Precision Original Equipment Manufacturer (OEM) sheet metal fabrication plays a crucial role in the manufacturing industry, providing high-quality components and custom solutions for various sectors. In this comprehensive guide, we will explore the definition, processes, advantages, industries, leading manufacturers, key processes and machinery, materials, and tips for choosing an OEM sheet metal fabrication supplier. Whether you are a professional in the field or someone looking to understand more about this industry, this guide will provide valuable insights.
What the reader will learn by reading the article:
- Definition and key features of OEM sheet metal fabrication
- Processes and technologies involved in OEM sheet metal fabrication
- Advantages of partnering with an OEM for sheet metal fabrication needs
- Industries that extensively rely on OEM sheet metal fabrication
- Leading OEM sheet metal fabrication manufacturers
- Key processes, machinery, and materials used in OEM sheet metal fabrication
- Tips for choosing an OEM sheet metal fabrication supplier
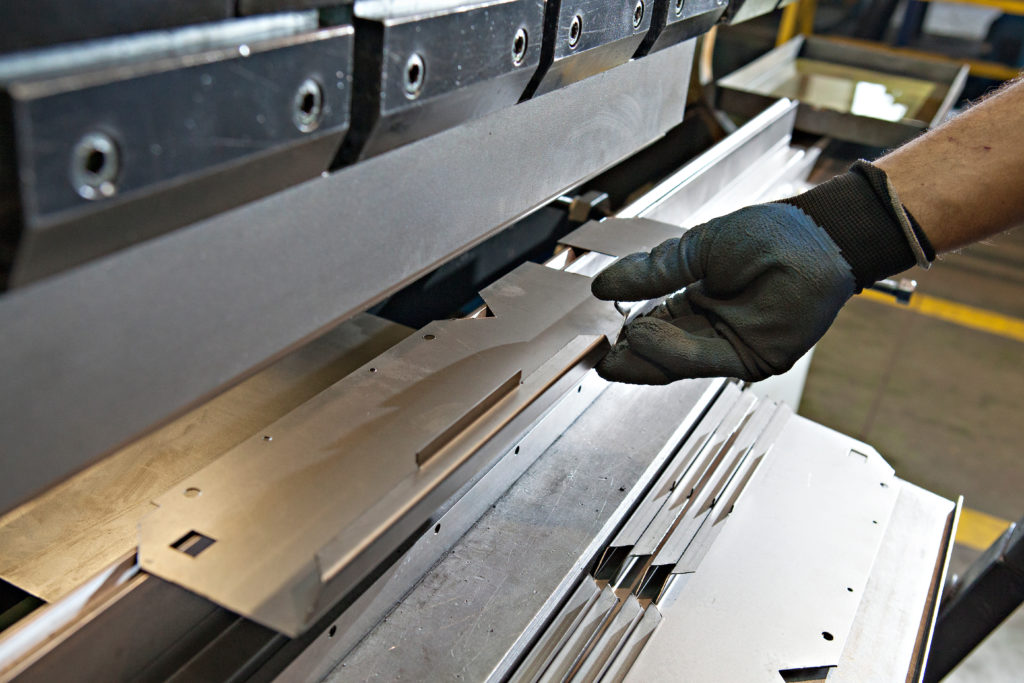
Understanding OEM Sheet Metal Fabrication
1.1 Definition and key features of OEM sheet metal fabrication
OEM sheet metal fabrication refers to the process of producing precision metal components and assemblies according to the specifications and requirements of original equipment manufacturers. These manufacturers often outsource their sheet metal fabrication needs to specialized companies with expertise in producing high-quality products. OEM sheet metal fabrication involves various processes, including cutting, bending, welding, and finishing, to create components that meet the exact specifications of the OEMs.
1.2 Overview of the precision manufacturing industry and its reliance on OEM services
The precision manufacturing industry focuses on producing highly accurate and intricate components for various applications. It heavily relies on OEM services, including sheet metal fabrication, to meet the demand for precision parts. OEMs play a vital role in this industry by providing specialized expertise, advanced technologies, and cost-effective solutions for manufacturing complex components.
