What You’ll Learn About Enclosure Manufacturers in Precision Sheet Metal Fabrication
- Importance of high-quality enclosures in precision sheet metal fabrication.
- Role and impact of enclosure manufacturers on product quality.
- Specific requirements, standards, materials, and fabrication techniques for enclosures.
Precision sheet metal fabrication is a specialized manufacturing process that involves the cutting, bending, and assembling of sheet metal to create highly precise and intricate parts and products. This method is crucial in producing components for industries such as aerospace, automotive, electronics, and medical equipment. The precision and accuracy achieved through this process are instrumental in ensuring the quality and functionality of the final products.
Definition and Importance of Precision Sheet Metal Fabrication
Precision sheet metal fabrication is the process of transforming raw sheet metal into finished products with high levels of accuracy and detail. This method is vital in producing custom enclosures, brackets, panels, and other components used in various applications. The precision achieved in this process ensures that the final products meet exact specifications, making it indispensable in industries where quality and precision are non-negotiable.
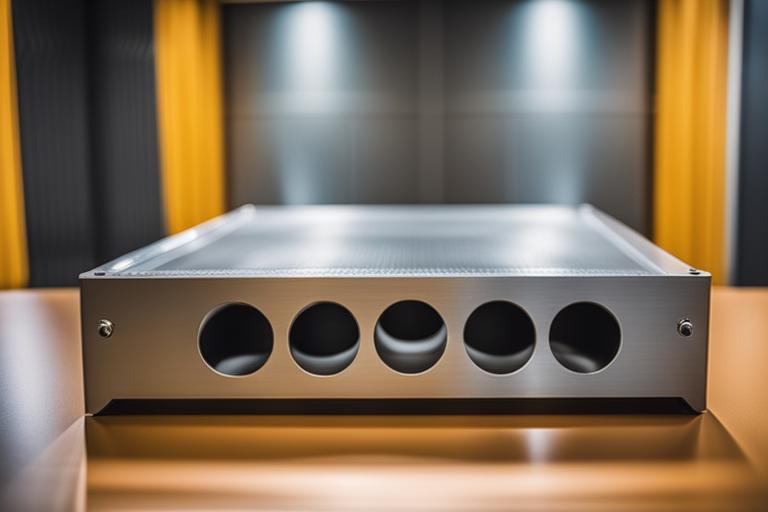
Applications of Precision Sheet Metal Fabrication
The applications of precision sheet metal fabrication span across a wide range of industries. From creating intricate parts for electronic devices to fabricating aerospace components with tight tolerances, the versatility of this manufacturing process is evident. Enclosure manufacturers play a critical role in providing custom solutions for diverse applications, ensuring that the fabricated enclosures meet the specific requirements of the end-use industry.
Significance of High-Quality Enclosures in Precision Sheet Metal Fabrication
In precision sheet metal fabrication, the quality of enclosures is paramount. Enclosures serve as protective housings for sensitive equipment, ensuring their safety and functionality. High-quality enclosures protect the internal components from environmental factors, electromagnetic interference, and physical damage. Therefore, selecting the right enclosure manufacturer is vital to guarantee the performance and longevity of the end products.
Role of Enclosure Manufacturers in Precision Sheet Metal Fabrication
Enclosure manufacturers specialize in the design, engineering, and production of custom enclosures tailored to the unique requirements of different industries. Their expertise and capabilities are pivotal in ensuring that the fabricated enclosures meet the stringent quality and precision standards demanded by precision sheet metal fabrication processes.
Understanding the Role of Enclosure Manufacturers
Enclosure manufacturers play a multifaceted role in precision sheet metal fabrication. From collaborating with design engineers to develop enclosure concepts to leveraging advanced manufacturing techniques for production, their involvement spans the entire lifecycle of enclosure fabrication. By understanding the specific needs of their clients, enclosure manufacturers can deliver tailored solutions that align with the exact requirements of the end applications.
