In a world where customer expectations are continually on the rise, ensuring product quality has become an indispensable aspect of manufacturing. Atlas Manufacturing, a leading provider of sheet metal fabrication services, has demonstrated its expertise in implementing a Production Quality Plan (PQP) in a complex medical device project, resulting in high-quality production and FDA clearance. So, what is the secret behind their success? The answer lies in their meticulous approach to product quality planning, which involves customer satisfaction, error reduction, and streamlined manufacturing processes.
Key Takeaways
- Product Quality Planning is essential for customer satisfaction, error reduction and manufacturing process optimization.
- Advanced Product Quality Planning (APQP) provides an effective approach to streamline the manufacturing process.
- Process Failure Mode and Effects Analysis (PFMEA) & Test Method Reports are essential for ensuring accuracy of critical dimensions in the manufacturing process.
The Importance of Product Quality Planning
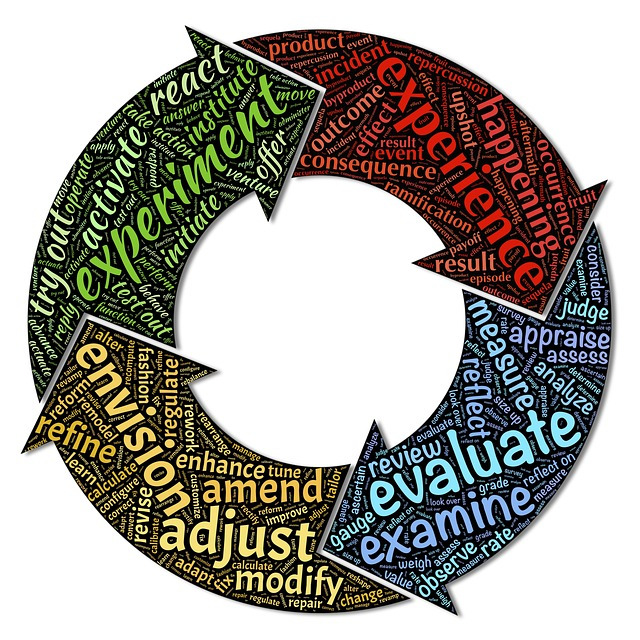
Product Quality Planning (PQP) plays a key role in customer satisfaction, error reduction, and manufacturing process streamlining. But why is it so important, and how does it contribute to the overall success of a manufacturing project?
Let’s delve deeper into the benefits of PQP and how it impacts various aspects of the manufacturing industry.
Customer Satisfaction
The correlation between product quality and customer satisfaction is undeniable. Customers are more content when they receive products of high quality that meet their requirements and expectations. Thorough testing activities, including the creation of test cases and analyzing test results, are imperative for guaranteeing product quality, as it provides valuable insights into product performance and effectiveness.
To ensure product quality, it is important to:
- Understand customer needs
- Set quality standards
- Implement quality assurance processes
- Verify product and process
- Continually improve product quality
By following these steps, PQP can meet or even exceed customer expectations.
Collecting valuable information from diverse sources like customer feedback and testing is essential to this process, as it allows us to provide feedback on the product’s performance.
Error Reduction
Maintaining product quality and minimizing potential losses requires a reduction of errors in the production process. PQP can reduce errors through assessment of the current workflow, implementation of technology, enhancement of worker training, creation of a mistake-proof plan, and maintenance of quality control practices. Gage R&R studies play a significant role in decreasing error by quantifying and distinguishing measurement error from part variation, allowing manufacturers to identify and address sources of variation in the measurement system. This leads to an increase in the accuracy and dependability of measurements.
Streamlined Manufacturing
Product Quality Planning, also known as Advanced Product Quality Planning (APQP), can streamline the manufacturing process by providing clear communication, effective planning, and efficient execution of quality standards and requirements from design to production. This structured process helps:
- Identify and eliminate inefficiencies
- Improve productivity
- Reduce costs
- Ultimately deliver a product that meets or exceeds customer expectations.
Adherence to APQP’s phases allows manufacturers to optimize workflow, boost product quality, and speed up market readiness by enhancing process capability. The phases include:
- Program planning
- Product design and development
- Process design and development
- Product and process validation
- Production launch
By following these manufacturing processes phases, manufacturers can ensure a systematic approach to their projects and achieve successful outcomes.