1.3 Importance of precision in OEM sheet metal fabrication and its impact on product quality
Precision is of utmost importance in OEM sheet metal fabrication. The ability to meet tight tolerances and maintain consistent quality ensures that the final products function as intended. Precision in sheet metal fabrication impacts the overall performance, durability, and reliability of the finished products. Components with precise dimensions and accurate specifications result in improved efficiency and reduced chances of failure or malfunction.
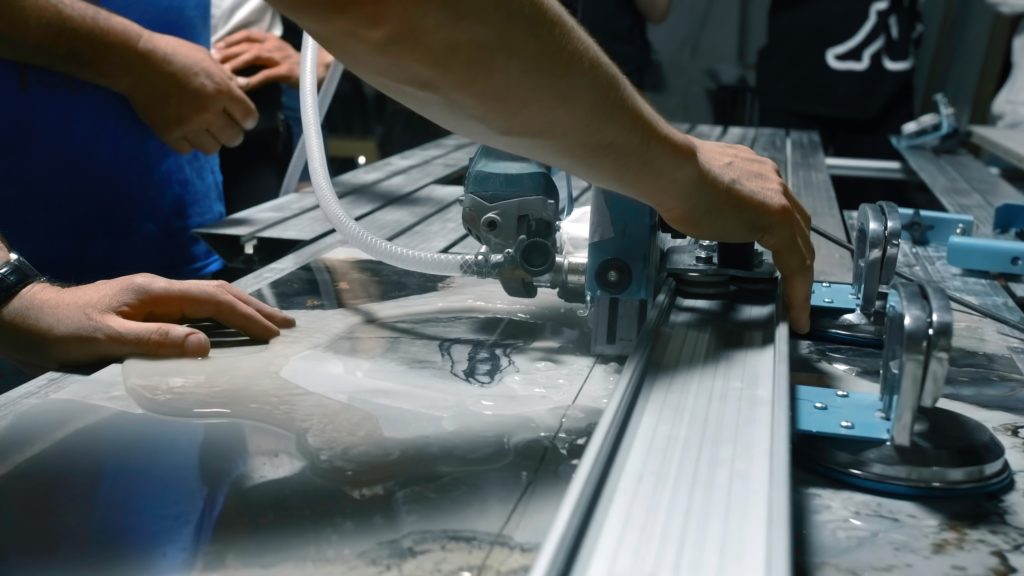
Processes involved in OEM Sheet Metal Fabrication
2.1 Overview of cutting, bending, welding, and finishing processes in OEM sheet metal fabrication
OEM sheet metal fabrication involves several essential processes to shape and transform raw materials into finished components. These processes include cutting, bending, welding, and finishing.
Cutting: The cutting process involves removing excess material from metal sheets to achieve the desired shapes and sizes. Advanced cutting techniques, such as laser cutting and waterjet cutting, ensure precise and clean cuts.
Bending: Bending is the process of shaping metal sheets into specific angles or curves. It is commonly achieved using press brakes or other bending machines. Accurate bending is crucial to ensure the proper fit and functionality of the components.
Welding: Welding joins metal parts together using various techniques, such as MIG welding, TIG welding, or spot welding. Welding is essential for creating strong and durable connections between different components.
Finishing: The finishing process involves surface treatments, such as sanding, grinding, and painting, to enhance the appearance and protect the components from corrosion or wear. Surface finishing can also include adding protective coatings or applying decorative finishes.
2.2 Importance of each process and its impact on the final product
Each process in OEM sheet metal fabrication plays a crucial role in determining the quality and functionality of the final product.
Cutting: Accurate cutting ensures that the components are precisely shaped and fit together seamlessly. Clean cuts also reduce the need for additional machining or finishing processes.
