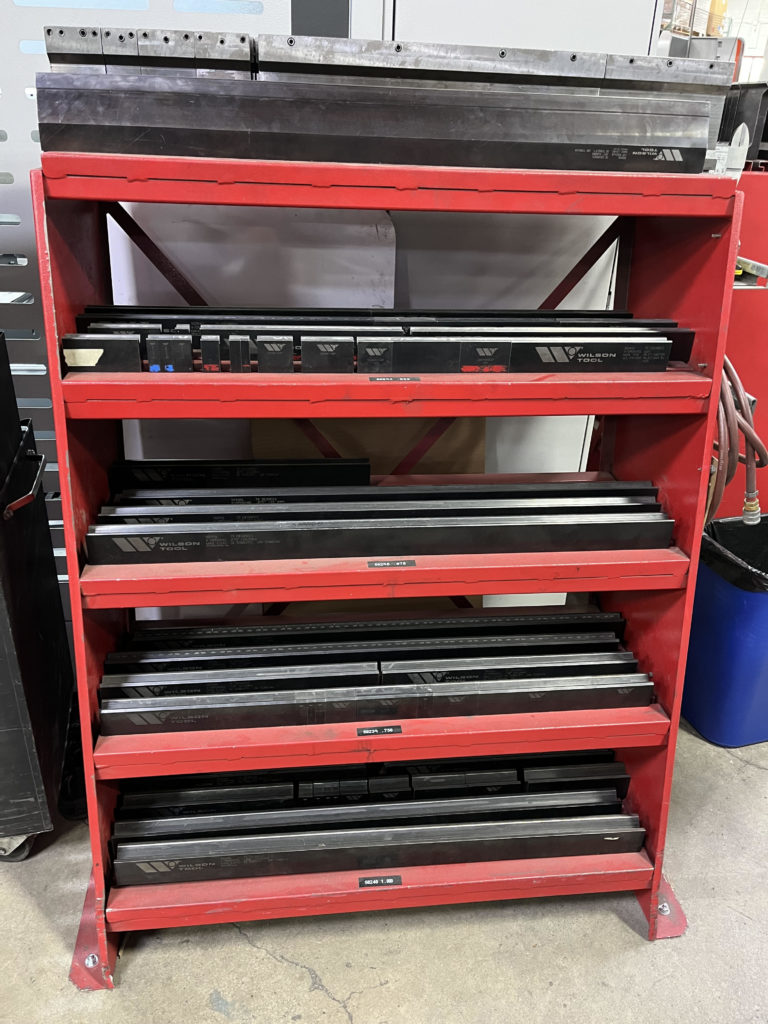
Before the birth of the groundbreaking Top Shelf Tool Systems, Atlas Manufacturing faced limitations imposed by conventional rack and shelf setups. While these systems were the go-to for tool storage, they harbored inefficiencies that hindered productivity and safety.
Scattered Tools
Within the manufacturing floor’s expansive space, tools scattered across racks and shelves became hurdles to efficiency. The absence of designated tool spaces resulted in lost minutes, often accumulating into hours, amidst misplaced equipment. Workers spent valuable time navigating disorganized tool arrangements, impeding operations’ fluidity and reducing productivity.
Inefficiencies and Downtime
The scattered layout of tools in the traditional rack and shelf system wasn’t merely inconvenient — it incurred tangible costs. Prolonged tool change times, worsened by the hunt for specific equipment, led to increased downtime at critical workstations like press brakes. Each minute spent searching for a misplaced tool translated to decreased productivity and strained operational efficiency.
Safety Concerns Amidst Disarray
Beyond affecting efficiency and productivity, disorganized tools posed significant safety risks. Cluttered storage setups heightened the chances of accidents. Workers navigating through a sea of tools faced an increased risk of trips, falls, and potential injuries.