Advanced Product Quality Planning (APQP) in Action
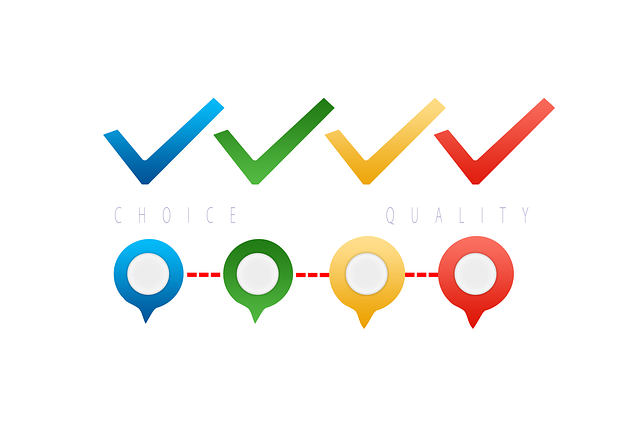
Advanced Product Quality Planning (APQP) follows a structured approach to product quality planning, using a series of processes and tools to confirm product quality. Developed in the late 1980s by a commission of experts from the ‘Big Three’ of the US automobile industry: Ford, GM, and Chrysler, APQP focuses on product quality and requirements from design to production, helping to streamline planning processes and improve efficiency.
APQP Process
The APQP process consists of several phases, including planning, design, development, and validation. Each phase serves a specific purpose in the product quality planning process. For instance, the planning phase facilitates clear communication, helps comprehend customer requirements, evaluates risks, and creates effective strategies for product development.
The product design and development phase, on the other hand, encompasses:
- Geometry
- Design features
- Details
- Tolerances
- Refinement of particular characteristics
Overall, APQP ensures that a product quality plan is generated, which will facilitate the development of a product or service that meets customer expectations.
APQP Tools and Techniques

APQP utilizes a variety of tools and techniques to identify and mitigate risks throughout the product development process. Some of the common tools and techniques used in APQP include:
- Failure Mode and Effects Analysis (FMEA)
- Statistical Process Control (SPC)
- Production Part Approval Process (PPAP)
- Control Plans
PFMEA, for instance, is a key tool for identifying and preventing potential failures in a product or system. It assists in identifying all potential or actual defects, errors, risks, or failures and prioritizes them based on their severity, occurrence, and detection. By employing these tools and techniques, APQP guarantees product quality and reduces risks throughout the product development process.
Atlas Manufacturing’s Approach to PQP: A Case Study
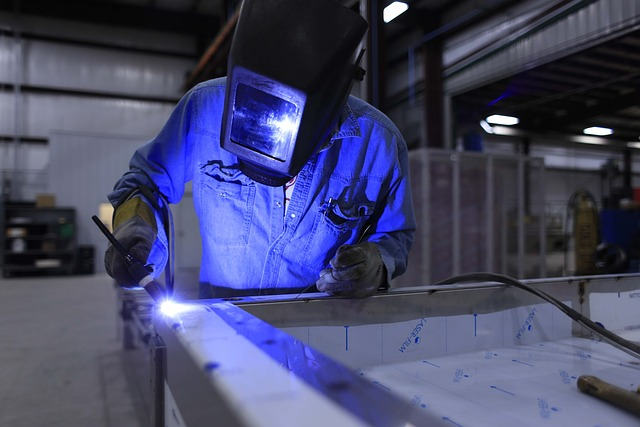
Atlas Manufacturing showcased its expertise in implementing a Production Quality Plan (PQP) in a complex medical device project with a major partner in the industry, spanning nearly two years. The company managed the transition from prototyping to production, underpinned by a well-structured PQP, ultimately resulting in high-quality production and FDA clearance.
Project Overview
This medical device project required Atlas Manufacturing to undertake the following steps:
- Readiness review
- Establish the manufacturing process
- Manufacture the medical device components
- Conduct the final testing and verification
The project timeline was contingent upon the complexity and size of the project, typically ranging from a few weeks to several months.
PQP Implementation
Atlas Manufacturing’s PQP implementation in the medical device project consisted of initial concept, product design, prototyping, device testing, design verification, and validation.
With a systematic approach to PQP, the company confirmed that their medical device adhered to the necessary quality standards and customer expectations, thanks to the test cases executed, leading to a successful project outcome.
Results and Impact
The implementation of Atlas Manufacturing’s PQP in the medical device project yielded high-quality production and FDA clearance, an impressive accomplishment in the competitive medical device industry. FDA 510(k) clearance indicates that the device has been subjected to a premarket submission to the FDA to demonstrate its safety and efficacy.