Bending: Proper bending ensures that the components have the desired angles and curves, allowing them to fit into assemblies correctly. Precise bending also contributes to the overall structural integrity of the components.
Welding: Welding creates strong and reliable connections between metal parts. High-quality welding ensures that the joints can withstand the intended loads and stresses, providing long-lasting durability.
Finishing: Surface finishing not only enhances the appearance of the components but also protects them from environmental factors, such as corrosion or abrasion. It improves the overall aesthetics and extends the lifespan of the products.
2.3 Advanced techniques and technologies used in precision sheet metal fabrication
Precision sheet metal fabrication has benefited greatly from advancements in technology. Several advanced techniques and technologies are now commonly used in the industry.
Computer Numerical Control (CNC) Machining: CNC machines utilize computer programming to control the movement and operation of cutting, bending, and forming tools. CNC machining ensures high accuracy and repeatability in the manufacturing process.
Laser Cutting: Laser cutting utilizes a concentrated beam of light to cut through metal sheets with precision. It offers exceptional accuracy, speed, and versatility, making it a popular choice in precision sheet metal fabrication.
Robotic Welding: Robotic welding automates the welding process using robotic arms. It ensures consistent weld quality, reduces cycle times, and enhances productivity. Robotic welding is particularly beneficial for high-volume production.
3D Printing: Although still in its early stages for sheet metal fabrication, 3D printing shows great potential for creating complex geometries and prototypes. It offers faster production times and reduced material waste.
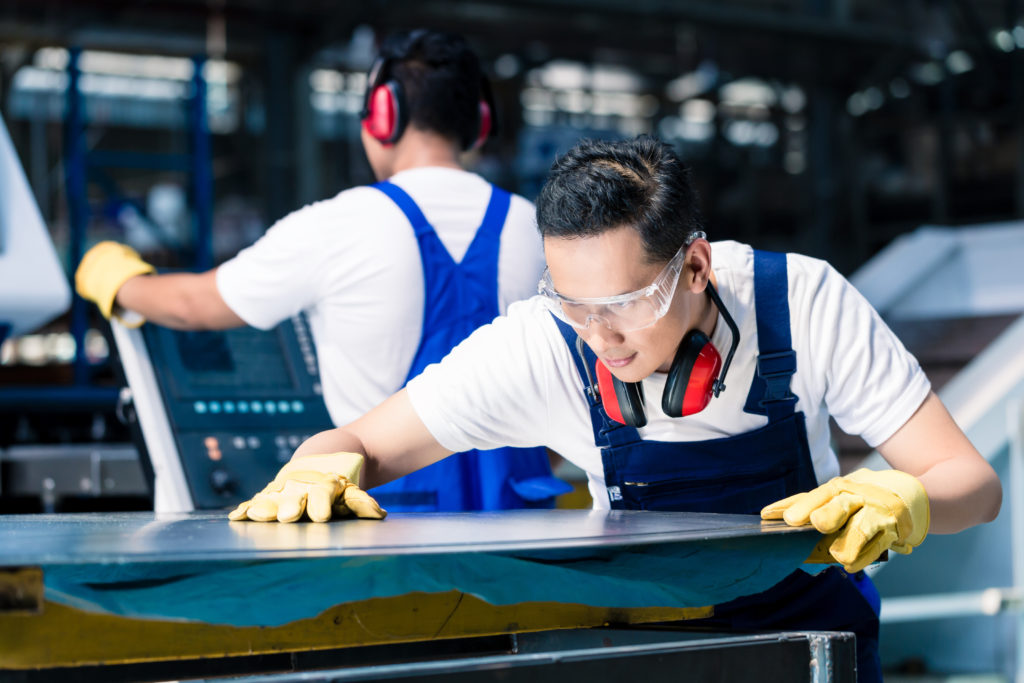
Advantages of OEM Sheet Metal Fabrication
3.1 Explanation of the OEM concept and its role in the manufacturing industry
Before delving into the advantages of OEM sheet metal fabrication, it is essential to understand the OEM concept. OEM stands for Original Equipment Manufacturer, which refers to companies that manufacture products or components that are used in the products of other companies. In the context of sheet metal fabrication, OEMs specialize in producing high-quality metal components for various industries.