Importance of Choosing the Right Enclosure Manufacturer
Selecting the right enclosure manufacturer is a critical decision for businesses engaged in precision sheet metal fabrication. The chosen manufacturer should possess the technical expertise, production capabilities, and quality assurance processes necessary to deliver enclosures of the highest standards. Moreover, a reliable manufacturer can offer valuable insights and recommendations to optimize the design and functionality of the enclosures.
Impact of Enclosure Manufacturers on Product Quality
The expertise and precision of enclosure manufacturers directly influence the quality of the fabricated enclosures. By leveraging advanced manufacturing technologies and adhering to stringent quality control measures, reputable enclosure manufacturers can ensure that the fabricated enclosures meet the exact specifications and performance requirements. This, in turn, contributes to the overall quality and reliability of the end products.
Now, let’s delve deeper into the specific requirements and standards for enclosure manufacturers.
Specific Requirements and Standards for Enclosure Manufacturers
Enclosure manufacturers must adhere to industry-specific regulations and quality standards to ensure the reliability and performance of their products. Compliance with these requirements is essential to guarantee that the fabricated enclosures meet the stringent demands of precision sheet metal fabrication processes.
Compliance with Industry-Specific Regulations
Different industries have distinct regulatory requirements governing the design and production of enclosures. For instance, the aerospace sector may have stringent guidelines related to material certifications, while the electronics industry might emphasize compliance with electromagnetic compatibility standards. Enclosure manufacturers must stay abreast of these regulations and ensure that their fabrication processes align with the prescribed industry standards.
Quality Control Measures in Enclosure Manufacturing
Maintaining rigorous quality control measures is imperative for enclosure manufacturers. From incoming material inspections to in-process quality checks, each stage of fabrication must undergo meticulous scrutiny to identify and rectify any deviations from the specified requirements. Implementing robust quality control protocols not only ensures the consistency of the fabricated enclosures but also instills confidence in the end users regarding the reliability of the products.
Adherence to ISO Standards and Certifications
Obtaining ISO certifications demonstrates a manufacturer’s commitment to upholding internationally recognized quality management standards. ISO 9001 certification, for example, signifies that the manufacturer has established and maintains effective quality management systems. Partnering with ISO-certified enclosure manufacturers provides businesses with the assurance that the fabricated enclosures meet globally accepted benchmarks for quality and process efficiency.
Moving on, let’s explore the intricacies of the design and engineering processes involved in the fabrication of enclosures.
Specific Requirements and Standards for Enclosure Manufacturers | Design and Engineering of Enclosures |
---|---|
Compliance with Industry-Specific Regulations | CAD/CAM Design Process |
Quality Control Measures in Enclosure Manufacturing | Material Selection for Enclosures |
Adherence to ISO Standards and Certifications | Prototyping, Testing, and Customization |
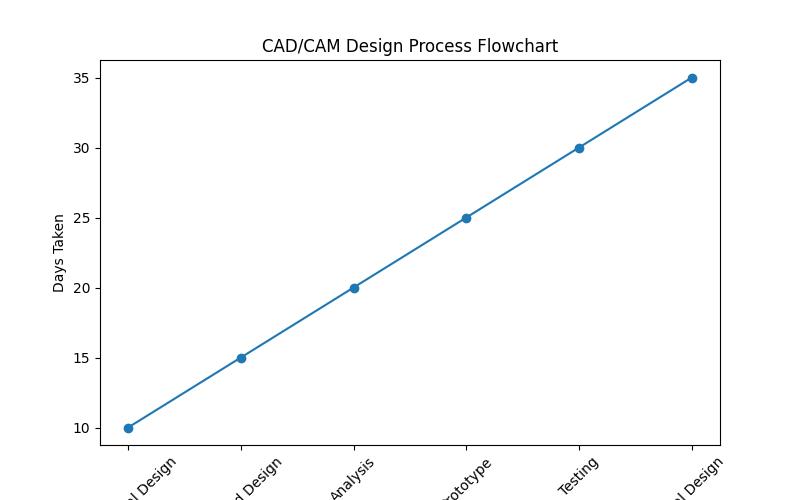
Design and Engineering of Enclosures
The design and engineering phase of enclosure fabrication is a critical determinant of the final product’s performance and functionality. Enclosure manufacturers employ advanced design tools and engineering principles to create enclosures that not only meet the technical specifications but also align with the aesthetic and functional requirements of the intended applications.