Maintaining high-quality standards, Atlas Manufacturing enhanced their chances of securing 510(k) clearance, reflecting their commitment to manufacturing excellence.
Gage R&R Studies for Quality Control
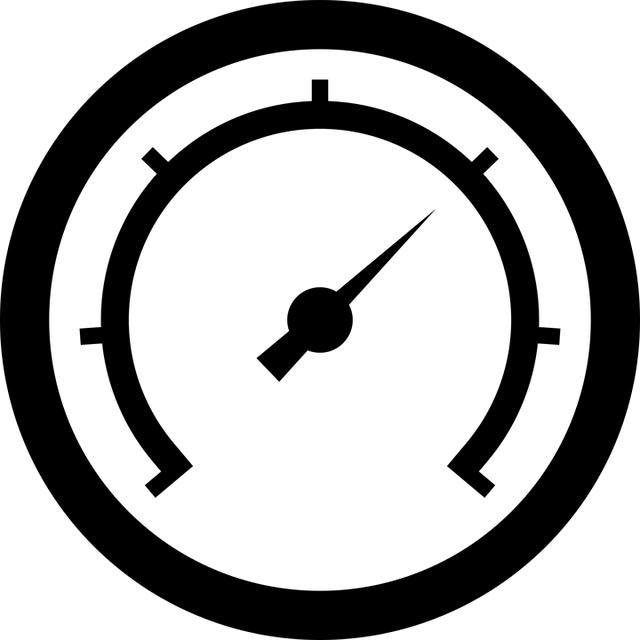
Gage Repeatability and Reproducibility (GR&R) studies, vital for quality control, offer valuable insights into the effectiveness of measurement systems and suggest potential improvements. Atlas Manufacturing conducted Gage R&R studies as a significant component of the quality control process for the medical device project, ensuring the accuracy and dependability of measurements.
Data Collection and Analysis
Data collection and analysis for Gage R&R studies involve multiple steps:
- Select an appropriate number of operators.
- Record the measurements taken by each operator.
- Gather a sufficient number of measurements to ensure statistical validity.
These steps are crucial in ensuring accurate and reliable results in Gage R&R studies.
Once the data is collected, it is typically analyzed using ANOVA (Analysis of Variance) and EMP (Expected Mean Squares) to assess the variability in the measurements and determine the percentage of variance in the data.
Interpreting Results
The interpretation of Gage R&R results aids in pinpointing areas needing improvement in the measurement system and overall product quality. By analyzing the repeatability and reproducibility factors impacting the measurements, manufacturers can pinpoint sources of variation and evaluate if the measurement system requires enhancement.
Furthermore, Gage R&R results can be utilized to assess the accuracy and reliability of the measurement system, allowing manufacturers to make informed decisions about their quality control processes.
Process Failure Mode and Effects Analysis (PFMEA)
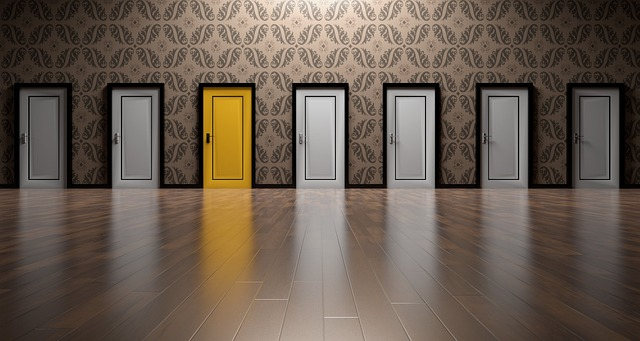
Process Failure Mode and Effects Analysis (PFMEA) is a proactive approach to identifying and mitigating potential failures in the manufacturing process. It involves a systematic analysis of process functions, failure modes, and their potential effects.
Implementing PFMEA allows manufacturers to:
- Identify and prioritize potential risks
- Devise actions to mitigate or eradicate risks
- Reduce risks
- Enhance product quality
- Boost customer satisfaction
PFMEA Methodology
PFMEA methodology involves analyzing each process step for potential failure modes and their effects on the final product. This includes:
- Examining the process or design
- Brainstorming potential failure modes
- Listing potential effects of each failure
- Assigning severity rankings to each potential effect
- Identifying potential causes of each failure mode
- Assigning occurrence rankings to each potential cause
- Determining the current detection methods for each failure mode
- Assigning detection rankings to each detection method.