Implementation of Innovative Mobile Top Shelf Tool Systems
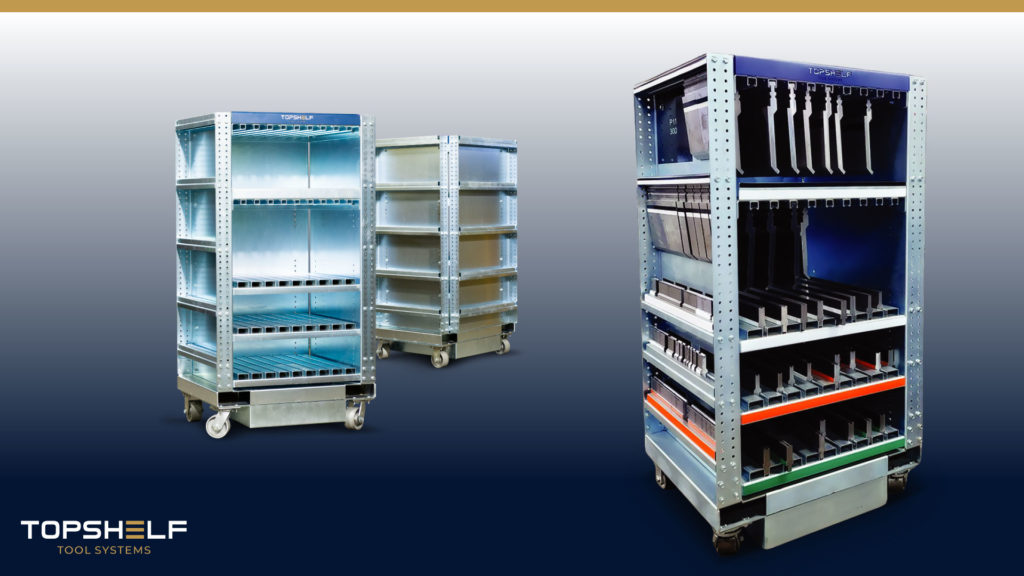
In response to the inefficiencies plaguing traditional tool storage, Atlas Manufacturing unveiled a game-changing solution — Top Shelf Tool Systems. These industry-leading tool storage systems represent a paradigm shift in fabrication shop organization, offering unparalleled efficiency, accessibility, and safety.
One of the key features distinguishing Top Shelf Tool Systems is their mobility. Placing a Top Shelf Tool System adjacent to your machine reduces handling times and distances significantly. The system’s mobility brought tools closer to press brakes. This strategic placement optimizes workflow, minimizing downtime and enhancing productivity.
Transformative Outcomes: Redefining Efficiency and Safety
The integration of Atlas’s Top Shelf Tool Systems heralded a new era, ushering in transformative outcomes that reshaped the very fabric of operational efficiency and safety within fabrication shops. Unlike manufacturing resource planning (MRP) systems that used push systems, implementing Lean established a pull system.
Streamlined Tool Changes: Boosting Productivity
The most palpable impact surfaced in the realm of press brake operations. With the implementation of Top Shelf Tool Systems, tool changes at press brakes underwent a revolutionary transformation. What was once a time-consuming endeavor plagued by the search for specific tools evolved into a seamless process.
Heightened Safety: A Paramount Priority
Safety, an intrinsic value at Atlas, soared to new heights with the introduction of these innovative tooling solutions. The organized and easily accessible nature of the Top Shelf Tool Systems mitigated the hazards posed by scattered tools. Reduced clutter translated to a safer work environment, diminishing the risk of accidents.
Introduction of Atlas’s Product Line: Innovation Personified
Beyond the immediate operational enhancements, the implementation of Top Shelf Tool Systems opened doors to a new chapter of innovation. Atlas ventured into introducing its own product line, leveraging our expertise in fabrication and tooling organization. These products, born from Atlas’s commitment to excellence, became invaluable assets for other manufacturers seeking streamlined tooling solutions.
Conclusion: Pioneering Lean Innovation for Continuous Improvement
Atlas Manufacturing’s adoption of the Top Shelf Tool Systems embodies a commitment to continuous improvement and Lean thinking within the production process. These systems signify more than an upgrade in our supply chain; they represent a cultural shift rooted in Lean principles.
Through this innovation, Atlas achieved streamlined tool changes, heightened safety, and a new product line. Accordingly, we forged a path of efficiency and innovation. This journey reflects a future where Lean thinking seamlessly integrates into the production process.