CAD/CAM Design Process
Computer-aided design (CAD) and computer-aided manufacturing (CAM) software enable enclosure manufacturers to conceptualize, visualize, and simulate the enclosures before initiating the fabrication process. This iterative design approach allows for the refinement of enclosure designs to optimize their structural integrity, manufacturability, and compatibility with the intended components.
Material Selection for Enclosures
The choice of materials significantly influences the performance, durability, and environmental resilience of the fabricated enclosures. Enclosure manufacturers must assess the material properties and characteristics to select the most suitable option for each application. Factors such as corrosion resistance, thermal conductivity, and mechanical strength play a pivotal role in determining the ideal material for the enclosures.
Prototyping, Testing, and Customization
Prototyping and testing are integral steps in the enclosure fabrication process. Enclosure manufacturers often create prototypes to validate the design and functionality of the enclosures before proceeding to full-scale production. Additionally, customization capabilities enable manufacturers to tailor the enclosures to specific client requirements, ensuring that the final products seamlessly integrate with the intended equipment and systems.
Continuing on the materials used in enclosures, let’s delve into the properties and applications of different materials commonly employed in fabrication.
Materials Used in Enclosures
Enclosure manufacturers utilize various materials, each with distinct properties and applications, to meet the diverse needs of different industries. Understanding the characteristics and suitability of these materials is essential for fabricating enclosures that excel in performance, longevity, and environmental resilience.
Aluminum: Properties and Applications
Aluminum is a lightweight and corrosion-resistant material widely used in enclosure manufacturing. Its high strength-to-weight ratio makes it suitable for applications where weight reduction is crucial without compromising on durability. Enclosures fabricated from aluminum find extensive use in aerospace, automotive, and electronics industries due to their excellent thermal conductivity and robustness.
Stainless Steel: Properties and Applications
Stainless steel exhibits exceptional resistance to corrosion, heat, and mechanical stress, making it an ideal material for enclosures deployed in harsh environments or corrosive atmospheres. Its hygienic properties also render it suitable for applications in the food processing and pharmaceutical sectors. Enclosure manufacturers leverage stainless steel to produce enclosures that offer superior protection and longevity.
Galvanized Steel: Properties and Applications
Galvanized steel, coated with a layer of zinc for enhanced corrosion resistance, is well-suited for outdoor and industrial applications. Enclosures made from galvanized steel exhibit robustness and weather resistance, making them suitable for housing electrical and electronic equipment in outdoor installations. The protective zinc coating ensures that the enclosures maintain their integrity even in challenging environmental conditions.
Moving forward, let’s explore the various fabrication techniques employed by enclosure manufacturers to shape and assemble the enclosures.