3.2 Benefits of partnering with an OEM for sheet metal fabrication needs
Partnering with an OEM for sheet metal fabrication offers numerous benefits for businesses.
Expertise and Specialization: OEMs have extensive experience and specialized knowledge in sheet metal fabrication. They understand the intricacies of the processes involved and can provide valuable insights to optimize designs and improve manufacturing efficiency.
Cost-effectiveness: OEMs often have the necessary infrastructure, equipment, and skilled workforce to carry out sheet metal fabrication at a large scale. By outsourcing to an OEM, businesses can avoid the costs associated with setting up their own fabrication facilities and training personnel.
Customization Options: OEMs can tailor their fabrication processes to meet the specific requirements of their clients. They can accommodate various design changes, material choices, and finishing options to ensure that the final products align with the customers’ needs.
Quality Assurance: OEMs prioritize quality control throughout the fabrication process. They have established quality management systems and adhere to industry standards to ensure that the finished components meet the highest quality standards.
3.3 Cost-effectiveness, expertise, and customization options offered by OEM manufacturers
Cost-effectiveness: OEM sheet metal fabrication can be a cost-effective solution for businesses. By partnering with an OEM, companies can avoid the expenses associated with setting up their own fabrication facilities, investing in machinery, and training personnel. OEMs often operate at a larger scale, allowing them to leverage economies of scale and offer competitive pricing.
Expertise: OEM manufacturers specialize in sheet metal fabrication, investing in advanced machinery, processes, and skilled personnel. Their expertise and experience enable them to produce high-quality components with precision and efficiency. By leveraging their expertise, businesses can benefit from improved product quality and reduced lead times.
Customization Options: OEM manufacturers understand that each customer’s requirements are unique. They offer customization options to accommodate specific design needs, material preferences, and finishing requirements. With the ability to tailor their fabrication processes, OEMs can deliver components that meet the exact specifications of their customers.
By partnering with an OEM for sheet metal fabrication needs, businesses can focus on their core competencies while leveraging the expertise and resources of specialized manufacturers. This collaboration results in cost-effective solutions, high-quality components, and increased overall efficiency.
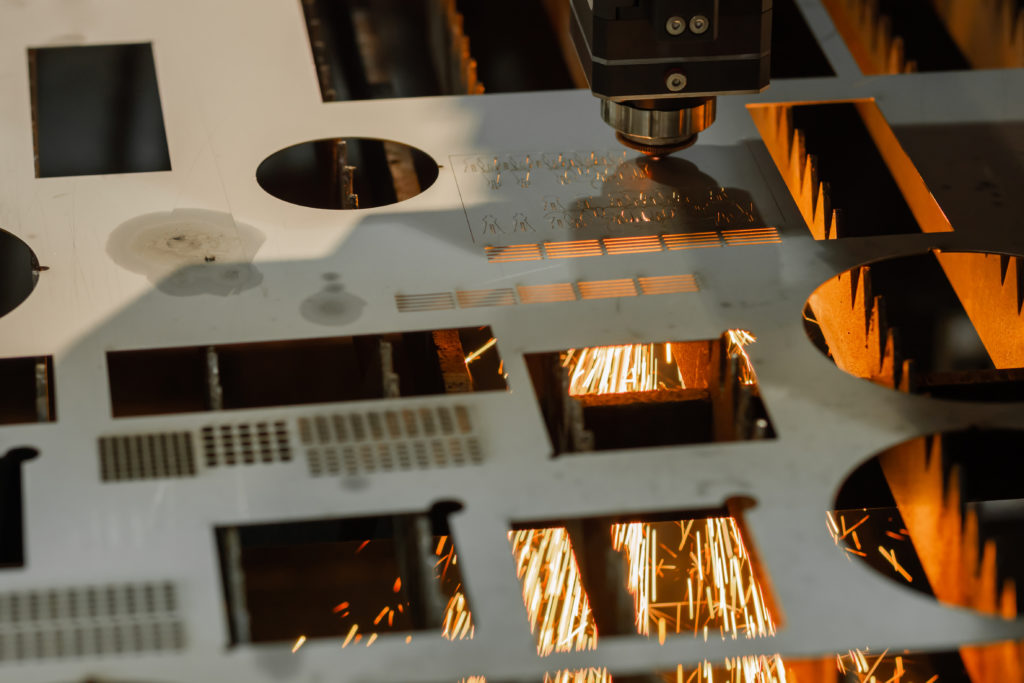
Industries Benefiting from OEM Sheet Metal Fabrication
4.1 Overview of industries that extensively rely on OEM sheet metal fabrication
Numerous industries extensively rely on OEM sheet metal fabrication to meet their manufacturing requirements. Some of the key sectors include automotive, aerospace, electronics, medical, and telecommunications.