Adhering to this methodology lets manufacturers determine the Risk Priority Number (RPN) by multiplying the severity, occurrence, and detection rankings, thus prioritizing failure modes based on their RPNs and formulating suitable actions to counter the risks.
Benefits of PFMEA
PFMEA offers manifold benefits for manufacturers, such as risk reduction, product quality enhancement, and customer satisfaction increment. By identifying potential failure modes and assessing the risks associated with each one, manufacturers can implement preventive actions to minimize the chances of failure, leading to a smoother production process and ultimately, a higher-quality product.
Furthermore, PFMEA enables manufacturers to:
- Proactively manage potential risks
- Identify areas of improvement in the manufacturing process
- Ensure that products meet customer requirements and expectations
- Result in increased efficiency and cost savings.
Test Method Reports (TMRs) for Critical Dimensions
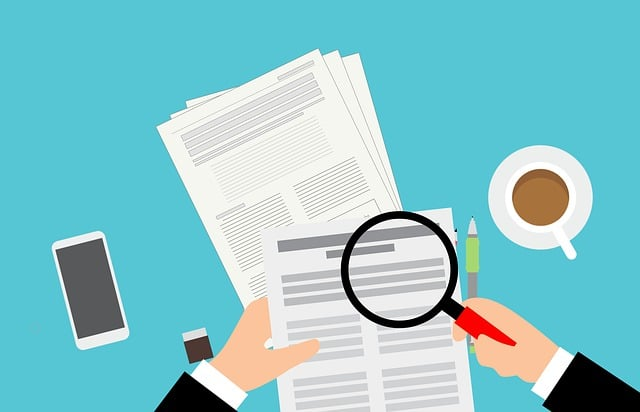
Test Method Reports (TMRs) are indispensable for confirming the accuracy and precision of critical dimensions in the manufacturing process. By documenting the test methods, equipment, and procedures used to measure critical dimensions, TMRs play a vital role in guaranteeing consistent quality control in the manufacturing process. A well-prepared test summary report can further enhance the effectiveness of these TMRs.
Creating TMRs
The creation of TMRs requires documentation of the test methods, equipment, and procedures deployed to measure critical dimensions during the testing process of the manufacturing process. This includes detailing the testing equipment, measurement techniques, and acceptance criteria to guarantee that the product meets the necessary quality standards.
By providing comprehensive instructions and guidelines for measurement and inspection, TMRs assist in sustaining uniformity and precision in the manufacturing of products.
Utilizing TMRs
The use of TMRs aids in maintaining consistent quality control and bolsters ongoing improvement endeavors in the manufacturing process. By monitoring and measuring key quality parameters, manufacturers can detect any deviations from standards and take corrective actions to maintain product quality throughout the manufacturing process. As a result, manufacturers can reduce defects, enhance process efficiency, and deliver superior-quality products to their customers.
Summary
In conclusion, Product Quality Planning, Advanced Product Quality Planning (APQP), Gage R&R studies, Process Failure Mode and Effects Analysis (PFMEA), and Test Method Reports (TMRs) are all essential components of an effective quality control strategy in manufacturing. By implementing these processes and tools, manufacturers can ensure that their products meet or exceed customer expectations, reduce errors, streamline manufacturing processes, and ultimately achieve success in the competitive manufacturing industry.
Frequently Asked Questions
What are the 4 steps of quality planning?
The four steps of quality planning include identifying customer needs, developing product features to meet those needs, establishing quality goals that meet customer and supplier requirements, and finding a process for quality assurance and control.
What are the 5 phases of APQP?
APQP consists of five phases: Planning, Product Design and Development, Process Design and Development, Product and Process Validation, and Feedback and Continuous Improvement.
What is a PQP?
PQP stands for Product Quality Planning. The PQP is unique for each individual development. A core group of personnel will review the concept design, process and product assumptions, and overall goals of the project. The core team selects tools, based on the value they may bring. The PQP is linked to the project timing plan.
What is the primary objective of Product Quality Planning (PQP)?
The primary objective of Product Quality Planning (PQP) is to facilitate communication and collaboration between engineering activities in order to create a comprehensive test summary report.
How does Advanced Product Quality Planning (APQP) differ from traditional PQP?
APQP is an improved structured approach to PQP that utilizes various processes and tools to ensure product quality across all stages of design, production, and delivery. It puts a greater emphasis on meeting customer requirements and delivering products of the highest quality.