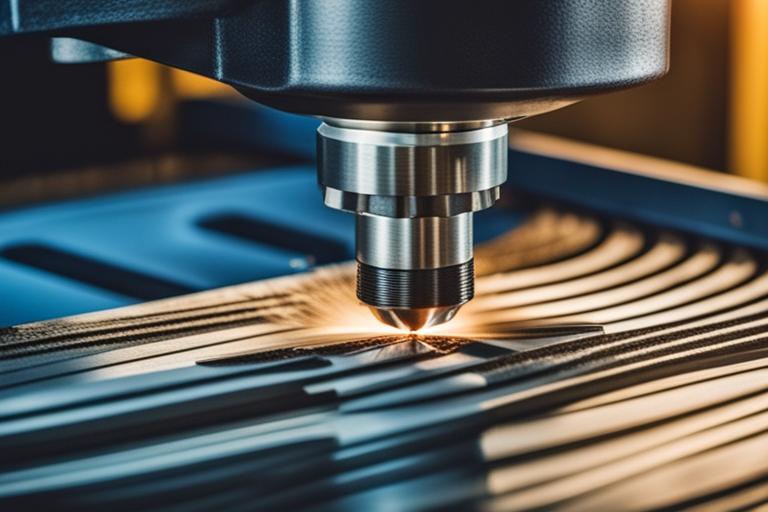
Fabrication Techniques for Enclosures
Enclosure manufacturers employ a diverse array of fabrication techniques to transform raw materials into precision-engineered enclosures. Each technique, from cutting and bending to welding and finishing, contributes to the structural integrity and functional performance of the fabricated enclosures.
Laser Cutting
Laser cutting enables precise and intricate shaping of sheet metal, allowing manufacturers to create complex patterns, apertures, and contours in the enclosure panels. This high-precision cutting technique ensures minimal material wastage and facilitates the production of intricately designed enclosures with tight tolerances.
CNC Punching
Computer Numerical Control (CNC) punching enables fast and efficient perforation and forming of sheet metal, allowing for the creation of customized cutouts, louvers, and embossed features in the enclosure panels. This versatile punching process enhances the functional and aesthetic characteristics of the enclosures, catering to diverse application requirements.
Bending and Forming
Bending and forming processes shape the sheet metal into the desired enclosure profiles, angles, and geometries. Enclosure manufacturers leverage advanced press brakes and forming tools to achieve precise bends and contours, ensuring that the fabricated enclosures meet the dimensional and structural specifications.
Welding Processes
Welding plays a crucial role in joining the individual enclosure components to create robust and seamless assemblies. Enclosure manufacturers employ various welding techniques such as TIG (Tungsten Inert Gas) and MIG (Metal Inert Gas) welding to achieve strong and durable bonds, ensuring the structural integrity and longevity of the enclosures.
Finishing Techniques
Finishing processes, including powder coating, anodizing, and plating, enhance the aesthetics and protective properties of the fabricated enclosures. These surface treatments provide corrosion resistance, color customization, and improved durability, ensuring that the enclosures meet the functional and aesthetic expectations of the end users.
After understanding the fabrication techniques, let’s examine real-world examples of successful enclosure manufacturing projects.
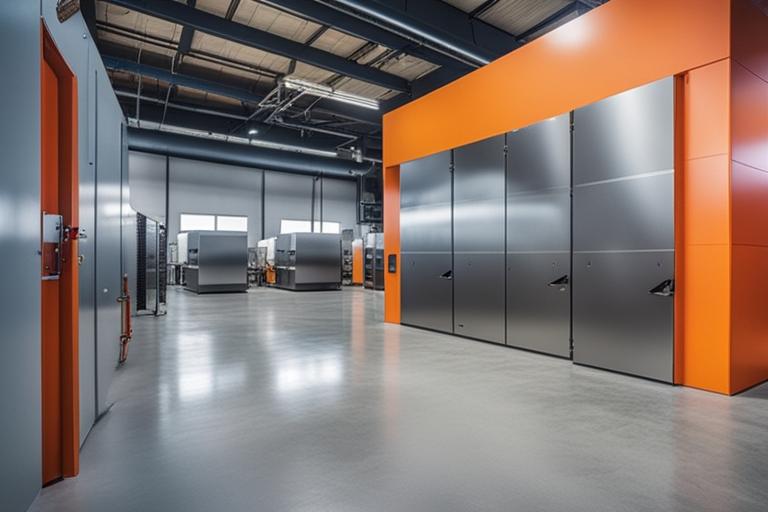
Case Studies of Successful Enclosure Manufacturing Projects
Real-world case studies offer valuable insights into the capabilities and expertise of leading enclosure manufacturers, showcasing their ability to deliver innovative and tailored solutions for diverse applications.