4.2 Examples include automotive, aerospace, electronics, medical, and telecommunications sectors
Automotive Industry: The automotive industry utilizes OEM sheet metal fabrication to produce various components, including chassis, body panels, brackets, and engine parts. Precision fabrication ensures the structural integrity, safety, and performance of vehicles.
Aerospace Industry: Aerospace companies rely on OEM sheet metal fabrication to manufacture critical components for aircraft, such as fuselages, wings, engine parts, and landing gear. The precision and quality of these components are paramount to ensure flight safety.
Electronics Industry: OEM sheet metal fabrication is essential in the electronics industry for producing enclosures, panels, and racks for electronic devices and equipment. These components provide protection, organization, and aesthetic appeal to electronic products.
Medical Industry: The medical industry requires precision sheet metal components for medical devices, diagnostic equipment, and surgical instruments. OEM fabrication ensures the accuracy, safety, and reliability of these crucial medical tools.
Telecommunications Industry: OEM sheet metal fabrication plays a vital role in the telecommunications industry by producing components for communication equipment, server racks, and infrastructure installations. These components provide durability, protection, and efficient functionality for telecommunications networks.
4.3 Explanation of specific applications and components where OEM sheet metal fabrication is crucial
In the automotive industry, OEM sheet metal fabrication is crucial for producing components such as chassis, body panels, brackets, and engine parts. These components form the structural framework of vehicles and contribute to their performance, safety, and aesthetics.
In the aerospace industry, OEM sheet metal fabrication is essential for manufacturing critical components like fuselages, wings, engine parts, and landing gear. These components must meet stringent quality standards to ensure the safety and reliability of aircraft.
In the electronics industry, OEM sheet metal fabrication is vital for producing enclosures, panels, and racks for electronic devices and equipment. These components provide protection, organization, and aesthetic appeal to electronic products while ensuring optimal functionality.
In the medical industry, OEM sheet metal fabrication is crucial for manufacturing precision components for medical devices, diagnostic equipment, and surgical instruments. These components must meet strict tolerances and quality standards to ensure accuracy, reliability, and patient safety.
In the telecommunications industry, OEM sheet metal fabrication is essential for producing components for communication equipment, server racks, and infrastructure installations. These components provide durability, protection, and efficient functionality for telecommunications networks.
By leveraging the expertise of OEMs specializing in sheet metal fabrication, industries can benefit from high-quality components that meet their specific requirements and contribute to the overall success of their products.
Case Study: How XYZ Company Benefited from OEM Sheet Metal Fabrication
In this case study, we will explore how XYZ Company, an automotive manufacturer, benefited from partnering with an OEM sheet metal fabrication supplier.
XYZ Company was facing a challenge in producing a new line of automotive components due to the complexity of the design and the tight tolerances required. They needed a reliable partner who could deliver high-quality sheet metal fabrication services with precision.