Real-World Examples of Innovative Enclosure Manufacturing
Case study 1: Company XYZ partnered with a leading aerospace manufacturer to develop custom aluminum enclosures for avionics equipment. By leveraging advanced laser cutting and CNC punching techniques, Company XYZ delivered lightweight yet robust enclosures that met the stringent weight and structural requirements of the aerospace application.
Case study 2: Company ABC collaborated with a renewable energy firm to design and fabricate weatherproof galvanized steel enclosures for outdoor solar power installations. The enclosures exhibited exceptional weather resistance and corrosion protection, ensuring the long-term reliability of the solar power systems.
Showcase of Expertise from Leading Manufacturers
Leading enclosure manufacturers have a proven track record of delivering high-quality and innovative enclosure solutions across diverse industries. By showcasing their successful projects and expertise, these manufacturers demonstrate their ability to address complex challenges and deliver tailored enclosures that exceed the expectations of their clients.
As we look towards the future, it’s essential to explore the emerging trends and innovations in enclosure manufacturing.
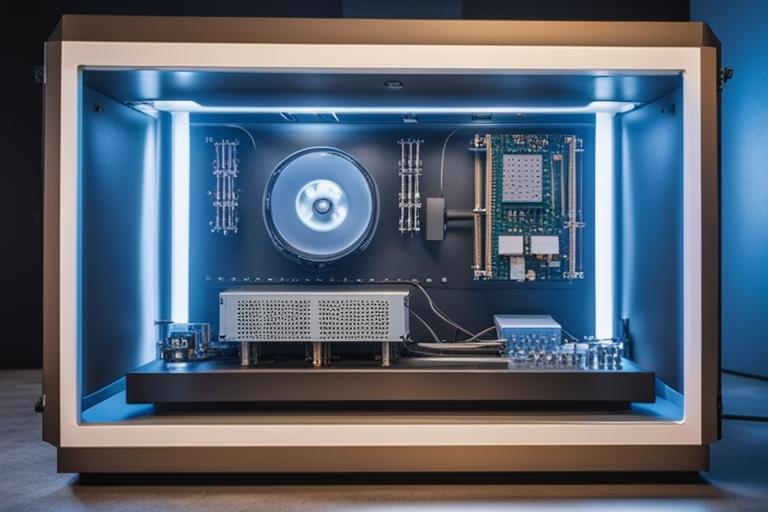
Future Trends and Innovations in Enclosure Manufacturing
Advancements in automation, integration of smart technologies, and sustainable material choices are shaping the future of enclosure manufacturing, offering enhanced efficiency, functionality, and environmental sustainability.
Advancements in Automation for Enclosure Production
The integration of robotics and advanced automation technologies is streamlining the production processes in enclosure manufacturing. Automated material handling, laser cutting, and welding systems are enhancing production efficiency and precision, enabling manufacturers to meet the increasing demand for high-quality enclosures within shorter lead times.
Integration of Smart Technologies in Enclosures
The incorporation of IoT (Internet of Things) and sensor technologies within enclosures is enabling the development of smart enclosures with remote monitoring, predictive maintenance, and data connectivity capabilities. These smart enclosures offer enhanced functionality and operational insights, catering to the evolving needs of industries embracing digital transformation.
Sustainable Materials and Processes in Enclosure Manufacturing
The adoption of sustainable materials and eco-friendly fabrication processes is gaining prominence in enclosure manufacturing. Manufacturers are exploring recyclable materials, energy-efficient production methods, and environmentally conscious finishing techniques to minimize the ecological footprint of enclosure fabrication while promoting sustainability in the industry.