After researching various options, XYZ Company decided to collaborate with ABC Manufacturing, an established OEM sheet metal fabrication supplier known for their expertise and customization capabilities.
ABC Manufacturing worked closely with XYZ Company’s engineering team to fully understand the design requirements and specifications. They used their advanced cutting, bending, and welding techniques to produce the intricate components with utmost precision.
The partnership with ABC Manufacturing proved to be highly beneficial for XYZ Company. The expertise and experience of the OEM supplier ensured that the automotive components met the required quality standards and specifications. The tight tolerances were consistently achieved, resulting in a significant reduction in product defects and rework.
Furthermore, by outsourcing their sheet metal fabrication needs to ABC Manufacturing, XYZ Company was able to focus on their core competencies and allocate resources more efficiently. This led to improved productivity and cost-effectiveness for the automotive manufacturer.
The collaboration between XYZ Company and ABC Manufacturing also allowed for customization options that perfectly aligned with the automotive industry’s specific requirements. The OEM supplier utilized their specialized tools and technologies to fulfill XYZ Company’s unique needs, resulting in a tailored solution that enhanced the overall performance and functionality of the automotive components.
In conclusion, XYZ Company’s partnership with ABC Manufacturing for OEM sheet metal fabrication services proved to be a strategic decision. By leveraging the expertise, advanced techniques, and customization options offered by the OEM supplier, XYZ Company was able to overcome their manufacturing challenges, improve product quality, and achieve greater efficiency in their operations. This case study highlights the advantages of partnering with a reputable OEM sheet metal fabrication supplier in the automotive industry.
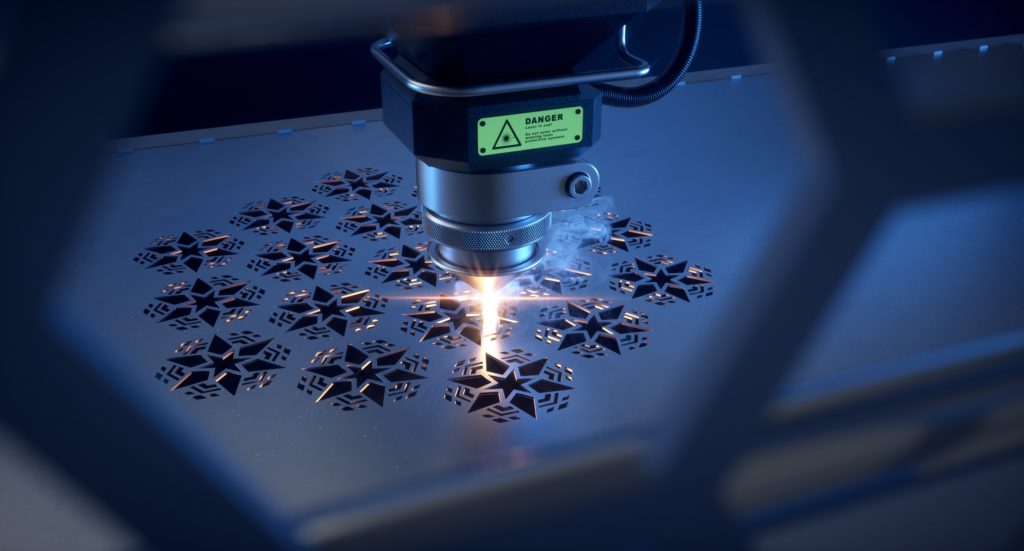
Leading OEM Sheet Metal Fabrication Manufacturers
5.1 Introduction to reputable manufacturers specializing in OEM sheet metal fabrication
Several reputable manufacturers specialize in OEM sheet metal fabrication, offering a wide range of capabilities and customized solutions. These manufacturers have established themselves as leaders in the industry, delivering high-quality products and services to meet the diverse needs of their clients.