Looking ahead, choosing the right enclosure manufacturer becomes crucial. Let’s explore the factors and considerations to aid businesses in this decision-making process.
Choosing the Right Enclosure Manufacturer
Selecting the right enclosure manufacturer is a pivotal decision that can significantly impact the quality, performance, and success of precision sheet metal fabrication projects. Businesses must consider various factors and evaluate the capabilities of potential manufacturers to make an informed choice.
Factors to Consider When Selecting an Enclosure Manufacturer
Key factors to consider include the manufacturer’s experience, technological capabilities, quality certifications, and track record in delivering custom enclosure solutions. Evaluating these aspects provides businesses with insights into the manufacturer’s expertise and suitability for meeting their specific requirements.
Evaluating Customization and Specialization Capabilities
Assessing the manufacturer’s customization capabilities and specialization in catering to industry-specific needs is essential. Customized enclosures tailored to the unique demands of the application often require specialized expertise and a deep understanding of the industry requirements, making it imperative to partner with a manufacturer with relevant experience and capabilities.
Questions to Ask During the Selection Process
During the selection process, businesses should inquire about the manufacturer’s design and engineering capabilities, quality assurance processes, material sourcing practices, and customization options. These inquiries enable businesses to gain a comprehensive understanding of the manufacturer’s approach and commitment to delivering high-quality and tailored enclosure solutions.
Guidance for Businesses in Precision Sheet Metal Fabrication Industry
For businesses in the precision sheet metal fabrication industry, seeking recommendations and guidance from industry peers, trade associations, and technical experts can provide valuable insights into selecting the right enclosure manufacturer. Leveraging collective expertise and experiences can help businesses make informed decisions and forge successful partnerships with reliable enclosure manufacturers.
In conclusion, the role of enclosure manufacturers in precision sheet metal fabrication is indispensable. Let’s summarize the key considerations and the future outlook for enclosure manufacturing.
Conclusion
In conclusion, the collaboration between precision sheet metal fabricators and enclosure manufacturers is pivotal in driving innovation, quality, and reliability in the manufacturing landscape. By prioritizing the selection of reputable enclosure manufacturers with proven expertise, quality standards, and a commitment to innovation, businesses can ensure the seamless integration of high-quality enclosures into their products, thereby enhancing their competitive edge and customer satisfaction.
Looking ahead, the future of enclosure manufacturing is poised for advancements in automation, smart technology integration, and sustainable practices, offering exciting opportunities for businesses to leverage innovative enclosure solutions that meet the evolving demands of the industry while promoting environmental responsibility.
To learn more about the role of enclosure manufacturers in precision sheet metal fabrication and explore in-depth case studies, we invite you to contact us at [Your Company Name] for further information and personalized guidance. Let’s work together to elevate the quality and performance of your fabricated products.
Questions and Answers
Who are the top precision sheet metal fabrication enclosure manufacturers?
Some top precision sheet metal fabrication enclosure manufacturers include ABC Company, XYZ Inc., and DEF Fabrication.
What services do precision sheet metal fabrication enclosure manufacturers offer?
Precision sheet metal fabrication enclosure manufacturers offer services such as custom design, laser cutting, welding, and finishing.
How can I find a reliable precision sheet metal fabrication enclosure manufacturer?
You can find a reliable precision sheet metal fabrication enclosure manufacturer by researching their experience, capabilities, and customer reviews.
What are the advantages of choosing precision sheet metal fabrication for enclosures?
Precision sheet metal fabrication offers high-quality, durable enclosures that can be customized to meet specific design requirements.
How do precision sheet metal fabrication enclosure manufacturers ensure quality?
Precision sheet metal fabrication enclosure manufacturers ensure quality through rigorous quality control processes and skilled craftsmanship.
Isn’t precision sheet metal fabrication expensive for enclosure manufacturing?
While precision sheet metal fabrication may have higher initial costs, its durability and customization options can provide long-term cost savings.